Стекломагнезитовый лист, применение, недостатки и преимущества
Стекломагнезитовый лист (СМЛ) по праву называют строительным материалом нового поколения. Он состоит из армирующей стекло-сетки и магнезиального вяжущего вещества. В состав последнего входят оксид и хлорид магния. Различное процентное соотношение компонентов в составе материала влияет на его прочность и на классность. Изготавливается материал в виде листов различной толщины, плотности и размеров.
Применение стекломагнезитовых листов
Данный материал считается достаточно универсальным строительным материалом. Стекломагнезитовый лист применяется в процессе строительства и отделки зданий, кровли, заборов, печей и каминов. Материал используют для монтажа кровли, стен, перегородок, пола и даже подоконников. Хорошая стойкость к химическим воздействиям и повышенная влагостойкость делают возможным применение материала в строительстве бассейнов, бань, саун и душевых. Такие листы прекрасно подойдут для выравнивания любых поверхностей.
Недостатки стекломагнезитовых листов
Недостатки стекломагнезитовых листов несущественны и имееют место только для низкокачественных дешевых образцах. Можно выделить следующее:
- низкокачественные стекломагнезитовые листы изготавливаются с добавлением таких добавок как мел, асбест, известь, что уменьшает их характеристики огнестойкости, прочности;
- листы низкого качества при попадании на них влаги могут выделять соль, что в свою очередь приводит к коррозии металла.
Из этого следует, что не стоит экономить на данном материале, лучше купить более дорогие качественные варианты.
Преимущества стекломагнезитовых листов
Специальная технология производства СМЛ придает ему прочность, твердость, морозостойкость. Кроме того, материал имеет высокую степень влагостойкости, не впитывает влагу и не боится сырости. Даже после продолжительного пребывания во влажной среде листы не расслаиваются, не лопаются и не набухают.
По степени огнеупорности стекломагнезитовый лист стоит на одном уровне с камнем, бетоном и сталью. Материал пожароустойчив, не дымит и не горит при очень высоких температурах. Лист отличается повышенной гибкостью. Наличие в его составе армирующей сетки позволяет хорошо гнуться, достигая радиуса кривизны 3 м. Это свойство снижает вероятность переломов листов в процессе перевозки и использования.Стоит отметить, что все положительные свойства стекломагнезитовых листов делают его очень удобным в работе. Лист можно без проблем закрепить с помощью гвоздей и шурупов, он не разрушается и не крошится в процессе разрезания и фрезеровки. С этой целью можно использовать различные материалы: нож, дрель или лобзик. На гладкую и ровную поверхность листа легко ложатся различные отделочные материалы: кафель, обои, декоративные смеси, лак или краска.
Похожие материалы
Стекломагниевый лист — это… Что такое Стекломагниевый лист?
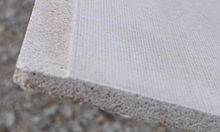
Стекломагниевый лист (СМЛ, КВЛ, КМЛ, новолист, стройлист, стекломагнезитовый лист, магнелит, стекломагнезит, магнезитовая плита
![]() | В этом разделе не хватает ссылок на источники информации. Информация должна быть проверяема, иначе она может быть поставлена под сомнение и удалена. Вы можете отредактировать эту статью, добавив ссылки на авторитетные источники. Эта отметка установлена 3 августа 2012. |
- Толщина — 3,5,6,8,10,12,15,18,20 мм (встречаются и промежуточные толщины).
- Плотность — как правило от 800 до 1100 кг/м3. В зависимости от плотности лист согласно китайскому стандарту JC688-2006 делится на семь классов: класс A — плотность листа не менее 1750 кг/м3, класс B — плотность листа не менее 1500 кг/м
3, класс C — плотность листа не менее 1250 кг/м3, класс D — плотность листа не менее 1000 кг/м3, класс E — плотность листа не менее 700 кг/м3, класс F — плотность листа не менее 500 кг/м3, класс G — плотность листа менее 500 кг/м3. - Цвет — белый.
- Пригоден для влажных помещений и наружных работ.
- Хорошая адгезия.
- Высокая прочность.
Применение
СМЛ используется для наружной и внутренней отделки стен, при изготовлении перегородок, при подготовке полов и облицовки потолков. СМЛ легко поддается механической обработке (резка, пиление, сверление). Монтаж во многом схож с технологией монтажа гипсокартона, но поскольку СМЛ более тверд, то при монтаже шурупами или саморезами рекомендуется предварительно засверлить углубление под шляпку (при плотности листа более 1200 кг/м3). Для закрепления листов с самой широко распространённой на рынке плотностью (980-1050 кг/м3) это не требуется. Рекомендуется использовать оцинкованный (белый цинк) универсальный саморез с потайной головкой диаметром 4,2-4,5 мм. Стыки между листами шпатлюются акриловой либо силиконовой шпаклёвкой с сеткой. Не рекомендуется использовать минеральные шпаклевки на гипсовой или цементной основе. Негорюч.
См. также
Для чего применяются стекломагниевые листы?
С каждым годом рынок строительных материалов пополняется за счет новых разработок производителей, которые представляют самые различные вида сырья. При этом можно отметить, что с развитием технологий качество продукции значительно улучшилось. Кроме того, появление модифицированных элементов и совершенно инновационных способов обработки и методов производства позволяет получить сырье для строительства с характеристиками значительно лучше предшествующих товаров. К такой продукции можно отнести стекломагниевые листы, применение которых в последнее время наиболее распространено.
Что такое стекломагниевый лист?
Стекломагниевые листы (СМЛ) представляют собой пластины, состоящие из двух слоев:
- Наружный слой (с двух сторон листа) выполнен из стекловолоконной сетки, что придает прочность и стойкость материалу к различным механическим нагрузкам.
- Внутренний слой состоит из наполнителя (хлорида и оксида магния, перлита) – экологически чистых веществ с антисептическими свойствами, что предотвращает разрушение структуры и появление грибковых образований и плесени.
Применение материала
Стекломагниевые листы применяют уже во многих странах Европы и Азии. Широкое использование обусловлено отличными характеристиками материала, такими как экологичность, прочность и устойчивость к различным видам воздействий (перепадам температуры, химическим реакциям и так далее).
Применяют СМЛ при строительстве помещений различного предназначения (промышленных, жилых и тому подобных). Это строительное сырье используют при «сухом» типе монтажных работ, что значительно сокращает временные затраты. При этом СМЛ может выступать в качестве альтернативного варианта следующих материалов:
- гипсокартона влагоустойчивого,
- гипсоволокнистого листа,
- ДСП и ДВП,
- плит OSB,
- плоского шифера,
- фанеры.
Можно также отметить, что продукция поступает в продажу с уже отшлифованной поверхностью, то есть не нужно подготавливать стекломагниевый лист. Применение отделочных материалов при этом не ограничено, можно использовать всевозможные образцы оформления:
Монтаж СМЛ
Стекломагниевые листы выпускают обычно стандартных размеров – длина 2,4 м, ширина 1,2 м и толщина 8 мм. При этом тыльной стороной считается неотшлифованная поверхность. Этот вид строительного сырья можно крепить как к металлическим и деревянным конструкциям (при помощи саморезов), так и к поверхностям из синтетических материалов, таких как полистирол, пенопропилен (для соединения используется клей).
Монтажные работы могут проводиться в следующем порядке:
- Установка обрешетки. При этом важно при работе с вертикальными поверхностями (стенами) помнить о расстоянии между стойками: оно должно быть 0,6 м. Монтаж потолка проводят с несущими профилями, которые устанавливают с промежутками в 0,4 м.
- Звукоизоляция. На тыльную сторону пристенного профиля можно наклеить ленту, предотвращающую проникновение шума.
- В случае использования саморезов и шурупов отверстия под них нужно предварительно выполнить с помощью сверла.
- Крепление может проводиться как в поперечном направлении, так и в продольном. При этом швы по горизонтали лучше выполнять с промежутком не менее 0,6 м. Расстояние между СМЛ – от 3 до 5 мм, крепление лучше начинать с центра листа с шагом 0,2 м.
Качественное исполнение работ при строительстве жилых и других типов помещений обеспечит использование такого материала, как стекломагниевый лист. Монтаж его достаточно прост, если соблюдать правила сборки.
Стекломагниевый лист и все о нем
Стекломагниевый лист уже достаточно хорошо знаком большинству строителей и заказчиков. Кто-то от этого материала в восторге, кто-то проклинает, но сегодня ясно одно – стекломагниевый лист уже завоевал свое место на рынке строительных материалов и, как у всех прочих материалов, у него есть свои сильные и слабые стороны. Выяснению тех и других посвящена данная статья.
Сырье и производство
Стекломагниевый лист производят из смеси обезвоженного оксида магния и хлористого магния с мелкофракционным органическим наполнителем, вспомогательными веществами и водой. Смесь распределяется равномерным слоем между двумя слоями стеклоткани в специальном формовочном оборудовании. Дополнительно к стеклоткани с лицевой стороны может быть введен слой стеклохолста, который делает поверхность практически идеально гладкой.
Производство стекломагниевого листа осуществляется поточным методом с небольшими технологическими остановками. Формовка производится на подложках, перемещаемых вдоль конвейера. В узел формовки небольшими порциями подается тщательно перемешанная масса, которая распределяется между валками машины, в которую одновременно заправлены верхний и нижний слои стекловаты и стеклохолст. На выходе из формовочного узла получается непрерывный стекломагниевый лист, который далее по ходу конвейера распиливают в требуемый размер.
После того как листы будут отрезаны, они подаются вместе с подложками в специальные клети – стеллажи, которые по мере заполнения снимают с конвейера и заменяют новыми. А заполненные клети отвозят на просушку. После просушки СМЛ упаковывают и складируют. После небольшой выдержки его отправляют потребителям.
Основным производителем, потребителем и поставщиком СМЛ на внешний рынок является Китай. Так как стекломагниевый лист был изобретен именно здесь. В России существует небольшое количество заводов, производящих СМЛ на собственном оборудовании и по собственным рецептурам. Но далеко не вся продукция отечественных производителей выдерживает конкуренцию с китайскими листами, как по качеству, так и по цене.
Свойства и применение СМЛ
Стекломагниевый лист обладает сочетанием полезных свойств, которые обусловливают сферу его применения. Кратко их можно перечислить в следующем виде:
- Высокая прочность
- Гибкость листа
- Водостойкость
- Огнестойкость
- Экологическая чистота
- Возможность использовать при внешних и внутренних работах
- Весьма низкий коэффициент теплопроводности
- Отсутствие необходимости в чистовой отделке по лицевой стороне
- Чистовая отделка практически любыми материалами
- Возможность чистовой отделки с изнаночной стороны
- Возможность окраски по всей глубине листа
- Возможность использования в качестве элементов покрытия пола
- Возможность монтажа на деревянный и металлический каркасы
- Возможность монтажа на клей
Недостатки, присущие СМЛ, можно свести к следующему перечню:
- Некоторая сложность обработки в связи с достаточно большой твердостью материала
- Своеобразные методы монтажа, при котором нужно оставлять зазор между листами
- Для шпаклевки швов и стыков применяют специальные шпаклевки
- Более плотные виды СМЛ требуют применения специальных самозенкующих саморезов
Применение СМЛ находят во многих областях строительства и ремонта жилых, производственных и гражданских сооружений. Исходное его предназначение – несъемная опалубка для заливки монолитных конструкций из бетона. При правильном использовании листов можно добиться исключительной экономии средств и необычного внешнего вида конструкции в целом. Особенно при использовании окрашенного СМЛ.
Все большее распространение находит стекломагниевый лист при облицовке интерьеров. Многих дизайнеров привлекает его совершенно гладкая лицевая сторона и способность хорошо изгибаться, не давая при этом трещин, подобно гипсокартону.
СМЛ так же идеально подходит для ванных комнат и санузлов. Благодаря его высокой прочности, можно совершенно спокойно использовать его в качестве обшивки инсталляций, а благодаря высокой влагостойкости СМЛ не боится потопов и прочих проблем, которые могут возникнуть у соседей сверху.
Отлично зарекомендовал себя СМЛ в качестве материала для облицовки жилых чердаков и мансардных помещений, так как он относится к негорючим материалам сам и не пропускает огонь внутрь себя под обшивку, предохраняя от перегрева и самовоспламенения стропильные системы в течение длительного времени.
Благодаря применению в СМЛ стеклоткани и стеклохолста, его поверхность не нуждается в обработке фунгицидами, так как в стекломатериалах не размножаются плесень, грибки, бактерии и вирусы. Стекломагнезит легко дезинфицировать. Поэтому он находит все большее применение в медицинских и детских учреждениях.
Более толстые листы СМЛ можно легко применять в качестве элементов сухой стяжки пола и вместо ОСП при строительстве каркасного дома. Уже многие производители перешли на применение СМЛ вместо ОСП при производстве СИП – панелей, что значительно увеличило количество вариантов облицовки фасадов и огнестойкость дома.
Состав, сырье для производства СМЛ
Сырье для СМЛ
Стекломагниевые листы (далее СМЛ) изготавливаются из хорошо освоенных промышленностью химических компонентов, но разными способами. В классический состав входят опилки, перлит, тальк, магнезит, стеклоткань, спанбонд, раствор солей магния и отходы самих СМЛ. Вяжущими компонентами являются магнезиальные смеси — каустический доломит и магнезит.
Оксид магния (MgO) получают из магнезии, методом обжига. Исходное сырье выглядит как кристаллы серого цвета, а кристаллы оксида бесцветные. MgO не горит и не взрывается, при реакции с водой выпадает в осадок Mg(OH)2, твердый и нерастворимый — поэтому используется для производства цемента. Плотность MgO 3,58 г/куб.см, температура плавления — 2825°C, кипения — 3600°C.
Хлорид магния (MgCl2) получают упариванием рассолов либо из бишофита — MgCL2-6h3O: обезвоживают минерал, потом подвергают дегидратации. Перлит тоже является веществом естественного происхождения: т.н. вулканическое стекло — это и есть вспученный перлит. Сырье (SiO2) добывают в виде горной породы, измельчают после термической обработки.
Важный момент: для производства СМЛ применяются не любые опилки, а мелкодисперсная стружка, просеянная через особое сито. Если подготовка целевая, отсев дорабатывают и снова просеивают. А вот в качестве сырья годится стружка из древесины практически любой породы.
Композиционных связующих в составе СМЛ всего 4%, но они тоже важны. Это карбонат кальция (CaCO3), фосфорная кислота (h4PO4) и клей на ее основе. Данный карбонат добывают из мела, мрамора, известняка, извлекая кальцит или аргонит для последующей переработки.
Каустический магнезит
Если вкратце — это окись магния, затворенная не водой. Когда затворителем служит раствор сернокислого либо хлористого магния, получается магнезиальный цемент. Для затворения каустического магнезита используют и другие химикаты — например, FeSO4 или ZnCL2. Сама окись магния получается при измельчении жженого магнезита (температура обжига — в диапазоне 700-800°C).
Сырьем для получения каустического магнезита служит обычный магнезит — разновидность минералов естественного происхождения. Химический состав магнезита довольно прост, в основном это MgCO3 — кристаллический или аморфный. Цвет зависит от состава примесей, аморфная порода часто белая и по виду напоминает фарфор, имеет плотность от 2,9 до 3,0 г/см.куб. Кристаллический минерал может иметь серый, белый или желтый цвет; его плотность — от 3,1 до 3,3 г/см.куб. Кристаллы гексагональной формы.
Технологический процесс состоит из 4-х этапов: добыча горной породы как сырья, ее дробление, обжиг и помол. В процессе обжига магнезит разлагается на MgO и CO2. Карбонат магния практически полностью разлагается при температуре около 650°C, хотя в реакцию вступает уже при 400°C. По мере повышения температуры обжига (более 800°C) окись магния уплотняется и кристаллизуется — получается т.н. периклаз. Это вещество в реакцию с водой почти не вступает. Вдобавок, при температуре выше 850°C начинается разложение углекислого кальция — а он в исходном сырье имеется очень часто и образует окись кальция.
Важный момент: если каустический магнезит затворяется хлористым магнием, окись кальция тоже реагирует на затворитель и получается хлористый кальций, отчего возрастает гигроскопичность и, как следствие, долговечность готовых изделий. При соблюдении технологии обжига плотность каустического магнезита составляет от 3,1 до 3,4 г/см.куб. Если температура обжига была недостаточной (недожог), плотность будет меньше 3,1 г/см.куб, а при слишком высокой (пережог) — более 3,4 г/см.куб., из-за содержания периклаза, плотность которого составляет 3,58 г/см.куб.
После обжига магнезит размалывается в специальных мельницах — к примеру, шаровых. Есть критерии качества помола: остаток на сите № 02 до 5%, на сите № 008 — до 25%. Что касается магнезиальных вяжущих, то у нас в стране до 2006 г. качественных химикатов такого назначения не выпускали совсем — не было ни одного профильного предприятия и стандартизованных параметров.
На сегодняшний день есть ПКМ-75 — каустический магнезит с одноименного предприятия (комбинат «Магнезит», расположен в г. Сатка), получаемый как побочный продукт при изготовлении периклазовых огнеупоров. Качество его оставляет желать лучшего — изделия часто растрескиваются, потому что в смеси содержится периклаз, в переменном количестве, как результат пережога оксида магния. При гидратации ПКМ-75 получается твердый магнезиальный камень с зернами периклаза, которые позже образуют гидроксид магния, увеличиваются в объеме и внутренним напряжением разрушают камень. Трещины появляются через 3 месяца после гидратации, а могут образоваться и через год. Предотвратить растрескивание магнезиального камня можно ускоренной гидратацией периклаза, пока вяжущее еще не затвердело — методом добавления активаторов либо тепловой обработкой.
Каустический доломит
Это смесь окиси магния и углекислого кальция в виде порошка. Получается в результате помола обожженного доломита (температура обжига — от 600 до 700°C). Часто содержит примеси — глину, песок, свободную окись кальция. Как от вяжущего, от каустического доломита требуется полная диссоциация магнезиального компонента, при минимальном содержании активной окиси кальция. Так, если этой окиси содержится более 3%, полезные свойства реактива сильно ухудшаются, т.е. его эффективность падает. Широко известный пример — использование некачественного вяжущего (со слишком большим содержанием окиси кальция) в изделиях с древесными наполнителями.
По химическому составу доломит является двойной углекислой солью, его формула — MgCO3-CaCo3. Плотность этого минерала составляет от 2,85 до 2,95 г/см.куб. Типичный состав породы — примерно 45% углекислого газа, 30% окиси кальция и 20% окиси магния. В естественных условиях гораздо чаще встречается именно доломит, а не магнезит. При обжиге сырья получают доломитовую известь, цемент либо каустический доломит — результат зависит от температуры.
Подробнее о свойствах продуктов обжига доломита
Рассмотрим их по возрастанию температурного режима. В диапазоне 600-800°C обжигается каустический доломит, из MgO и CaCO3. Потом его измельчают, в результате углекислый кальций не разлагается, но инертность этого компонента ухудшает качество каустического доломита по сравнению с магнезитом.
При более высокой температуре (от 750 до 850°C) обжигают доломитовый цемент. Его состав иной — туда кроме MgO и CaCO3 входит CaO. После обжига цемент размалывается в порошок. По испытаниям трамбованных образцов на прочность, такой цемент маркируют в диапазоне 25-50. Проверяется затворенный водой цемент методом сжатия, раствор в пропорции 1:3 испытывается через 28 дней твердения на атмосферном воздухе.
Обжигом окисей магния и кальция при температуре от 900 до 950°C получают доломитовую известь. А огнеупорный материал образуется при спекании доломита, когда он обжигается при температуре 1400-1450°C. После такой процедуры вяжущие свойства утрачиваются. И с водой спекшийся доломит в реакцию не вступает.
Качество каустического доломита зависит в основном от содержания окиси магния в исходном сырье и от соблюдения температуры обжига. Изначально должно быть как минимум 15% окиси магния, а свободной окиси кальция — до 2,5%. Нормальные потери при прокаливании — от 30 до 35%.
Затворение каустических доломита и магнезита
Если доломит затворять раствором солей магния, окись кальция тоже вступит в реакцию — образуется сернокислый либо хлористый кальций, что ухудшит качество затвердевшего доломита. Нормы остатков на сите при измельчении каустического магнезита и доломита одинаковы, но практика показывает, что вяжущие свойства порошка при тонком помоле существенно возрастают. Концентрация водного раствора солей магния для затворения каустических доломита и магнезита требуется одна и та же.
В процессе гидратации MgO образуется оксихлорид магния, либо другие основные соли — это и обеспечивает схватывание, а потом твердение доломита или магнезита. Т.к. в доломите (каустическом) окиси магния меньше, он менее активен. Например, для ксилолитовой смеси есть пропорция замен: магнезиально-каустический цемент эквивалентен молотому каустическому доломиту или смеси цемента с измельченным минералом — 1:1,7:1,2 соответственно. Причем под смесью цемента и порошка подразумевается пропорция 2:1 по массе, при крупности порошка до 0,15 мм. Этой смеси эквивалентен по массе состав из магнезиально-каустического цемента и молотого каустического доломита в пропорции 1:1. Т.е. налицо 4 взаимозаменяемых состава с общей пропорцией 1:1,7:1,2:1,2.
Объемная масса каустического доломита зависит от измельчения, средний показатель порошка — от 1050 до 1100 кг/куб.м. Плотность этого же вещества составляет от 2,78 до 2,85 г/куб.см.; чем больше параметр — тем выше содержание свободной окиси кальция. При комнатной температуре раствор начинает схватываться через 3-10 часов с момента затворения, заканчивает через 8-20 часов.
Свойства отвердевшего камня
Чтобы объем менялся равномерно, каустический доломит следует обжигать в режиме до температуры диссоциации CaCO3. Если содержание свободной окиси кальция от 2 до 2,5% и соотношение воды с MgO-MgCL2 неправильное — объем будет меняться неравномерно и появление трещин неизбежно.
Следует иметь в виду, что каустический магнезит прочнее доломита. При испытаниях трамбованных доломитовых образцов на растяжение через 7 суток показатели составили от 1 до 1,5 МПа, через 28 дней — от 2,5 до 3 МПа. Прочность аналогичных образцов на сжатие достигла 15-20 МПа. Раствор на этом вяжущем в пропорции 1:3 по массе при испытании трамбованных образцов через 28 суток показал предел прочности на сжатие 10-30 МПа.
Обладая таким набором свойств, каустические магнезит и доломит используются для изготовления теплоизоляции, ксилолита, фибролита и других материалов.
Затворение магнезиальных вяжущих водой
Для затворения используются разные вещества, что сказывается и на технологическом процессе. Так, при контакте окиси магния с водой происходит гидратация. Скорость реакции зависит от температуры и активности (площади поверхности, т.е. тонкости помола) MgO. От воды магнезиальные вяжущие твердеют сравнительно медленно, изделия получаются не очень прочными. Хотя на заводе «Магнезит» (в г. Сатка) добились от опытных образцов прочности в 113 кг/кв.см, затворив водой вяжущее из отходов производства и обработав бегунами 15 минут, причем испытания проводились через 28 дней с момента затворения. Для сравнения там же затворили водой вяжущее без механической обработки и протестировали через полгода — прочность оказалась всего 6 кг/кв.см.
Отдельного упоминания заслуживает морозостойкость подобных изделий: 25 циклов понизили ее лишь на 10%, причем гигроскопичность не отмечена. У затворенных хлористым магнием образцов этот параметр составил 30-40% после сравнительных испытаний.
Затворение растворами
Подразумеваются растворы хлористого (MgCL2-6h3O) либо сернокислого (MgSO4-7h3O) магния. Скорость твердения с такими затворителями гораздо выше, чем с водой. По прочности хлористый вариант превосходит сернокислый. Плотность раствора сульфата магния должна быть 1,14 г/куб.см. Есть диапазоны концентрации растворов хлористого магния (12-30 по Боме) и сернокислого (15-20 по Боме). Следует учитывать, что степень концентрации влияет на время схватывания вяжущего и на достигаемую прочность камня. Общий принцип таков: чем выше концентрация — тем медленнее схватывается вяжущее, но прочнее становится камень. При избыточной концентрации на изделиях появляются трещины и кристаллический налет на поверхности.
Соотношение компонентов учитывает содержание активной окиси магния в каустическом магнезите — приблизительно 85% от массы, а также учитывает твердый хлористый магний. Итого при затворении хлористым магнием по массе получается примерно 62-67% MgO и 33-38% MgCL2-6h3O. Если используется сернокислый магний, соотношение пересчитывается на чистый сульфат, без воды — для раствора это обычно в пределах 80-84% MgO и 16-20% MgSO4-7h3O. Если нужна самая высокая прочность вяжущего, соотношение магнезита и MgCL2-6h3O по массе должно быть в пределах 1:0,6-0,65. Излишек хлористого магния приведет к потере прочности и появлению выцветов на поверхности.
Изделия, выполненные из каустического магнезита с хлористым магнием, отличаются гигроскопичностью. И чем больше содержание хлористого магния, тем выше вероятность появления высолов. Чтобы снизить гигроскопичность, в раствор можно добавить т.н. железный купорос — им частично заменяют хлористый магний (до половины). Это кардинально решает проблему — настолько, что впору говорить о водостойкости изделий. Купорос заодно снижает вероятность появления выцветов и ускоряет схватывание. Так, чтобы понизить гигроскопичность ксилолита, используется Fe2(SO4)3.
Затворение бишофитом
Этот минерал еще называют техническим хлоридом магния. Он ничем не особенный, просто взят в качестве базового для ГОСТа 7759-73 и применяется как затворитель вяжущего гораздо шире других вариантов. Раствор бишофита делается так: соль выгружают из тары в емкость и заливают водой, через 10-12 часов сливают раствор и разбавляют его до нужной плотности. Есть свои нюансы: емкость должна быть не из металла (рекомендуется дерево или пластик), а хранить хлористый магний надо в герметичной таре и открывать только перед использованием. И вода нужна нежесткая. Вдобавок, для отделения осадка сливной кран не должен быть у самого дна емкости.
Прочие методы затворения
Чтобы затворить магнезиальный цемент, годится хлористый цинк, дисульфат натрия, азотнокислый магний, магнезиальная рапа солевых озер, карналлит. Можно и отходы химической промышленности использовать — например, от травильных цехов, добавляя серную кислоту. По химическому составу минерал карналлит представляет собой соль калия и магния — KCl-MgCl2-6h3O, из него получают собственно магний и калийные соли. Согласно ГОСТу 16109, в составе карналлита помимо хлорида магния допускается до 25% хлоридов калия и натрия.
Как затворитель карналлит востребован для производства ксилолита: его водным раствором затворяют магнезиально-каустический цемент. Требуемая плотность раствора — от 1,12 до 1,16 г/куб.см., при этом хлорида магния должно быть как минимум 32%, а прочих хлористых солей и натрия — до 25%. При затворении карналлитом, а не хлористым магнием, прочность изделий падает в полтора раза. Но чем выше концентрация раствора MgCl2, выделенного из карналлита, тем меньше в нем примесей (NaCl и KCl). Типичный метод приготовления раствора требуемой плотности таков: карналлит растворяется в воде, в пропорции 1000:638 — получается раствор плотностью 1,25 г/куб.см. Потом из смеси удаляется осадок и разбавлением достигается нужная плотность.
Известен метод затворения каустического магнезита растворами серной и соляной кислот, предложенный Б.Г.Скрамтаевым. При нем промежуточные реагенты исключаются, в результате упрощается технологический процесс и что еще важнее — в разы снижается расход кислот. Так можно использовать отходы химической промышленности, потому что рабочая концентрация кислотных растворов составляет от 5 до 15%.
Как это выглядит на практике?
Рассмотрим метод травления кислоты. Техническая соляная кислота нейтрализуется каустическим магнезитом, отчего образуется раствор хлористого магния. Делается это подальше от зданий, людей и растений, в чанах с толстыми стенками, высотой и диаметром по 1 м. Процесс идет на открытом воздухе, т.к. из емкостей испаряется кислота. Для безопасности исполнители обязательно надевают закрытые комбинезоны, резиновые сапоги и рукавицы, фартуки, респираторы. По нынешним меркам это слишком вредное производство, т.к. соляная кислота относится к прекурсорам и открытый метод травления явно губителен для экологии.
Что касается самой технологии, то нюансов в ней немного. Кислоту предварительно разбавляют водой — так, чтобы плотность раствора получилась в пределах 1,12-1,14 г/куб.см.; тогда раствор хлористого магния будет с удельным весом примерно 1,3 г/куб.см. Реакция магнезита и соляной кислоты сопровождается выделением значительного количества тепла, раствор при этом разогревается до 120°C. Если переборщить с магнезитом, вероятно образование гидрата окиси магния. Когда магнезит добавляется в раствор, интенсивно выделяется газ, а жидкость вспенивается. Если процесс идет слишком бурно, подачу магнезита останавливают, пока выделение газа не ослабеет. Определить, что нейтрализация прекратилась, очень просто: газ больше не выделяется, хотя магнезит в раствор подается.