Цементный клинкер — Википедия
Материал из Википедии — свободной энциклопедии
У этого термина существуют и другие значения, см. Клинкер.Кли́нкер (в цементной промышленности) — промежуточный продукт при производстве цемента.
Впервые получен французом Луи Вика в 1817 году.
При нагревании смеси, полученной из известняка (около 75 %) и глины (около 25 %) или других материалов сходного валового состава и достаточной активности до температуры 1450°С происходит частичное плавление и образуются гранулы клинкера. Для получения цемента, клинкер перемешивают с несколькими процентами гипса (около 5 %, что зависит от марки гипса и содержания SO3 в клинкере) и тонко перемалывают. Гипс управляет скоростью схватывания; его можно частично заменить другими формами сульфата кальция. Некоторые технические условия разрешают добавлять другие материалы при помоле. Типичный клинкер имеет примерный состав 67 % СаО, 22 % SiO2, 5 % Аl2О3, 3 % Fе2
Алит[править | править код]
Является наиболее важной составляющей всех обычных цементных клинкеров; содержание его составляет 50—70 %. Это трёхкальциевый силикат, 3СаO*SiО2 (сокращенно обозначают C3S), состав и структура которого модифицированы за счёт размещения в решётке инородных ионов, особенно Mg2+, Аl3+ и Fе3+. Алит относительно быстро реагирует с водой и в нормальных цементах из всех фаз играет наиболее важную роль в развитии прочности; для 28-суточной прочности вклад этой фазы особенно важен.
Белит[править | править код]
Содержание белита для нормальных цементных клинкеров составляет 15—30 %. Это двукальциевый силикат 2СаO*SiО2 (C
Алюминатная фаза[править | править код]
Содержание алюминатной фазы составляет 5—10 % для большинства нормальных цементных клинкеров. Это трехкальциевый алюминат 3СаO*Al2O3, существенно изменённый по составу, а иногда и по структуре, за счёт инородных ионов, особенно Si4+, Fe3+, Nа+ и К
Алюмоферритная фаза[править | править код]
Ферритная фаза (CaAlFe) составляет 5—15 % обычного цементного клинкера. Это — четырёхкальциевый алюмоферрит 4CaO*Al2O3*Fe2O3, состав которого значительно меняется при изменении отношения Al/Fe и размещении в структуре инородных ионов. Скорость, с которой ферритная фаза реагирует с водой, может несколько варьировать из-за различий в составе или других характеристиках, но, как правило, она высока в начальный период и является промежуточной между скоростями для алита и белита в более поздние сроки.
В клинкере обычно присутствуют в небольших количествах и несколько других фаз, таких как щелочные сульфаты и оксид кальция.
Как и из чего делают цемент?

Строительные материалы появились в тот момент, когда на заре нашей цивилизации первые люди начали строительство домов и укреплений. С течением времени человечество искало материалы, обладающие большой прочностью и доступностью в любом месте проживания. После длительных поисков и экспериментов было выявлено, что мелкодробленый известняк и гипс, при смешивании с водой и минералами, приобретает особые вяжущие свойства.
После затвердевания образует монолитное соединение имеющие характеристики твердого камня. С того момента цемент начали производить в больших количествах и использовать в строительстве больших и маленьких сооружений. Проходя очередной раз мимо постройки из камня и металла, мы часто задаёмся вопросом: «Так как же делают цемент?»
Интересный факт: в период постройки Египетских пирамид, фараоны использовали технологию похожую на производство бетона. Смесь измельчённого известняка и каменной крошки заливали водой и превращали в монолитные каменные блоки.
Из чего делают цемент?


Первый этап производства начинается в известняковом карьере, когда с помощью горнодобывающих машин из почвы изымают компоненты будущего цемента. Чтобы строительный материал имел требуемую прочность, для производства выбирают известняк, который лежит близко к поверхности. В его составе, в большом количестве, присутствует кремний, железо и окись алюминия. Если копать глубже, то порода будет чище, но с большим содержанием углекислого кальция. Добытый камень, по необходимости, сортируют и отправляют на производство, где меняют пропорции, чтобы получить цемент разных марок.
Обработка известняка


На заводе по производству цемента, породу выгружают в аппарат для первичного дробления камней. Большие валуны под воздействием давящей силы в несколько тонн, постепенно измельчаются до размеров теннисного мяча и поступают на конвейер. Мелкие и крупные камни направляются на вторичное дробление, где они уменьшаются до размеров мячика для гольфа и в мелкий порошок. Известняк, с разным процентом содержания углекислого кальция, обрабатывается отдельно.


Сортировка и шлифование
Мелкий известняк, с помощью сортировочного погрузчика, размещают в сухие склады, защищенные от влаги и перепадов температуры. Формируются кучи из сырьевой смеси, разного состава, готовые к этапу шлифования. По конвейеру дробленый камень поступает в шлифовальную машину – вальцовую мельницу, в которой образуется известняковая пыль.
Смешивание


Чтобы создать цемент разных марок, к подготовленной породе добавляют железо, двуокись алюминия и кремний. Состав и количество добавок определяется после химического исследования известняка. Роллер равномерно перемешивает составляющие цемента, до получения однородного порошка без камней. По завершению процесса готовую смесь направляют на термическую обработку.
Термическая обработка


Порошок отправляют в печь, в которой под воздействием температуры 800°С, в каменной муке начинается процесс химического соединения минеральных компонентов. После проведения первой термической обработки, его отправляют в кальцинатор, где с помощью химической реакции, за несколько секунд убирают 95 – 97% двуокиси углерода и отделяют известь. Далее смесь отправляют в вращающуюся цилиндрическую печь, в которой ее медленно перемешивают под воздействием температуры в 1500 – 1800°С.
При длительном воздействии высокой температуры, порошок превращается в стекловидные образования под названием «клинкеры». По выходу из печи клинкеры охлаждают до 60 – 80°С, отправляют в накопитель и далее на дробление.
Окончательное дробление


Клинкер помещается в вращающийся барабан, с металлическими шариками внутри. К содержимому добавляют гипс, количество которого зависит от марки цемента. Под воздействием вращательных движений и перемещения шариков, смесь измельчается до порошкообразной формы – это и есть готовый цемент.
Интересный факт: всплеск производства бетона начался в 19 веке после того, как в 1824 Джозеф Эспдин запатентовал цемент под названием «Портландцемент» имеющий прочность природного камня.
Производство цемента проходит на специализированных заводах с использованием силы трения и термической энергии. При этом, известняковые породы медленно превращаются в цемент. По завершению технологического процесса, готовый продукт можно использовать для строительства любых конструкций, больших и маленьких размеров.
Если Вы нашли ошибку, пожалуйста, выделите фрагмент текста и нажмите Ctrl+Enter.
Как производят цемент ⋆ Как это сделано
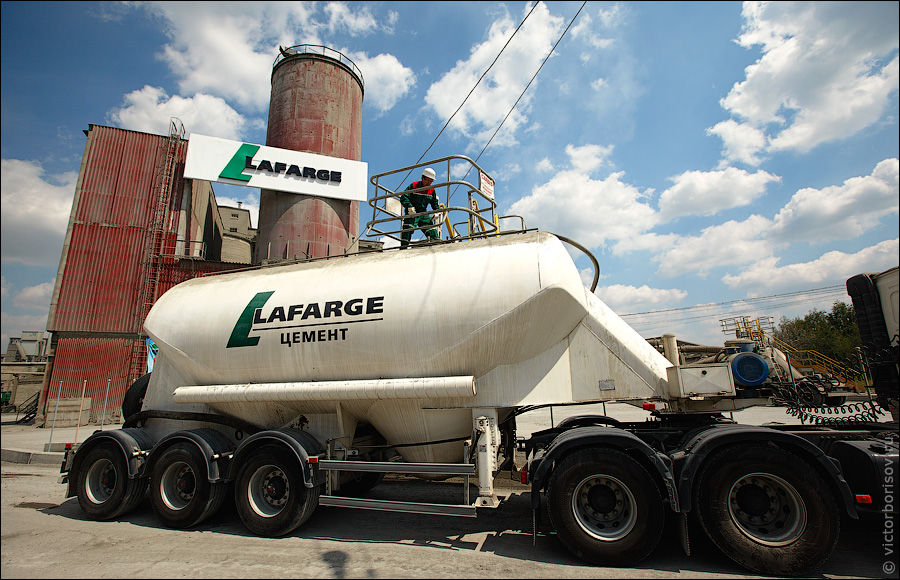
Цементная промышленность является одной из важнейших отраслей материального производства. Значение этой отрасли в народном хозяйстве определяется прежде всего ее неразрывной связью с ходом капитального строительства. Цемент — один из главнейших строительных материалов, предназначенных для изготовления бетонов, железобетонных изделий, а так же для скрепления отдельных деталей строительных конструкций, гидроизоляции и многих других целей.
Я провёл съемку на заводе Lafarge («Уралцемент») расположенном в поселке Первомайский, Челябинской области. Завод производит цемент по мокрому способу с 1957 года и по объемам производства находится в десятке крупнейших цементных заводов России. Для производства цемента используют глину и известняк. В качестве топлива выступает природный газ.
История портландцемента начинается 21 октября 1824 года, когда английский каменщик Джозеф Аспдин получил патент на вещество, которое назвал «портландцемент», поскольку его цвет напоминал серый цвет скал, находившихся вокруг города Портланд.
Портландцемент — гидравлическое вяжущее вещество, получаемое путем совместного тонкого измельчения портландцементного клинкера, гипса и специальных добавок. Свойства портландцемента зависят от состава клинкера и степени его измельчения. Важнейшее свойство портландцемента — способность твердеть при взаимодействии с водой. Оно характеризуется маркой портландцемента, определяемой по прочности на сжатие и изгиб стандартных образцов цементно-песчаного раствора после 28 суток твердения во влажных условиях.
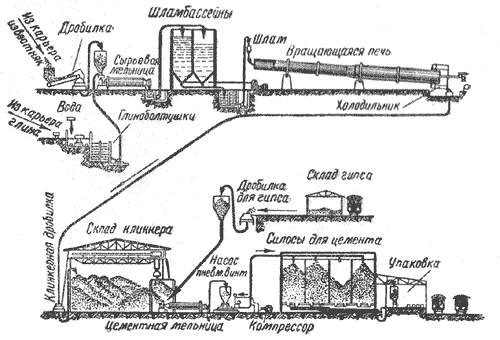
2. Производство цемента складывается из двух основных технологических процессов: получение клинкера (наиболее трудоемкий и энергозатратный этап) и его помол с соответствующими добавками.

3. Для изготовления цемента сначала добывают известняк и глину из карьера.

4.
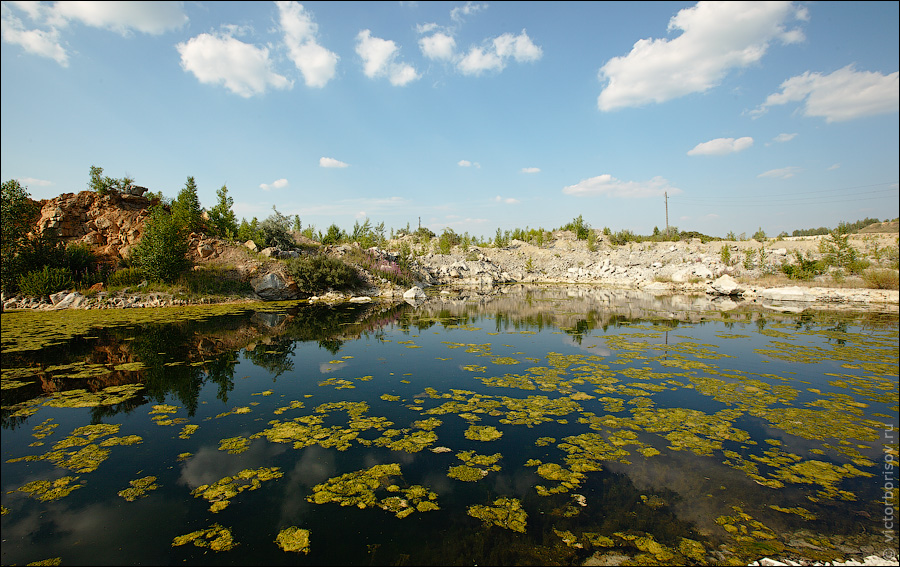
5.

6. Пройдя предварительную обработку, исходные материалы поступают в мельницу мокрого самоизмельчения «Гидрофол», где перерабатываются в шлам. Затем шлам домалывается в сырьевых мельницах и усредняется в шламбассейнах.

7. На заводе находится специальная лаборатория, в которой производят постоянный контроль качества и дозировку сырьевых материалов и добавок. И в том числе проводят тестирование конечного продукта на прочность.

8.
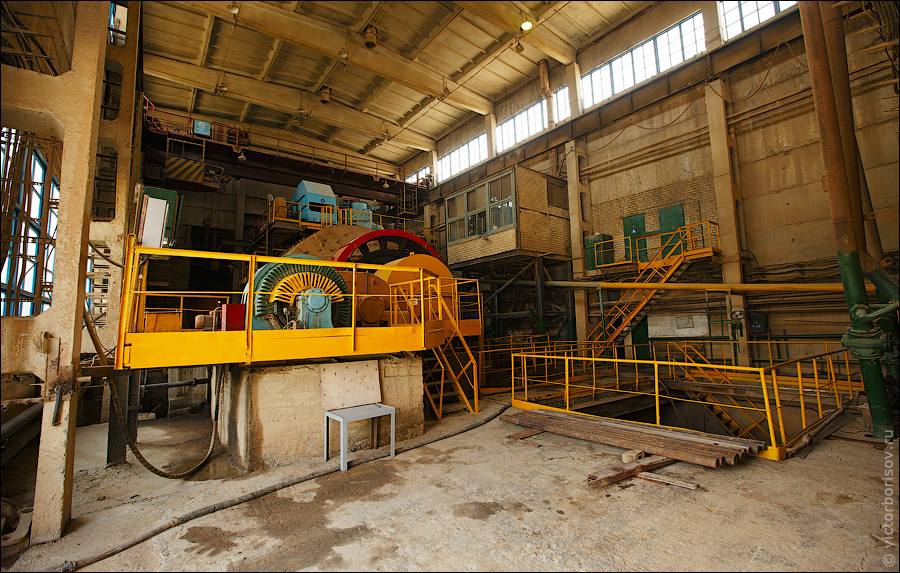
9.

10.

11. Затем тонкомолотый сырьевой шлам вводится во вращающуюся печь (длиной около 200 м и диаметром 4 м) и обжигается при температуре 1450 градусов Цельсия.

12. При обжиге частички сырья сплавляются между собой, образуя клинкер.

13. Печь для обжига представляет собой вращающийся металлический цилиндр, который наклонен к горизонтальной плоскости под углом 3-4 градуса, чтобы обеспечить возможность движения материала вдоль печи.

14. Полученный клинкер охлаждается в холодильниках, дробится и подается транспортерами в бункеры цементных мельниц для помола.
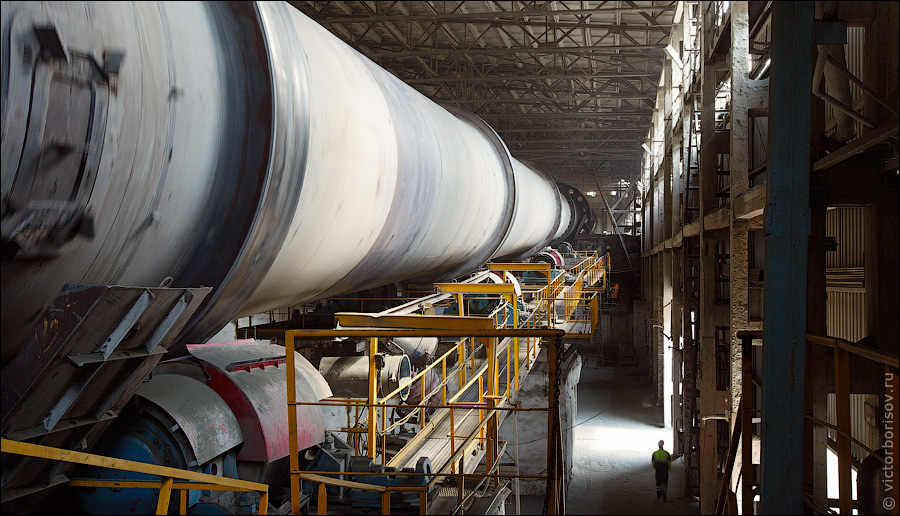
15. Электрофильтры на вращающихся печах позволяют сократить выбросы пыли в атмосферу в 10-30 раз.

16.

17.

18. Остывший клинкер подается в мельницу.
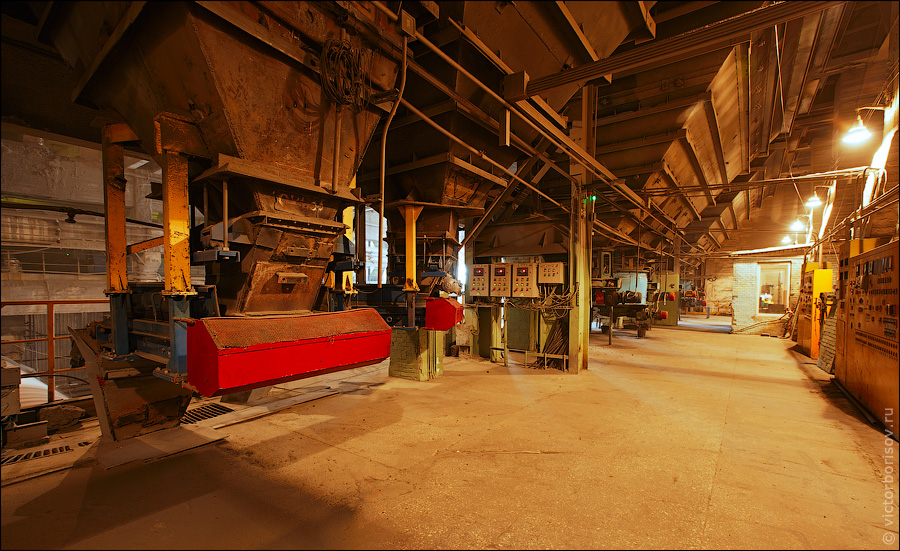
19.

20. Это самый шумный участок производства. Находится в цеху без наушников просто невозможно.

21. Цемент получают путем совместного тонкого измельчения портландцементного клинкера, минеральных добавок (10-15%) и гипса (3-7%), который служит для регулирования сроков схватывания. Размер зерен цемента лежит в пределах от 1 до 100 мкм.

22.

23.
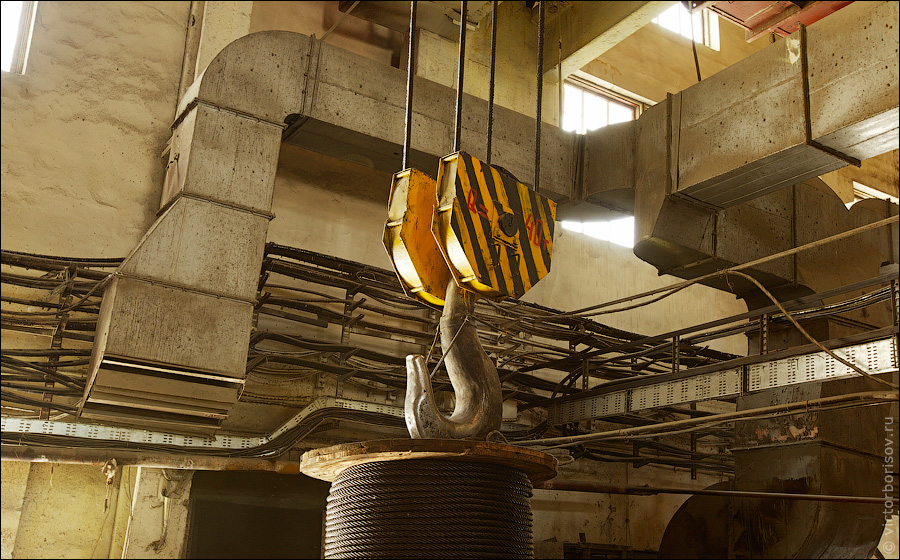
24. Процедура LOTOTO (LockOut / TagOut / TryOut). Комплекс действий для повышения безопасности на производстве.
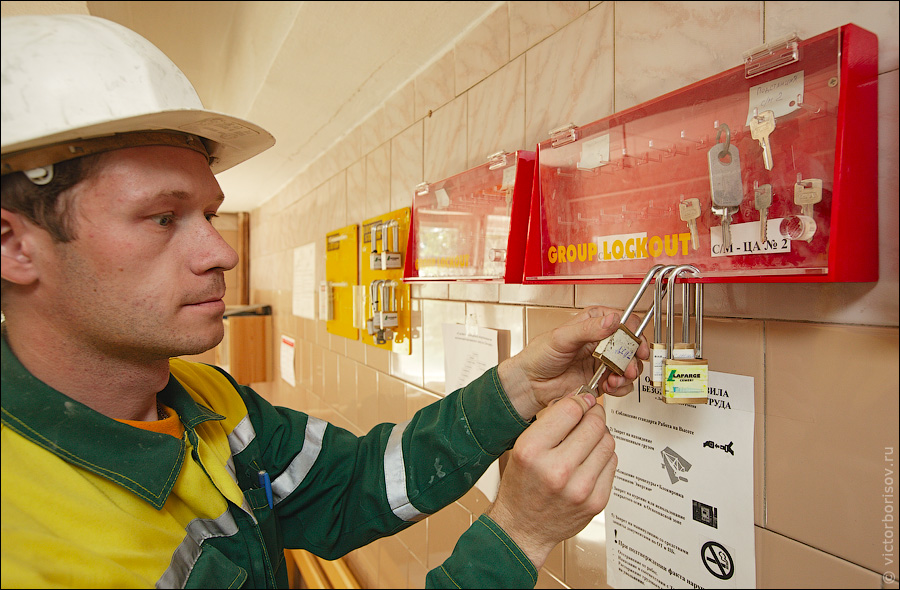
25. Различные минеральные добавки служат для придания бетонам, растворам и др. изделиям на основе цемента специальных свойств (скорость затвердевания, устойчивость в природных водах, морозостойкость).
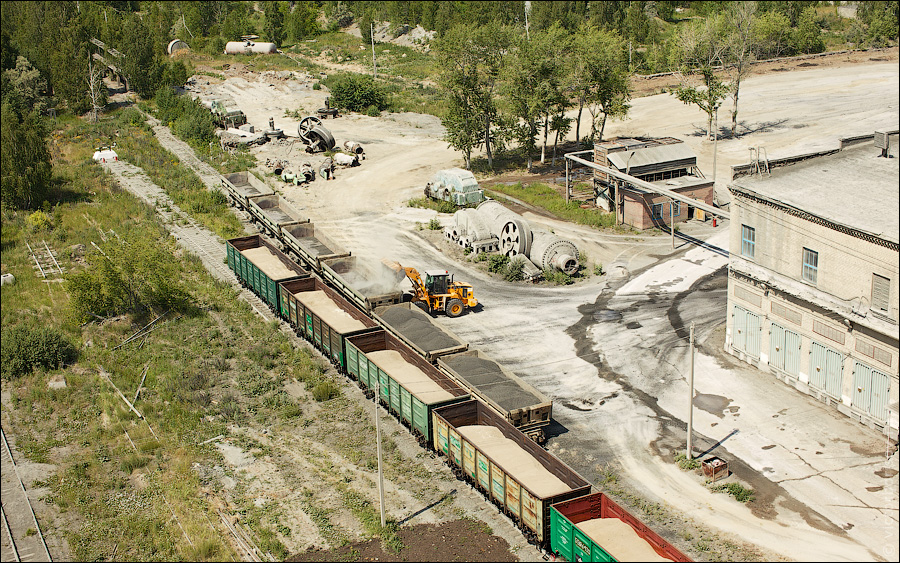
26.

27.
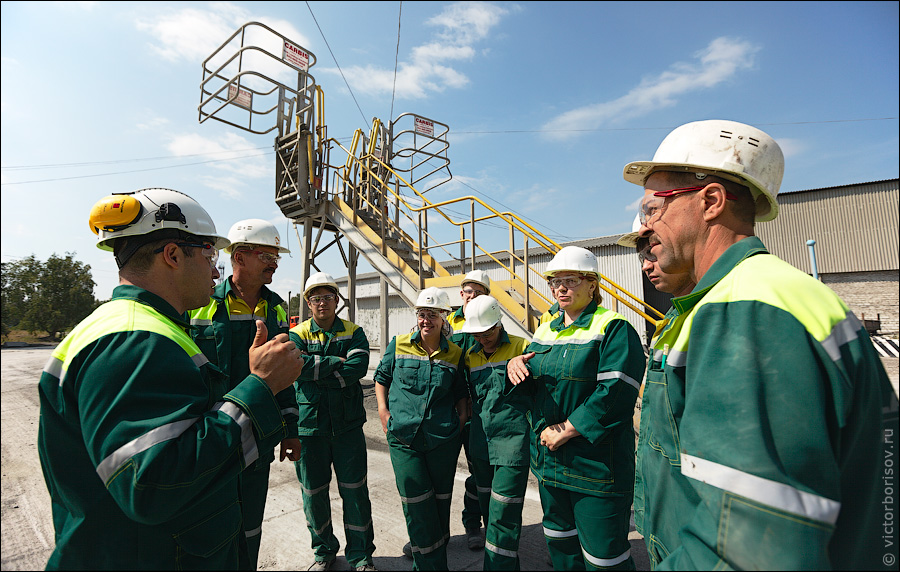
28. Полученный портландцемент транспортируется из мельниц в силосы для хранения.

29. Из силосов цемент отгружают железнодорожными вагонами и автомобильным транспортом в следующем виде: навалом, специальными контейнерами МКР весом до 1 тонны, бумажными мешками весом 50 кг.

30.
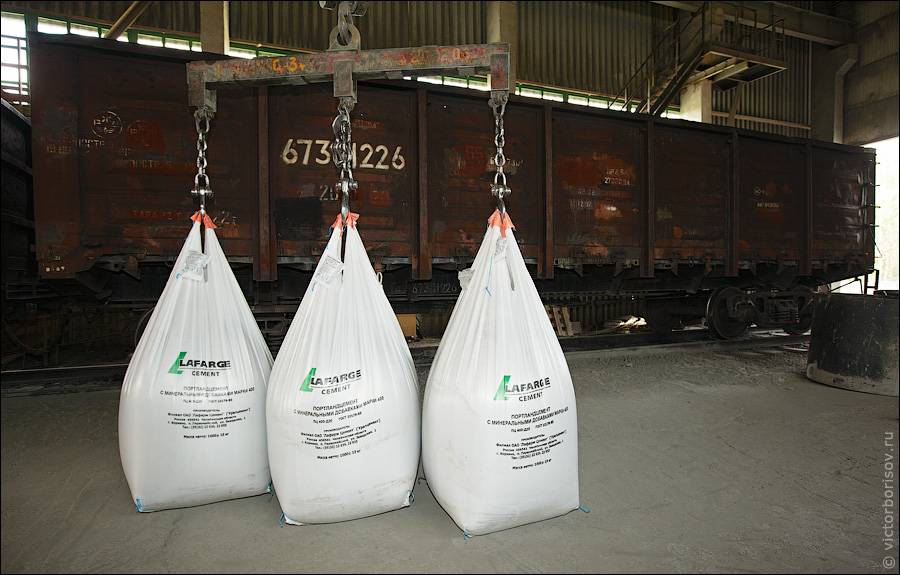
31.

32.

33.

Источник
Цемент (предприятие) — Википедия
Материал из Википедии — свободной энциклопедии
ООО «Цемент», ранее Одесский цементный завод — крупнейший производитель цемента в южном регионе Украины. С 2011 года входит в промышленную группу CRH, с штаб-квартирой в Дублине.
Производственная мощность по выпуску цемента — 550.000 тонн в год. Завод расположен на северной окраине г. Одессы. В 15 км от завода находится Одесский порт, в 30 км — Ильичевский порт, в 40 км — порт Южный.
Одесский цементный завод начал свою работу в 1965 году. Одесская область находится далеко от промышленно развитых районов страны, поэтому завод был построен для того, чтобы удовлетворить локальный спрос на цемент.
8 сентября 1965 года была запущена вращающаяся печь № 1, а в ноябре 1966 года — начала свою работу вращающаяся печь № 2. В 1966 году производство цемента составило 165,5 тыс. тонн.
Завод продолжал наращивать производственные мощности, и в 1971 года была достигнута проектная мощность 320 тыс. тонн.
Изначально, месторождение сырья — известняка и глины — находилось в 2 км от завода.
Елизаветовский карьер цементного сырья был разработан в 1973 году. Он находился в 40 км от завода, и туда было перемещено горное оборудование. В 1986 году была введена в действие частная ветка от станции Карьерная, что позволило перевозить сырье по железной дороге. После истощения залежей, была проведена рекультивация земель и подготовка сельхозугодий.
Строительство сушильного отделения для шлака в 1976 году с навальным хранением позволило запустить производство нового цемента — сульфатостойкого шлакопортландцемента — и в то же время увеличить объём промышленного производства до 360 тыс. тонн.
В 1986 году была построена железнодорожная ветка протяженностью 18 км от станции Карьерная до станции Карпово, что обеспечило доставку сырья на завод по железной дороге собственными думпкарными вертушками.[1]
В мае 1990 года на заводе состоялось 15 Всесоюзное совещание «Основы повышения эффективности производства цемента и качества контроля».[1]
В мае 2005 г. завод был приобретен португальской компанией (C+PA, Cimento e Produtos Associados, S.A.).
За время пребывания в Одессе португальцы вложили в украинский актив около 40 млн евро. За счет этого его мощность выросла с 360 тыс. до 550 тыс. т в год.[2]
В 2011 году 51% акций завода купила швейцарская компания Jura-Cement-Fabriken, входящая в ирландский строительный холдинг Cement Roadstone Holdings (CRH). Планируется до конца 2014 года приобрести оставшуюся долю акций и Одесский цементный завод будет полностью передан в собственность компании CRH.
Группа CRH обладает представительствами в 35 странах мира и является одним из ведущих мировых производителей стройматериалов.
Сейчас Одесский цементный завод не производит клинкер, который поставляет Каменец-Подольский цементный завод[3].
Продукцию ООО «Цемент» было использовано для значимых инфраструктурных объектов Украны, среди которых Южный и Ильичевский морские порты, Одесская обл., НСК «Олимпийский», г. Киев.
![]() | ![]() | ![]() |
- Цемент (неопр.). CRH Украина. Дата обращения 10 октября 2019.
кто это сделал и в каком году?
История цемента как строительного материала насчитывает много лет, в течение которых менялись его структура, состав и технические характеристики с целью улучшения качеств и определения самого удачного варианта. Сегодня цемент является одним из основных строительных материалов, ведь представить осуществление каких-либо работ без бетона очень сложно.
Цемент представляет собой неорганическое гидравлическое вяжущее искусственного происхождения, которое в процессе взаимодействия с водой и другими жидкостями создает пластичную массу, способную затвердевать и превращаться в каменный монолит с высокими прочностными характеристиками. Особенность цемента – способность набирать прочность в условиях влажности, что не могут делать другие минеральные вяжущие (воздушная известь, гипс и т.д.).
Основным показателем свойств цемента является его марка: буква М и цифры рядом обозначают уровень прочности на сжатие и другие сопутствующие характеристики (М200, М500). Производят цемент посредством тонкого помола гипса и клинкера (продукт равномерного обжига до состояния спекания однородного сырья из глины и известняка). В процессе измельчения в состав могут вводиться разные добавки для изменения свойств.
- Романцемент – больше белита, сейчас его не производят.
- Портландцемент – больше алита, самый распространенный.
- Магнезиальный (цемент Сореля) – на базе магнезита, затворяется только водным раствором солей.
- Глиноземистый – преобладает алюминатная фаза.
- Биоцемент – появился благодаря использованию в производстве биотехнологий.
- Кислотоупорный – на базе гидросиликата натрия: смесь кремнефтористого натрия и кварцевого песка затворяют водным раствором жидкого стекла.
Чаще всего используют портландцемент, который производят путем нагрева глины и известняка до +1450-1480 градусов. Смесь плавится, формируя гранулы клинкера, который потом смалывают с гипсом.
- Алит – самый важный компонент клинкера (его в составе 50-70%), быстро вступает в реакцию с водой, влияет на прочность, особенно важен для 28-суточной прочности.
- Белит – 15-30% в составе, в реакцию вступает медленно, на прочность влияет мало в течение 28 суток, но потом повышает показатель.
- Алюминат – 5-10%, реагирует с водой быстро, может стать причиной слишком быстрого схватывания (для препятствования этому часто добавляют гипс).
- Феррит – 5-15% в составе, скорость реакции с водой может быть разной, но обычно высокая вначале, замедляется позже.
Немного предыстории о материале
На вопрос о том, когда изобрели цемент, ответить трудно. Принято считать, что основные способы производства вяжущих нашли в 3-4 тысячелетии до н.э. Случилось это при обжиге горных пород и измельчении того, что получилось. Самые первые созданные искусственно вяжущие – это строительный гипс и известь.
Именно их использовали в строительстве бетонной галереи лабиринта (Египет, 3600 год до н.э.), Великой Китайской стены, Римского Пантеона, давних домов в Мексике.
Ввиду того, что глина и гипс могут затвердевать лишь на воздухе, их называют воздушными. Прочность материалы демонстрируют сравнительно невысокую. По мере изучения свойств материалов их водостойкость начали повышать добавлением мелкосмолотой обожженной глины, вулканических пород (это «пуццоланы» — название пошло от места залегания пород в городе Поццуолли, древний Рим).
С 1584 года в Москве начал действовать «Каменный приказ», направленный на производство кирпича, заготовку камня для строительных целей, а также производство извести. В течение многих лет гипс и известь оставались основными видами вяжущего. В 18 столетии в России начала интенсивно развиваться промышленность, были попытки систематизировать знания про вяжущие вещества, создавать новые виды.
Цемент был изобретен в 1822 году, когда русский строитель Егор Челиев смешал глину с известью и получил материал, обладающий вяжущими свойствами. Через несколько лет он издал книгу, где полностью описал процесс приготовления не только цементных материалов, но и бетон, а также рассмотрел достоинства их применения в кладке кирпичей, возведении зданий и набережных.
В 1824 году Джозеф Аспдин смог придумать современный портландцемент, который после смешивания с щебнем, песком и водой можно было применять в качестве бетона. Материал прекрасно выдерживал сжатие, но боялся растяжений. Тогда же начали изучать другие материалы и знали, что железные балки хорошо выдерживают растяжение, но боятся сжатия.
Практически одновременно несколько людей решили соединить свойства двух материалов для лучшего результата. На юге Франции в 1850 году Жан-Луи Ламбо построил несколько лодок из армированного железной сеткой бетона. В 1854 году британец Уильям Уилкинсон первым использовал бетонные панели, армированные железными балками, в возведении 2-этажного дома в Ньюкасле.
Тогда же примерно еще один строитель, Франсуа Куанье, во Франции решил поэкспериментировать – он первым связал стеновые панели со стальной арматурой перекрытий. Правда, в массы это не пошло. А вот ввел в практику железобетон человек, далекий от строительства. Создание железобетона стало одним из самых важных событий за всю историю строительства.
В 1846 году Джозеф Монье был назначен садовником оранжереи в известном саду Тюильри, что возле Лувра. Ему понадобились прочные садовые кадки для пересадки на зиму апельсиновых деревьев. Монье создал несколько кадок из смеси цемента, песка, молотого кирпича, золы (бетон), но конструкция постоянно покрывалась трещинами. И тогда Монье решил укрепить их железными стержнями.
Тогда принято было считать, что железо разрушает бетон при перепадах температур, но за 3 года все кадки остались целы. Тогда Монье сделал таким же образом емкости для воды, элементы украшения ландшафта, а в 1867 году представил железобетон миру в Париже, запатентовав его использование в искусственных водоемах. Дальше были оформлены и другие патенты – на бассейны и трубы, строительные панели, конструкции мостов, шпалы и балки.
Изобретенный Монье материал в 1875 году под его же руководством был использован в строительстве небольшого моста в замке Шазелье. А потом, в 1879 году, инженер-строитель из Германии по имени Густав Вайс выкупил все патенты у Монье и усовершенствовал конструкцию, передвинув арматуру в бок максимальной нагрузки на растяжение (ведь Монье инженером не был, такие нюансы не учитывал).
Таким образом, Густав Вайс завершил работы по созданию современного железобетона. Цемент с самого момента появления был очень высоко оценен. Сегодня без него не обходится практически никакое грандиозное строительство, материал используется во всех сферах, разных изделиях, конструкциях, зданиях.
Цемент – это не какой-то отдельный строительный материал, этот термин обозначает группу веществ с определенными физическими характеристиками: порошкообразность, вязкость, способность создавать пластичную массу с водой, а после высыхания становиться монолитом. Процесс всегда односторонний, обратно вернуть ничего нельзя.
Затвердевший цемент никогда не вернется в исходное состояние. Главные компоненты цемента – маргелистые, глинистые, известковые породы, разные добавки (бокситы, шлак и т.д.). После высокотехнологичной и высокотемпературной обработки сырье сплавляется (частично или полностью), создавая алюминаты/силикаты кальция, что делает его прочным. Видов цемента много.
Добавки в цементе обозначаются буквой Д и указывают процент (Д20 – 20% модифицирующих добавок). Если цемент чистый, стоит Д0. Благодаря добавкам удается повысить такие показатели, как стойкость к воде и коррозии, морозу и солнцу, упругость и пластичность, а также другие.
Характеристики и области применения наиболее востребованных марок
Рассматривая цемент и его характеристики, нужно понимать, какой функционал возложен на материал. Главная задача вяжущего – связывание всех компонентов конструкции/изделия в монолитное целое. Существует всего 2 типа вяжущих: воздушные (твердеющие на воздухе) и те, на свойства которых оказывает воздействие вода. Воздушные вяжущие – это гипс, глина, воздушная известь, гидравлические – цемент и гидравлическая известь.
Цемент – самый часто используемый вяжущий материал, который дает возможность создавать изделия/конструкции высокой прочности. В соответствии с типом исходного сырья и добавок есть два типа цемента – портландцемент и шлакопортландцемент. Портландцемент делится на быстротвердеющий материал и вяжущее с минеральными добавками.
Бетонные конструкции, в производстве которых используют цемент, могут обладать самыми разными техническими характеристиками. Добавки позволяют повышать свойства стойкости к морозу, влаге, агрессивным средам, погодным условиям, нагрузкам и т.д. Так, бетон используют для возведения домов и зданий, изделий и конструкций, даже ракетно-стартовых площадок и аэродромов.
Для обозначения максимальных показателей прочности используют понятие «марка» и цифры. Так, марка М400 указывает, что в лабораторных испытаниях затвердевший кубик из цемента с ребром 10 сантиметров при раздавливании под прессом выдерживает нагрузку 400 кг/см2. Самые распространенные марки – от М200 до М500. Есть цемент М600 и выше, но он актуален для возведения военных объектов, конструкций особого назначения.
Все цементы твердеют достаточно быстро – первоначальное схватывание начинается через 40-50 минут после затворения водой, конец твердения – через 12 часов. Полную прочность цемент набирает в течение 28 суток.
Самые востребованные марки цемента:- Портландцемент М400 – прочность 400 кгс/см2, применяют в производстве бетонных/железобетонных, монолитных конструкций, сборных ЖБИ, строительных растворов для штукатурки и кладки. Также цемент используют в бетоне для производства искусственной брусчатки, элементов мощения, садовых и дорожных бордюров.
- Портландцемент М500 – прочность на сжатие равна 500 кгс/см2, марка отличается быстрым схватыванием и твердением. Из цемента выполняют строительство гидротехнических сооружений, создание высокопрочных сборных ЖБИ, монолитных сооружений, проведение аварийных ремонтных работ (при условии первоначально высокой прочности) и т.д.
- Сульфатостойкий цемент – используют для создания конструкций, которые будут испытывать влияние сульфатных вод, при переменном горизонте, с постоянным замораживанием/оттаиванием, увлажнением/высыханием. Делают мосты, сваи, опоры для работы в минеральных водах.
- Тампонажный – для цементирования газовых, нефтяных, иных скважин.
- Напрягающий – актуален для ремонта/строительства подземных емкостных конструкций бассейнов, сооружений, гаражей под землей, тоннелей и т.д.
- Высокоглиноземистый цемент – дает бетонам быстрое твердение, максимальную прочность в минимальные сроки, высокую огнеупорность и стойкость к агрессивным средам. Часто такой цемент используют для восстановления прорванных труб и плотин, разрушенных мостов и дорог, в срочном создании фундаментов.
- Белый и цветной портландцемент – актуален для выполнения скульптурных, архитектурно-отделочных работ, покраски бетонных, кирпичных, шлакоблочных частей сооружений/зданий.
Разные виды цемента могут отличаться по физико-техническим свойствам. Основной критерий выбора марки цемента – сфера эксплуатации изделия, конструкции, здания, предполагаемые нагрузки, условия.
Дополнительные характеристики цемента, на которые нужно обращать внимание:- Активность – проверяется путем сжимания образца до разрушения, выражается в определенных показателях.
- Плотность – считают по объему свежего цемента. Имеет значение крупность помола, которая должна быть равна 1.3 т/м3, но многое зависит от условий транспортировки, хранения. Цемент может слеживаться, уплотняться, поэтому при весе 1.3 т допускается уменьшение веса, но не очень значительное.
- Срок годности – с момента производства до использования должно пройти не больше 6 месяцев (но производители гарантируют заявленные характеристики лишь в течение 2 месяцев). Цемент в мешках в условиях закрытого помещения и оптимальной влажности может храниться 3 месяца, в биг-бегах – до 6.
- Время застывания – добавки регулируют этот параметр, но многое зависит от сезона (в летнее время кладочный раствор застывает за 2-3 часа до первичной крепости, зимой – до 8 часов).
- Стойкость к коррозии – способность твердого монолита противостоять различным агрессивным воздействиям (щелочных/химических сред).
- Водопотребность – потребность сухой смеси в определенном объеме воды для получения подвижности в применении.
- Тонкость помола – главный показатель дисперсности, определяется числом сухого остатка на сите при контрольном просеивании. Параметр влияет на прочность застывшего монолита.
- Морозостойкость – стойкость к отрицательным температурам, способность выдерживать определенное число циклов замораживания/оттаивания. Для повышения показателя используют минеральные добавки.
История цемента показывает, что создание данного вещества стало одним из самых важных событий в ремонтно-строительной сфере. Не менее важным этапом стало и объединение бетона с металлом, открыв эру железобетонных зданий, конструкций, изделий. При выборе цемента необходимо ориентироваться на основные марки и их характеристики, обращая внимание на соответствие требованиям по проекту, условиям эксплуатации, нагрузкам и т.д.
Сырье для производства цемента, из чего делают цемент
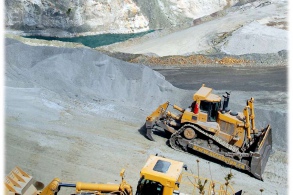
Сырьевыми материалами в производстве цемента служат в основном глинистые и карбонатные породы, а также иное природное сырье и некоторые типы промышленных отходов, шлаков и т.п.
Карбонатные породы — это известняк, известняк-ракушечник, мел, мергелистый известняк, мергель, метаморфические либо осадочные горные породы доломитового, карбонатно-глинистого и известнякового состава. Качество и ценность таких пород в качестве сырья для создания цемента определяется их структурой и физическими свойствами. Породы с кристаллической структурой хуже, по сравнению с породами аморфной структуры, взаимодействуют с другими элементами смеси при обжиге.
- Мел – легко растирающаяся мягкая осадочная горная порода, вид мажущего известняка. Он легко измельчается и является популярным сырьем для создания цемента.
- Мергель — осадочная порода, переходная от известняковых к глинистым. Может иметь твердую или рыхлую структуру, различную плотность и влажность в зависимости от процентной доли глинистых примесей. Строительные растворы на основе мергеля активно применяются при устройстве печей, каминов и т.п.
- Из известняков для производства цемента предпочтительны пористые и мергелистые виды с небольшим порогом прочности на сжатие и без содержания кремниевых включений.
- Из глинистых пород в производстве цемента применяют: суглинок, глину, лесс, глинистый сланец, а также лессовидные суглинки.
Глины, горные осадочные породы, состоят из разного рода минералов, при увлажнении приобретают пластичность и разбухают. В сухом способе производства цемента связующая способность и пластичность глины дает возможность гранулирования муки и брикетирования. Суглинком называется глина, в которой содержится высокое количество пылеватых и песчаных частиц.
Глинистые сланцы представляют собой плотные и твердые горные породы, способные легко расслаиваться на пластинки небольшой толщины. Относительно глины глинистые сланцы имеют более постоянный состав и меньшую влажность.
Лессом называется тонкозернистая горная порода, рыхлая и пористая, состоящая из тончайших частиц глинистых материалов, полевого шпата, кварца и иных силикатов. Лесс не отличается высокой пластичностью. Лессовидный суглинок – материал, по своим свойствам являющийся переходным между суглинком и лессом.
Кроме основного сырья в процессе производства активно используются различные виды корректирующих добавок в цемент, позволяющих изменить некоторые свойства конечного продукта. Это могут быть глиноземистые, кремнеземистые, глиносодержащие добавки, а также плавиковый шпат в качестве минерализаторов (кремнефтористый натрий, гипс, апатит, фосфогипс, флюорит)
Хотелось бы отметить, что сырьевой состав, как при сухом, так и при мокром способе производства цемента, может меняться в зависимости от местоположения цементного завода, от доступности того или иного вида сырья, от возможностей оборудования, спроса на те или иные виды продукции в этом регионе и многого-многого другого
виды, марки, технические характеристики, технология производства
Дата: 23 января 2019
Просмотров: 4415
Коментариев: 0

Невозможно представить производство строительных работ без вяжущих материалов, соединяющих в монолитную конструкцию блоки, плиты, кирпич. Самым распространенным и востребованным в данной категории материалов является портландцемент.
Смешиваясь с водой или растворами различных солей, цемент образует эластичную массу, которая в процессе высыхания преобразуется в цементный камень. Без применения растворов на основе портландцемента невозможно изготовление железобетонных конструкций, монолитных сооружений, высококачественных смесей для каменных кладок и отделочных мероприятий.
Портландцемент получают путем соединения мелкоизмельченного клинкера с небольшим объемом гипса, который ускоряет процесс схватывания смеси. При производстве, в зависимости от предъявляемых к смеси требований, добавляются различные добавки, повышающие устойчивость материала к воздействиям негативных факторов.

Один из наиболее распространенных видов вяжущего вещества для бетонных смесей – портландцемент
Виды
Для придания готовому изделию определенных свойств, портландцемент обогащают минеральными добавками – белитом, алитом, целитом, браунмиллеритом. В зависимости от используемых минеральных составляющих портландцемент делится на следующие виды:
- Характеризующийся средней скоростью схватывания.
- Быстротвердеющий состав.
- Пластифицированный.
- Устойчивый к влаге, гидрофобный.
- С повышенной тепловой отдачей.
- Особо стойкий по отношению к химическим реагентам.
- Декоративный (цветной или белый), применяемый при отделочных работах.
Марки цемента
Опираясь на требования нормативной документации, предъявляемые к цементному образцу, подвергающемуся испытаниям на сжатие и изгиб, можно выделить основные марки портландцемента:
- М700 – особо прочный состав. Область применения ограничена изготовлением бетона с увеличенными прочностными характеристиками для возведения напряженных конструкций. Цена такого цемента высока, что делает его нерентабельным при ведении обычных строительных мероприятий;

Любой вид портландцемента марки 400 применяют для создания обычных и стандартных конструкций, не подвергающихся увеличенным нагрузкам
- М600 – состав увеличенной прочности. Область применения – производство ответственных железобетонных изделий и конструкций;
- М500 – цемент, обладающий достаточно хорошими прочностными показателями, что позволяет использовать его при реконструкции зданий и сооружений после аварий, возведении военно-технических объектов, укладке дорожного покрытия;
- М400 – самая доступная и широко используемая марка. Объясняется это тем, что заложенные показатели морозоустойчивости, влагостойкости позволяют применять его при возведении объектов любого назначения.
Предприятия-изготовители выпускают портландцемент марок М200 и М300, но в довольно ограниченном количестве. Такое ограничение закономерно, поскольку спрос на эти марки невелик.
Цифровой индекс, указанный в маркировке портландцемента, обозначает величину давления, которую способен воспринять эталонный образец материала. Например, портландцемент, маркируемый М500, воспринимает давление, превышающее 500 кг/см².
Используемое основное сырье
При изготовлении портландцемента используют известковые и глинистые породы в определенной пропорции, обеспечивающей требуемый химический состав для обжига.

Все виды портландцемента (ПЦ) изготавливают из разного сырья, общим компонентом для всех является только цементный клинкер
Из известковых пород наиболее часто применяют:
- Известняк, не содержащий включений кремния. Плотная порода с мелкокристаллической структурой.
- Мергель – переходная от известняковых к глинистым порода. Включает в свой состав мелкие частицы солей кальция с примесью полевого шпата, доломита и пр.
- Мел – податливая, легко измельчаемая осадочная порода.
- Ракушечный известняк.
К глинистой составляющей относятся:
- Глинистые сланцы. Благодаря своей слоистой структуре легко раскалываются, что значительно облегчает обработку.
- Лесс. Рыхлая мелкозернистая порода, содержащая большое количество карбоната кальция.
- Глина. Представляет собой смесь основного глинистого вещества – гидроалюмосиликата с соединениями железа, магния и других элементов.
- Суглинки. Отличаются от глины увеличенным содержанием песка.
Однозначно квартира! Комфорт, уют и тепло, вокруг люди и инфраструктура 831 ( 7.62 % )
Только частный дом! Вокруг тишина, покой, много места и мало людей! 4972 ( 45.57 % )
Зачем выбирать что-то одно? В городе квартира, а за городом — частный дом. 4622 ( 42.36 % )
Я — свободный Гражданин Планеты Земля! Мне не нужна рукотворная клетка! 485 ( 4.45 % )
Назад
Для экономии природных сырьевых ресурсов и удешевления производства цемента все чаще используются отходы металлургической промышленности (шлам, зола).
Минеральные составляющие клинкера
Для получения основного компонента портландцемента – клинкера, проводится обжиг сырьевой смеси (известняк + глина). В результате этой операции образуются минеральные соединения, процентное содержание которых не должно превышать допустимые значения.

В большинстве случаев клинкер получают из искусственных смесей, потому что в природе сырье, содержащее примерно 75% карбоната кальция и 25% глины, встречается довольно редко
К основным минералам, определяющим свойства получаемого клинкера относятся:
- быстро твердеющий алит. Этот компонент отвечает за скорость твердения состава и нарастание эксплуатационной прочности. Его количество регламентировано в пределах 45-60 процентов;
- медленно твердеющий белит. Его присутствие позволяет цементным составам достигать высоких прочностных показателей при длительном твердении. Чтобы белит не потерял вяжущих свойств, клинкер максимально быстро охлаждают. Количество минерала выдерживается в рамках 20-35 процентов, что позволяет достичь оптимальных сроков твердения;
- быстро гидратирующий трехкальциевый алюминат, ускоряет процесс гидратации, но параллельно с этим снижает прочностные характеристики и увеличивает возможность появления коррозии. Поэтому содержание ограничено 4-10 процентами;
- образующийся на определенной фазе обжига алюмоферрит, значительно не влияет на процессы твердения и тепловыделения. Его содержание в клинкере находится в пределе 10-18 процентов.
Поскольку портланд цемент получают из разного по химическому и минералогическому составу сырья, то на выходе получают цемент, отличающийся свойствами. Используя испытанные технологии производства, придерживаясь разработанных рекомендаций по процентному содержанию минеральных включений, предприятия-изготовители получат на выходе качественный продукт, отвечающий требуемым параметрам.
Технология производства
Споры по поводу, какой метод производства цементного состава лучше, не утихают долгие годы. Существует мнение, что, используя неоднородное по составу сырье повышенной влажности, предпочтительно воспользоваться мокрым способом. Параллельно с этим отстаивается позиция о применении сухого метода, как более экономически целесообразного, если предварительно подготовить должным образом шихту.

Клинкерную смесь обжигают при высоких температурах (до 1500°С), получая на выходе гранулы, которые потом измельчаются
Попытаемся разобраться в основных различиях существующих способов изготовления клинкера, из которого получают портландцемент. Известны три варианта получения смеси для обжига:
- Мокрый. Изначально проводят измельчение компонентов до нужной величины (известняк – размер частиц 8-10 мм, глина – куски до 10 см). Глину отмачивают до приобретения 70% влажности и отправляют в мельницы с известняком, где происходит смешивание.
- Сухой. Технология позволяет при уменьшенных затратах изготавливать портландцемент по сокращенному методу. Это обусловлено совмещением технологических стадий, обеспечивающих возможность одновременного выполнения сушки ингредиентов и их помола в специальных мельницах, в которые поступают горячие газы. Полученный шихтовый материал характеризуется порошкообразным составом.
- Полусухой (комбинированный). В данном методе совмещаются элементы сухой и мокрой технологии изготовления, которые используют производители цементных смесей. Допускается уменьшать влажность шихтового материала, произведенного мокрым методом, и получать шихтовой состав, влажность которого не превышает 18%. Согласно второму способу, готовится сухая смесь, которая насыщается водой до 14-процентной влажности, подвергается гранулированию и обжигается.
Свойства состава
Портландцемент обладает комплексом положительных характеристик, обеспечивающих его широкое применение в жилищном строительстве, при возведении промышленных конструкций. Главными характеристиками являются:
- удельный вес, зависящий от степени уплотнения состава. Для насыпных смесей составляет 1100 кг/м3, для уплотненных достигает величины 1600 кг/м3;
- гранулометрический состав, характеризующий тонкость цементной фракции и качество помола. Параметры влияют на эксплуатационные характеристики, интенсивность твердения раствора. Усредненный размер частиц цемента составляет порядка 40 микрон, что обеспечивает необходимую прочность и время твердения;
- потребление воды, влияющее на способность массива впитывать определенный объем жидкости. Недостаток влаги снижает прочность, а излишек – вызывает расслоение цементной массы. Согласно проверенной рецептуре, для замеса вводится 25-28 процентов воды от общего объема смеси;
- продолжительность схватывания, регламентированная стандартом, составляющая до 45 минут после смешивания с водой. Продолжительность окончательного твердения зависит от температурного режима и замедляется в зимний период;
- высокие прочностные характеристики, позволяющие воспринимать сжимающие нагрузки, что отражается в обозначении портландцемента.
Заключение
Представленная в статье информация о распространенном в строительной отрасли портландцементе знакомит с особенностями производства, свойствами, маркировкой и технологическими особенностями изготовления. Застройщики подтверждают, что это прочный материал, обеспечивающий высокий ресурс эксплуатации конструкций и сооружений.
Повышенные рабочие характеристики обеспечивают широкую сферу применения популярного материала.

На сайте: Автор и редактор статей на сайте pobetony.ru
Образование и опыт работы: Высшее техническое образование. Опыт работы на различных производствах и стройках – 12 лет, из них 8 лет – за рубежом.
Другие умения и навыки: Имеет 4-ю группу допуска по электробезопасности. Выполнение расчетов с использованием больших массивов данных.
Текущая занятость: Последние 4 года выступает в роли независимого консультанта в ряде строительных компаний.