Фибробетон своими руками — технология изготовления своими руками фибробетона
В большом семействе бетонов относительно недавно появился новый участник – фибробетон. Он получил свое название из-за наличия в своем составе фибры, которая представляет измельченные волокна различных материалов. Исходным материалом для нее может служить стекловолокно, базальт, пластики, мелкие фракции металла и иные материалы растительного или искусственного происхождения. Применение волокон придает бетону новые свойства.
Материал становится более прочным и одновременно пластичным. Предотвращается растрескивание при высыхании и отвердении, а так же предотвращается коррозия арматуры. Все чаще его применяют при индивидуальном строительстве, и домашние умельцы изучают, как приготовить фибробетон своими руками.
Состав.
Прочность материала определяется типом и количеством фибры в его составе. Добавки могут составлять от 0,3 до 10 кг/м3 и более. В зависимости от класса бетона изменяется и соотношение между содержанием песка и бетона. Для приготовления своими руками фибробетона класса В 20 применяется соотношение 1:4, а для В 25 1:3. Учитывая отсутствие в составе бетона тяжелых наполнителей, таких как щебень или гравий, особое требование предъявляется к качеству песка. Он не должен содержать примесей и камней. Перед использованием его необходимо тщательно просеять и промыть.
Для придания материалу, сделанного своими руками, более высокого качества в фибробетон добавляют пластификаторы и добавки. Это несколько увеличивает его стоимость, но позволяет добиться качества достаточно близкого к материалу заводского изготовления.
Технология приготовления.
Технология приготовления своими руками фибробетона во многом похожа на стандартную, но имеет некоторые отличия.
Для процесса изготовления потребуется бетономешалка и дробилка. Исходный материал для приготовления фибры измельчают с помощью дробилки и добавляют в сухую смесь песка и цемента. Ее можно добавить и в процессе перемешивания, но тогда время замеса необходимо увеличить для более равномерного распределения фибры по объему. В случае добавления волокна в сухую смесь, для приготовления фибробетона, оно намного быстрее равномерно распределится, что позволит добиться равномерности свойств материала, изготовленного своими руками.
Равномерность свойств по объему – одна из наиболее важных характеристик любого материала. При приготовлении своими руками фибробетона необходимо следить за тем, чтобы не образовывались скопления волокна. Для того, чтобы избежать этого, рекомендуется увеличить время перемешивания по сравнению с приготовлением обычного бетона примерно на 30-50%.
В процессе замеса рекомендуется периодически проверять качество приготовляемого раствора. При тщательном соблюдении технологии, фибробетон, сделанный своими руками получается довольно близким по своим характеристикам к материалу промышленного производства.
Некоторые особенности применения.
Полученный раствор можно использовать как для заливки монолитных конструкций, так и для изготовления сборных блоков. Использование фибробетона позволяет уменьшить расход арматуры, благодаря его структурному армированию волокнами.
Особенно прочными получаются изделия, в которых наполнителем является стекловолокно или мелкофракционный металл. Их прочность может превышать прочность обычного бетона в несколько раз. Это находит частое использование для изготовления своими руками блоков из фибробетона. Учитывая повышенную прочность материала, их толщину можно делать меньше, чем в случае изготовления блоков из ячеистого бетона. Это позволяет уменьшить расход материала и трудоемкость выполняемых работ.
Декабрь 28, 2012Статьи по теме: | |
Утилизация железобетона Строительство новых объектов нередко сопрягается с демонтажом ранее возведенных. При этом возникает вопрос утилизации демонтированных строительных материалов, в частности железобетона. … | |
Миксер с бетононасосом Конструкции из монолитного железобетона находят применение при строительстве объектов различного назначения. Одним из важных этапов возведения таких конструкций является заливка … | |
Самодельный бетононасос Применение монолитных конструкций существенно снизило трудоемкость и стоимость выполнения строительных работ, сократило сроки строительства. При выполнении этих работ нередко приходится … |
Фиброцементный сайдинг своими руками изготовление — Про стройку и не только
29 Янв by admin
Современное строительство подразумевает, что дом будет не только удобным, уютным, теплым, но и красивым. Эти условия проще выполнить в странах с умеренным климатом, а вот в тех местах, где в течение года погода коренным образом меняется, требуется применение специфических строительных материалов и хорошей теплоизоляции. Осталось выяснить, будет ли построенный дом красивым. Хочется отметить, что фиброцементные фасадные панели – это надежная и красивая защита дома. Если принято решение о такой отделке дома, которая может стать центральным элементом придомовой территории, то далее мы расскажем о том, что такое фиброцементные панели, из чего они состоят, кто их производит и как с ними работать.
Такая отделка преобразит фасад дома и подчеркнет благосостояние хозяев.
Содержание статьи:
Что это за панели
Предоставленное описание поможет лучше познакомиться с этим материалом.
Фиброцемент изготавливается из смеси таких компонентов:
- измельченный песок;
- цемент;
- древесная масса.
Он разработан таким образом, чтобы быть устойчивым к:
- насекомым;
- влаге;
- суровым погодным условиям.
Фиброцементные панели, используемые как сайдинг, украшены рисунком, имитирующим древесину.
Панели на основе фиброцемента изобрели более 100 лет назад, но тогда в их состав входил асбест, опасный для здоровья человека. Впоследствии его заменили древесной массой. Это только улучшило качество материала, и теперь он стал ударопрочным.
Производство панелей делится на такие этапы:
- На конвейер подается песок, который попадает во вращающийся цилиндрический измельчитель.
- Внутри измельчителя находятся металлические шары, который превращают песок в мелкую пыль.
- В песок добавляется вода. Это помогает избавиться от пыли и способствует размягчению песка, в результате чего его становится легче перемещать.
- После транспортировки в специальную емкость удаляются излишки воды.
- Остается смесь песка (20%) и воды (80%).
- Теперь очередь древесной массы, без которой плиты были бы очень хрупкими.
- В массу добавляется вода и перемешивается до тех пор, пока состав не станет такой консистенции, как густая овсяная каша.
- На следующем этапе песок, древесная масса и цемент перемешиваются. В этот состав добавляется вода.
- Раствор заливают в желоб под сетчатым фильтром, где происходит его перемешивание.
- Излишки воды отводятся через решетчатые стены фильтра, остается слой фиброцемента.
- Этот состав наносится на лист картона и по конвейеру передвигается дальше.
- На следующем этапе вакуумный механизм вытягивает оставшуюся влагу через картон, пока не получается лист прочного фиброцемента.
- При проходе через валики несколько листов спрессовываются в единое целое. Таким образом получается толстый пласт.
- Если из панелей будет сделан сайдинг, то еще один валик делает на нем рельефную структуру, имитируя срез дерева.
- Мощным напором воды или резаком от пласта отрезается панель нужной длины.
- Лист еще влажный и с ним нужно бережно обращаться, поэтому дальнейшее его перемещение выполняется манипулятором с присосками. Он переносит их на большой поддон.
- Теперь листы отправляются под пресс, который выдавливает из них лишнюю влагу Одновременно увеличивается плотность и прочность панелей.
- Далее листы помещаются в специальную камеру, где проходят тепло-влажностную обработку.
- На очереди обработка в автоклаве, куда листы попадают вместе с поддоном, на котором они и были уложены.
- После обработки в автоклаве листы становятся максимально прочными, выдерживают большую нагрузку на изгиб и сжатие. Также они становятся стойкими к ударным воздействиям.
- Плиты проходят проверку, и при необходимости отбраковываются.
Продукция попадает в другой цех, в котором происходит следующий этап подготовки их использования в качестве фасадных панелей ‒ обработка влагоотталкивающими составами, антистатиками и нанесение финишного слоя. Все действия выполняются при прохождении листов через конвейер.
- Первым делом выполняется обеспыливание тыльной поверхности листа.
- На эту же сторону наносится полимерное покрытие, которое обеспечивает пароизоляцию материала.
- С помощью ультрафиолетовых ламп выполняется полимеризация покрытия.
- Лист переворачивается и теперь проводится обеспыливание его лицевой стороны.
- Для обеспечения высокой адгезии на лицевую сторону наносится двухкомпонентный эпоксидный грунт.
- Выйдя с конвейера, лист погружается в специальную кассету и оставляется в ней для полимеризации, которая продолжается от 6 до 10 часов.
По истечении предусмотренного срока приступают к нанесению на плиты лако-красочного покрытия.
- Лист вынимается из кассеты и подается на следующий конвейер, в котором лицевая сторона обеспылевается.
- На следующем этапе выполняется нанесение на лицевую сторону матового, цветного лакокрасочного покрытия на основе акрила.
- В следующей камере с помощью инфракрасных ламп покрытие сушится при температуре 60°C.
- На выходе с конвейера плита вновь попадает в кассету, после чего она поступает в продажу.
Характеристики фиброцементных панелей
Вначале затронем положительные характеристики материала:
- Плиты не горючи, поэтому они даже в некоторой степени могут служить защитой дома от наружных источников возгорания.
- Прекрасно переносят ультрафиолетовое излучение, сохраняя свой первоначальный вид.
- Не страшна коррозия.
- Чувствительно улучшается звукоизоляция.
- Материал ударопрочный.
- Плиты устойчивы даже к резким перепадам температур.
- Нет вредных испарений, что говорит об экологичности материала.
Если приобретаются более дешевые, неокрашенные плиты, то многие пункты из перечисленных положительных качеств материала к ним применить нельзя.
Теперь опишем недостатки:
- Если приобретены неокрашенные плиты, то потом их придется периодически красить. В результате возрастет конечная стоимость изделия и работ.
- У материала высокий уровень водопоглощаемости (до 10 %). Из-за этого плиты испытывают незначительную линейную деформацию (до 2%). Справедливости ради стоит отметить, что это не отражается на прочности и структуре панелей. Кроме того, производители постоянно стараются исправить это негативное явление, применяя защитную пленку и делая материал более пористым. Всё это направлено на то, чтобы влага могла беспрепятственно испаряться из плит.
Сделав сравнительный анализ, упомянем о преимуществах:
- Срок службы панелей более 20 лет.
- Плиты выдерживают более 100 циклов заморозки и разморозки.
- Даже неутепленный дом получает некоторую защиту от холода зимой и не нагревается летом.
- Монтажные работы можно выполнять в любое время года.
- Богатая цветовая гамма материала, окрашенного в заводских условиях.
- Можно подобрать фактуры с имитацией природных или искусственных материалов.
- Отделка получается красивой, не требующей дополнительных финансовых вложений.
- Плиты самостоятельно очищаются от грязи во время дождя.
Теперь можно перейти к технологии монтажа.
Монтаж плит
Ознакомившись с процессом изготовления фиброцемента и фасадных панелей, рассмотрим способы их крепления. Сразу оговоримся, что технология монтажа фиброцементных панелей несложная и может быть выполнена неспециалистом.
Инструмент для работы
Для работы нужны будут как ручные, так и электроинструменты:
- Водяной уровень или лазерный нивелир.
- Строительный уровень (длина 1–2 м).
- Шуруповерт.
- Болгарка.
- Перфоратор и бур Ø10 мм.
- Электродрель и сверла Ø4 мм.
- Алмазная или торцовая пила, которой нужно будет подрезать некоторые листы.
- Рулетка (длина измерительной ленты 5–10 м).
- Строительный нож.
- Ножницы по металлу.
- Металлический угольник.
- Просекатель.
- Молоток.
- Правило длиной 2–2,5 м (или алюминиевая рейка).
Изготовление металлического каркаса
Заготовив инструмент, приступим к подготовке стен:
- В первую очередь нужно определить наличие, а если есть, то и величины неровностей на внешних стенах здания.
- Определяем горизонтальный уровень, высоту монтажа панелей и уровень установки отливов для фундамента.
- Нужно сделать разметку фасада для последующего монтажа кронштейнов, количество которых рассчитывается из условий, что шаг по вертикали будет 60 см, а по горизонтали ‒ 100 см. Длина кронштейна зависит от толщины утеплителя и кривизны стены.
- Согласно нанесенной разметке, производится установка кронштейнов с помощью дюбелей или анкеров. Выбор крепежа зависит от материала стен здания и проекта фасада.
- Чтобы снизить теплопотери и предотвратить контакт различных материалов, рекомендуется использовать прокладки из паронита.
- На стене крепится утеплитель.
- Поверх утеплителя накладывается защищающий теплоизолятор ‒ паропроницаемая мембрана.
- Теперь настал черед системы из профилей и направляющих. Устанавливаются по краям стены вертикальные П-образные профили.
- Затем профили закрепляются на кронштейнах заклепками (или с помощью болтов и гаек).
- Производится установка дверных и оконных коробов.
- В завершение, к профилям заклепками крепятся фиброцементные плиты.
В зависимости от вида панелей и технологии монтажа их крепление может выполняться заклепками, саморезами или кляммерами.
Процесс монтажа детально показан в видео, состоящем из нескольких частей:
Работа с каркасом из дерева
- По ширине утеплителя на доме закрепляется горизонтальная обрешетка.
- После проверки ее положения строительным уровнем, укладывается и закрепляется утеплитель, а поверх него дышащая непромокаемая пленка.
- Поверх горизонтальной обрешетки набивается вертикальная обрешетка (строго по уровню). Размер доски и расстояние между брусков обрешетки выбирается в зависимости от габаритов и веса плит. Чаще всего именно изготовитель плит предоставляет такую информацию.
- Сами же панели крепятся кляммерами или гвоздями.
- Если же панели используются как сайдинг, то они крепятся к обрешетке гвоздями. Причем верхний лист перекрывает часть нижнего, в котором забиты гвозди.
Изложенный в статье материал не является инструкцией по монтажу, а предоставлен только в ознакомительных целях.
Видео
Посмотрите видео о производстве фиброцементных плит LATONIT:
Вашему вниманию представлена инструкция по монтажу фасадных фиброцементных панелей KMEW:
Фото
20 ошибок при монтаже японских фиброцементных панелей • Самоделки своими руками
На строительном рынке в отделке фасадов жилых домов в последние годы стали очень востребованы японские фиброцементные панели. Основные особенности данного материала это прочность, пожаростойкость и экологичность. Существует несколько известных производителей японских панелей: KMEW (Кемью), NICHIHA (Нитиха), Konoshima (Коношима), Toray (Торей). Продукция по основным функциям всех производителей идентична, но имеются различия в сырьевых компонентах, покрытиях и незначительные отличия в размерах панелей.

В данной статье расскажем вам об основных ошибках при монтаже японских панелей. Надеюсь данная статья пригодится как мастерам по фасадам, так и заказчикам, которые планируют контролировать процесс монтажа самостоятельно.
Основные ошибки при монтаже японских фиброцементных панелей:
1 — Все сделаю сам! (Дизайн, подсчет материалов)
Рекомендуем обратится в компании по продаже японских панелей, которые вам помогут с дизайном и подсчетом всех материалов, чтобы избежать лишних трат. Следует учесть, что доставка материалов из Японии осуществляется в пределах 3-4 месяцев. Соответственно если будет просчет в материале можно упустить драгоценное время.
2 — Неправильно подобранный крепеж для крепления подконструкции (обрешетки).

3 — Некачественный материал при устройстве обрешетки из деревянных брусков.
Деревянные бруски должны быть сухими, ровными и хорошо обработаны антисептиком.
4 — Хранение панелей плохо организовано.

5 — Отсутствие вентилируемого зазора между панелью и утеплителем.
Обязательно необходимо предусмотреть вентзазор не менее 40 мм между утеплителем и тыльной стороной панели. Между бруском (профилем) и утеплителем расстояние не менее 20 мм. Эти зазоры обеспечат беспрепятственную вентиляцию воздухом и вывод водяных паров из утеплителя.

6 — Начало установки панелей выполнено сразу от отмостки.
Необходимо обеспечить минимальное расстояние от отмостки 20-30 мм. Что обеспечит вентиляцию фасада, защитит панели от обледенения и предотвратит повреждения от движений отмостки при различных погодных условий.

7 — Плохо выровнен первый ряд панелей по контуру здания.
В следствие чего выполнить углы ровными не получится, так как будет происходить смещение всех панелей от вертикали.
8 — При монтаже панелей не соблюдается минимальное расстояние от края при закреплении саморезом или гвоздем.
Данное расстояние должно быть не менее 35-45 мм. Если в процессе монтажа расстояние будет меньше возможно образование сколов и трещин по краям панелей. Также эти дефекты могут произойти не сразу, а уже в последствии ветровых нагрузок (давления ветра).

9 — Засверливание саморезов в панель без подготовки отверстий.
Отверстие для саморезов необходимо подготовить, предварительно засверлив его зенкером со сверлом. Это нужно чтобы шляпка самореза устанавливалась вровень с плоскостью панели.

10 — Уменьшение количества крепежа при монтаже панелей.
Согласно рекомендациям производителя для панелей толщиной 14 мм необходимы три точки крепления по вертикали (гвоздь, саморез) и с шагом по горизонтали не более 500 мм. Для панелей 16(18) мм первый ряд панелей устанавливается на стартовую планку длиной около 3 метров, а сверху панель и последующие выше ряды закрепляются кляммерами с шагом по горизонтали не более 600 мм. Уменьшение количество точек крепления может в дальнейшем привести к деформациям панелей.
11 — Монтаж второго ряда панелей одновременно с первым рядом.
Устройство панелей второго ряда правильно начинать только после полного монтажа первого ряда. Так как исправление неровностей по высоте в дальнейшем приведет к демонтажу всех панелей.
12 — Углы «под запил» выполнены не правильно.
Ошибка в подготовке углов является в запиле панелей ровно под 45 без среза фаски. Это приводит к невозможности правильно нанести герметик (силикон) в шов угла.

13 — Сборка панелей впритык без соединительных планок и герметика.
Такая установка панелей запрещена, так как данные разрывы необходимы для обеспечения температурных расширений материала. Если пренебречь данному правилу, то в дальнейшем возможны различные деформации торцов панелей (сколы, трещины, смещения панелей). Планка с герметиком компенсирует все деформации при расширении материала панелей.

14 — Установка панелей вплотную к металлическим откосам.
При стыковке панелей и откосов необходимо оставлять руст 10 мм. Он необходим для учета температурных расширений материалов.

15 — Неправильное сопряжение панелей с кровлей.
Стандарты правильного сопряжения панелей с кровлей:
1) Если при устройстве верхнего ряда панелей подшивка кровли еще не смонтирована, то необходимо оставить выпуски панелей выше чем линия будущей подшивки на 40-50 мм. При таком варианте планка софитов крепится непосредственно сквозь панели к обрешетке (подсистеме).
2) Если подшивка уже готова, то применяется финишная планка, которая закрывает верхние торцы панелей.
16 — Открытые и срезанные края панелей без защитной обработки.
Все торцы и срезы панелей должны обрабатываться гидрофобным раствором, для защиты от влаги.
17 — Неправильное использование праймера.
Обязательно после нанесения праймера выдержать время для полного высыхания (не менее 20 мин), только после этого наносить герметик (силикон). Если герметик нанести раньше, то возможно отслоение герметика от панелей.

Если после нанесения праймера прошло более 6 часов, то необходимо нанести его заново.
18 — Перед нанесением герметика не проведены работы по защите лицевой стороны панелей.
Обязательно перед нанесением герметика проклеить малярным скотчем весь стык панелей с двух сторон и плотно прогладить его по всем неровностям фактуры. После нанесения герметика удалить скотч.

19 — Герметизация швов панелей в холодное время года.
Если монтаж панелей производится при температуре воздуха ниже +5С , то герметизацию швов лучше перенести на более теплое время года.
20 — Использование других расходных материалов: герметик, краска, шпаклевка.
Не рекомендуется использовать расходные материалы других производителей, отличных от панелей. Так как сложно подобрать материалы с такими же свойствами и составом, которые будут выполнять все те же функции и сохранять свои свойства на протяжении длительного времени.
Заключение
Монтаж японских фиброцементных панелей требует профессионализма от исполнителей. Наличие опыта и грамотный подход приведет к положительному результату. Поэтому советуем серьезно подойти к изучению инструкции по монтажу или обратиться к проверенным монтажникам, чтобы в итоге получить красивый и качественный вентилируемый фасад дома.
samodelof.ru
Фиброцементный волокнистый сайдинг своими руками… — Блоги
Главная > Блоги > Фиброцементный волокнистый сайдинг своими руками…Внешняя отделка своей дачи является довольно таки сложным и щепетильным процессом, лично я очень долго не мог выбрать конкретную внешнюю отделку для своего загородного дома. Сам дом мой построен из ракушечника в два этажа, в общем, хорошенький домик, однако как сделать его фасадную отделку я долго не знал. Решал этот вопрос почти шесть месяцев, с одной стороны хотелось сделать что-то уникальное, чтобы всем очень нравилось, но с другой стороны, разумеется, хотелось сделать отделку очень недорогую. Пересмотрел ряд сайтов в Интернете и обошел точно больше пятисот домов, прежде чем остановиться на конкретном выборе внешней отделки. Просто штукатурить стены и затем их покрасить мне показалось слишком простым и не привлекательным, тем более что почти все дома со штукатуркой имеют не привлекательные трещины, то есть любая штукатурка уже через 1…3 года дает трещины и потом просто осыпается.
Хотелось также облицовывать кирпичом дом, но это удовольствие стоит дороговато, во всяком случае, для моей зарплаты. Однако нашел я недалеко от города то, что искал! Это был одноэтажный домик, отделанный деревянным сайдингом, поговорив с хозяином, узнал, что такое удовольствие совсем не дорогое. Также смотрится такая отделка дома очень красиво и эстетично, тем более отделка такая еще и очень долговечная, по словам хозяина этого домика, сайдинг он сделал еще около десяти лет назад, но держится такая отделка просто превосходно и сегодня. Наконец-то я спустя годы поиска наилучшей отделки дома нашел все-таки эстетичный и в тоже время простой и недорогой вариант. В общем, решено, — делаю сайдинг, осталось только выбрать какой материал применять. Деревянный сайдинг я решил точно не делать, по той причине, что с деревянной отделкой на улице, во всяком случае, я так считаю, могут возникнуть множество проблем, то есть дерево особенно на улице требует слишком тщательно ухода. Вариант с сайдингом из металла мне также показался не очень эффективным. Но нашел на одном сайте очень интересный вариант из фиброцемента (цементный сайдинг), — наконец-то вариант отделки фасада дачи найден, этот вариант действительно очень привлекателен и красив, а также очень долговечен.
Сайдинг на основе цемента делается из специальной смеси высококачественного цемента и универсального целлюлезного волокна. Такая отделка уникальна и хороша по многим показателям, во-первых, такая отделка не горит, она не требует особенного ухода как отделка из дерева, а также прослужит точно не одно десятилетие. Единственно он немного дороже стоит, чем металлическая отделка, но эта разница довольно незначительная. Почему я выбрал цементный сайдинг, поймет меня любой строитель, то есть пластины такой облицовки, я делал просто сам у себя же на даче. Сложного тут ничего нет, просто сделал ряд форм, залил их бетоном и утопил в форму целлюлезное волокно, вот и все. Если захотите сделать также сами себе такие пластины для отделки, то продумайте заранее все размеры и необходимые отверстия при литье, иначе разрезать бетонные армированные пластины, потом будет не просто. Еще один совет — все знают, что бетон жадно пьет воду, поэтому чтобы пластины не набирали вес за счет впитанной влаги, покройте их водонепроницаемым составом, например, можно просто покрасить пластины.
poremontu.ru
Меняем свойства бетона добавлением фибры
Фибробетон в среде строителей давно не новинка, и его применение в промышленном строительстве привнесло дополнительную прочность объектам. На что можно рассчитывать дачникам и владельцам загородного жилья? Такой бетон значительно облегчает строительство дома, реставрационные работы.
Применение фибры – дополнительного компонента в традиционном бетоне позволяет отказаться от каркасного армирования, поскольку дисперсные волокна из различных материалов обеспечивают внутреннее армирование бетонной смеси. Бетонные блоки, благодаря дополнительной прочности, можно уменьшить в толщине.
Обеспечивая прочность всего объема бетона, армирующие волокна так же помогают избавиться от недостатков традиционного материала из смеси цемента и песка – появления трещин, сколов и слабой прочности на растяжение.
Возможность использовать разные пропорции и типы (виды) фибры делают фибробетон универсальным. Чуть ранее мы рассматривали, как сделать самому тротуарную плитку из самой простой смеси цемента, песка, воды. Добавление фибры позволит придать такой плитке прочность, а значит долголетие всем дорожкам и площадкам, выложенным из самодельной плитки, снизить расход цемента.
Такой раствор можно применять тогда, когда нет возможности провести армирование металлическим каркасом, для создания прочных, но легких элементов архитектуры, для заливки фундамента и установки шумо-поглощающего забора. Для каждой поставленной задачи можно подобрать соответствующий вид фибры.
Что такое фибра для бетона, и какие фибры используются сегодня
Дисперсное волокно – фибра для бетона условно делится на два вида:
- Металлическая фибра изготавливается из стали, она усиливает бетон на разрыв, растяжение, предотвращает образование трещин, принимая возникающие нагрузки на себя. Снижает возможность усадки при сушке.
Сталефибробетон стойкий к перепадам температурных режимов, в воздействию влаги. Волокна из стальной проволоки могут быть с анкерами (загнутыми кончиками) – анкерная стальная фибра. Дисперсное армирование такой фиброй снижает расход цемента, но значительно повышает прочность любых, даже самых сложных по конфигурации зданий, фундаментов, где трудно применить каркасное армирование. Размеры фибры варьируются в зависимости от области использования бетона.
- Неметаллическая фибра, это целый ряд видов волокон, который пополняется с каждой новой разработкой. Прогресс не стоит на месте и помимо натуральных: стеклянных, асбестовых, базальтовых волокон, производители используют синтетические материалы: пропилен, акрил и другие.
Больший спрос имеют фибры из стали, стекла, полипропилена, именно они считаются самыми востребованными. Каждый вид обладает своими уникальными характеристиками. Базальтовая фибра — достойный конкурент стальному аналогу, а по некоторым параметрам и превосходит стальную. Но цена на базальтовую дисперсную добавку пока выше из-за сложных технологий производства. Там, где нужна особая прочность, применяют стальную фибру.
Для создания облегченных архитектурных форм, устойчивых к внешним воздействиям, химическим веществам, сколам, трещинам, изготавливают бетон с добавкой фибры из полипропилена. Фибра из полипропилена востребована при изготовлении ячеистого бетона, пеноблоков.
Стеклофибробетон упругий и пластичный, прекрасно гасит шумы, устойчив к влаге и ударным нагрузкам. Не боится перепадов температуры. Но стекловолокно нуждается в защите от щелочной среды бетона. Достигается защита добавлением специальных полимеров в состав бетонного сырья.
Как производят фибробетон кустарным способом
Производство фибробетона имеет свои особенности. На каждый вид фибры существует своя технология замеса. И если на производстве все отработано и рассчитано, имеется специальное оборудование, то — как изготовить фибробетон кустарным способом?
Фибробетон изготавливается без использования щебеня, гравия. Основными компонентами являются цемент, песок (обязательно чистый) и фибра. Для получения более качественного раствора желательно применение пластификатора.
Основным и общим требованием остается тщательный замес с равномерным распределением компонентов. Обеспечить качество раствора поможет бетономешалка, наличие пластификатора в составе и увеличенное время замеса. Фибра вводится в раствор несколькими методами. В сухую смесь, в цемент и в замешиваемый раствор. Приготовление раствора мы рассмотрели в статье «Как изготовить самому тротуарную плитку».
При самостоятельном изготовлении фибробетона небольшими партиями, неметаллическую фибру для более равномерного распределения удобней вводить в сухую смесь, желательно порционно, при этом контролировать, чтобы фибра не «комковалась». Добавляя волокна фибры, необходимо следить, чтобы она была взрыхленной.
Стальные волокна (для равномерного распределения) рекомендуется вводить в готовую смесь. Следует учесть, что стандартное оборудование подвергается большему износу при изготовлении бетона со стальной фиброй.
Пропорции армирующих волокон на 1 м3 зависит от предъявленных требований к бетону, от материалов наполнителя. Минимальное содержание фибры изменит характеристики бетона к более высоким показателям. Для снижения стоимости бетона, изготовленного самостоятельно, можно использовать смеси дорогого и дешевого наполнителя из армирующих волокон.
Строительные работы не ограничиваются изготовлением бетона. Наша строительная компания предлагает ряд услуг в области строительства. Вы можете вызвать мобильную бригаду рабочих для работ связанных с обустройством рабочей площадки, загородного участка, ремонтом или строительством. Также мы проводим утепление эковатой любых строений или элементов дома. Целлюлозный утеплитель от производителя обладает уникальными характеристиками и не имеет торговых надбавок.
9999812.ru
Фиброцемент своими руками пропорции — Портал о стройке
Бетон на загородном участке применяется для сооружения фундаментов, цокольных этажей, стен хозпостроек, дорожек, бассейнов и т. д. Большие объемы этого строительного материала заказываются на предприятиях, занимающихся его изготовлением. Чтобы соорудить небольшую хозяйственную конструкцию и при этом сэкономить средства, можно изготовить бетон своими руками.
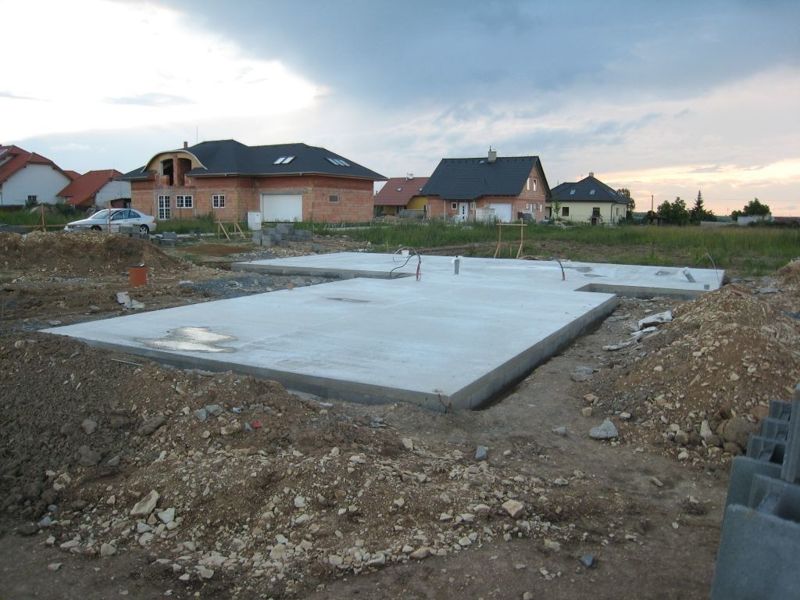
На загородном участке бетон служит для фундамента домов, изготовления садовых дорожек, бассейна и т.д.
Если вы хотите получить качественный бетон, необходимо найти ответы на три самых важных вопроса:
- Какую марку нужно получить?
- Какие пропорции компонентов следует соблюсти?
- Как приготовить состав?
Содержание статьи:
Выбор марки
Для выбора марки, необходимого для возведения конкретного объекта, лучше получить консультацию у осведомленного человека. Марка имеет значения в диапазоне от М50 до М1000. На практике эти цифры ограничены в интервале М100-М500. Значение цифры усреднено показывает предел прочности материала при сжатии куба из бетона с размерами сторон 200 мм. Прочность бетона указывается с учетом его затвердевания в течении 28 суток в нормальных условиях и выражается в единицах кгс/см2.
В современной классификации используется также параметр “класс”. В отличие от марки он указывает не усредненное значение прочности, а гарантированное. Но для хозяйственного строительства особой разницы в использовании вида характеристик бетона нет. Другие буквенные обозначения указывают на следующие свойства бетона:

Марки М300-М350 – основной материал для плит перекрытия, балок и других жб конструкций.
- В – класс по прочности;
- W – давление воды, которое сможет выдержать материал;
- F – число циклов заморозки-разморозки, выдерживаемое конструкцией из бетона.
Общепринятое соответствие марки сооружаемым объектам следующее:
- Марки М100-М200 используют для подготовки перед заливкой лент фундаментов. На подушку из песка или гравия небольшим слоем заливают бетон М100 и после его схватывания производят армирование. М150 применяется для бетонирования садовых дорожек.
- Марки М200-М250 применимы для установки подпорных стен, монолитных фундаментов, обустройства площадок и дорожек.
- Марки М300-М350 являются основным материалом для колонн, балок, плит перекрытий и других железобетонных изделий.
- Бетон более высоких марок предназначен для особо прочных конструкций: элементов мостов, чаш бассейнов, гидротехнических сооружений и пр.
Для выполнения работ небольшого объема нет необходимости в точном соответствии маркировки бетона и возводимого объекта. В большинстве случаях универсальными являются марки М200 и М250.
Пропорции компонентов

Таблица пропорций компонентов бетонной смеси.
Изготовление бетона своими руками – процесс, при котором необходимо учесть пропорции всех компонентов, входящих в состав смеси. Основным является водоцементное соотношение (В/Ц). Идеальной считается смесь с содержанием 25-30 % воды. Но изготовив бетон в такой пропорции, мы получим слишком сухую смесь, которую впоследствии практически невозможно будет уложить. Воду в состав добавляют с некоторым избытком.
Завышенный процент водной составляющей приведет к образованию пор при ее испарении, что станет причиной снижения прочности материала.
Определить водоцементное соотношение при приготовлении требуемой марки бетона можно по следующей таблице:
Марка портланд-цемента | Марка бетона | |||||
300 | 250 | 200 | 150 | 100 | 75 | |
600 | 0,62 | 0,70 | 0,78 | — | — | — |
500 | 0,56 | 0,62 | 0.71 | 0,78 | — | — |
400 | — | 0,55 | 0,62 | 0,75 | 0,89 | — |
300 | — | — | 0,56 | 0,68 | 0,79 | 0,88 |
200 | — | — | — | 0,62 | 0,76 | 0,86 |
По данным таблицы, к примеру, можно определить, что для приготовления бетона марки М250 из цемента марки 400 необходимо выдержать пропорции В/Ц=0,62/1.
Наполнители для смеси

Схема наполнителей для бетонной смеси.
Определив пропорции воды и цемента, нужно просчитать объем и состав наполнителей смеси. От этих значений будет зависеть важный показатель свойств – пластичность (удобоукладываемость). Чем больше состав смеси содержит наполнителя, тем сложней будет проводить работы по его укладке. Переизбыток цемента в смеси может привести к деформации структуры в процессе усадки. Для строительства жилых строений применяются только наполнители природного происхождения. К ним относятся: щебень, песок, гравий и пр. В них не должно быть синтетических составляющих и пыли.
В песке не должно быть присутствия глины, ее пластичность отрицательно сказывается на свойствах. Лучшим вариантом является использование намывного песка. Заполнители различаются по размеру частиц. Желательно добавлять крупнозернистый песок. Иногда его смешивают с мелкозернистым, т. к. он дешевле по цене. Искусственные заполнители (шлак) применяют для сооружений, не требующих особой экологичности. Их применение снижает срок эксплуатации сооружения.

Гранитный и гравийный щебни являются самыми прочными и морозостойкими наполнителями бетонной смеси.
Гранитный и гравийный щебни более прочны и морозостойки, но и выше по стоимости. Желательно применять мелкие фракции наполнителя – 5-20 мм. Доломитовый и известняковый щебень используются при изготовлении низких марок, без повышенных требований к свойствам. Вода для замеса должна быть без солей и посторонних агрессивных химических примесей.
Пластичность раствора определяется методом осадки смеси в конусе. Конус – специальная металлическая емкость без дна соответствующей формы. Нижний ее диаметр равен 20 см, верхний -10 см, высота – 30 см. Конус заполняется изготовленным бетоном с тщательным штыкованием для удаления воздушных полостей.

Схема определения пластичности раствора.
После заполнения емкость снимается и устанавливается рядом с полученной горкой. По верхнему краю конуса определяется, на сколько сантиметров произойдет усадка горки от изначальной высоты. Состав считается малоподвижным, если высота конуса из раствора не изменилась или уменьшилась менее чем на 6 см. Бетон такой структуры используют для укладки фундамента с нечастым армированием и усиленной трамбовкой. Более широкое применение у смеси, которая осаживается на 7-12 см. Изготовленный бетон считается пригодным для сооружения монолитных конструкций, если образец уменьшился по высоте на 13-18 см.
Пропорции компонентов для смеси по соотношению В/Ц для определенной марки цемента можно подобрать по таблице. Данные приведены для изготовления бетона с осадкой конуса 7-12 см.
Тип наполнителя | В/Ц | Состав бетона по объему (цемент, песок, наполнитель) | Расход компонентов на 1 м3 бетона | |||
Вода, л | Наполнитель, м3 | Песок, м3 | Цемент, кг | |||
Гравий | 0,5 | 1:1,3:2,7 | 176 | 0,80 | 0,38 | 352 |
0,55 | 1:1,4:3,1 | 176 | 0,83 | 0,37 | 320 | |
0,6 | 1:1,6:3,3 | 176 | 0,81 | 0,39 | 294 | |
0,65 | 1:1,8:3,6 | 176 | 0,86 | 0,43 | 270 | |
0,7 | 1:2,0:3,8 | 176 | 0,80 | 0,42 | 252 | |
0,75 | 1:2,2:4,1 | 176 | 0,80 | 0,43 | 235 | |
0,8 | 1:2,4:4,4 | 176 | 0,80 | 0,43 | 220 | |
0,85 | 1:2,5:4,5 | 176 | 0,78 | 0,43 | 208 | |
Щебень | 0,5 | 1:1,4:2,7 | 198 | 0,90 | 0,46 | 396 |
0,55 | 1:1,7:2,9 | 198 | 0,87 | 0,51 | 360 | |
0,6 | 1:1,9:3,1 | 198 | 0,85 | 0,52 | 330 | |
0,65 | 1:2,1:3,3 | 198 | 0,83 | 0,52 | 304 | |
0,7 | 1:2,3:3,5 | 198 | 0,82 | 0,54 | 282 | |
0,75 | 1:2,5:3,6 | 198 | 0,79 | 0,55 | 264 | |
0,8 | 1:2,8:3,8 | 198 | 0,78 | 0,58 | 248 | |
0,85 | 1:3,1:4,0 | 198 | 0,77 | 0,6 | 232 |
Пример. Если необходимо приготовить 1 м3 бетона марки М200 средней подвижности, имея в наличии цемент марки 400, щебень и песок, в первой таблице находим водоцементное отношение для этих марок. Оно равно 0,62. Во второй таблице находим пропорции цемента, песка и щебня для В/Ц=0,6. Их соотношение 1:1,9:3,1. Состав компонентов будет 330 кг, 0,54 м3, 0,85 м3 соответственно с добавлением 198 литров воды.
Приготовление раствора

Приготовление бетонной смеси схема.
Определив пропорции всех компонентов, изготавливаем бетон своими руками. Сначала смешивают песок и цемент. За счет сыпучей структуры их легче перемешать между собой. Затем в состав добавляют воду небольшой струей. И лишь добившись однородности замеса, его соединяют с наполнителем периодически добавляя воду.
Смесь должна быть тщательно перемешана и иметь консистенцию густого творога. Если гребни смеси при их создании лопатой не осаживаются и имеют гладкую поверхность, значит бетон приобрел нужную консистенцию. Процесс замешивания должен проходить при положительных температурах.
Для облегчения процесса используются компактные бетономешалки, которые можно взять напрокат. В барабан машины загружают половину объема наполнителя и наливают воду. Затем поочередно порциями добавляют цемент, песок и остатки щебня или гравия. Состав должен перемешиваться в течение нескольких минут. Далее, наклонив барабан, отливают небольшое количество полученной смеси в тачку. Если материал не готов, операцию продолжают.
Недостаточно размешенные компоненты ухудшат качество будущего сооружения. Правильно приготовленный бетон при сжатии в ладони должен сформироваться с выделением небольшого количества цементного молока. Приготовленный материал необходимо выработать в течении двух часов после замеса. В период затвердевания важно не допустить промерзания бетона. Неокрепшая структура может разрушиться в результате образования льда.
Оценив затраты средств и усилий на самостоятельное изготовление бетона, можно прийти к выводу, что отказываться от покупки готового материала рационально только при незначительном объеме выполняемых работ.
Source: o-cemente.infoЧитайте также
stroyka.ahuman.ru
состав, характеристики и технология изготовления
На рынке стройматериалов предлагают новый материал – фибробетон. Он являет собой бетон, который в своем составе имеет частицы фиброволокна, от названия которых и исходит название бетона. Эти волокна исполняют роль арматуры, которая применяется с целью повышения прочности бетонного раствора. Фибробетонные вкрапления одинаковы по длине и толщине. Это позволяет равномерно распределить их во всей структуре бетона. Существует много преимуществ фибробетона. Ниже мы детально обсудим их.
Понятие и состав фибробетона
Фибробетон – это мелкозернистый материал, одним из составляющих которого является армирующий наполнитель. В прошлом с расчетом на снижение хрупкости и количества появления трещин, предпринимались меры по повышению прочности бетона. Так, строители добавляли дисперсные волокна и распределяли их равномерно по всей бетонной массе. В результате этих работ характеристики полученного бетона улучшались:
- прочность повышалась до 30%;
- стойкость к физическим нагрузкам возросла;
- трещины образовывались реже.
Различают две группы фибры:
- металлическая – исходным веществом является сталь, которая имеет различную форму и размеры;
- неметаллическая – производится из таких материалов, как стекло, акрил, хлопок, базальт, полиэтилен, карбон, углевод и другие.
Самыми популярными волокнами являются стеклянные и металлические. Однако с каждым днем все большую популярность приобретает полипропиленовая фибра. Что касается материалов из базальта и углерода, то они применяются крайне редко в связи с высокой стоимостью.
Волокна хлопка, вискозы и нейлона предают специфические особенности бетону, армированному фиброй из стали. Структура фибробетона являет собой однородную конструкцию, которая со всех сторон пронизана волокнами из различных материалов. Именно они определяют технические характеристики бетона, создают эффект армирования.
Вернуться к оглавлениюТехнические характеристики
Свойства бетона зависят в первую очередь от используемого стройматериала в производстве. Рассмотрим характеристики основных видов фибробетона. Стальная фибра – самый распространенный наполнитель. Он обладает повышенной прочностью к нагрузкам, не усаживается и не образует трещин во время службы. Наиболее примечательные его качества – длительный срок эксплуатации, плотность и стойкость к износу. Кроме того, данный фибробетон не теряет свойства под действием низких температур, влаги и огня.
Следующее в рейтинге популярности волокно из стекла. Бетон этого типа обладает высокими качествами упругости, что наделяет его пластичностью. Однако щелочная среда вредна этому материалу. Стойкость к химическому влиянию обеспечивается полимерной пропиткой, путем добавления в бетон добавок на основе глиноземистого раствора. Именно он связывает щелочи и препятствует повреждению фибробетона. В конечном варианте вы получаете раствор с высокой прочностью, устойчивостью к высоким температурам, гидроизоляцией, стойкостью к воздействию химических средств и истиранию.
Асбестовая фибра характеризуется долговечностью, стойкостью к щелочной среде, нагрузкам и термозащитными качествами. Бетон на основе базальта имеет повышенную прочность. Больше всего он подходит для конструкций, которые подвержены постоянным нагрузкам, деформации и вокруг которых существуют факторы для появления трещин.
Общие характеристики остальных типов волокон – это защита от воздействия химических веществ, прочность на деформацию, стойкость к перепадам температур и неспособность проводить электричество. Благодаря синтетичной природе материалов вес бетона снижается.
Вернуться к оглавлениюПреимущества и недостатки
Каждый материал имеет плюсы и минусы. Фибробетон не является исключением.
Вернуться к оглавлениюПреимущества
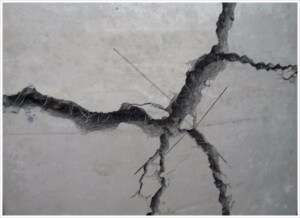
Выделяют следующие достоинства фибробетона:
- снижение затрат на строительство при использовании фибры для армирования вместо армирующей сетки или каркаса;
- высокая продуктивность работы по фибробетону;
- расход бетона с применением фибры значительно меньше;
- в отличие от остальных видов бетона фибробетон не теряет своих технических характеристик даже после окончания срока службы, поскольку благодаря фибре материал становится вязким;
- фибробетон обладает хорошими адгезионными качествами;
- фибра может применяться как в газо-, так и в пенобетонных конструкциях;
- в ходе армирования в газобетоне происходит процесс поризации и как следствие наблюдается его устойчивость;
- фибра в пенобетоне повышает его прочность.
Недостатки
На удивление, минус у этого бетона только один, а именно, высокая стоимость, если сравнивать с обычным бетонным раствором. Однако этот недостаток легко компенсируется долговечностью стройматериала и его стойкостью к износу.
Вернуться к оглавлениюОбласти применения
Учитывая вышеперечисленные технические характеристики фибробетона, этот материал стал популярным на рынке. Он применяется в конструкциях, на которые оказывается сильное давление со стороны окружающей среды. Эти конструкции могут быть как промышленного, так и бытового характера. Каждый исходный материал имеет свою сферу применения. Стальной фибробетон чаще всего применяется:
- шпалы, фундамент, мостовое покрытие, берегозащитные полосы;
- полы, тоннели;
- дороги, полосы для взлета и посадки на аэродромах, тротуары;
- тротуарная плитка, бордюрный материал;
- каркас конструкции, монолитные сооружения;
- каналы для водоотвода, шахты колодцев под канализацию, плотины, водоочистные системы;
- фибробетонные полы.
Бетон со стекловолокном используется при устройстве:
- щитов для шумозащиты;
- гидроизоляции для очистительных сооружений;
- декоративных изделий небольшого веса для отделки покрытий;
- фасадной отделки фибробетоном жилых конструкций;
- промышленных помещений, покрытия в которых подвержены загрязнению;
- заборов, скамеек, цветочных клумб и других объектов.
Базальтовый бетон является незаменимым при строительстве:
- перекрытий, фундамента, дорог;
- резервуаров, дамб, конструкций железнодорожного характера.
Фибробетон из полипропилена необходим для создания:
- конструкций из пеноблоков;
- ячеистого бетона;
- объектов небольшого веса.
Хлопковые и вискозные материалы используются при замешивании текстильбетона.
Вернуться к оглавлениюФибробетонные полы
Фибробетон часто применяется для устройства фибробетонных полов. На практике этот бетон обрел большую популярность благодаря низкому показателю хрупкости. Напольная стяжка из фибробетона и ее вид зависит напрямую от требований и марки применяемого цемента. В процессе заливки полов наибольший перепад в 2 метра равен 2 мм. Благодаря этому затраты на строительство снижаются, как и последующие работы по готовому материалу. Кроме того, процесс заливки происходит быстро, что обеспечивается благодаря пневмооборудованию.
Фибробетонные полы устраиваются в следующих типах помещений:
- промышленные и производственные;
- склады;
- автомастерские, паркинги, гаражи;
- залы для выставок и торговли;
- аэродромные и грузовые ангары;
- конструкции под офисы.
Технология изготовления бетона
Фибробетон может быть приготовлен как по стандартной промышленной технологии, так и своими руками. Второй способ — своими руками — имеет особенности. Процесс изготовления требует применения бетономешалки и дробилки. На первом этапе происходит расчет и дробление исходного материала. Песок и цемент может добавляться как после измельчения, так и в процессе перемешивания. В первом случае равномерное распределение фибры происходит быстрее в отличие от второго варианта, который требует большего количества времени.
Именно качественное распределение арматуры по всему объему раствора – это ключевое условие его качества. Изготавливая бетон своими руками, следует контролировать отсутствие скоплений фибры. С этой целью замешивание должно длиться на 30-50% дольше обычного. В процессе необходимо иногда проверять качество раствора. При соблюдении инструкции созданный бетон будет идентичен промышленному.
Вернуться к оглавлениюВывод
Вышеизложенные факты дают право утверждать, что фибробетон обладает множеством положительных свойств. Кроме того, для его изготовления и применения не требуется специальная техника. Это дает возможность данному бетону справедливо конкурировать с другими типами бетонов.
Характеристики фибробетона позволяют использовать его при различных строительных работах. В качестве фибры могут выступать как металлические, так и неметаллические волокна.
kladembeton.ru