Состав электролитов цинкования и их режимы

Защитные свойства цинкового покрытия определяются не его средней толщиной на всей поверхности изделий, а фактической толщиной на том или ином участке и степенью его равномерности и целостности. Поэтому основная характеристика электролита при цинковании — рассеивающая способность.
Виды электролитов
Для осаждения цинка разработано большое количество электролитов как кислых, так и щелочных. Из кислых электролитов следует отметить:
- сернокислые и борфтористоводородные.
А из щелочных электролитов:
- цианистые и нецианистые. К ним относятся цинкатные, пирофосфатные и аммиакатные. Последние могут иметь и слабокислую реакцию.
Основное различие между ними — это низкая рассеивающая способность кислых и высокая рассеивающая способность щелочных электролитов. Промышленное применение из кислых электролитов нашли сернокислые электролиты, из щелочных -цианистые, а также их заменители — аммиакатные.
Для цинкования используют аноды из металлического цинка в форме вальцованных пластин толщиной 5-12 мм различных размеров или сферические аноды диаметром 50 мм. Во избежание загрязнения электролита аноды необходимо помещать в чехлы из кислотостойкой ткани (стеклоткань, шерсть). Аноды следует периодически очищать травлением или щетками. Сферические аноды более целесообразны, так как имеют равномерный износ и позволяют легко регулировать глубину погружения.
Кислые электролиты имеют плохую рассеивающую способность. Кроме того, покрытия, полученные в кислых электролитах, обладают более грубой структурой и меньшей коррозионной стойкостью, чем покрытия, полученные в щелочных электролитах. В то же время кислые электролиты устойчивы, допускают применение высокой плотности тока, особенно при перемешивании и высоком (близком к 100 %) выходе цинка по току. Покрытия имеют светлый цвет, характеризуются повышенной пластичностью, прочным сцеплением с основным металлом и могут выдержать различную механическую обработку. Поэтому кислые электролиты широко используют для нанесения покрытий на малорельефные изделия, а также полуфабрикаты — листы, проволоки, полосы.
Сернокислые электролиты отличаются простотой состава, низкой стоимостью компонентов и хорошим качеством покрытий даже при больших изменениях состава электролита и режима его работы. Так, температурный режим электролита колеблется в пределах 15-30 °С, а практически сернокислые электролиты позволяют вести осаждение цинка даже при температурах около 0 °С и ниже.
Для составления сернокислого электролита требуются следующие материалы:
- Сернокислый цинк ZnSО4*7Н2О — белый кристаллический порошок, растворимость в воде при 20 °С — свыше 900 г/л;
- Сернокислый натрий Na2SО4*10Н2О — бесцветные кристаллы, растворимость в воде при 20 °С — более 400 г/л. Вводится для повышения электропроводности электролитов;
- Сернокислый алюминий Аl2(SО4)3*18Н
- Пекстрин — желтый порошок, растворимый в воде с образованием клейкого мутного раствора. Применяется для создания мелкокристалличности покрытия. Качество и эффективность добавки следует проверять, растворением отдельной пробы в опытной ванночке;
При составлении сернокислого электролита желательно каждый из компонентов растворять в отдельности в теплой воде. После отстаивания и фильтрации растворы сливают вместе в рабочую ванну цинкования. Затем электролит доливают водой до заданного уровня и проверяют величину рН, корректируя ее 2-3%-ным раствором серной кислоты или едкого натра. После этого прорабатывают электролит на случайных катодах до получения светлых и гладких покрытий и приступают к его эксплуатации.
Некоторые составы кислых электролитов представлены в табл. 5.7.
Сернокислый электролит номер 1 предназначен для деталей простой конфигурации, позволяющий получать светлые матовые покрытия. Электролит номер 2 пригоден для непрерывного цинкования проволоки или ленты, с повышением плотности тока до 8-10 А/дм2. Следует иметь ввиду, что при плотности тока более 2 А/дм2 обработку производят при перемешивании и фильтрации электролита. При введении в электролит блескообразователей типа дисульфонафталиновой кислоты покрытия (электролит номер 3) получаются очень светлые, блестящие или полублестящие.
Из кислых электролитов следует для отдельных работ рекомендовать борфтористоводородный. По стоимости компонентов он дороже сернокислого, но позволяет применять плотности тока от 10 и выше А/дм2, а насыщение водородом и, следовательно, водородная хрупкость в несколько раз ниже, чем при цинковании в других электролитах. Для электролита характерен следующий состав (г/л) и режимы:
- цинк борфтористоводородный — 280-300;
- аммоний борфтористоводородный — 28-30;
- аммоний хлористый — 28 30;
- солодковый корень — 0,5-1,0;
- кислота борфтористоводородная (свободная) вводится для достижения кислотности на уровне рН — 1,4-2;
- температура, °С — 15-25;
- плотность тока доходит, А/дм2 — до 10;
- температура, °С — 50-55;
- плотность тока, А/дм2 — до 50.
Таблица 5.7. Составы и режимы работы электролитов.
Компоненты |
Содержание компонентов (г/л) в электролите |
||
1 |
2 |
3 |
|
Сернокислый цинк |
200-250 |
400-500 |
200-250 |
Сернокислый натрий |
50-100 |
50-100 |
— |
Сернокислый алюминий |
|
20-30 |
25-30 |
Декстрин |
8-10 |
8-10 |
8-10 |
Борная кислота |
— |
— |
25-30 |
Блескообразователь ДЦУ и У2 |
|
— |
1,5-2,5 |
Температура, °С |
15-30 |
15-30 |
15-30 |
Величина рН |
3,6-4,4 |
— |
4,0-4,2 |
Плотность тока, А/дм2 |
1-4 |
8-10 |
1-3 |
Выход по току |
96-98 |
96-98 |
— |
При указанных режимах выход по току составляет около 90 %.
Щелочные электролиты обладают хорошей рассеивающей способностью, а покрытия, полученные в этих электролитах, — более высокой коррозионной стойкостью. Однако щелочные электролиты менее устойчивы, допустимая плотность тока в них ниже, и с повышением ее заметно снижается выход цинка по току. Такие электролиты применяют для цинкования изделий сложной формы. По составу щелочные электролиты подразделяются на цианистые, аммиакатные и цинкатные.
Цианистые электролиты
Цианистые электролиты обладают высокой рассеивающей способностью и служат для цинкования изделий сложной формы в стационарных, колокольных и барабанных ваннах. Сами покрытия получаются светлыми, гладкими и отличаются мелкокристаллической структурой. В настоящее время существует несколько вариантов их составов, но все они состоят из трех обязательных компонентов: окиси цинка, цианистого натрия и едкого натра, которые сочетаются между собой в различных соотношениях, образуя сложные комплексные соединения. Кроме того, они могут отличаться различными добавками, способствующими получению светлых, блестящих или полублестящих покрытий.
Однако следует иметь в виду, что цианистые электролиты очень ядовиты, и обращаться с ними необходимо очень осторожно. Токсичность их повышается, если в электролите мало едкого натра, в результате чего образуется синильная кислота — сильнейший яд.
Для составления цианистых электролитов требуются следующие химикаты:
- Окись цинка ZnO;
- Цианистый натрий NaСN — белый порошок, растворимость в воде до 600 г/л. Весьма ядовит. При составлении электролитов применяется только в предварительно растворенном состоянии. Служит для получения комплексной соли Na2Zn(СN)4;
- Едкий натр NaОН;
- Глицерин технический — вязкая прозрачная жидкость, применяется для повышения мелкокристалличности осадков цинка;
- Сернистый натрий Na2S — белая кристаллическая масса, легко растворимая в воде, имеет характерный запах. Вводится в электролит для осаждения тяжелых металлов — меди, свинца и железа.
При составлении электролита сухую окись цинка замешивают водой до сметанообразного состояния и затем вводят в раствор цианистого натрия. После этого приливают крепкий раствор едкого натра, доводят электролит водой до рабочего уровня и вводят добавку глицерина. Сернистый натрий добавляют в последнюю очередь и дают осесть возможному осадку тяжелых металлов, затем приступают к эксплуатации.
Составы и режимы работы наиболее применяемых электролитов приведены в табл. 5.8.
Покрытия, полученные в электролите номер 1 после осветления в 3%-ном растворе азотной кислоты и пассивирования в 5%-ном растворе хромового ангидрида, становятся блестящими и не оставляют следов от захвата руками. Электролит 2 предназначен для получения светлых матовых покрытий, создающих после пассивирования на поверхности яркую радужную пленку. Электролит 3 характеризуется высокой рассеивающей способностью и особо пригоден для колокольных и барабанных ванн.
Для замены токсичных цианистых электролитов разработаны и используются аммиакатные, аммиакатно-уротропиновые, цин-катные, пирофосфатные и другие электролиты. Они не ядовиты, просты по составу и дешевы, обладают высокой электропроводностью и хорошей рассеивающей способностью цианистых электролитов. Выход цинка по току в них значительно выше, чем в цианистых.
Наиболее высокой рассеивающей способностью, приближающейся к цианистым электролитам, отличаются аммиакатные, в частности аммиакатно-уротропиновые электролиты. Для приготовления таких электролитов необходимы следующие основные химикаты:
- хлористый аммоний NH4Cl технический — белый кристаллический порошок, растворимость в воде — до 300 г/л. Горячий крепкий раствор хлористого аммония переводит окись цинка в растворимые комплексы;
- окись цинка ZnO — может быть заменена сухими цилковыми белилами. Белый порошок, нерастворимый в воде, но растворимый в концентрированных растворах цианистого натрия, едкого натра, а также в горячих концентрированных растворах хлористого аммония и сернокислого аммония;
- уксуснокислый аммоний — белый кристаллический порошок.
Таблица 5.8. Составы и режимы цианистых электролитов.
Компоненты |
Содержание компонентов (г/л) в электролите |
||
1 |
2 |
3 |
|
Окись цинка |
10-20 |
40-45 |
8-10 |
Цианистый натрий |
20-30 |
75-85 |
15-25 |
Едкий натр |
50-70 |
40-60 |
10-25 |
Сернистый натрий |
0,5-5,0 |
— |
— |
Глицерин |
0,5-1,0 |
— |
— |
Температура, °С |
15-40 |
15-25 |
15-25 |
Плотность тока, А/дм2 |
1-2 |
1,5-7 |
0,5-2 |
Выход по току, % |
80-83 |
75-80 |
70-80 |
Для приготовления электролита необходимо подогреть концентрированный раствор хлористого аммония до 60-70 °С и прибавить к нему при непрерывном помешивании окись цинка или гидрат окиси цинка. После растворения соединений цинка в растворе хлористого аммония и образования комплексных солей цинка в полученный раствор вводят остальные компоненты, доводят водой до рабочего уровня и устанавливают правильную величину рН. При этом если величина рН получилась менее 7, то корректировку рН производят водным раствором аммиака, а при рН = 8,5 и выше эту величину доводят до заданной раствором уксусной кислоты. После этого электролит следует проработать на случайных катодах.
Один из таких электролитов имеет следующий состав (г/л) и режим работы:
- окись цинка — 25-40;
- хлористый аммоний — 200-220;
- уксуснокислый аммоний — 80-100;
- уротропин — 20-25, диспергатор НФ, мл/л — 6-8;
- препарат ОС-20 — 4-5;
- температура, °С — 20-35;
- величина рН — 7,5-8,2;
- плотность тока, А/дм2 — 1-3.
Следует отметить, что электролиты на основе хлористого аммония содержат агрессивный ион хлора. Поэтому промывка деталей в воде (после цинкования) должна быть тщательной, особенно для деталей со сложным профилем, глухими отверстиями и щелевыми зазорами. Пренебрежительное отношение к операции промывки может привести к ускоренной коррозии.
Основной недостаток аммиакатных электролитов — наличие в сточных водах солей аммония, которые недопустимы по требованиям санитарии (допускается не более 2,5 мг/л). В связи с этим применение аммиакатных электролитов в отличие от цинкатных сокращается.
Основу цинкатных электролитов составляют окись цинка и едкий натр. Ориентировочный состав такого электролита (г/л) и режим работы следующие:
- окись цинка — 15-16;
- едкий натр — 150-160;
- полиэтиленполиамин — 1,2-1,6;
- температура, °С — 15-25;
- плотность тока, А/дм2 — 2,0-3,0;
- выход по току, % — 90-95.
Электролит допускает колебания температуры с перегреванием его до 40-50 °С. Для сложнопрофилированных деталей в электролит вводится добавка фенолформальдегидной смолы. Приготовление электролита не имеет специфических особенностей.
Пирофосфатный электролит получил наименьшее распространение, но рассеивающая способность его достаточно высока. Его основу составляет пирофосфорнокислый натрий Na4Р2О7*10Н2О и фосфорнокислый аммоний двузамещенный (NН4)2НРО4. Состав электролита (г/л) и его режим работы следующие:
- пирофосфорнокислый натрий — 180-200;
- сернокислый цинк — 50-60;
- фосфорнокислый аммоний двузамещенный — 16-20;
- декстрин — 3,0-5,0;
- температура, °С — 50-55;
- величина рН — 8,0-8,5;
- катодная плотность тока, А/дм2 — 1,0-3,0;
Электролит пригоден для деталей средней конфигурации.
Возможно Вас так же заинтересуют следующие статьи: comments powered by HyperCommentsГальваническое цинкование металла: технология, оборудование
Гальваническое цинкование – эффективный и недорогой, а потому распространенный способ защиты черных металлов от коррозии. Чаще всего его используют при производстве метизов и крепежных изделий, а также стальной сетки.
Способы нанесения цинкового покрытия
Антикоррозионное цинкование выполняется различными способами, а срок службы покрытия зависит от толщины защитного слоя.
Способ нанесения покрытия зависит от его необходимых свойств, размеров изделия, условий его дальнейшей эксплуатации.
Самый простой и технологичный, но недостаточно обеспечивающий стойкость к механическим воздействиям защитного слоя, – это холодное цинкование с помощью грунтов, в которых в большом количестве содержится высокодисперсный цинковый порошок.
По объему цинковальных производств второе место занимает горячее цинкование. Покрытие, получаемое таким способом, качественное и долговечное, но экологически небезопасное, так как используется расплав цинка, да еще на поддержание его температуры немногим меньше 500 °С необходимо большое количество электроэнергии, химические методы подготовки поверхности.
Очень похож на горячее цинкование более технологичный, но менее производительный метод термодиффузионного нанесения защитного слоя. Он используется, когда задаются высокие требования к толщине и внешнему виду покрытия.
Еще один способ цинкования – это газо-термическое напыление, которое используется для защиты крупногабаритных изделий и конструкций, которые в ванну просто невозможно поместить.
Гальваническое цинкование лишено многих недостатков других способов нанесения покрытия и имеет свои положительные стороны.
Преимущества гальванического цинкования
Способ нанесения цинкового покрытия путем электролиза наиболее распространен.
Основным достоинством, из-за которого применяется именно гальваническое цинкование металла, является высокая степень защищенности поверхности материала от коррозии. Тонкий слой цинка увеличивает срок службы изделий в несколько раз, а значит, и снижает затраты на их техническое обслуживание и замену.
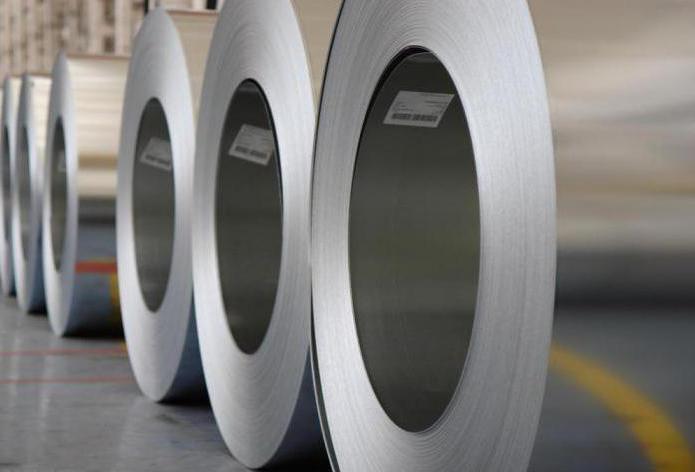
Покрытие получается ровным, без потеков и капель, сохраняется и форма, и размер изделия. Нанести его можно на предметы любой, даже самой сложной формы.
Гладкие и блестящие декоративные покрытия не требуют в большинстве случаев дополнительной обработки.
Кроме того, сам процесс нанесения цинкового покрытия требует незначительных расходов, а гальванические агрегаты обладают высокой производительностью.
Недостатки гальванического цинкования
Способ нанесения защитного покрытия электролизом не лишен недостатков.
Основной недостаток – низкая адгезия цинка с металлом, из-за которой поверхность изделия необходимо тщательно зачищать.
Минусом также является образование в процессе нанесения покрытия ядовитых отходов, требующих серьезной очистки.
Несоблюдение режимов может привести к наполнению водородом основного металла, что приводит к хрупкости самого изделия и к нарушению качества покрытия.
Принцип действия
Гальваническое цинкование основано на принципе защитного действия, который определяется разностью электрохимических потенциалов цинка и железа. Поскольку цинк имеет меньший электрохимический потенциал, покрытие из него является протекторной защитой для черных металлов. То есть во влажной среде электрохимической коррозии подвергается именно он.
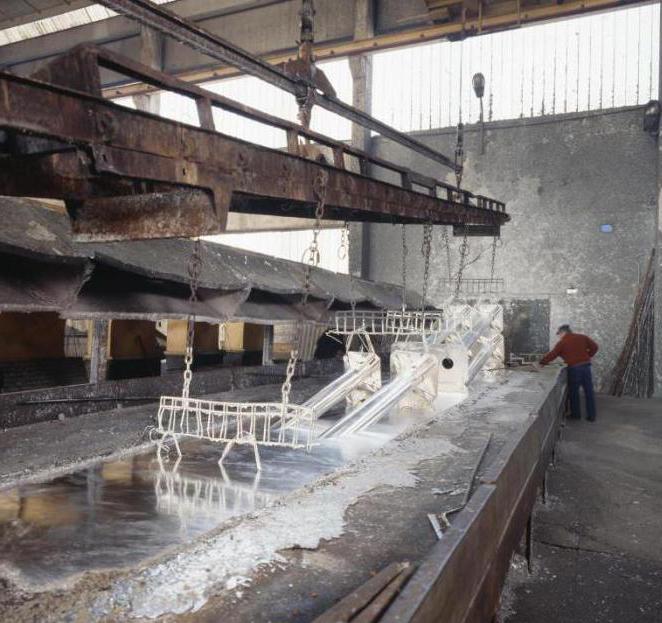
При окислении железа образуются оксиды, имеющие больший объем, чем первоначальный металл. Оксидная пленка становится рыхлой и пропускает к еще не окисленному металлу кислород. А на цинке при окислении пленка образуется тонкая и плотная, она не пропускает кислород вглубь металла, защищая не только покрытие, но и основной металл под ним.
Виды гальванического цинкования
Цинкование гальваническое – технология, представляющая собой электролиз, т. е. электрохимические окислительно-восстановительные процессы в электролите под действием постоянного электрического тока.
По составу электролита цинкование делится на три вида: кислотное, цианидное и щелочное.
Чаще всего используется метод нанесения цинкового покрытия в слабокислых электролитах, особенно для чугунных и стальных деталей сложной конфигурации. Изделия из углеродистых и легированных сталей при этом виде цинкования меньше подвергаются возникновению водородной хрупкости, да и внешний вид получается превосходный, с замечательным декоративным эффектом в широкой цветовой гамме.
Дополнительная защита при цинковании
Защитное действие покрытий из цинка зависит от его толщины, которая при гальваническом нанесении всего 5 мкм, и характера электролита.
В некоторых случаях защитные свойства цинкового покрытия увеличиваются пассивированием, фосфатированием или покраской.
Пассивирование (хроматирование) – химическая обработка изделий в растворах с хромовой кислотой либо ее солями, в результате которой на поверхности образуются хроматные пленки. Это процесс усиливает не столько защитные свойства, сколько декоративные, потому что в результате усиливается блеск покрытия, и оно может быть окрашено в различные цвета.
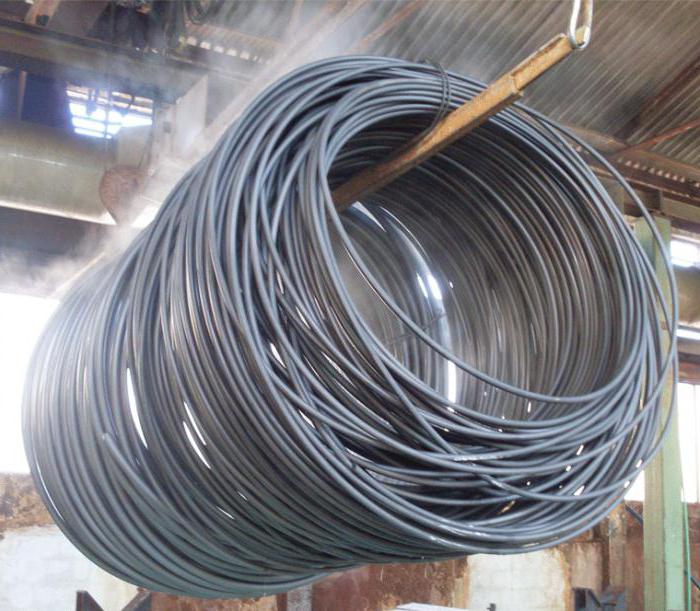
При фосфатировании (обработке в солях фосфорной кислоты) оцинкованных изделий на поверхности пленка образуется фосфатная. После фосфатирования может еще наноситься лакокрасочное покрытие.
Этапы гальванического цинкования
На производстве гальваническое цинкование состоит из нескольких технологических процессов, каждый из которых завершается промывкой водой в проточной ванне или щеточно-моечным способом.
Сначала изделия тщательно очищаются от ржавчины, окалины, технологической смазки, остатков охлаждающей жидкости или краски и обезжириваются в щелочных растворах. Затем происходит обезжиривание электролитическое.
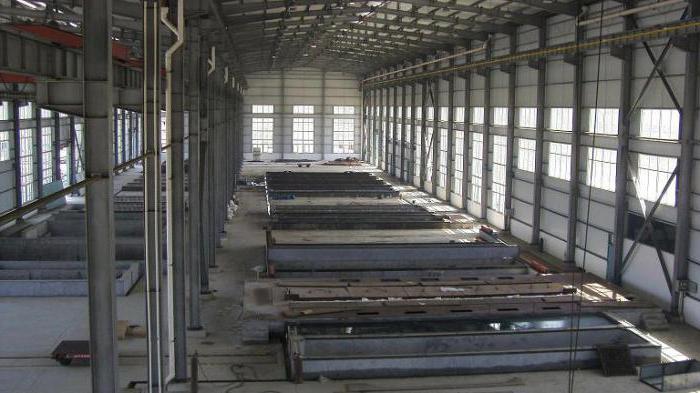
После него протравливаются в водном растворе соляной кислоты, при котором поверхность окончательно очищается без нарушения поверхностного слоя и происходит ее декапирование – активация перед нанесением цинкового покрытия. Только потом производится собственно цинкование.
После него, при необходимости, изделия осветляются и очищаются от окисной пленки в водном растворе азотной кислоты, затем фосфатирование, пассивация и сушка.
При цинковании различных изделий могут выполняться дополнительные операции. Например, полосу перед цинкованием разматывают, сваривают концы, правят, а после него промасливают и сматывают.
Оборудование гальванического цинкования
Гальваническая линия — это определенная последовательность промывочных и технологических ванн, в которых создаются одно- или многослойное цинковое покрытие с требуемыми функциональными свойствами.
В соответствии с объемами производства используется оборудование с различной степенью механизации. На крупных предприятиях устанавливаются механизированные линии с автоматическим управлением. Существуют линии с частичным или полным ручным управлением, а также мини-линии.
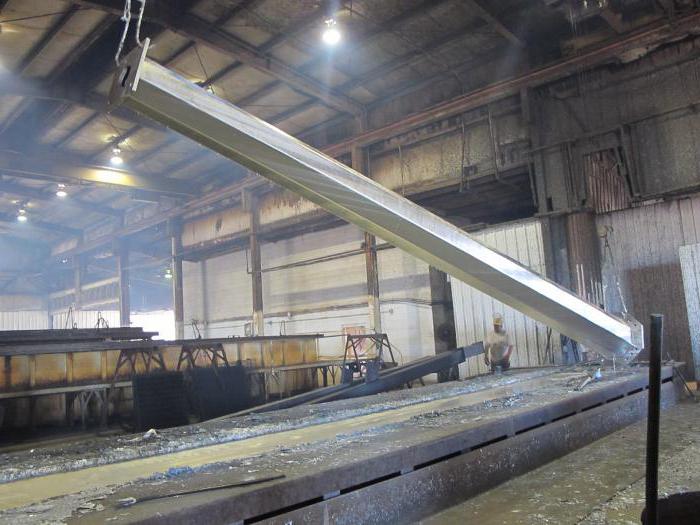
Линия гальванического цинкования состоит не только из ванн. В нее входят транспортные системы различной конструкции, обязательно оборудование для очистки сточных вод, вспомогательное оборудование, к которому относятся приспособления для цинкования, ТЭНы, теплообменники, катодные и анодные штанги.
В дополнительное оборудование входят системы вентиляции, сушильные камеры и шкафы, холодильное оборудование, фильтровальные установки, оборудование получения демиводы, насосы.
Электролиты для цинкования
Для гальванического цинкования в зависимости от назначения изделия применяют электролиты, которые делятся на две основные группы.
Электролиты, в которых цинк находится в виде простых гидратированных ионов, называют простыми кислыми. Это борфтористоводородные, сульфатные и хлоридные растворы.
Сложные комплексные кислые и щелочные электролиты содержат цинк в комплексных ионах с положительным и отрицательным зарядом. Это аммиакатные, пирофосфатные, цианидные и другие растворы.
От того, какой электролит применяется, зависит в первую очередь скорость осаждения, а затем качество осадков цинка на изделии (катоде).
Из комплексных электролитов цинк оседает на катоде при высоком рассеивании ионов. При увеличении плотности тока выход металла снижается и увеличивается выход водорода.
Поэтому цинкование в сложных электролитах производится при малой плотности тока, а покрытие получается очень качественное, мелкозернистое и равномерное.
В слабокислых простых электролитах гальваническое цинкование, в домашних условиях в том числе, проходит при большой плотности тока, с большей, чем при использовании сложных растворов, скоростью. Внешний вид изделий получается хороший, но покрытие не очень качественное и подходит только для изделий достаточно простой формы.
Гальваническое цинкование
Технологический процесс непосредственно цинкования происходит в ванне с электролитом. В нее опускаются изделия из черного металла, к которым через специальные электроды подводится электрический ток (катод), и чистый цинк в виде шаров или пластин, уложенных в специальные сетчатые секции (анод).
В процессе электрохимической реакции под воздействием электрического тока плотностью от 1 до 5 А/дм цинк растворяется в электролите, затем его ионы оседают на катоде, образуя гальваническое покрытие толщиной 4-25 мкм.
Именно с использованием такой технологии получают крепежные изделия (болты и гайки) с равномерным и блестящим покрытием.
Автоматизированная линия для гальванического цинкования
Современная линия гальванического цинкования – это полностью автоматизированная линия, на которой осуществляются все этапы нанесения покрытия, включая сварку и качественное обезжиривание изделий разного назначения и конфигурации.
Автоматическая линия в общем случае состоит из комплекта технологических гальванических ванн, модульных выпрямителей, стенда загрузки/разгрузки, транспортного оборудования, оборудования для вытяжной вентиляции, подвода воды и отвода канализационных стоков, металлокаркаса с трапом обслуживания.
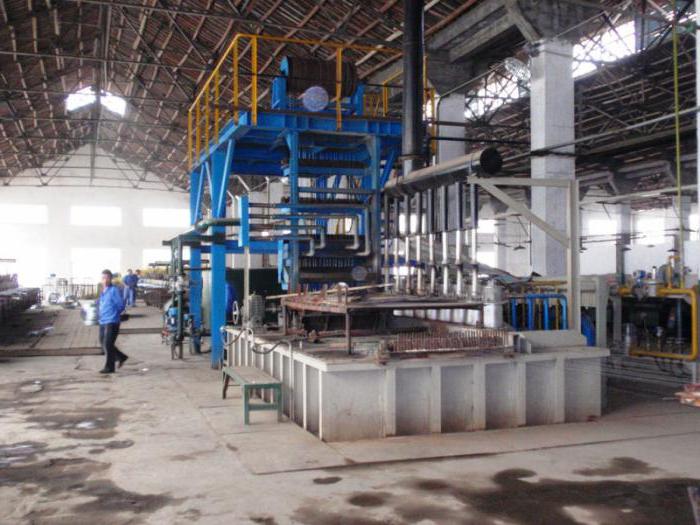
Гальванические ванны могут изготавливаться из нержавеющей стали, стали, футерованной полимерными материалами или резиной. Современные ванны, сваренные из листовых полимеров, все больше вытесняют металлические емкости. Выбор материала ванн зависит от состава и концентрации электролита и рабочей температуры.
Коммуникации систем водоснабжения и канализации, и в большинстве случаев вентиляции располагаются под ваннами и также изготавливаются из полипропилена.
Размеры линии определяются ее производительностью и габаритами гальванических ванн.
Гальваническое цинкование происходит с образованием сточных вод с высокой концентрацией ионов тяжелых металлов. Поэтому их отстаивают, фильтруют, нейтрализуют, используют химическое осаждение, сорбцию и другие процессы в емкостях из инженерных полимеров.
Электролитическое цинкование в домашних условиях
Гальваническое цинкование, своими руками производимое, начинается с подбора материалов. Электролитом может служить раствор хлорида цинка и соляной кислоты в дистиллированной воде. Это так называемая паяльная кислота, которая чаще всего используется в домашних условиях. Умельцы протравливают цинк в аккумуляторной серной кислоте и получают электролит ZnSO4, но этот процесс опасен, поскольку при реакции выделяется взрывоопасный водород и теплота. В электролите ни в коем случае не должно быть осадка из нерастворенных кристаллов соли.
Чистый цинк можно купить в магазине химреактивов или на радиорынке, а можно получить из солевых батареек или плавких предохранителей, сохранившихся со времен Советского Союза.
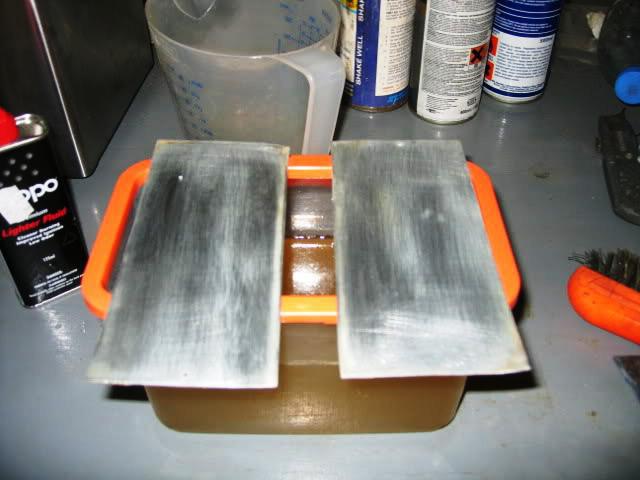
Гальванической ванной может служить стеклянная или пластиковая емкость. В нее устанавливаются штативы для анода и катода. Анод – это пластина цинка, к которой от источника питания подсоединяется «плюс». Чем больше анод, тем более равномерным получится покрытие на катоде, изделии, на которое будет наноситься защитное покрытие. Анодов может быть несколько, их можно располагать вокруг катода на одинаковом расстоянии, чтобы его поверхность покрывалась цинком равномерно и одновременно со всех сторон. К катоду подсоединяется «минус» источника питания.
Даже когда в домашних условиях производится цинкование гальваническое, технология обязательно включает тщательную очистку и обезжиривание детали, а также ее активацию в растворе кислоты.
Источник питания – это автомобильный аккумулятор с лампой накаливания небольшой мощности или другого потребителя в схеме, чтобы сила тока в цепи была ниже, или блок питания с постоянным напряжением на выходе. Главное, чтобы не было бурного кипения электролита в процессе цинкования.
Собственно цинкование происходит, когда аноды и катод опущены в электролит и замкнута электрическая цепь. Чем дольше длится процесс, тем толще слой цинка получается на изделии.
С помощью гальванического цинкования защитное покрытие на изделиях становится точным, равномерным и гладким, с декоративным эффектом. Его используют и в промышленности, и в домашних условиях, несмотря на то что требуется очистка сточных вод от экологически опасных отходов.
Гальваническое цинкование: оборудование, подготовка, проведение
Популярный способ защиты металлических изделий от появления ржавчины — оцинковка заготовки. На поверхность детали наносится слой цинка, который увеличивает ее эксплуатационные характеристики, срок службы. Существует несколько вариантов выполнения этого технологического процесса. Особо популярно гальваническое цинкование.
Ванны для гальванического цинкования (Фото: Instagram / pt_plast)
Общие сведения и назначение
Многие стальные изделия эксплуатируются в местах с высокой влажностью. Со временем это приводит к появлению ржавчины, разрушению металлоконструкций. Без дополнительной защиты детали придут в негодность.
Цинковый слой, нанесенный по определенной технологии, принимает негативное воздействие влаги, щелочей, кислот на себя. Антикоррозийные свойства сохраняются до полного разрушения цинковой пленки.
С развитием технологического прогресса появилось несколько способов нанесения цинкового слоя на разные металлы. Цинкование своими руками возможно, но для этого необходимо точно изучить выбранный метод, подготовить оборудование.
Методы
Существует несколько методов цинкования металлических конструкций. Они выбираются зависимо от того, какие технические характеристики защитного слоя необходимо получить. Виды обработки:
- Горячая оцинковка металла. Процедура проводится в ваннах, заполненных расплавленным цинком. Перед погружением в емкости металлические конструкции проходят несколько этапов подготовки. После подготовительных действий изделие покрывается флюсом, погружается в расплавленный металл. Последний этап — охлаждение.
- Холодная оцинковка металлических деталей. Для проведения этой процедуры используется специальный химический состав Цинконол. Его наносят кистью или валиком. После нанесения, на поверхности металла образуется прочная защитная пленка.
- Термодиффузионная оцинковка. Второе название метода — шерардизация. Металлоконструкцию помещают в контейнер, засыпают цинком. После этого внутреннее пространство нагревается до 2600 градусов. Цинк принимает газообразное состояние, проникает в верхние слои обрабатываемой детали.
- Гальваническое цинкование металла. На поверхность обрабатываемого изделия воздействует электричество. Образуется защитная пленка, толщиной 30 мкм.
- Газотермическое напыление. При обработке применяется сухая цинковая смесь, которая напыляется на поверхность металлического листа в газовой среде.
При гальваническом методе соединение защитной пленки с основой происходит на молекулярном уровне. Показатель адгезии изменяется зависимо от загрязнения детали масляными пятнами. Чем их меньше, тем лучше соединение.


Газотермическое напыление цинка
Преимущества и недостатки
Преимущества электролитического метода покрытия цинком:
- готовое покрытие не требует дополнительной обработки;
- цинковая пленка ровная, без подтеков;
- можно покрывать изделия разной формы, размеров.
У данной технологии есть два существенных минуса. Первый — низкий показатель адгезии. Второй недостаток — выделение ядовитых веществ при проведении работ.
Оборудование
Гальваника подразумевает применение механического или автоматического оборудования:
- питания для гальванической ванны;
- камеры для сушки;
- каркаса из металла;
- ванны для нанесения цинка;
- труб, по которым будет поступать, отходить рабочая жидкость;
- мощной вытяжки;
- гальванических барабанов;
- систем фильтрующих аппаратов;
- центрифуги для ускорения процесса сушки.
Автоматические линии дополнительно оборудуются электроавтоматикой, панелью для настройки и задания алгоритмов.
Подготовка к выполнению процедуры
Цинкование металла в домашних условиях, как и на производстве, делится на два этапа:
- подготовка поверхности;
- проведение основных работ.
Подготовка состоит из нескольких действий:
- Стороны металлоконструкции очищаются от мусора щеткой по металлу.
- Заготовка обезжиривается, чтобы убрать подтеки масла.
- Очищающий состав смывается водой.
Для снятия слоя ржавчины используется соляная кислота. После использование кислоты железо, сталь или другой обрабатываемый металл необходимо промыть под проточной водой.
Щетка для металла (Фото: Instagram / hoz.magazin)
Как выполнить процедуру в домашних условиях?
Чтобы выполнить гальваническое цинкование в домашних условиях, необходимо подготовить оборудование, расходные материалы, изучить технологию обработки в теории.
Можно собрать аппарат для гальваники самостоятельно. Для этого нужен источник постоянного тока, приспособление для удерживания детали, электрод. Рабочей жидкостью будет выступать любой раствор на основе соли, которой содержит цинк.
Факторы, влияющие на толщину защитного слоя:
- температура рабочего раствора;
- форма металлоконструкции;
- плотность воздействия напряжения на единицу обрабатываемой площади;
- температура электролита.
Чтобы приготовить качественный рабочий раствор, необходимо вскрыть рабочий аккумулятор, слить из него электролита. Затем растворить в электролитической жидкости цинк. Перед использованием готовый раствор необходимо процедить.
Наносить цинкосодержащий состав нужно в два слоя, чтобы повысить антикоррозийные свойства. Способы получения цинка для приготовления рабочего раствора:
- переплавка предохранителей, которые изготавливались во времена СССР;
- купить в магазинах с химическими реактивами;
- из солевых батареек.
При цинковании рабочий состав не должен сильно бурлить. Это указывает на большую силу тока, которую нужно снизить. Со временем на поверхности катода образуется защитный слой, который будет постепенно увеличиваться. Оцинкованная деталь остужается, очищается от остатков паяльной кислоты.
Гальваническое цинкование — метод повышения коррозионной стойкости металла. Он подразумевает применение напряжения, направленного на активизацию цинкосодержащего раствора. При желании можно обрабатывать металлические заготовки самостоятельно.
Смотрите видео о гальваническом цинковании в домашних условиях:
Электролиты цинкования | Цинковый портал
Существует большое разнообразие электролитов для цинкования, т. к. цинк способен образовывать различные растворимые и нерастворимые соединения в щелочных и кислых средах. Реакции, при которых образуются цинковые водорастворимые соединения (в электролитах для цинкования), протекают в диапазоне кислотности (рН) от 0 до 14.
Электролиты для цинкования. Классификация и виды
Электролиты для цинкования по характеру среды делятся на
· кислые (хлоридные, сульфатные,кремнефтористоводородные , борфтористоводородные)
· слабокислые электролиты (сульфатно — аммонийные, хлоридно -аммонийные, хлоридные безаммонийные),
· слабощелочные или нейтральные (аммиакатные, пирофосфатные, аминокомплексные),
· щелочные электролиты (цианидные, цинкатные).
Электролиты для цинкования по составу могут быть
· простыми (к ним относятся кислые и слабокислые электролиты),
· комплексными.
В простых электролитах цинкования металл находится в виде катионов(Zn^(2+)*mH_2 O) . Механизм разряда цинка на катоде основывается на реакции присоединения к каждому иону цинка двух электронов: Zn^(2+)*mH_2 O+2¯e=Zn+mH_2 O. Двухвалентные ионы цинка разряжаются при низкой катодной поляризации (20-40 мВ). Выход по току в простых электролитах достигает 98%. Рассеивающая способность простых электролитов низкая. Структура осажденного слоя имеет неравномерное, крупнокристаллическое строение.
Комплексные электролиты цинкования характеризуются наличием в составе рабочего раствора комплексных анионов цинка: [〖Zn(CN)〗_4 ]^(2-) , [〖Zn(OH)〗_4 ]^(2-), [〖Zn(CN)〗_4 ]^(2-). Механизм разряда ионов цинка может протекать двумя способами:
- [Zn〖(CN)〗_4 ]^(2- )= Zn^(2+)+ 4CN^-; Zn^(2+)+2¯e=Zn.
- [Zn〖(CN)〗_4 ]^(2-)+2¯e=Zn+4CN^-.
Осаждение цинка на катоде (разряд) происходит при высокой катодной поляризации. Выход по току в различных по химическому составу комплексных электролитах значительно уменьшается, по сравнению с простыми. Рассевающая способность увеличивается. Микроструктура цинкового покрытия имеет мелкозернистое строение.
Основные технологические параметры электролитов для цинкования
Основными отличительными признаками цинкования в различных электролитах являются:
· катодная поляризация – изменение разряда на катоде при изменении величины плотности тока (при высокой катодной поляризации высокая электропроводность электролита),
· поляризуемость электролита в процессе осаждения цинка (чем выше поляризуемость (потенциал) при изменении плотности тока, тем лучше рассевающая способность электролита),
· кинетика и механизм электроосаждения цинка.
На критерии поляризации и поляризуемости активное влияние оказывает не только тип электролита (простой, комплексный), но и рабочий интервал температур при цинковании, химический состав, концентрация составляющих компонентов, блескообразующие активные добавки. Самые высокие показатели поляризуемости присущи щелочным электролитам (цианидным, цинкатным).
Величина разряда комплексных ионов на катоде выше, чем катодная поляризация гидратированных ионов. Следовательно, рассеивающая способность увеличивается, структура поверхностного слоя становится равномерно мелкозернистой, плотной. Однако выход по току уменьшается. Цинк на аноде в результате гальванического процесса растворяется с образованием положительно заряженных гидратированных ионов и комплексных анионов.
Сравнительный анализ электролитов для цинкования
Цинковые соли в кислых и слабокислый электролитах хорошо растворимы в воде, поэтому анодное растворение цинка происходит легко, без затруднений и практически без выделения водорода. Процесс протекает при невысокой катодной поляризации, с высокими показателями выхода по току и скоростью осаждения, низкой рассеивающей способностью.
К основным достоинствам цинкования в кислых электролитах относятся:
· высокая производительность процесса,
· стабильность и простота,
· низкий процент наводораживания готовой продукции,
· отсутствие в процессе производства ядовитых веществ.
Используются кислые электролитические растворы для оцинковки деталей простой конфигурации (проволоки, листов, ленты, стержней, пластин).
В щелочных электролитических растворах анодно — катодные процессы затруднены. Это объясняется тем, что
· выделение цинка на катоде происходит из комплексных соединений (в щелочной среде происходит гидролиз солей цинка с образованием нерастворимого осадка, поэтому в рабочем растворе необходимы компоненты, которые способны образовывать водорастворимые соединения цинка),
· разряд цинка сопровождается выделением водорода (при увеличении плотности тока возрастает потенциал выделения цинка на катоде и возрастает скорость выделения водорода),
· в составе рабочего раствора присутствуют различные загрязнения и примеси,
· существует возможность протекания на аноде как электрохимических, так и химических реакций растворения цинка.
Все вышеперечисленные факторы уменьшают показатель выхода металла по току.
В щелочных электролитах за счет высокой катодной поляризации происходит равномерное распределение осаждаемого цинка на катодной поверхности, поэтому их используют при цинковании изделий различной геометрической формы и конфигурации. К недостаткам щелочного цинкования можно отнести следующие показатели:
· наводораживание оцинкованной поверхности, что ухудшает механические свойства изделия, уменьшает пластичность, увеличивает возможность хрупкого разрушения,
· неустойчивость химического состава,
· наличие в составе некоторых электролитов ядовитых веществ (цианидные).
При выборе типа электролита для промышленного применения учитываются:
· производительность,
· технологическая простота использования,
· возможность получения равномерного покрытия,
· толщина и структура поверхностного слоя,
· покрытие деталей различной конфигурации,
· экологические параметры.
Разнообразие электролитических составов расширяют возможности нанесения цинкового покрытия гальваническим путем.
Гальваническое цинкование | Цинковый портал
Гальваническое цинкование — технология основана на принципе работы гальванической пары. При гальваническом цинковании в качестве анода используется стальная или цинковая пластина, катодом является обрабатываемая деталь. Деталь при помощи технологических приспособлений погружается в солевой раствор цинковых соединений (электролит). Через раствор пропускается электрический ток. Происходит поляризация активных частиц (анионов, катионов). При гальваническом цинковании формирование поверхностного слоя детали производится из положительно заряженных ионов цинка, которые осаждаются на отрицательно заряженном катоде.
В зависимости от используемой соли цинка электролиты бывают:
· щелочными,
· нейтральными (слабощелочные),
· слабокислыми,
· кислыми.
Принципиальная схема гальванического цинкования
Каждый электролитический раствор при гальваническом цинковании обладает характерными специфическими признаками, поэтому при выборе рабочего состава для цинкования приоритетом служат окончательные технологические параметры изделия: толщина цинкового слоя, качество сцепления покрытия с металлической основой, стойкость защитного слоя к агрессивному воздействию.
Основной характеристикой при гальванической обработке (цинковании) считается толщина защитного слоя. Толщину цинкового покрытия (от 3 мкм до 40 мкм) можно регулировать путем изменения величины различных технологических параметров электролитического процесса:
· силы тока,
· рабочей температуры электролита,
· концентрации активных составляющих рабочего раствора.
В конструкторской документации задается не только толщина цинкового покрытия, но и цвет финишной обработки (бесцветный, желтый, черный, хаки).
Преимущества гальванического цинкования
1. Высокая степень чистоты осаждаемого покрытия.
2. Большая химическая стойкость цинкового слоя.
3. Возможность регулирования толщины покрытия.
4. Высокие механические свойства защитного слоя.
5. Надежное сцепление осаждаемого цинка с покрываемым изделием.
6. Возможность цинкования деталей различной конфигурации.
7. Презентабельный внешний вид.
Сложности гальванического цинкования
При осаждении цинка на заданную поверхность потребляется значительное количество электроэнергии. Расход электроэнергии напрямую зависит от толщины наносимого слоя, от геометрических размеров обрабатываемых изделий и времени цинкования, технологических выходных параметров используемого оборудования (выпрямителей).
При гальваническом цинковании потребляется значительное количество воды. Это необходимо для увеличения степени чистоты обрабатываемой поверхности, улучшения процесса сцепления осаждаемого цинка со стальным основанием, придания изделию необходимого внешнего вида (согласно КД).
Дополнительная статья расходов при гальваническом цинковании связана с нейтрализацией вредных отходов, получаемых в процессе производства. Для решения этой проблемы строятся специальные очистные сооружения.
Гальваническое цинкование – распространенный и востребованный способ нанесения защитного покрытия на стальные изделия. Технология гальванического цинкования хорошо изучена и постоянно модифицируется.