Неавтоклавный газобетон: технология производства и
Газобетон в последнее время есть весьма популярным стройматериалом, благодаря ряду своих преимуществ. Обычно застройщики отдают предпочтение более недорогому его варианту – неавтоклавному газобетону. Но что представляет собой данный материал, чем отличается автоклавный и неавтоклавный газобетон и стоит ли на нем экономить?
Потом мы попытаемся ответить на все эти вопросы и дать исчерпывающую данные по данному типу ячеистого бетона.
Неспециализированные сведения
Многие люди уверены в том, что газобетон – это современный материал. Но,в действительности он был запатентован в первый раз еще в 1889 г. в Праге неким изобретателем Гофманом. Он придумал изготавливать материал на базе газа, получаемого в следствии химической реакции между соляной кислотой и бикарбонатом натрия.
В Голландии в начале прошлого века была запатентована технология изготовление газобетона с применением дрожжей. Мало позднее в Германии внесли предложение использовать в качестве газообразующего вещества железную пудру.
Фактически современная технология изготовления пористого бетона была создана в Швейцарии изобретателем Эриксоном в 1923 г. Уже в 1925 году было налажено производство неавтоклавного газобетона как стройматериала. Весьма скоро его производство появилось и во многих других государствах.
В то время материал приготавливали на базе портландцемента, а мало позднее стали использовать и вяжущие на базе зол и шлаков. Изначально материал был придуман как утепляющий, но уже в 30-х годах удалось взять и конструкционный газобетон. Его использовали для ограждающих конструкций в малоэтажных зданиях.
Так, материал сложно назвать совсем новым, поскольку он прошел уже достаточную и в полной мере успешную диагностику временем.Само собой разумеется, на сегодня применяют современное технологическое оборудование для производства неавтоклавного газобетона, с новыми видами тепловлажностной обработки. Помимо этого, подобраны самые оптимальные составы, что существенно повысило уровень качества изделия.
Технология производства
Состав
В составе данного типа ячеистого бетона применяют следующие основные компоненты:
- Портландцемент – есть вяжущим элементом;
- Наполнители – песок в чистом виде, или с добавлением золы-уноса ТЭЦ, мела, гипса и пр.
- Алюминиевая пудра – употребляется при формировании материала в качестве парообразующего вещества.
Помимо этого, для улучшения черт, в состав неавтоклавного газобетона додают разные модифицированные добавки, к примеру, полуводный микрокремнезем либо гипс. Для ускорения процесса твердения применяют хлорид кальция.
На сегодня ведутся работы по повышению прочностных черт изделия выполненного неавтоклавным способом. Самым перспективным считается применение разных армирующих добавок, воображающих собой волокна различного происхождения.
Это смогут быть:
- Стекловолокна;
- Полимерные волокна;
- Базальтовые;
- Ас
Неавтоклавный газобетон: технология, состав, свойства
В строительстве неавтоклавный газобетон применяется при возведении малоэтажных зданий. В многоэтажных конструкциях — оформление разделительных перегородок, внутренних стен, заполнение бетонных и стальных каркасов, для теплоизоляции поверхностей. Преимуществом материала является возможность заливки монолитной конструкции любого размера и веса.
Что это такое?
Первоначально технология производства ячеистого газобетона предусматривала помещение блоков в специальные печи-автоклавы при давлении в 8—10 бар и температуре 200 градусов, что обеспечивало полный выход влаги из материала. Позднее стал использоваться более простой способ производства под названием «неавтоклавный газобетон» — без давления и обжига в печах, с процессом твердения в естественных условиях. Составы растворов, заливаемых в формы для формирования блоков, одинаковы в обоих случаях.
Состав и свойства
Компоненты, входящие в состав смеси для производства неавтоклавного газобетона:
- портландцемент марки не ниже М300, не менее 50% от общего веса;
- песок;
- зола, мел, гипс, доменный шлак;
- алюминиевая пудра для пенообразования;
- известь;
- вода;
- хлорид кальция — для ускорения процесса твердения смеси;
- добавки и присадки для улучшения эксплуатационных характеристик материала.
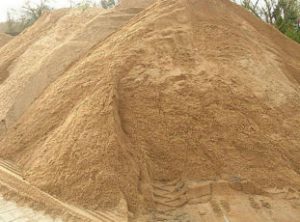
Рецептура раствора для неавтоклавного бетона требует использования песка без примесей глины или ила, воды — без содержания соли. В качестве добавок для улучшения прочности газобетона рекомендуются: полуводный гипс, микрокремнезем, кислая зола-унос. С этой же целью могут добавляться армирующие волокна, что улучшит характеристики материала. Для более качественного пенообразования могут быть добавлены стиральные порошки, поваренная соль.
Как производится: технология
Изготовление стандартное: приготовление раствора, заливка в опалубку или формы, застывание и твердение продукции. Из инструментов понадобится бетономешалка, лопата, ведра. Все сухие компоненты перед началом работ взвешиваются и отмериваются согласно долям, что требуют составы по технологии. Пенообразование происходит при вступлении в реакцию щелочных составляющих цементного раствора с алюминиевой пудрой. В результате высвобождается водород и формируются ячеистые поры.
Самый важный момент в процессе неавтоклавного изготовления газобетона, влияющий на конечные характеристики продукта, — вспенивание смеси. Реакция с газообразованием должна произойти до момента добавления в смесь вяжущего вещества.
Поэтапный процесс производства неавтоклавного газобетона:
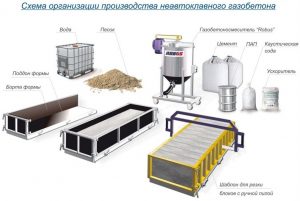
- Готовится опалубка либо формы для заливки. Внутренние поверхности обрабатываются маслом.
- В отдельной емкости готовится пенообразователь: заливается вода с алюминиевой пудрой из расчета 50:1. Добавляется стиральный порошок и оставшаяся часть пудры согласно рецептуре. Тщательно перемешивается до полного исчезновения металлических частиц на поверхности.
- В бетономешалку заливается расчетное количество воды, агрегат включается.
- Засыпается песок, цемент.
- Через 2 мин в смесь добавляется известь.
- Засыпается поваренная соль.
- Через 5 мин от начала процесса смесь готова для заливки в опалубку/формы.
- После полного отвердения массы опалубка снимается либо демонтируется каркас и монолитный газобетон нарезается на блоки нужной формы.
Плюсы и минусы использования
Составы бетонных блоков, применяемых в строительстве сходны, при этом неавтоклавный газобетон имеет свои достоинства. К ним относятся: небольшой вес; теплостойкость; влаго- и морозоустойчивость; энергосберегающие свойства; высокие звукоизоляционные характеристики; сейсмостойкость; податливость любым электрическим и ручным инструментам; возможность заливки блоков любой формы; несложный процесс изготовления. При этом показатели прочности ниже других подобных материалов. К другим недостаткам относится склонность к разрушению под действием механических нагрузок, большая усадка, длительный период ожидания затвердения материала в процессе производства.
Автоклавный и неавтоклавный газобетон — АлтайСтройМаш
Вы обязательно должны выделить несколько минут своего времени, чтобы прочитать эту важную статью. Сегодня мы расскажем вам всю правду об автоклавном и неавтоклавном газобетоне (а точнее, о его производстве):
— Почему неавтоклавное производство с каждым годом становится все популярнее?
— Чем отличается автоклавный газобетон от неавтоклавного?
— Почему сроки окупаемости бизнеса на производстве неавтоклавного газобетона как минимум
— Почему неавтоклавное производство намного выгоднее для производителей?
Итак, что лучше: автоклавный или неавтоклавный газобетон? Читайте нашу статью, и вы все узнаете!
1. Технология производства
Основной компонент автоклавного газобетона – известь, которая затвердевает только при особой обработке. Для этого используются автоклавы – герметично закрывающиеся аппараты, в которых поддерживается постоянная температура (180-200С) и давление (12-14 атм). Твердение автоклавных газоблоков происходит
Основной компонент невтоклавного газобетона – цемент, который смешивается с наполнителем (песок, зола уноса ТЭЦ, доломитовая мука и др.) и газообразователем (алюминиевая пудра/паста). Для затвердевания таких газобетонных блоков необходимо добиться температуры всего 40-60С (для этого используются простые прогревочные камеры). Необходимое время для набора первоначальной прочности – 6-10 часов.
2. Стоимость
Для запуска автоклавного производства
Если рассматривать качественное оборудование от немецких производителей, то стоимость линии с производительностью 200 кубометров газобетона в сутки составит примерно более 6 000 000 долларов!
Линию для производства неавтоклавного газобетона можно купить за 85 000 долларов. Это стоимость оборудования с максимальной производительностью – 200 кубометров в сутки. При этом линию с минимальной производительностью можно купить всего за
3. Сроки изготовления оборудования
Если вы хотите организовать бизнес «здесь и сейчас», то автоклавное производство – точно не для вас. Сроки изготовления автоклавного оборудования – минимум 1 год (а в среднем – 1,5 года) после официального заключения сделки.
Срок изготовления и поставки оборудования по производству неавтоклавного газобетона в среднем составляет 10-30 дней.
4. Затраты на электроэнергию
Энергозатраты на автоклавном производстве в десятки раз больше. К примеру, мощность электродвигателя шаровой мельницы – около
Энергозатраты на неавтоклавном производстве минимальны:
— Электропитание основного оборудования: от 4 до 15 кВт (зависит от типа оборудования).
— Нагрев воды до 50-60С.
— Нагрев прогревочной камеры до 40-60С (требуется только поддержание температуры).
5. Сроки окупаемости бизнеса
Учитывая все предыдущие пункты, приходим к логичному заключению: бизнес по производству
Срок окупаемости бизнеса по производству неавтоклавных газоблоков составляет всего 5-6 месяцев!
Отличия автоклавного и неавтоклавного газобетона: есть или нет?
Мы рассмотрели основные различия бизнеса по производству автоклавного и неавтоклавного газобетона. Переходим к подведению итогов!
1. Автоклавный и неавтоклавный газобетон должны отвечать требованиям одного и того же ГОСТа.
2. Соответственно, при соблюдении технологии производства на выходе мы получим
3. Самое интересное, что после отделки многие не могут отличить дома, построенные из автоклавного и неавтоклавного газобетона. Единственное отличие – цвет блоков; прочностные характеристики будут идентичны.
Более 5 000 клиентов компании АлтайСтройМаш уже стали производителями неавтоклавного газобетона!
А какой бизнес выберете вы?
Подобрать оборудование
Неавтоклавный газобетон: характеристики, технология производства
Газобетон, или искусственный камень, относится к легким ячеистым бетонам. Свое название они получили из-за наличия в структуре небольших сферических пор от 1 до 3 мм в диаметре, равномерно распределенных по всему объему. Замкнутые ячейки образуются в результате химической реакции между порообразователем, например, алюминиевой пудрой и водой. Их наличие и объясняет положительные технические характеристики газобетона, привлекающие строителей.
Оглавление:
- Технические параметры неавтоклавного бетона
- Процесс изготовления
- Как сделать газоблок в домашних условиях?
Существуют и другие технологии создания пор в структуре материалов, например, введение в цементно-песчаную смесь технической пены, которая приготавливается в соответственном агрегате. В результате получается не менее популярный неавтоклавный пенобетон. Далее будет рассмотрены его свойства и способы производства.
Характеристики и особенности
Автоклавы – это специальные печи, где согласно технологии создается повышенная температура и избыточное давление для спекания бетонной смеси. Изготовленный таким образом стройматериал называется автоклавным. Естественно, что для этого процесса необходимо наличие оборудования промышленного предприятия.
Неавтоклавный газобетон твердеет естественным путем под действием атмосферного давления. Иногда, особенно в первые сутки, на производстве создают повышенную температуру для лучшего «созревания». Технология изготовления не представляет трудности, поэтому этим можно заниматься дома самостоятельно. Тем более что по цене газобетонные блоки своими руками обойдутся более чем на 30 % меньше заводских, без учета транспортных расходов.
Правда, бюджетность этого стройматериала сопровождается характеристиками, уступающими искусственному камню, созданному в автоклавах. Речь идет о следующих свойствах:
- Небольшая прочность. Невозможно добиться автоклавной твердости, создавая газобетон своими руками в домашних условиях.
- Длительный период твердения.
- Отсутствие твердости влечет за собой значительную усадку неавтоклава: 2-3 мм против 0,3 автоклавного.
- Необходимость использования армопоясов в местах наибольшей нагрузки.
- Несовершенная поверхность, которая сказывается при возведении стен и требует дополнительных затрат.
Неавтоклавный и автоклавный газобетон отличаются друг от друга многими параметрами, но первый все-таки обладает преимущественными характеристиками, в том числе:
1. в его составе имеются только природные компоненты, которые не выделяют вредностей;
2. неподвластен воздействию влаги;
3. способен сохранять тепло;
4. обладает высокой звукоизоляцией;
5. огнестоек и сохраняет прочность при термических нагрузках и открытом огне;
6. экологичен и стоек к гниению;
7. оказывает противодействие микробным и грибковым образованиям;
8. имеет низкую стоимость производства;
9. легкий и удобный для механической обработки различными инструментами, при этом сохраняет значимые свойства, что облегчает прокладку через него коммунальных сетей;
10. значительные габариты блоков способствуют увеличению скорости монтажа;
11. возможность изготовления на полигоне рядом со строительной площадкой, что позволяет снизить расходы на транспортировку;
12. легкий вес избавляет от необходимости в подъемных механизмах, а это удешевляет стоимость строительного объекта;
13. возможность использования в качестве монолитного бетона;
14. стойкость при землетрясениях.
Производство неавтоклава обходится без больших затрат электроэнергии, а стоимость базового оборудования вполне приемлема даже для частного лица, планирующего изготавливать этот материал своими силами.
Схема производства
В состав базовой линии для изготовления неавтоклавного ячеистого бетона входит следующее оборудование:
- смеситель для ручной загрузки компонентов, который передвигается вдоль поддонов на колесах;
- поддоны-формы, куда разливается готовая смесь;
- борта для форм, легко снимающиеся с поддонов;
- специальные пилы для удаления горбушки и нарезания блоков.
Кроме этого при покупке поставляется информационная документация: чертежи, инструкции, руководство по эксплуатации, схема работы.
Схематично технологический производственный процесс выглядит таким образом:
Дозированный цемент | Просеянный и взвешенный песок | Определенное количество воды с температурой 40–50°C | Дозированный порообразователь – алюминиевая суспензия (вода, пудра, синтетическое моющее средство) |
↓ | |||
Поступают в смеситель для перемешивания | |||
↓ | |||
Смесь заливается в поддоны-формы | |||
↓ | |||
Подъем, созревание смеси и предварительный набор прочности около 2-х часов | |||
↓ | |||
Удаление горбушки пилой | |||
↓ | |||
Освобождение поддонов от бортов (распалубка) | |||
↓ | |||
Нарезание блоков из массива | |||
↓ | |||
Прогревание теплоизолирующим колпаком разрезанных блоков 6-10 часов | |||
↓ | |||
Перенос блоков на транспортный поддон, упаковка, отправление на склад | |||
↓ | |||
Очистка смазка, установка бортов на освободившуюся форму для подготовки к следующей заливке |
Согласно инструкции песок и цемент вначале отмеряют, а затем загружают. Суспензию предварительно готовят в небольшом объеме, смешивая компоненты дрелью с насадкой.
Количество и состав оборудования зависит от мощности, которою определяет заказчик. Также, при желании, можно к базовой комплектации купить вспомогательные технологические элементы за дополнительную стоимость (весы, колпаки, водонагреватель и прочее).
Как сделать в домашних условиях?
Будущему хозяину небольшого дома изготовить такой газобетон самому очень привлекательно, с точки зрения экономии стоимости строительства. Правда, для получения нужных характеристик необходимо иметь помощников, соответствующее оборудование (хотя бы бетономешалку, формы для заливки, резательные струны), четкое соблюдать этапы, грамотно дозировать ингредиенты.
Для получения газобетона марки D600 нужно придерживаться следующих пропорций состава:
- портландцемент ПЦ500 D0 – не менее 65 %;
- очищенного песка должно быть 30 %;
- известковой муки – 5–10 %.
Разброс в содержании последнего компонента объясняется цветовым предпочтением. Большее количество извести дает более светлую окраску. Еще добавляется алюминиевая пудра до 0,48 % для выделения водорода, образования пены и, в дальнейшем, получения сферических пор в готовом ячеистом бетоне.
Количество необходимого материала, чтобы своими руками сделать 1 м3 неавтоклавного искусственного камня представлено в таблице:
Чистая питьевая вода | 250 – 300 л |
Мелкий, до 2 мм чистый песок | 250 – 350 кг |
Цемент марки M500D0, M400D0 | 260 – 320 кг |
Алюминиевая пудра | 0,5 – 0,7 кг |
Смазка для контейнеров | 0,3 – 0,5 кг |
Добавки для улучшения характеристик, в том числе прочности | 1– 3 кг |
Пошагово этот процесс будет выглядеть так:
- Тщательное взвешивание сухих компонентов.
- Замешивание ингредиентов в бетономешалке с добавлением предварительно подготовленной алюминиевой эмульсии.
- Заливка полученной смеси в контейнеры до половины, так как масса увеличивается в объеме из-за образования ячеек. Заполненные формы должны находиться на защищенной от непогоды территории.
- Через 6–8 часов снятие горбушки массива металлическим прутом или специальной пилой.
- Через 12 часов полуготовые блоки извлечь из контейнеров и оставить на 48 часов на ровной поверхности набирать твердость.
- Через 28 суток газобетонные блоки будут готовы для эксплуатации.
Очевидно, что для изготовления блоков бетона лучше применять спецоборудование, которое обеспечит отличное качество, и процесс займет меньше времени. А аренда агрегатов, даже для личного домостроения, ненамного увеличит стоимость искусственного камня.