определение качества при приемке и после заливки
Строительство достаточно трудоемкий процесс. Чтобы исключить лишние затраты и не растрачивать время, стоит хорошо позаботиться о качестве материалов. В первую очередь необходимо задуматься о том, как проверить марку бетонной смеси.
Заказанный раствор не всегда соответствует прописанным в документе характеристикам. Если добавленное сырье для изготовления бетона не отвечает должным пропорциям, автоматически меняется качество раствора. Чтобы точно узнать марку необходимо провести оценку качества.
Как определить марку бетона
Марка бетона — показатель, показывающий предел прочности на сжатие. Для строительства пригодны марки М300-400. М100-250 обладают минимальной прочностью, годятся только для вспомогательных работ. Многое зависит от выбранного поставщика. Стоит поискать проверенные фирмы с хорошей репутацией, которые могут предоставить необходимые документы на предлагаемую продукцию. Если по каким-то причинам вы сомневаетесь в честности поставщика, стоит подумать о дальнейшем исследовании раствора на соответствие указанной марки.
Определение марки бетона может производиться разными методами:
- Лабораторная экспертиза;
- Ультразвуковой метод;
- Самостоятельная проверка.
Каждый способ различается по проценту точности и имеет определенные тонкости.
Контактные способы проверки
Контактная проверка производится двумя методами. Первый — с помощью профессионального оборудования — склерометра. Прибор определяет прочность путем ударного импульса. Склерометр бывает механическим и электронным, а его цена составляет от 10 до 35 тысяч, покупка для одноразового применения просто не рациональна для рядового покупателя.


Второй метод предполагает отправку пробы в лабораторию. Сначала необходимо провести ряд манипуляций:
- Подготовить деревянный ящик объемом 15 см³;
- Приобретенный раствор залить в форму непосредственно с лотка бетоносмесителя, ящик предварительно смочить водой. Залитый раствор уплотнить, сделав несколько проколов арматурой;
- Поместить пробу на 28 дней в такие же условия, в каких находится основная конструкция;
- Застывший образец отвозится в лабораторию для исследования. Оценку можно производить на промежуточных этапах схватывания (3, 7 и 14 дней).
Экспертиза выдаст заключение об исследовании образца этой марки, ее соответствие установленным нормам.


Ультразвуковая методика
Ультразвуковые приборы, помимо исследования прочности, используются для дефектоскопии. Скорость распространения ультразвука в бетоне достигает 4500 м/с.
Градуировочную зависимость между скоростью распространения звука и прочностью бетона на сжатие фиксируют заранее для каждого состава смеси. В случае использования 2-х зависимостей для бетонов альтернативных или неизвестных составов, может возникнуть неточность при определении прочности. На соотношение «прочность — скорость ультразвука» воздействует ряд факторов, от колебания которых в данном случае нужно отталкиваться при применении ультразвуковой проверки:
- Способ изготовления бетонного раствора;
- Количество и зерновой состав;
- Изменение расхода цемента более, чем на 30%;
- Возможные полости, трещины и дефекты в готовой конструкции;
- Уровень уплотнения бетона.

Ультразвуковая проверка подходит для массовых испытаний конструкций любой формы, а также для ведения постоянного контроля набора или снижения прочности. Минусом метода является погрешность при переходе от акустических показателей к прочностным. Ультразвуковым оборудованием не стоит проводить проверку качества высокопрочных марок, допустимый диапазон ограничивается классами В7,5…В35 (10-40 МПа), в соответствии с ГОСТом 17624-87.
Способы самостоятельной проверки
Проверка в лаборатории или специальными средствами не всегда оправдывает себя. Это касается тех случаев, когда возводится небольшая постройка на частной территории. Залитый и застывший раствор можно проверить в домашних условиях несколькими способами. Если он не будет соответствовать необходимым требованиям, можно воспользоваться платной экспертизой и возместить ущерб с поставщика.
Проверка на гладкость
Внимательно рассмотрите застывшую конструкцию. Она должна быть гладкой, наличие узоров говорит о несоблюдении правил заливки. Такой раствор скорей всего промерзал, что значительно снизит его прочность. Фактически, бетон марки М300, станет по своим свойствам как М200-250.
Тест на звонкость
Можно провести проверку по звуку удара. Для этого берется молоток или кусок металлической трубы, весом не более 0,5 кг. Здесь важна звенящая тональность при нанесении удара. Глухой звук говорит о низкой прочности и плохом уплотнении. А при появлении трещин, крошек необходимо полностью или частично заменять конструкцию.
Визуальная оценка
Способ подразумевает проверку характеристик раствора при приемке. Можно выделить такие моменты, как:
- Цвет — качественная смесь серая с синеватым оттенком, если в цементном молочке отчетливо проявляется желтизна, в смеси присутствуют глинистые примеси или шлакодобавки. Коричневый или рыжий цвет характеризуется превышением песка или заполнителя в недопустимом количестве, от раствора с неравномерным оттенком разумней отказаться вообще;
- Правильная консистенция однородна, без комков и сгустков и напоминает увлажненную почву;
- Излишки воды — определяются заливкой небольшого количества смеси в котлован, должна получиться лепешка без слоев и трещин;
- Купленный раствор ненадлежащего качества начинает расслаиваться еще при транспортировке, смесь не получается извлечь лопатой или подать через рукав.
Если доставлен миксер, определить качество бетона без осмотра можно только по предоставленным документам. В данном случае все зависит от добросовестности продавца.
Проверка бетона молотком и зубилом
Молоток и зубило самый простой ответ на вопрос как проверить качество бетона заливки. Для этого проводится тест на удар с помощью молотка. К поверхности полностью засохшего фундамента приставляется зубило, и наносится удар в среднюю силу. Если полученная вмятина превышает 1 см, класс прочности В5 (М75), менее 0,5 см — В10 (М150). Небольшая вмятина остается на В15-25 (М200-250), на В25 (М350) появляется незначительная отметина.
Необходимо брать молоток весом 300-400 гр.
Все описанные способы имеют свои достоинства и недостатки, для точности результата стоит обратиться за помощью к специалистам. Лабораторное, ультразвуковое и ударно-импульсивное исследования более достоверные и исчерпывающие. Качество напрямую зависит от характеристики составных компонентов, соблюдения пропорций, условий хранения и транспортировки. Поэтому обезопасить себя можно выбором проверенного поставщика с хорошей репутацией, это значительно снизит риск возникновения проблем в будущем.
Определение марки бетона
Если выполняется строительство любого типа объекта, то одним из тех материалов, которые требуются практически в любом случае, является бетон. Соответственно, возникает большое количество вопросов, касающихся определения характеристик состава. Вы хотите определиться с тем, насколько эффективна та, или иная смесь, а также удовлетворяет ли она требованиям? В сети можно найти большое количество материала по поводу того, как осуществляется определение марки бетона. К сожалению, все описанные способы являются косвенными и правильный результат способно обеспечить только проведение экспертизы. Любая другая методика того, как определить марку бетона, является неэффективной. В лучшем случае, она предоставит только приблизительный результат с высокой степенью погрешности. Если требуется определить марку бетона и определить его эксплуатационные характеристики, следует дождаться решения специализированной лаборатории. В неё команда специалистов осуществит ряд анализов, направленных на выявление параметров испытуемого объекта. После того, как подобные мероприятия будут осуществлены, клиенту выдаётся на руки документ. В нём записана вся необходимая информация. Следует отметить, что подобный процесс имеет массу факторов, а также особых моментов, требующих освещения.
Прежде всего, определить марку бетона может потребоваться тогда, когда состав прибывает на строительную площадку в автобетоносмесителе, цистерне или же самосвале. К сожалению, нет методики, позволяющей обеспечить немедленное предоставление информации о том, какими характеристиками будет обладать смесь после её застывания и превращения в монолитную массу. Чтобы определить марку бетона, необходимо взять несколько контрольных образцов. Перед тем, как переходить к этому мероприятию, следует рассказать про сам процесс получения состава с завода. Машина прибывает вместе с документами на смесь и если таковые отсутствуют, это считается серьёзным нарушением. Дополнительно, материал должен полностью соответствовать требованиям государственного стандарта. Если проверка выявит, что характеристики реального состава отличаются от того, что идёт по документам, то предприятие ждут проблемы. Чтобы быть уверенным в соответствии параметров и не задумываться над тем, как определить марку бетона, стоит закупаться только у проверенных производителей. Наша компания оказывает свои услуги уже многие годы. За столь продолжительный период мы смогли заработать репутацию фирмы, которая заслуживает доверия. Клиентом всегда предоставляется именно тот бетон, марку которого они заказывали. Дополнительно, мы не практикуем недовоз, поскольку в своей работы ориентированы только на заказчика, а не получение максимально возможной прибыли.
Если вернуться к рассмотрению того, как определить марку бетона, то необходимо создать опалубку для кубиков из завезённого состава. Она довольно проста по своей конструкции и позволяет обеспечить придание требуемой формы смеси. Прежде всего, необходимо уложить бетон в несколько кубиков. Не следует делать их в малом количестве, поскольку это может привести к неточному результату и слишком высокой погрешности. Большое число испытуемых, аналогично, не является логичным. Для того, чтобы узнать характеристики состава после его твердения и быть уверенными в достоверности данных, следует создать около 5-6 образцов. Когда необходимо задуматься над тем,
Когда на бетонный куб оказывается давление, то оно постоянно возрастает. С увеличением данного параметра происходит увеличение вероятности механического разрушения. Марка представляет собой максимальный показатель давления, после которого происходит полное разрушение изделия и дальнейшее использование невозможно. Стоит отдельно заметить, что других надёжных и на сто процентов достоверных способов того, как определить марку бетона не существует. Лабораторное исследования является проверенным методом, что следует учитывать при решении задач этого типа.
Марки бетона определение
Как определить класс и марку бетона?
Главная|Полезные статьи|Как определить класс и марку бетона?
Дата: 30 декабря 2016
Просмотров: 1316
Коментариев: 0
Строительство объектов любого типа, независимо от материалов, из которых они изготавливаются, производится с применением бетона. У застройщиков возникает множество вопросов, связанных с определением характеристик смеси. Главные показатели бетонного состава – марка бетона и его класс. Это основные параметры, на которые обращают внимание заказчики, приобретая раствор.
Разбираясь в характеристиках, можно избежать проблемных ситуаций, связанных с финансовыми затратами и конфликтов с поставщиком раствора. Ведь надежной базой любой постройки является прочное основание, которое не осядет, не вызовет появления трещин.
Определение марки бетона позволяет принять решение об эффективности применения смеси. Лабораторные методы контроля обладают высокой точностью. Замеры производят специализированные лаборатории. Выполнение замеров актуально, когда смесь доставляется на стройплощадку. Тогда необходимо определить, какими характеристиками она будет обладать после того, как превратится в монолит. Рассмотрим особенности определения качественных характеристик.
Подготовка образцов
Стандарт регламентирует определение предела прочности бетонного состава на сжатие путем контроля отлитых кубических образцов.
Значение класса бетона по прочности является его основной характеристикой, которую используют при расчете конструкций
Подготовку эталонов выполняйте в следующем порядке:
- подготовьте из древесины порядка пяти специальных форм кубической формы, обеспечив размер стороны 10, 15 или 20 сантиметров в зависимости от лабораторного оборудования, на котором будет осуществляться проверка;
- увлажните внутреннюю поверхность деревянного ящика, смочив его водой или нанеся специальную смазку. Это обеспечит нормальное протекание гидратации, позволит легко извлечь образцы;
- залейте в группу форм смесь, применяя методику послойной укладки состава;
- удалите воздушные полости, тщательно проштыковав раствор, уплотнив его. Образец выдерживайте на протяжении 28 суток.
Выбирая для выполнения строительства необходимый раствор, ориентируйтесь на его класс и марку, характеризующие прочность.
Изменение прочности
Образцы, по которым определяется марка состава, предохраняйте от повреждений, храните при положительной температуре (20 градусов Цельсия), влажности порядка 90%. Прочность – характеристика, которая изменяется в процессе затвердевания. Помните, что она увеличивается с течением времени следующим образом:
- Спустя 7 дней после заливки прочность достигает 70 процентов проектного значения. Ускоренный метод контроля позволяет предварительно определить прочность образцов-эталонов через неделю после заливки. Например, предварительное значение средней прочности для бетона марки М200 составляет 140 кг/см ².
- Эксплуатационные характеристики материал приобретает после затвердевания через 4 недели.
- Процесс приобретения окончательной твердости исчисляется годами.
Марка и класс бетона характеризуют его прочность на сжатие
Классификация бетонных составов
Марка бетона характеризует предел прочности образца на сжатие, измеряется в килограммах на сантиметр квадратный. Причём эталон должен на протяжении 4 недель пройти выдержку. Цифровой индекс, указанный в марке бетонной смеси, характеризует усредненное значение параметра, зависит от объемной доли цемента в составе. Диапазон изменения марок состава расположен в интервале от М50 до М1000. Область использования бетона изменяется в зависимости от маркировки, характеризующей прочность:
- Работы, связанные с бетонированием, подготовка фундаментных лент, установка бордюров производится составом М100, соответствующим классу В7,5.
- Заливка полов, подготовка фундаментов малоответственных объектов, выполнение стяжек, бетонирование площадок производится с помощью товарного раствора класса B12,5, соответствующего марке М150.
- Подготовка фундаментов объектов, бетонирование лестниц, выполнение отмосток, опорных стенок осуществляется раствором М200 и М250 (классы В15 и В20).
- Индивидуальное жилищное строительство, постройка промышленных объектов, заливка монолитных конструкций выполняется на базе смесей М300 (В22,5)-М350 (В25), которые имеют наибольшее распространение.
- Постройка объектов гидротехнического назначения, специальных сооружений банковской сферы, конструкций, к которым предъявляются особые требования, выполняется прочным бетоном М 400.
- Возведение специальных объектов, требующих сверхпрочного состава, производится с использованием смесей маркировкой 500 и выше.
Требования к бетону в нормативных документах указываются именно в классах, но при заказе бетона строительными компаниями бетон обычно заказывается в марках
Окончательное представление о прочностных характеристиках бетонного массива позволяет получить классификация по классам. Класс смеси учитывает допустимое значение погрешности качества раствора, характеризует реальную твердость массива.
Класс бетона обозначается заглавной буквой «В» и цифровым индексом, находящимся в интервале от 3,5 до 80. Наиболее распространённым диапазоном смеси по классам является интервал от В7,5 до В40.
Прочностной показатель состава характеризуют результаты испытаний эталонного образца. Значение параметра определяется:
- объемом и маркой вяжущих компонентов в растворе;
- удельным весом смеси;
- типом применяемого наполнителя.
Таблица соотношения классов и марок бетона
Современный строительны
Определение прочности бетона — методы проверки и приборы
Прочность бетона — важнейшая характеристика, которая применяется при проектировании и расчете конструкций для строительства различных сооружений. Она задается маркой М (в кг/см²) или классом В (в МПа) и выражает максимальное давление сжатия, которое выдерживает материал без разрушения.
При определении марочной прочности бетона строительные организации и изготовители конструкций должны руководствоваться требованиями нормативных документов — ГОСТ 22690-88, 28570, 18105-2010, 10180-2012. Они регламентируют методику проведения испытаний, обработку результатов.

Что влияет на прочность?
Затвердевшая в условиях строительной площадки бетонная смесь может давать отличные от лабораторных результаты. Помимо качества цемента и заполнителей на характеристику влияют:
- условия транспортировки;
- способ укладки в опалубку;
- размеры и форма конструкции;
- вид напряженного состояния;
- влажность, температура воздуха на всем протяжении твердения смеси;
- уход за монолитом после заливки.
Качество смеси и ее прочностные характеристики ухудшаются, если при производстве работ совершались грубые нарушения технологии:
- доставка производилась не в миксере;
- время в пути превысило допустимое;
- при заливке смесь не уплотнялась вибраторами или трамбовками;
- при монтаже была слишком низкая или высокая температура, ветер;
- после укладки в опалубку не поддерживались оптимальные условия твердения.
Неправильная транспортировка приводит к схватыванию, расслоению и потере подвижности смеси. Без уплотнения в толще конструкции остаются пузырьки воздуха, которые ухудшают качество монолита.
При температуре 15°-25°С и высокой влажности в первые 7-15 суток бетон достигает прочности 70%. Если условия не выдерживаются, то сроки затягиваются. Опасно как охлаждение смеси, так и ее пересушивание. Зимой опалубку утепляют или прогревают, летом поверхность монолита увлажняют, накрывают пленкой.
На заводах ЖБИ осуществляют пропаривание или автоклавную обработку конструкций, чтобы уменьшить время набора прочности. Процесс занимает от 8 до 12 часов.
Чтобы определить, насколько характеристики конструкции соответствуют проектным, а также при обследованиях и мониторинге технического состояния зданий проводят проверку прочности бетона. Она включает лабораторные испытания образцов, неразрушающие прямые и косвенные методы исследования объектов.
Факторы, влияющие на погрешность измерений при контроле и оценке прочности бетона:
- неравномерность состава;
- дефекты поверхности;
- влажность материала;
- армирование;
- коррозия, промасливание, карбонизация внешнего слоя;
- неисправности прибора — износ пружины, слабую зарядка аккумуляторной батареи.
Самый информативный способ проверки бетонных конструкций — изъятие образцов из тела монолита с последующим их испытанием. Такой метод сводит к минимуму ошибки, но достаточно дорог и трудоемок. Поэтому чаще пользуются более доступными исследованиями с помощью приборов, измеряющих зависимые от прочности характеристики — твердость, усилие на отрыв или скол, длину волны. Зная их, можно с помощью переходных формул вычислить искомую величину.

Требования к проверке
С точки зрения заказчика наиболее предпочтительно проводить испытания неразрушающими методами контроля фактической прочности бетона. Сегодня созданы приборы, которые позволяют быстро получить результаты без бурения, высверливания или вырубки образца, портящих целостность конструкции.
Для осуществления контроля и оценки прочности бетона рассматривают три показателя:
- точность измерений;
- стоимость оборудования;
- трудоемкость.
Наиболее дорогими являются испытания кернов на лабораторном прессе и отрыв со скалыванием. Исследования по величине ударного импульса, упругого отскока, пластических деформаций или с помощью ультразвука имеют меньшую затратную часть. Но применять их рекомендуется после установления градуировочной зависимости между косвенной характеристикой и фактической прочностью.
Параметры смеси могут существенно отличаться от тех, при которых была построена градуировочная зависимость. Чтобы определить достоверную прочность бетона на сжатие, проводят обязательные испытания кубиков на прессе или определяют усилие на отрыв со скалыванием.
Если пренебречь этой операцией, неизбежны большие погрешности при контроле и оценке прочности бетона. Ошибки могут достигать 15-75 %.
Целесообразно пользоваться косвенными методами при оценке технического состояния конструкции, когда необходимо выявить зоны неоднородности материала. Тогда правила контроля допускают применение неточного относительного показателя.
Как определить прочность бетона?
В производстве материалов и строительстве применяются методы для испытания бетона на прочность:
- разрушающие;
- неразрушающие прямые;
- неразрушающие косвенные.
Они позволяют с той или иной точностью проводить контроль и оценку фактической прочности бетона в лабораториях, на площадках или в уже построенных сооружениях.
Разрушающие методы
Из готовой смонтированной конструкции выпиливают или выбуривают образцы, которые затем разрушают на прессе. После каждого испытания фиксируют значения максимальных сжимающих усилий, выполняют статистическую обработку.
Этот метод, хотя и дает объективные сведения, часто не приемлем из-за дороговизны, трудоемкости и причинения локальных дефектов.
На производстве исследования проводят на сериях образцов, заготовленных с соблюдением требований ГОСТ 10180-2012 из рабочей бетонной смеси. Кубики или цилиндры выдерживают в условиях, максимально приближенным к заводским, затем испытывают на прессе.
Неразрушающие прямые
Неразрушающие методы контроля прочности бетона предполагают испытания материала без повреждений конструкции. Механическое взаимодействие прибора с поверхностью производится:
- при отрыве;
- отрыве со скалыванием;
- скалывании ребра.
При испытаниях методом отрыва на поверхность монолита приклеивают эпоксидным составом стальной диск. Затем специальным устройством (ПОС-50МГ4, ГПНВ-5, ПИВ и другими) отрывают его вместе с фрагментом конструкции. Полученная величина усилия переводится с помощью формул в искомый показатель.
При отрыве со скалыванием прибор крепится не к диску, а в полость бетона. В пробуренные шпуры вкладывают лепестковые анкеры, затем извлекают часть материала, фиксируют разрушающее усилие. Для определения марочной характеристики применяют переводные коэффициенты.
Метод скалывания ребра применим к конструкциям, имеющим внешние углы — балки, перекрытия, колонны. Прибор (ГПНС-4) закрепляют к выступающему сегменту при помощи анкера с дюбелем, плавно нагружают. В момент разрушения фиксируют усилие и глубину скола. Прочность находят по формуле, где учитывается крупность заполнителя.
Внимание! Способ не применяют при толщине защитного слоя менее 20 мм.
Неразрушающие косвенные методы
Уточнение марки материала неразрушающими косвенными методами проводится без внедрения приборов в тело конструкции, установки анкеров или других трудоемких операций. Применяют:
- исследование ультразвуком;
- метод ударного импульса;
- метод упругого отскока;
- пластической деформации.
При ультразвуковом методе определения прочности бетона сравнивают скорость распространения продольных волн в готовой конструкции и эталонном образце. Прибор УГВ-1 устанавливают на ровную поверхность без повреждений. Прозванивают участки согласно программе испытаний.

Данные обрабатывают, исключая выпадающие значения. Современные приборы оснащены электронными базами, проводящими первичные расчеты. Погрешность при акустических исследованиях при соблюдении требований ГОСТ 17624-2012 не превышает 5%.
При определении прочности методом ударного импульса используют энергию удара металлического бойка сферической формы о поверхность бетона. Пьезоэлектрическое или магнитострикционное устройство преобразует ее в электрический импульс, амплитуда и время которого функционально связаны с прочностью бетона.
Прибор компактен, прост в применении, выдает результаты в удобном виде — единицах измерения нужной характеристики.
При определении марки бетона методом обратного отскока прибор — склерометр — фиксирует величину обратного движения бойка после удара о поверхность конструкции или прижатой к ней металлической пластины. Таким образом устанавливается твердость материала, связанная с прочностью функциональной зависимостью.
Метод пластических деформаций предполагает измерение на бетоне размеров следа после удара металлическим шариком и сравнение его с эталонным отпечатком. Способ разработан давно. Наиболее часто на практике используется молоток Кашкарова, в корпус которого вставляют сменный стальной стержень с известными характеристиками.
По поверхности конструкции наносят серию ударов. Прочность материала определяется из соотношения полученных диаметров отпечатков на стержне и бетоне.
Заключение
Для контроля и оценки прочности бетона целесообразно пользоваться неразрушающими методами испытаний. Они более доступны и недороги по сравнению с лабораторными исследованиями образцов. Главное условие получения точных значений — построение градуировочной зависимости приборов. Необходимо также устранить факторы, искажающие результаты измерений.
Как определить прочность бетона | Статьи
Прочность бетона является важнейшей характеристикой, от которой зависят эксплуатационные параметры материала. Под прочностью подразумевают способность бетона противостоять внешним механическим силам и агрессивным средам. Особенно актуальны способы определения этой величины методами неразрушающего контроля: механическими или ультразвуковым.
Правила испытания прочности бетона на сжатие, растяжение и изгиб определяются ГОСТ 18105-86. Одной из характеристик прочности бетона является коэффициент вариации (Vm), который характеризует однородность смеси.
Навигатор предлагает приобрести высококачественный строительный бетон по низким ценам с доставкой по СПб.По ГОСТ 10180—67 предел прочности бетона при сжатии определяется при сжатии контрольных кубов с размерами ребер 20 см в 28-суточном возрасте — это так называемая кубиковая прочность. Призменная прочность определяется как 0,75 кубиковой прочности для класса бетона В25 и выше и 0,8 для класса бетона ниже В25
Помимо ГОСТов, требования к расчётной прочности бетона задаются в СНиПах. Так, например, минимальная распалубочная прочность бетона незагруженных горизонтальных конструкций при пролете до 6 метров должна составлять не менее 70% проектной прочности, а свыше 6 метров – 80% проектной прочности бетона.
Механические неразрушающие методы определения прочности бетона
Неразрушающие способы бетона на сжатие основываются на косвенных характеристиках показаний приборов. Испытания прочности бетона проводятся с помощью основных методов: упругого отскока, ударного импульса, отрыва, скалывания, пластической деформации, отрыва со скалыванием.

О том, какие существуют марки бетона по прочности, в этой статье рассказывают специалисты.
Закажите лучший бетон М200 для строительства и изготовления стяжек полов, дорожек, бетонных лестниц.
Рассмотрим виды испытательных приборов механического принципа действия. Таким способом прочность бетона определяется глубиной внедрения рабочего органа прибора в поверхностный слой материала.
Принцип действия молотка Физделя основан на использовании пластических деформаций строительных материалов. Удар молотка по поверхности бетона образует лунку, диаметр которой и характеризует прочность материала. Место, на которое наносятся опечатки, должно быть очищено от штукатурки, шпатлевки, окрасочного слоя. Испытания проводятся локтевыми ударами средней силы по 10-12 раз на каждом участке конструкции с расстоянием между отпечатками не менее 3 см. Диаметр полученных лунок измеряется с помощью штангенциркуля по двум перпендикулярным направлениям с точностью до десятой миллиметра. Прочность бетона определяется с помощью среднего диаметра отпечатка и тарировочной кривой. Тарировочная кривая строится на сравнении полученных диаметров отпечатков и результатов лабораторных исследований на образцах, взятых из конструкции или изготовленных по технологиям, аналогичных примененным.
На свойствах пластической деформации основан и принцип действия молотка Кашкарова. Различие между этими приборами заключается в наличии между молотком и завальцованным шариком отверстия, в которое введен контрольный стержень. Удар молотка Кашкарова приводит к образованию двух отпечатков. Одного — на поверхности обследуемой конструкции, второго — на эталонном стержне. Соотношение диаметров получаемых отпечатков зависит от прочности исследуемого материала и контрольного стержня и не зависит от скорости и силы удара молотка. По среднему соотношению диаметров двух отпечатков с помощью тарировочного графика устанавливают прочность бетона.
Пистолеты ЦНИИСКа, Борового, молоток Шмидта, склерометр КМ, оснащенный стержневым ударником, работают, основываясь на принципе упругого отскока. Измерения величины отскока бойка проводятся при постоянной величине кинетической энергии металлической пружины и фиксируются указателем на шкале прибора. Взвод и спуск бойка происходят автоматически при соприкосновении ударника и испытуемой поверхности. Склерометр КМ имеет специальный боек определенной массы, который с помощью предварительно напряженной пружины с заданной жесткостью ударяет по металлическому ударнику, прижатому другим концом к обследуемой поверхности.
Метод испытания на отрыв со скалыванием позволяет определить прочность бетона в теле бетонного элемента. Участки для испытания подбираются таким образом, чтобы в этой зоне не было арматуры. Для проведения исследований используют анкерные устройства трех типов. Анкерные устройства первого типа устанавливаются в конструкцию при бетонировании. Для установки второго и третьего типов анкерных устройств предварительно подготавливают шпуры, высверливая их в бетоне.
Ультразвуковой метод измерения прочности бетона
Принцип действия приборов ультразвукового контроля основывается на связи, которая существует между скоростью распространения ультразвуковых волн в материале и его прочностью.
В зависимости от способа прозвучивания разделяют две градуировочные зависимости: «скорость распространения волн — прочность бетона», «время распространения ультразвуковых волн — прочность бетона».
Метод сквозного прозвучивания в поперечном направлении применяется для сборных линейных конструкций — балок, ригелей, колонн. Ультразвуковые преобразователи при таких испытаниях устанавливаются с двух противоположных сторон контролируемой конструкции.
Поверхностным прозвучиванием испытывают плоские, ребристые, многопустотные плиты перекрытия, стеновые панели. Волновой преобразователь устанавливается с одной стороны конструкции.
Для получения надежного акустического контакта между испытуемой конструкцией и рабочей поверхностью ультразвукового преобразователя используют вязкие контактные материалы типа солидола. Возможна установка «сухого контакта» с использованием конусных насадок и протекторов. Ультразвуковые преобразователи устанавливают на расстоянии не менее 3 см от края конструкции.

Способы уплотнения бетонной смеси — здесь описано, какие они бывают и какой выбрать.
Цена бетона М400 по этой ссылке, в нашем каталоге.
Приборы для ультразвукового контроля прочности состоят из электронного блока и датчиков. Датчики могут быть раздельными или объединенными для поверхностного прозвучивания.
Скорость распространения ультразвуковой волны в бетоне зависит от плотности и упругости материала, наличия в нем пустот и трещин, отрицательно влияющих на прочность и другие качественные характеристики. Следовательно, ультразвуковое прозвучивание предоставляет информацию о следующих параметрах:
- однородности, прочности, модуле упругости и плотности;
- наличии дефектов и особенностях их локализаций;
- форме А-сигнала.
Прибор записывает и преобразует в визуальный сигнал принимаемые ультразвуковые волны. Оснащенность контрольного оборудования цифровыми и аналоговыми фильтрами позволяет оптимизировать соотношение сигнала и помех.
Методы разрушающего контроля прочности бетона
Каждый застройщик может выбирать самостоятельно методы неразрушающего контроля, но согласно существующим СНиПам разрушающий контроль является обязательным. Способов организации выполнения требований СНиПов существует несколько.
- Контроль прочности бетона может проводиться на специально изготовленных образцах. Применяется этот метод при производстве сборных железобетонных конструкций и для выходного контроля БСГ (бетонной смеси готовой) на стройплощадке.
- Прочность бетонов может контролироваться на образцах, которые были получены способами выпиливания и вырубывания из самой конструкции. Места взятия проб определяются с учетом снижения несущей способности в зависимости от напряженного состояния. Целесообразно, чтобы эти места указывались самими проектировщиками в проектной документации.
- Испытания образцов, изготовленных на месте проведения работ в условиях, определенных конкретным технологическим регламентом. Однако укладка бетона в кубы для проведения последующих испытаний, его твердение и хранение значительно отличаются от реальных условий укладки, уплотнения и твердения рабочих бетонных смесей. Эти различия существенно снижают достоверность получаемых таким способом результатов.
Самостоятельное измерение прочности бетона
Профессиональные методы определения прочности бетона дороги и не всегда доступны. Существует способ самостоятельного проведения обследования на прочность бетонных конструкций.
Для испытаний потребуется молоток весом 400-800 г и зубило. По приставленному к поверхности бетона зубилу наносится удар средней силы. Далее определяется степень повреждения, нанесенного поверхностному слою. Если зубило оставило лишь небольшую отметину, то бетон можно отнести к классу прочности В25. При наличии более значительной зазубрины бетон можно отнести к классам В15-В25. Если зубило проникнет в тело конструкции на глубину менее 0,5 см, то образец можно отнести к классу В10, если более 1 см — к классу В5. Класс или марка бетона по прочности — это основной показатель качества бетонной смеси, которые определяют среднюю прочность бетона. Например, средняя прочность бетона В30 (М400) составляет 393 кгс / см2.
Ориентировочно определить прочность бетона Rб в на 28 сутки в МПа можно по формуле Боломея-Скрамтаева, которая является основным законом прочности бетона. Для этого необходимо знать марку примененного цемента — Rц и цементно-водное соотношение — Ц/В. Коэффициент А при нормальном качестве заполнителей равен примерно 0,6.
Rб = А*Rц*(Ц/В-0,5)
При этом набор прочности бетона во времени подчиняется формуле
n = Марочная прочность *(lg(n) / lg(28)) , где n не менее 3 дней,
на 3 сутки бетон набирает около 30% марочной прочности, на 7 сутки — 60-80%, а 100% предел прочности достигается на 28-е сутки. Дальнейшее повышение прочности бетона происходит, но очень медленно. Согласно СНиП 3.03.01-87, уход за свежим бетоном продолжается до набора 70% прочности или до другого срока распалубливания.
Методы самостоятельного определения прочности бетонных конструкций просты и экономичны. Однако в случае строительства важных объектов целесообразно обратиться к услугам специализированных лабораторий.
Желаете сэкономить? Изучите цены на бетон от компании «ТД Навигатор».Понятие о классах и марках бетона. Стандартные классы и марки тяжёлого бетона по прочности.
Марки и классы бетона. При проектировании бетонных и железобетонных конструкций назначают требуемые характеристики бетона: класс (марку) прочности, марки морозостойкости и водонепроницаемости. За проектную марку бетона по прочности на сжатие принимают сопротивление осевому сжатию (кгс/см2) эталонных образцов-кубов. За проектную марку бетона по прочности на осевое растяжение принимают сопротивление осевому растяжению (кгс/см2) контрольных образцов. Эта марка назначается тогда, когда она имеет главенствующее значение. Проектную марку бетона по прочности на сжатие контролируют путем испытания стандартных бетонных образцов: для монолитных конструкций – в возрасте 28 сут, для сборных конструкций – в сроки, установленные для данного вида изделий стандартом или техническими условиями. Прочность бетона определяют путем испытания образцов, которые изготовляют сериями; серия, как правило, состоит из трех образцов. Предел прочности при растяжении возрастает при повышении марки бетона по прочности при сжатии, однако увеличение сопротивления растяжению замедляется в области высокопрочных бетонов. Поэтому прочность бетона при растяжении составляет 1/10–1/17 предела прочности при сжатии, а предел прочности при изгибе – 1/6–1/10. Класс бетона – это числовая характеристика какого-либо его свойства, принимаемая с гарантированной обеспеченностью 0,95. Это значит, что установленное классом свойство обеспечивается не менее чем в 95 случаях из 100 и лишь в 5-ти случаях можно ожидать его не выполненным. Бетоны подразделяются на классы: В1; В1,5; В2; В2,5; В3,5; В5; В7,5; В10; В12,5; В15; В20; В25; В30; В40; В45; В50; В55; В60. Соотношение между классом и марками бетона по прочности при нормативном коэффициенте вариации =13,5% следует принять R=В/0,778, например, для класса В5 средняя прочность будет R=6,43 Мпа.
Влияние производственных факторов на качество бетона (приготовление и уплотнение бетонной смеси, условия твердения бетона).
В процессе переработки исходного сырья в готовый бетонный элемент качество бетона может изменяться под воздействием ряда объективных и субъективных факторов. Совокупность этих производственных факторов можно условно разделить на группы, охватывающие все этапы бетонных работ. Первый этап — оценка качества исходных материалов и определение состава бетона. В число факторов, оказывающих решающее влияние на показатели качества бетона (прочность, долговечность, экономичность), входит качество цемента, заполнителей и воды. Качество цемента должно обеспечить получение бетона заданной прочности и долговечности. Поэтому марку цемента следует выбирать в зависимости от проектной прочности бетона, а вид цемента — в соответствии с условиями эксплуатации конструкции. Как правило, марка цемента должна быть выше требуемой прочности бетона в 1,25… 2 раза. Если марка цемента намного превышает прочность бетона, то расход цемента, рассчитанный из условия прочности, оказывается меньше необходимого по условию плотности бетона. Чтобы избежать перерасхода высокомарочного цемента, вводят в состав бетона тонкомолотую минеральную добавку. Снижение расхода цемента как наиболее дорогостоящего компонента бетона важно не только по экономическим причинам. При сокращении количества цемента уменьшается усадка бетона, возрастает его трещиностойкость. В массивных конструкциях, например гидротехнических сооружениях, большой расход цемента вызывает значительное тепловыделение, которое может привести к растрескиванию бетонного массива в результате неравномерного разогрева бетона. Вид цемента выбирают с учетом особенностей изготовления и условий эксплуатации бетона. Например, бвклротвердеюшие цементы целесообразно использовать при изготовлении сборных железобетонных изделий, так как при быстром наборе прочности ускоряется оборачиваемость металлических форм. Однако такие цементы вследствие большой экзотермии не рекомендуются для бетонов в массивных конструкциях гидротехнических сооружений. Для этих целей больше подходят смешанные цементы (пуццолановый и шлакопортландцемент). Для повышения морозостойкости бетона рекомендуется использовать цементы с органическими добавками — гидрофобный и пластифицированный. Качество заполнителей оценивают зерновым составом, содержанием пылевидных и глинистых примесей, органических растительных остатков, вредных примесей и т.д. Загрязненные заполнители подвергают промывке и классификации, рассеивая на отдельные фракции. Качество воды для изготовления бетона зависит от содержания сульфатов, хлоридов и ряда других соединений. Без предварительного испытания можно применять воду, пригодную для питья, речную и озерную воду. Второй этап — приготовление бетонной смеси и укладка ее в конструкцию. На данном этапе необходимо обеспечить приготовление однородной, хорошо перемешанной бетонной смеси, обладающей заданной удобоукладываемостыо, и плотную укладку смеси в опалубку. Здесь главными факторами, определяющими качество бетона, являются однородность смешивания компонентов и качество уплотнения бетонной смеси. Приготовление бетонной смеси включает операции дозирования и перемешивания составляющих материалов. Дозирование компонентов бетона осуществляют по массе, обычно с помощью автоматических дозаторов. Отклонения от заданной массы при дозировании на замес не должны превышать ±2 % для цемента, воды и водных растворов добавок и ±2,5 % для заполнителей. Однородность смешивания компонентов достигается выбором типа смесителя и режима перемешивания в соответствии с удобоукладываемостыо приготовляемой бетонной смеси. При смешивании материалов приходится преодолевать силы сцепления между частицами, сопротивление смеси сдвигу, а также силы тяжести. Подвижные смеси с повышенным содержанием воды и вяжущего вещества, обладающие малым сопротивлением сдвигу, перемешиваются значительно легче, чем жесткие. По принципу перемешивания бетоносмесители подразделяют на гравитационные и с принудительным перемешиванием. Гравитационные бетоносмесители выполнены в виде барабана, вращающегося вокруг горизонтальной оси. При перемешивании частицы смеси поднимаются на некоторую критическую высоту и, как только сила тяжести становится больше суммы центробежной силы и сил сцепления между частицами, они падают и, имея значительную кинетическую энергию, внедряются в бетонную смесь в нижней части смесительного барабана. Тем самым достигается эффект перемешивания. Продолжительность перемешивания определяют опытным путем в строительной лаборатории. Для этого отбирают из смесителя пробы бетонной смеси с интервалом 15…30 с, изготовляют контрольные образцы. После затвердевания бетона определяют прочность и рассчитывают коэффициент вариации прочности бетона. Чем меньше коэффициент вариации, тем более однороден бетон. Продолжительность перемешивания назначают по времени, при котором коэффициент вариации прочности бетона не превышает 4…5 %. Время перемешивания отсчитывают от момента окончания загрузки материалов в смеситель до начала выгрузки. Гравитационные смесители оказываются малопригодными для перемешивания жестких бетонных смесей; в таких случаях применяют машины принудительного перемешивания. В них компоненты смеси подвергают принудительному перемещению по весьма сложным траекториям, благодаря чему и получается однородная бетонная смесь. Продолжительность смешивания крупнозернистых смесей 2…3 мин, мелкозернистых — 3…5 мин. Качество уплотнения бетонной смеси должно быть таким, чтобы уложенный в опалубку или форму бетон обладал однородным строением с минимальным объемом вовлеченного воздуха — не более 2 %. Энергетические затраты на уплотнение тем больше, чем выше жесткость бетонной смеси. Основным способом уплотнения является вибрирование. При вибрировании частицы бетонной смеси совершают вынужденные колебания, в результате которых ослабляются силы внутреннего трения и сцепления между частицами. Бетонная смесь переходит в состояние пластично-вязкого течения и, подобно тяжелой жидкости, равномерно укладывается в форму. Для уплотнения монолитного бетона на строительной площадке применяют переносные поверхностные и глубинные вибраторы. На заводах железобетонных изделий используют эффективные комбинированные способы уплотнения бетонных смесей: вибрирование под нагрузкой, вибро-штампование, вибропрокат, прессование, трамбование. Для изготовления полых железобетонных изделий, форма которых приближается к поверхности вращения (трубы, опоры ЛЭП), применяют уплотнение с помощью центробежных сил — центрифугирование. Третий этап — твердение бетона. Уложенная в опалубку бетонная смесь благодаря гидратации цемента самопроизвольно затвердевает. Заданная проектом прочность достигается при определенном уходе за твердеющим бетоном, т.е. при создании оптимального температурно-влажностного режима твердения и защите бетона от ударов и сотрясений, которые могут нарушать еще не сложившуюся структуру. Важнейшими факторами, влияющими на качество бетона на данном этапе, являются условия и длительность твердения. Условия твердения считают нормальными, если бетон находится в теплой и влажной среде. При преждевременном высыхании или замерзании взаимодействие цемента с водой прекращается, что отрицательно сказывается на строении и свойствах бетона. Часто возникает необходимость ускорить твердение бетона. Для этой цели используют преимущественно тепловую обработку, позволяющую повысить температуру бетона при обязательном сохранении его влажности. В результате скорость взаимодействия цемента с водой значительно возрастает и прочность бетона в начальные сроки увеличивается. В качестве теплоносителя применяют пар или паровоздушную смесь с температурой 60…90 С. Прочность бетона после пропари-вания в течение 10…14 ч достигает 70…75 % марочной. Еще более ускоряет твердение бетона обработка насыщенным паром при давлении 0,8…1,2 МПа и температуре 175…190 ° С,осуществляемая в автоклавах. Однако такую обработку можно использовать только в заводских условиях, поэтому ее применяют в тех случаях, когда обычные методы ускорения твердения неэффективны, например для изделий из силикатных и ячеистых бетонов. Кроме тепловой обработки пропариванием для ускорения твердения бетона применяют электропрогрев изделий. На строительных площадках широко используют тепловую обработку с помощью инфракрасного излучения. Излучатели инфракрасных лучей нагреваются электрическим током или газом. Выделяемая ими лучистая энергия поглощается стенками опалубки либо непосредственно изделием и аккумулируется в бетоне в виде теплоты. Для ускорения твердения бетона применяют также добавки-ускорители. Введение в бетонную смесь таких добавок повышает прочность бетона в возрасте 3 сут в 2..3 раза, а к 28 сут прочность оказывается такой же, как и у бетона без добавки.
Марки и классы бетона. При проектировании бетонных и железобетонных конструкций назначают требуемые характеристики бетона: класс (марку) прочности, марки морозостойкости и водонепроницаемости. За проектную марку бетона по прочности на сжатие принимают сопротивление осевому сжатию (кгс/см2) эталонных образцов-кубов. За проектную марку бетона по прочности на осевое растяжение принимают сопротивление осевому растяжению (кгс/см2) контрольных образцов. Эта марка назначается тогда, когда она имеет главенствующее значение. Проектную марку бетона по прочности на сжатие контролируют путем испытания стандартных бетонных образцов: для монолитных конструкций – в возрасте 28 сут, для сборных конструкций – в сроки, установленные для данного вида изделий стандартом или техническими условиями. Прочность бетона определяют путем испытания образцов, которые изготовляют сериями; серия, как правило, состоит из трех образцов. Предел прочности при растяжении возрастает при повышении марки бетона по прочности при сжатии, однако увеличение сопротивления растяжению замедляется в области высокопрочных бетонов. Поэтому прочность бетона при растяжении составляет 1/10–1/17 предела прочности при сжатии, а предел прочности при изгибе – 1/6–1/10. Класс бетона – это числовая характеристика какого-либо его свойства, принимаемая с гарантированной обеспеченностью 0,95. Это значит, что установленное классом свойство обеспечивается не менее чем в 95 случаях из 100 и лишь в 5-ти случаях можно ожидать его не выполненным. Бетоны подразделяются на классы: В1; В1,5; В2; В2,5; В3,5; В5; В7,5; В10; В12,5; В15; В20; В25; В30; В40; В45; В50; В55; В60. Соотношение между классом и марками бетона по прочности при нормативном коэффициенте вариации =13,5% следует принять R=В/0,778, например, для класса В5 средняя прочность будет R=6,43 Мпа.
Основные методы определения прочности тяжелого бетона на сжатие в сборных и монолитных бетонных и железобетонных конструкциях и изделиях
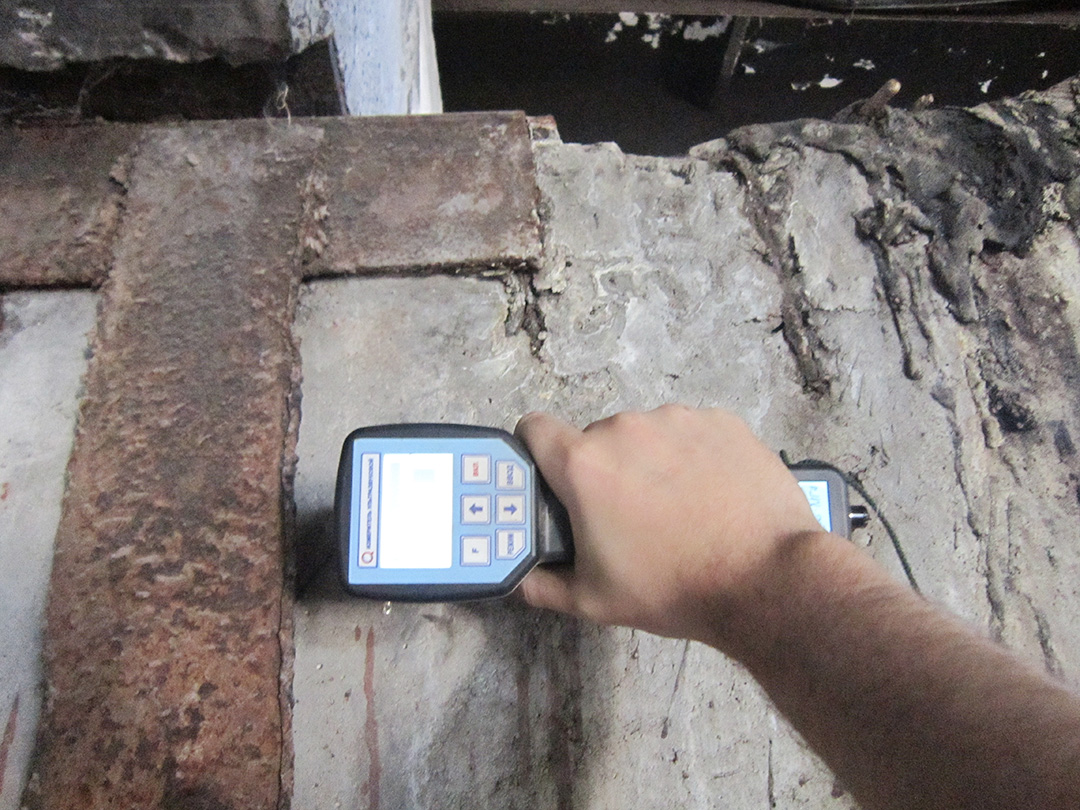
Рассмотрим некоторые основные методы и приборы определения прочности бетона в конструкциях, которыми пользуются на практике. Определение прочности механическими методами неразрушающего контроля осуществляется согласно ГОСТ 22690-88 «БЕТОНЫ. ОПРЕДЕЛЕНИЕ ПРОЧНОСТИ МЕХАНИЧЕСКИМИ МЕТОДАМИ НЕРАЗРУШАЮЩЕГО КОНТРОЛЯ», определения прочности ультразвуковым методом неразрушающего контроля осуществляется по ГОСТ 17624-87 «БЕТОНЫ. УЛЬТРАЗВУКОВОЙ МЕТОД ОПРЕДЕЛЕНИЯ ПРОЧНОСТИ», определение прочности по бетонным образцам, выбуренным или выпиленным из конструкций, осуществляется по ГОСТ 28570-90 «БЕТОНЫ. МЕТОДЫ ОПРЕДЕЛЕНИЯ ПРОЧНОСТИ ПО ОБРАЗЦАМ, ОТОБРАННЫМ ИЗ КОНСТРУКЦИЙ».
Неразрушающие методы определения прочности на сжатие бетонных конструкций основаны на косвенных характеристиках показаний приборов, основанных на методах упругого отскока, ударного импульса, пластической деформации,отрыва, скалывания ребра и отрыва со скалыванием, скорости прохождения ультразвука. Определение прочности на сжатия по образцам, отобранным из конструкций, подразумевает испытание их на прессе.
Для определения класса и марки бетона в зависимости от прочности сжатия или растяжения, можно использовать табл.6, приложения 1, ГОСТ 26633-91 «БЕТОНЫ ТЯЖЕЛЫЕ И МЕЛКОЗЕРНИСТЫЕ»
СООТНОШЕНИЕ МЕЖДУ КЛАССАМИ БЕТОНА ПО ПРОЧНОСТИ НА СЖАТИЕ И РАСТЯЖЕНИЕ И МАРКАМИ
Таблица 6
Класс бетона по прочности
Средняя прочность бетона (
)*, кгс/см2
Ближайшая марка бетона по прочности М
Отклонение ближайшей марки бетона от средней прочности класса, %,
Сжатие
В3,5
45,8
M50
+9,2
В5
65,5
M75
+14,5
В7,5
98,2
M100
+1,8
В10
131,0
M150
+14,5
B12,5
163,7
M150
-8,4
B15
196,5
M200
+1,8
В20
261,9
M250
-4,5
В22,5
294,7
M300
+1,8
В25
327,4
M350
+6,9
В27,5
360,2
M350
-2,8
В30
392,9
M400
+1,8
В35
458,4
M450
-1,8
В40
523,9
М550
+5,0
В45
589,4
M600
+1,8
B50
654,8
M700
+6,9
В55
720,3
M700
-2,8
В60
785,8
M800
+1,8
В65
851,3
M900
+5,7
В70
916,8
M900
-1,8
В75
982,3
М1000
+1,8
В80
1047,7
M1000
-4,6
____________
• Средняя прочность бетона R рассчитана при коэффициенте вариации V, равном 13,5 %, и обеспеченности- 95 % для всех видов бетона, а для массивных гидротехнических конструкций- при коэффициенте вариации V, равном 17 %, и обеспеченности- 90%.
Методы и приборы неразрушающего контроля
Для определения прочности бетона на сжатие данные показаний необходимо преобразовывать с помощью предварительно установленных градуировочных зависимостей между прочностью бетона и косвенной характеристикой прочности (в виде графика, таблицы или формулы), по методикам, указанным в ГОСТ 22690-88 и по прилагаемым графикам градуировочных зависимостей к приборамб, установленным на заводе-изготовителей прибора.
Испытание прочности приборами неразрушающего контроля выполняют, непосредственно, в местах расположения конструкций, однако, также можно выполнять испытание бетона проб из конструкций. Испытание бетона в пробах рекомендуется для определения его прочности в труднодоступных зонах конструкций и в конструкциях, находящихся при отрицательной температуре. Пробу вмоноличивают в раствор, прочность которого на день испытания должна быть не менее половины прочности бетона пробы (для предотвращения разрушения пробы при испытании). Вмоноличивание проб в раствор удобно производить с использованием стандартных форм, для изготовления бетонных контрольных образцов по ГОСТ 10180-90. Расположение проб после распалубки представлено на рис.1.
Рис.1. 1 — проба бетона; 2 — наиболее удобная для испытания сторона пробы 3 — раствор, в котором закреплена проба
Обычно приборы поставляются с графиками градуировочной зависимости или с базовыми настройками для тяжелого бетона средних марок. Для обследования конструкций допускается применять методы упругого отскока, ударного импульса или пластической деформации, используя градуировочную зависимость, установленную для бетона, отличающегося от испытываемого (по составу, возрасту, условиям твердения, влажности), с уточнением ее в соответствии с методикой, приведенной в приложении 9 (ГОСТ 22690-88). Для ультразвуковых приборов требуется градуировка и корректировка согласно ГОСТ 17624, ГОСТ 24332 и методических рекомендаций МДС 62-2.01 ГУП «НИИЖБ» по контролю прочности бетона монолитных конструкций ультразвуковым методом поверхностного прозвучивания.
Согласно ГОСТ 22690-88 п. 4.4. для методов неразрушающего контроля число испытаний на одном участке, расстояние между местами испытаний на участке и от края конструкции, толщина конструкции на участке испытания должны быть не меньше значений, приведенных в табл. 3.
Таблица 3
Наименование метода
Число испытаний на участке
Расстояние между местами испытаний, мм
Расстояние от края конструкции до места испытаний, мм
Толщина конструкции
Упругий отскок
5
30
50
100
Ударный импульс
10
15
50
50
Пластическая деформация
5
30
50
70
Скалывание ребра
2
200
—
170
Отрыв
1
2 диаметра диска
50
50
Отрыв со скалыванием
1
5 глубин вырыва
150
Удвоенная глубина установки анкера
Метод упругого отскока
При испытании методом упругого отскока, расстояние, от мест проведения испытания до арматуры, должно быть, не менее 50 мм.
Испытание проводят в следующей последовательности:
- прибор располагают так, чтобы усилие прикладывалось, перпендикулярно к испытываемой поверхности, в соответствии с инструкцией по эксплуатации прибора;
- положение прибора, при испытании конструкции относительно горизонтали, рекомендуется принимать таким же, как при испытании образцов для установления градуировочной зависимости; при другом положении, необходимо вносить поправку на показания в соответствии с инструкцией по эксплуатации прибора;
- фиксируют значение косвенной характеристики, в соответствии с инструкцией по эксплуатации прибора;
- вычисляют среднее значение косвенной характеристики на участке конструкции.
Определение прочности бетона прибором «Склерометр – ОМШ1»
Склерометр предназначен для определения прочности бетона и раствора методом упругого отскока по ГОСТ 22690-88. Пределы измерений для данного метода- от 5, до 50 МПа (для марок бетона от М50 до М500)
Прибор представляет собой цилиндрический корпус со шкалой, в котором размещены ударный механизм с пружинами и стрелка – индикатор. Испытания проводят путем нажатия приставленного к бетону склерометра и после удара бойка и величине его отскока, зафиксированного стрелкой-индикатором по графику, определяют прочность бетона(раствора). Продолжительность одного испытания- 20 сек.
К склерометру прилагается график, определяющий зависимость между твердостью при ударе и прочностью бетона. График, построен путем выполнения большой серии испытаний на кубиках, причем каждый кубик раздавливался в прессе непосредственно, после испытания склерометром (до ± 32%).
Отрыв со скалыванием
При испытании, методом отрыва, участки должны располагаться в зоне наименьших напряжений, вызываемых эксплуатационной нагрузкой или усилием обжатия, предварительно напряженной арматуры.
Испытания проводят в следующей последовательности:
- если анкерное устройство не было установлено до бетонирования, то в бетоне сверлят или пробивают шпур, размер которого выбирают в соответствии с инструкцией по эксплуатации прибора в зависимости от типа анкерного устройства;
- в шпуре закрепляют анкерное устройство на глубину, предусмотренную инструкцией по эксплуатации прибора, в зависимости от типа анкерного устройства;
- прибор соединяют с анкерным устройством;
- нагрузку увеличивают, со скоростью 1,5 — 3,0 кН/с;
- фиксируют показание силоизмерителя прибора и глубину вырыва с точностью не менее 1 мм.
Если наибольший и наименьший размеры вырванной части бетона от анкерного устройства до границ разрушения по поверхности конструкции отличаются более чем в два раза, а также если глубина вырыва отличается от глубины заделки анкерных устройств более чем на 5 %, то результаты испытаний допускается учитывать только для ориентировочной оценки прочности бетона.
Еслис прибором применяются анкерные устройства в соответствии с приложением 2 ГОСТ 22690-88, то допускается использовать следующую градуировочную зависимость:
ПРИЛОЖЕНИЕ 5
Рекомендуемое
ГРАДУИРОВОЧНАЯ ЗАВИСИМОСТЬ ДЛЯ МЕТОДА ОТРЫВА СО СКАЛЫВАНИЕМ
При использовании анкерных устройств, приведенных в приложении 2, прочность бетона R, МПа можно вычислять по градуировочной зависимости по формуле
(1)
где m1 — коэффициент, учитывающий максимальный размер крупного заполнителя в зоне вырыва и принимаемый равным 1 при крупности менее 50 мм и 1,1 при крупности 50 мм и более;
m2 — коэффициент пропорциональности для перехода от усилия вырыва, кН, к прочности бетона, МПа;
Р — усилие вырыва анкерного устройства, кН.
При испытании тяжелого бетона прочностью 10 МПа и более и керамзитобетона прочностью от 5 до 40 МПа значения коэффициента пропорциональности m2 принимают по табл. 9.
Таблица 9
Условие твердения бетона
Тип анкерного устройства
Предполагаемая прочность бетона, МПа
Глубина заделки анкерного устройства, мм
Значение коэффициента m2 для бетона
тяжелого
легкого
Естественное
I
? 50
48
1,1
1,2
> 50
35
2,4
—
II
? 50
48
0,9
1,0
> 50
30
2,5
—
III
? 50
35
1,5
—
Тепловая обработка
I
? 50
48
1,3
1,2
> 50
35
2,6
—
II
? 50
48
1,1
1,0
> 50
30
2,7
—
III
? 50
35
1,8
—
Прибор для определения прочности бетона «ПИБ»
На испытываемой конструкции выбирают ровный участок размером 0,2×0,2 м и выполняют пробивку отверстия, глубиной 55×10-3 м перпендикулярно испытываемой поверхности. Допускается отклонение оси отверстия от нормали испытываемой поверхности до 1 градуса. Пробивку отверстия выполняют шлямбуром с оправкой или механизированным (электромеханическим) инструментом, обеспечивающим выполнение заданных требований.
В подготовленное отверстие устанавливается анкерное устройство, состоящее из конуса и 3-х сегментов, и накручивают гайку-тягу с усилием, предотвращающим проскальзывание анкерного устройства при испытании.
Опору прибора закручивают до упора в рабочий цилиндр. Винт поршневого насоса выкручивают в крайнее верхнее положение. Присоединяют прибор к гайке-тяге и выкручивают опору 4 до упора в поверхность испытываемого материала.
После проведения подготовительных операций производят вырыв анкерного устройства (тип 1 или 2). Вращают ручку поршневого насоса со скоростью, обеспечивающей приложение нагрузки равной 1,5 … ЗкН/с.
В момент разрушения испытываемого материала визуально устанавливают максимальное давление по манометру. Снятие показаний по манометру следует выполнять с точностью до 2,5 кгс/см2.
При проведении испытаний необходимо следить за тем, чтобы не происходило проскальзывания анкерного устройства. Результаты испытаний не учитываются, если произошло проскальзывание анкерного устройства более 5×10-3 м. Повторное испытание данного отверстия не допускается из-за возможности получения заниженных результатов. После вырыва анкерного устройства необходимо уточнить глубину разрушения бетона, используя для ее определения две линейки, одну из которых устанавливают ребром на поверхность бетона в зоне испытаний, другой — замеряют глубину.
Ультразвуковой метод
Ультразвуковой метод основан на связи между скоростью распространения ультразвуковых колебаний в бетоне и его прочностью. Прочность бетона в конструкциях определяют по экспериментально установленным градуировочным зависимостям «скорость распространения ультразвука — прочность бетона» или «время распространения ультразвука — прочность бетона» в зависимости от способа прозвучивания.
Ультразвуковые измерения в бетоне проводят способами сквозного или поверхностного прозвучивания. Сборные линейные конструкции (балки, ригели, колонны и др.) испытывают, как правило, способом сквозного прозвучивания в поперечном направлении. Изделия, конструктивные особенности которых затрудняют осуществление сквозного прозвучивания, а также плоские конструкции (плоские, ребристые и многопустотные панели перекрытия, стеновые панели и т. д.) испытывают способом поверхностного прозвучивания. При этом база прозвучивания при измерениях на конструкциях должна быть такой же, как на образцах при установлении градуировочной зависимости.
Между бетоном и рабочими поверхностями ультразвуковых преобразователей должен быть обеспечен надежный акустический контакт, для чего применяют вязкие контактные материалы (солидол по ГОСТ 4366, технический вазелин по ГОСТ 5774 и др.).
Градуировочную зависимость «скорость — прочность» устанавливают при испытании конструкций способом сквозного прозвучивания. Градуировочную зависимость «время — прочность» устанавливают при испытании конструкций способом поверхностного прозвучивания.
Допускается при испытании конструкций способом поверхностного прозвучивания использовать градуировочную зависимость «скорость — прочность» с учетом коэффициента перехода, определяемого в соответствии с приложением 3.
Измерение времени распространения ультразвука в бетоне конструкций следует проводить в направлении, перпендикулярном уплотнению бетона. Расстояние от края конструкции до места установки ультразвуковых преобразователей должно быть не менее 30 мм. Измерение времени распространения ультразвука в бетоне конструкций следует проводить в направлении, перпендикулярном направлению рабочей арматуры. Концентрация арматуры вдоль выбранной линии прозвучивания не должна превышать 5 %. Допускается прозвучивание вдоль линии, расположенной параллельно рабочей арматуре, если расстояние от этой линии до арматуры составляет не менее 0,6 длины базы.
Пульсар 1.2.
Рис. 2. Внешний вид прибора
Пульсар-1.2: 1 — вход приемника;
2 — выход излучателя
Прибор состоит из электронного блока (см. рис. 3.2) и ультразвуковых преобразователей — раздельных или объединенных в датчик поверхностного прозвучивания. На лицевой панели электронного блока расположены: 12-ти клавишная клавиатура и графический дисплей. В верхней торцевой части корпуса установлены разъёмы для подключения датчика поверхностного прозвучивания или отдельных УЗ преобразователей для сквозного прозвучивания. На правой торцевой части прибора расположен разъем USB интерфейса. Доступ к аккумуляторам осуществляется через крышку батарейного отсека на нижней стенке корпуса.
Работа прибора основана на измерении времени прохождения ультразвукового импульса в материале изделия от излучателя к приемнику. Скорость ультразвука вычисляется делением расстояния между излучателем и приемником на измеренное время. Для повышения достоверности в каждом измерительном цикле автоматически выполняется 6 измерений и результат формируется путем их статистической обработки с отбраковкой выбросов. Оператор выполняет серию измерений (от 1 до 10 измерений по его выбору), которая также подвергается математической обработке с определением среднего значения, коэффициента вариации, коэффициента неоднородности и с отбраковкой выбросов.
Скорость распространения ультразвуковой волны в материале зависит от его плотности и упругости, от наличия дефектов (трещин и пустот), определяющих прочность и качество. Следовательно, прозвучивая элементы изделий, конструкций и сооружений можно получать информацию о:
- прочности и однородности;
- модуле упругости и плотности;
- наличии дефектов и их локализации.
- форме А-сигнала
Возможны варианты прозвучивания со смазкой и сухим контактом (протекторы, конусные насадки), см. рис. 3.1.
Рис. 3. Варианты прозвучивания
Прибор осуществляет запись и визуализацию принимаемых УЗК, имеет встроенные цифровые и аналоговые фильтры, улучшающие соотношение «сигнал-помеха». Режим осциллографа позволяет просматривать сигналы на дисплее (в задаваемом масштабах времени и усиления), вручную устанавливать курсор в положение контрольной метки первого вступления. Пользователь имеет возможность вручную изменять усиление измерительного тракта и смещать ось времени для просмотра и анализа сигналов первого вступления и огибающей.
Оформление результатов для методов определения прочности неразрушающего контроля
Результаты испытаний прочности бетона заносят в журнал, в котором должно быть указано:
- наименование конструкции, номер партии;
- вид контролируемой прочности и ее требуемое значение;
- вид бетона;
- наименование неразрушающего метода, тип прибора и его заводской номер;
- среднее значение косвенной характеристики прочности и соответствующее значение прочности бетона;
- сведения об использовании поправочных коэффициентов;
- результаты оценки прочности бетона;
- фамилия и подпись лица, проводившего испытание, дата испытания.
Для ультразвукового метода определения прочности нужно воспользоваться формой журнала, установленной в приложениях №8-9, ГОСТ 17624-87 «БЕТОНЫ. УЛЬТРАЗВУКОВОЙ МЕТОД ОПРЕДЕЛЕНИЯ ПРОЧНОСТИ»