Глиноземистый цемент, ГОСТ, применение и отличия
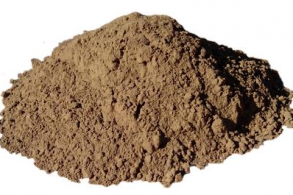
Глиноземистый цемент — это вяжущее вещество строительного назначения, полученное при измельчении клинкера с большим содержанием глинозема и окиси кальция. Клинкер получается спеканием раздробленных пород, таких как бокситы, известняки или известь. Главное отличие глиноземистого цемента от портландцемента заключается в том, что большая часть ГЦ состоит из низкоосновных алюминатов кальция. Тогда как ПЦ производится из клинкера, в составе которого преимущественно силикаты кальция.
Классификация
По составу глиноземистый цемент подразделяется на высокоизвестковый и малоизвестковый. В первом более 40% объёма занимает CaO, также он имеет повышенное содержание C5A3. Для малоизвестковых свойственно количество CaO менее 40% и наличие другого алюмината кальция CA2. Высокоизвестковые ГЦ имеют большую начальную прочность и характеризуются незначительным повышением этого показателя со временем.
Малоизвестковые, наоборот, вначале твердения менее прочные, но имеют значительный прирост твёрдости и в конце периода гидратации показывают более высокие значения прочности. Вы можете найти более подробную классификацию глиноземистых цементов в ГОСТ 969-91.
Характеристики
Момент начала схватывания глиноземистого цемента не может быть позднее 12 часов после его затворения водой. Минимальный интервал начала твердения составляет 30 минут. Для получения раствора с быстрыми сроками твердения, в цемент добавляют специальные компоненты. Например, гидрат окиси кальция или натрия, сульфаты железа, кальция или натрия и другие химические вещества. Увеличить период начала схватывания может азотистый или хлористый натрий, сахар, борная кислота, глицерин, хлористый барий, бура и другие соединения.
ГЦ характеризуется меньшей усадкой, его пористость в 1,5 раза ниже, чем у портландцемента. Соответственно глиноземистый цемент обладает более высокой водонепроницаемостью. Химический состав и структура ГЦ дают ему также преимущество в коррозиеустойчивости и стойкости к сульфатам кальция и магния, лучшую сопротивляемость воздействию солёной и пресной воды.
Применение
Глиноземистый цемент обходится в 3-4 раза дороже, поэтому его применяют только когда есть острая необходимость использовать материал с соответствующими свойствами. ГЦ показывает отличную огнестойкость, способен быстрее набирать прочность на ранних сроках твердения, имеет лучшее сцепление с арматурой, чем ПЦ.
Таким образом, оптимальные сферы применения материала будут следующими: производство огнеупорных растворов, изготовление конструкций или изделий при низких температурах, создание бетонных сооружений, которые будут эксплуатироваться в воде с повышенным содержанием минералов. И самое важное — это изготовление бетонных конструкций, требующих максимально быстрого твердения раствора.
Глиноземистый цемент и его разновидности — ТехЛиб СПБ УВТ
Глиноземистый цемент — быстротвердеющее гидравлическое вяжущее, состоящее преимущественно из моноалюмината кальция (СаО — Аl
Получение. Сырьем для глиноземистого цемента служат бокситы и известняки. Бокситы — горная порода, состоящая из гидратов глинозема (А12О3•nН2О) и примесей (в основном Fе2О3, SiO2, СаО и др.). Бокситы широко используются в различных отраслях промышленности: для получения алюминия, абразивов, огнеупоров, адсорбентов и т. п., а месторождений с высоким содержанием А1
Производство глиноземистого цемента более энергоемко, чем производство портландцемента. Клинкер глиноземистого цемента получают либо обжигом до плавления брикетов в электрических или доменных печах при температуре 1400…1500 °С, либо обжигом шихты до спекания во вращающихся печах при температуре 1200…1300 °С. Затем следует тонкий размол продукта, который сильно затруднен из-за его высокой твердости.
Состав. Химический состав глиноземистого цемента, получаемого разными методами, следующий: СаО — 35…45 %; Аl2О3
Твердение. Процесс твердения глиноземистого цемента и прочность образующегося цементного камня существенно зависят от температуры твердения. При нормальной температуре(до +25 °С) основной минерал цемента СА взаимодействует с водой с образованием кристаллического гидроалюмината кальция и гидроксида алюминия в виде гелевидной массы
2(СаО • Аl2О3) + 11H2О= 2СаО • Аl2О3 • 8Н2О + 2Аl(ОН)3+Q
Суммарное тепловыделение у глиноземистого цемента немного ниже, чем у портландцемента (около 300…400 кДж/кг), но протекает оно в очень короткие сроки (в первые сутки выделяется 70… 80 % от общего количества теплоты). Поэтому возможен перегрев бетонов на глиноземистом цементе в случае больших объемов бетонирования.
Если же температура твердеющего глиноземистого цемента превысит 25…30 °С, то процесс твердения изменяется, и вместо С
Свойства. Сроки схватывания глиноземистого цемента почти такие же, как у портландцемента: начало — не ранее 30 мин, конец — не позднее 12ч (реально 4…5 ч). После окончания схватывания прочность нарастает очень быстро (лавинообразно).
Глиноземистый цемент выпускают марок 400, 500 и 600, определенных в трехсуточном возрасте, но уже через одни сутки образцы набирают прочность при сжатии соответственно не менее 23, 28 и 33 МПа.
Усадка глиноземистого цемента при твердении на воздухе ниже, чем у портландцемента в 3…5 раз; пористость цементного камня ниже примерно в 1,5 раза. Это связано с тем, что при одинаковой с портландцементом водопотребности глиноземистый цемент при твердении химически связывает 30… 45 % воды от массы цемента (портландцемент — около 20 %).
Среда в процессе твердения и в затвердевшем цементном камне у глиноземистого цемента слабощелочная. Свободного Са(ОН)
Применение. Глиноземистый цемент целесообразно использовать при аварийных и срочных работах, при зимнем бетонировании и в тех случаях, когда от бетона требуется высокая водостойкость и водонепроницаемость.
Специальная область применения глиноземистых цементов -жаростойкие бетоны. Объясняется это тем, что, во-первых, в продуктах твердения этого цемента отсутствует Са(ОН)2 (при нагреве переходит в СаО, который при контакте с водой гасится с увеличением объема) и, во-вторых, при высокой температуре (700…800 °С) между продуктами твердения цемента и заполнителями бетона начинаются реакции в твердой фазе, по мере протекания которых прочность бетона не падает, а повышается, так как бетон превращается в керамический материал.
Кроме того, глиноземистый цемент является компонентом многих расширяющихся цементов, которые даже при твердении на воздухе имеют небольшое увеличение в объеме. Безусадочные цементы — это расширяющиеся цементы, у которых расширение только компенсирует усадку. Поэтому такие цементы как бы сами уплотняют себя, делая бетон водонепроницаемым. Если расширяющиеся цементы используются в железобетонных конструкциях, то эффект расширения вяжущего может вызывать натяжение арматуры и сжатие самого бетона, что дополнительно защитит его от образования трещин. Такие цементы называют
Эффект расширения вяжущего может быть достигнут различными методами, например путем гашения свободного СаО, добавляемого в твердеющее вяжущее, либо с помощью образования эттрингита — гидросульфоалюмината кальция ЗСаО•Аl2О3•ЗСаSО4•(31…32)Н2О. Последнее возможно при взаимодействии алюминатов и сульфатов кальция в водной среде.
В твердеющем материале протекают два процесса — расширение, обусловленное процессом кристаллизации эттрингита (или гашения СаО) с увеличением объема новообразований и ростом внутренних растягивающих напряжений, и препятствующий расширению процесс — рост прочности самого цементного камня. Если рост расширяющихся новообразований будет протекать при недостаточной прочности цементного камня, то податливая гелеобразная масса будет сжиматься и заметного расширения не произойдет. И наоборот, если рост расширяющихся новообразований будет продолжаться, когда цементный камень набрал достаточно высокую прочность, то напряжения, обусловленные ростом кристаллов в ограниченном объеме, могут вызвать падение прочности и даже разрушение цементного камня.
В свою очередь деформации расширения могут быть свободными и связанными, т. е. когда расширение цементного камня ограничено арматурой или кондуктором (формой). Деформации бетона при свободном расширении выше, чем при связанном, что обусловлено низкой прочностью цементного камня в раннем возрасте и его неспособностью напрягать кондуктор, а в более позднем возрасте — появлением микро- и макротрещин, которые увеличивают свободное расширение, но не вызывают дополнительного самонапряжения.
Связанные деформации вызывают самонапряжение, противодействуют развитию усадочных деформаций и способствуют самоуплотнению цементного камня, усилению контакта камня с заполнителем и кристаллизационных контактов. При изготовлении преднапряженных железобетонных конструкций в этом случае меньше потери преднапряжения и выше трещиностойкость получаемых изделий.
Главной задачей при разработке составов расширяющихся и безусадочных вяжущих является правильный выбор не только вида и количества расширяющихся компонентов, но и момента их образования относительно процесса формирования структуры цементного камня. Для различных видов расширяющихся цементов период наиболее интенсивного и безопасного расширения цементного камня составляет от 12 ч до 3…7 сут. в зависимости от свойств основного структурообразующего вяжущего.
Для обеспечения образования эттрингита в смесях с безусадочными и расширяющимися цементами должна присутствовать вода в продолжение всего периода твердения. Кроме того, эти Цементы нельзя применять при работе конструкций при температурах выше 80 °С, так как постепенно разрушается важный кристаллический компонент цементного камня — эттрингит: он отдает кристаллизационную воду, что сопровождается падением прочности.
Расширяющийся водонепроницаемый цемент получают совместным помолом глиноземистого цемента (70 %), гипса (20 %) и высокоосновного гидроалюмината кальция С4АН13 (10 %). Он является быстросхватывающимся и быстротвердеющим гидравлическим вяжущим веществом (Лсж через 6 ч — не менее 7,5 МПа, через 3 сух. — не ниже 30 МПа).
Линейное расширение твердеющего цемента на воздухе составляет в возрасте 1 сут. не менее 0,05 %, в возрасте 28 сут. — не менее 0,02 %. Цемент используют при восстановлении железобетонных конструкций, для гидроизоляции подземных сооружений, зачеканки трещин и стыков.
Гипсоглиноземистый расширяющийся цемент получают совместным помолом высокоглиноземистых шлаков (70 %) и двуводного гипса (30 %). Гипсоглиноземистый расширяющийся цемент имеет начало схватывания не ранее 20 мин и конец схватывания не позднее 4 ч от начала затворения. При необходимости могут использоваться замедлители сроков схватывания -ЛСТ, бура, уксусная кислота и др. Линейное расширение твердеющего цемента в состоянии теста нормальной густоты при твердении на воздухе составляет в возрасте 28 сут. не менее 0,1 %. Предел прочности при сжатии через 1 сут. твердения составляет 35 МПа для марки 400 и 45 МПа — для марки 500. Марки цемента соответствуют трехдневному возрасту. Гипсоглиноземистый расширяющийся цемент применяют для получения безусадочных и расширяющихся водонепроницаемых бетонов, гидроизоляционных штукатурных растворов, при бурении скважин и т. п. Он обладает морозо- и атмосферостойкостью в растворах и бетонах, изготовляемых на его основе.
Напрягающийся цемент (НЦ) получают совместным помолом клинкера портландцемента (65…75 %), двуводного гипса (6… 10 %) и высокоглиноземистого компонента (13…20 %). Сроки схватывания: начало — не ранее 30 мин, конец — не позднее 4 ч. Прочность через 1 сут. — не менее 15 МПа, через 28 сут. — не менее 50 МПа.
Напрягающий цемент обладает способностью к значительному расширению (до 4 %) при твердении в состоянии цементного теста нормальной густоты. В железобетоне НЦ создает после отвердевания в арматуре предварительное напряжение. Этим свойством как функцией химической энергии цемента пользуются при изготовлении предварительно напряженных железобетонных конструкций. С учетом величины достигаемой энергии самонапряжения, т. е. удельного давления в МПа, развиваемого при твердении НЦ в условиях ограничения свободного расширения, выделяют его разновидности НЦ-2, НЦ-4 и НЦ-6. Напрягающий цемент отличается также повышенными показателями водо- и газонепроницаемости, морозостойкости, прочности при растяжении и изгибе. Марки цемента (400 и 500) определяются испытанием образцов — балочек из цементно-песчаного раствора состава 1 : 1 в возрасте 28 сут.
Напрягающий цемент применяют для изготовления конструкций из самонапряженного железобетона, а также для гидроизоляции шахт, подвалов, зачеканки швов и т. д.
Перспективная область применения бетонов и растворов на расширяющихся и безусадочных вяжущих — бесшовные тонкослойные стяжки или лицевые покрытия полов большой площади. С помощью полимерных модификаторов таким смесям придают свойство самовыравнивания, а эффект безусадочности гарантирует трещиностойкость покрытия. Быстрое твердение и защитные полимерные добавки обеспечивают необходимое количество воды для протекания полной гидратации без какого-либо специального ухода.
Читать по теме:
К разделу
Строительные материалы
16. Глинозёмистый цемент. Состав, свойства и области применения.
Глинозёмистый цемент – быстротвердеющее и высокопрочное ГВВ, получаемое путем тонкого измельчения клинкера, содержащего преимущественно низкоосновные алюминаты Са. Однокальциевый алюминат CaOAl2O3 определяет быстрое твердение и другие свойства ГЦ. В небольших количествах в нем также содержатся другие алюминаты Са(CaO2Al2O3) и алюмосиликат Са-геленит 2CaOAl2O3 SiO2. ГЦ обладает высокой прочностью, если он твердеет при умеренной t (не выше 25), поэтому ГЦ нельзя применять для бетонирования массивных конструкций из-за разогрева бетона, а также подвергать тепловлажностной обработке. Если же t бетона превысит 25 , то прочность уменьшится в 2-3 раза. ГЦ очень быстро твердеет. По сравнению с обычным П, у ГЦ при таком же сроке схватывания (30мин-12ч) – тепловыделение примерно в 1,5 раза больше. ГЦ обладает высокой коррозионной стойкостью в сульфатных, морских и углекислых водах.
ГЦ применяют в специальных сооружениях, при спешных ремонтных и монтажных работах, для изготовления жаростойких бетонов и растворов. Он также входит в состав многих расширяющихся цементов.
17. Расширяющиеся и безусадочные цементы.
Безусадочные, расширяющиеся и напрягающие цементы применяют во избежание усадочных трещин для плотной и непроницаемой заделки швов между элементами сборных конструкций, а также для придания конструкции повышенной трещиностойкости (напрягающий). Расширяющийся цемент обладает контролируемым расширением, которое, проявляясь в стесненных условиях, вызывает самоуплотнение цементного камня. Растворы и бетоны на расширяющемся цементе практически непроницаемы для воды и нефтепродуктов (керосин, бензин и др.). Эти цементы относятся к числу смешанных, иногда многокомпонентных вяжущих.
Водонепроницаемый расширяющийся цемент – быстросхватывающееся и быстротвердеющее ГВВ, получаемое путем тщательного смешивания глиноземистого цемента (≈70%), гипса (≈20%) и молотого высокоосновного гидроалюмината Са (≈10%).
Гипсоглиноземистый расширяющийся цемент – быстротвердеющее ГВВ, получаемое совместным или раздельным (с последующим тщательным смешиванием) тонким измельчением высокоглиноземистых клинкеров или шлака и природного двуводного гипса (до 30%). Он расширяется при твердении в воде и проявляет безусадочные свойства при твердении на воздухе. Применяется для омоноличивания стыков сборных конструкций, гидроизоляционных штукатурок, плотных бетонов в ж/б судостроении и при возведении емкостей для хранения нефтепродуктов.
Расширяющийся П – ГВВ, получающееся совместным тонким помолом П-ого клинкера (58-63%), глиноземистого шлака или клинкера (5-7%), гипса (7-10%), доменного гранулированного шлака или других активных минеральных добавок (23-28%). Он отличается быстрым твердениям в условиях кратковременного пропаривания, высокой плотностью и водонепроницаемостью цементного камня.
Напрягающий цемент – быстротвердеющий ГВВ, состоящий из 65-75% П, 13-20% глиноземистого цемента и 6-10% гипса. В процессе расширения в определённых условиях твердения этот цемента создает в арматуре, независимое от ее расположения в ж/б конструкции, предварит напряжения. НЦ применяют для газонепроницаемых конструкций, хранилищ бензина, подводных и подземных напорных сооружениях, спортивных объектов.
ГЛИНОЗЕМИСТЫЙ ЦЕМЕНТ
ГЛИНОЗЕМИСТЫЙ ЦЕМЕНТ
Этот цемент называют по-разному (он известен так же как алюминатный цемент или как цемент из алюмината кальция). Этот цемент, первый патент на который был выдан в 1908 г., появился в результате интенсивных поисков сульфатостойкого заменителя портландцемента.
Благодаря высокой скорости нарастания прочности, химической стойкости от жаростойкости этот цемент нашел свою область применения, однако масштабы его использования все же ограничены; так, в Великобритании, но данным за 1975 г., производство глиноземистого цемента составило 120 тыс. т, т. е. около 20 % его мирового выпуска, не считая РФ.
Высокоалюминатный клинкер получают, обжигая сырьевые материалы (известняк или мел и бокситы) при высокой температуре. Полученный клинкер, в отличие от портландцементного, не требует последующего введения добавок, по скольку он содержит такие алюминатные фазы, для которых не характерны короткие сроки схватывания (подобно CSA в портлаидцементном клинкере). Высокоалюминантный клинкер, будучи более прочным, чем портлапдцементный, требует поэтому больших энергозатрат на помол.
Английским стандартом 1972 г., предусматривается помол высокоалюминатного клинкера до удельной поверхности 225 м2/кг, т. е. это меньше, чем удельная поверхность современных портландцементов.
Цвет глиноземистого цемента может быть от желто-коричневого до темно-серого в зависимости от содержания в нем железа и степени окисления компонентов, присутствующих в цементе. Железо в двухвалентном состоянии придает цементу темную окраску, тогда как трехвалентное — светлую. Глиноземистый цемент белого цвета выпускают в качестве жароупорного; он содержит очень мало железа.
Хотя сроки схватывания глиноземистого цемента и портландцемента сопоставимы, прочность бетонов на первом из них растет так интенсивно, что уже к одним суткам может достичь 90 % нормативной. Благодаря высокой ранней прочности бетонов на глиноземистом цементе их используют при производстве сбор железобетона (главным образом, предварительно напряженного) и проделанных ремонтных работ. В связи с высокой экзотермичностью процессов гидратации глиноземистого цемента, протекающих за весьма короткий период времени, на этом цементе можно вести бетонирование при низкой температуре окружающего воздуха без специального утепления. Однако из-за высокой стоимости такого цемента он для этих целей практически не применяется.
Прочность бетона на глиноземистом цементе зависит от температуры, причем ее увеличение приводит к ухудшению механических показателей бетона. Как мы знаем, по мере повышения температуры воды в течение 28 сут прочность бетона снижалась независимо от ВЦ.
Аналогичная тенденция прослеживалась и для бетонов в более раннем возрасте. Этот факт весьма важен, поскольку бетон на глиноземистом цементе часто используют в тонкостенных изделиях и очень существенно, чтобы при уходе за ними предусматривалось исключение подъема температуры. При этом следует иметь в виду, что прочность таких бетонов снижается и в том случае, если они первоначально выдерживались при температуре окружающей среды, а затем при более высокой температуре. Однако сказанное не относится к бетонам на глиноземисто-портландцементных смесях.
При температуре 80 СС процессы гидратации (приводящие к образованию C3AHfi и АН3) протекают весьма интенсивно; поскольку упаковка частиц СА очень плотна, возможно непосредственное формирование прочных структур между кристалликами С3АНе. При 20 СС, однако, подобные связи становятся менее предпочтительными, так как С3АН6 и АН3 переносятся и рекристаллизуются в порах первичной структуры гексагональных фаз.
Шлакопортландцементы.
КОРРОЗИЯ БЕТОНА В МОРСКОЙ ВОДЕ
Теории карбонизационной усадки бетона
УСАДКА ПРИ КАРБОНИЗАЦИИ
Механизм действия морозного разрушения бетона.
ВОЗДЕЙСТВИЕ МОРОЗА
НЕДОСТАТКИ ЦЕМЕНТОВ, СОДЕРЖАЩИХ MgO И СаО
БИОЛОГИЧЕСКАЯ КОРРОЗИЯ БЕТОНА
Способы предупреждения щелочной коррозии.
Кремнеземистые заполнители.
ЩЕЛОЧНАЯ КОРРОЗИЯ ЗАПОЛНИТЕЛЯ
Жаростойкий бетон.
Глиноземистый цемент содержит заметное количество алюмоферрита кальция.
ГЛИНОЗЕЛНИСТЫЙ ЦЕМЕНТ
ФОСФАТНЫЕ ЦЕМЕНТЫ
Стирол
СЕРНЫЙ БЕТОН
Повторное использование бетона
Портландцементный бетон
Справедливость законов смеси применительно к прочности пропитанного бетона
Раствор и бетон пропитанный серой
Техника полимеризации
Пропитанный полимером раствор и бетон
Армирование асбестовыми волокнами композитов на основе цемента
Свойства зоны контакта проволоки и цемента
Механические свойства дисперсно-армированных цементных композитов
Основы дисперсного армирования
Высокоподвижная бетонная смесь
Свежеприготовленная бетонная смесь
Затвердевший бетон
Литая бетонная смесь
Замедлители схватывания бетона
Микроструктурные аспекты
Оценка количества хлорида
Хлорид кальция и коррозия.
Хлорид кальция и свойства бетона.
Химические добавки в бетон
Сорбция воды и модуль упругости.
Явления сорбции и изменения длины: теоретическое рассмотрение
Бетон.
1 526 просмотров
Производство глиноземистого цемента.
Сырьем для глиноземистого цемента служат бокситы и известняки. Известняки были уже описаны на странице о производстве цемента, поэтому здесь мы ограничимся рассмотрением бокситов.
Бокситы представляют собой смесь какого-либо гидрата окиси алюминия (бемита y-Аl2О3*Н2О; диаспора a-Аl2О3*Н2О или гидраргиллита y-Аl2O3 -3Н2О), являющегося главной составной частью, с глинистым веществом, кварцем, окислами железа и титана и т. д. Бокситы встречаются в ограниченном числе мест. Они служат также сырьем для производства глинозема, электрокорунда, огнеупоров.
По химическому составу бокситы неоднородны. Содержание в них отдельных окислов колеблется в довольно широких пределах; так, например, АI2О3 в них может быть 30-75%; SiO2 2-20%; Fе2O3 2-40%; TiO до 5% и связанной воды 10-25%. Для производства глиноземистого цемента необходимо, чтобы кремневый модуль или коэффициент качества (%Аl2О3/%SiO2) боксита был не меньше 2.
Известняк, используемый в производстве глиноземистого цемента, не должен содержать больше 1,5% SiO2 и 2% MgO.
Существуют два способа производства глиноземистого цемента. Первый из них основан на спекании сырьевой смеси, а второй — на ее плавлении. По первому способу тонкоизмельченная и тщательно перемешанная смесь боксита и известняка обжигается до спекания при температуре 1150-1250°С; полученный продукт обжига размалывается в тонкий порошок. Обжиг до спекания можно вести во вращающихся, шахтных, кольцевых, камерных, туннельных печах и на спекательной решетке. При обжиге не во вращающихся печах сырьевую шихту нужно брикетировать. Во вращающихся печах обжиг можно вести как по сухому, так и по мокрому способу производства. При обжиге шихты в печах, где возможна присадка золы, следует применять малозольное или беззольное топливо.
В процессе производства глиноземистого цемента методом спекания приходится сталкиваться с затруднениями, вызываемыми малым интервалом плавкости, т. е. малой разницей между температурами плавления и спекания. Чем больше этот интервал, тем удобнее вести обжиг сырьевой смеси до спекания, так как возможные местные перегревы в печи не вызывают расплавления или сваривания обжигаемого материала. Сырьевая смесь, содержащая повышенное количество окислов железа; имеет близкие температуры спекания и плавления (разница между ними не более 30-50 0С) и поэтому непригодна для получения глиноземистого цемента методом спекания. Следует отметить, что температура плавления цементного клинкера превышает температуру его спекания примерно на 300°С.
При обжиге глиноземистого цемента методом спекания требуются более чистые бокситы с небольшим содержанием кремнезема (до 8%) и окиси железа (до 10%). При получении глиноземистого цемента методом плавления можно, использовать сырье с большим количеством примесей и менее тонко размалывать сырьевую смесь. Указанные трудности препятствуют распространению метода спекания, несмотря на меньший расход топлива и более легкую размалываемость клинкера.
Глиноземистый цемент можно получать плавлением в вагранках, электрических, доменных печах, а также в конвертерах. Вагранки с водяным охлаждением применяют при небольшом объеме производства. Стенки ее сделаны из пустотелых металлических коробок, по которым циркулирует вода. На металлических стенках, с внутренней стороны, в процессе работы вагранки образуется обмазка, которая и служит огнеупорным футеровочным слоем. Сырьевую смесь подготавливают так же, как и при обжиге цемента в шахтных печах. Шихту в виде брикетов загружают через загрузочное отверстие вперемешку с коксом, откуда она поступает в цилиндрическую или коническую шахту. В нижнюю часть печи — горн — подается необходимый для горения воздух. Расплавленная при 1500-1600°C шихта собирается на дне горна и через определенные промежутки времени выпускается из печи сквозь выпускное отверстие. В процессе плавки кокс восстанавливает железо, содержащееся в шихте в окисной форме, до FeO и частично до металлического железа, причем высокоглиноземистый шлак вследствие меньшего удельного веса собирается над восстановленным железом, которое стекает в нижние слои расплава и может удаляться. Кремнезем в вагранке не восстанавливается, поэтому для такого производства требуются высокосортные бокситы с небольшим содержанием примесей. Потребляет эта печь довольно большое количество малозольного топлива — кокса (35-40% от веса цемента). Все это ограничило сферу распространения печей такого типа.
В электрических печах используется теплота, развиваемая током, проходящим через расплавленную шихту. Шихта обычно состоит из боксита, извести, металлических добавок (железная стружка, скрап) и кокса. Кокс является восстановителем кремнезема и окислов железа, а металлические добавки вводятся для связывания образующегося кремния в ферросилиций. В этих печах можно плавить шихту в сильно восстановительных условиях. Это необходимо при использовании сырья с высоким содержанием кремнезема. Восстановление кремнезема начинается при температуре 1150-1200°С и идет достаточно интенсивно при температуре 1800-2000 0С при избытке углерода. Часть кремния (до 15%) при этом улетучивается, а остальное его количество растворяется в расплаве так же восстановленного железа и образует малокремнистый ферросилиций. Удельный вес его достигает 6,5, а удельный вес высокоглиноземистого шлака около 3,0.
При таком способе производства бокситы должны содержать не более 15-18% SiO2; 15-17% окислов железа, отношение АI2О3 к SiO2 должно быть не менее 3. В электрические печи сырье подают в виде кусков размером 20-40 мм, причем известняк обычно предварительно обжигают до удаления СО2, боксит же сушат, а иногда и обжигают для обезвоживания. При загрузке в электрическую печь влажного боксита и необожженного известняка, они, попадая сразу в зону с высокой температурой, вызывают бурление расплава, выбросы и взрывы, а выделяющаяся из известняка углекислота, кроме того, реагирует с углеродом электрода, ускоряя его обгорание.
В нижней части печи скопляется ферросилиций, а в верхней — глиноземистый цемент, очищенный от кремнезема, что улучшает качество цемента. Оба материала при температуре 1550-1650°С периодически выпускают через летки в изложницы. Электроплавка дает возможность получать из низкосортных бокситов высококачественный глиноземистый цемент.
В электрических печах можно получать глиноземистый цемент и в окислительных условиях. При этом в шихту не вводят восстановитель и она должна содержать небольшое количество кремнезема.
При доменной плавке шихта состоит из железистого боксита, известняка, металлического лома и кокса. В доменной печи шихта подсушивается и декарбонизируется. Окислы железа восстанавливаются газами, содержащими СО, а также твердым углеродом. В горне печи образуется в верхней части высокоглиноземистый шлак, а в нижней чугун. Оба материала периодически выпускаются из домны, причем температура шлака составляет 1600-1700°C, а чугуна 1450-1550°С. Охлаждают высокоглиноземистый шлак в изложницах или же разливают его на площадках слоем 100-150 мм. Домна является агрегатом, производящим три ценных продукта: чугун, глиноземистый цемент и доменный газ. Содержание окислов железа при этом не ограничивается, так как они восстанавливаются и переходят в чугун. Кремнезем восстанавливается лишь в небольшой степени, и поэтому коэффициент качества (А12О3/SiО2) должен быть не менее 7.
Глиноземистый цемент можно получать и путем плавления в конвертере.
Расплавленная масса охлаждается медленно. Это повышает качество глиноземистого цемента, так как образующиеся при медленном охлаждении кристаллические алюминаты кальция обладают более высокими гидравлическими свойствами.
Дробление и помол получаемых при плавлении в домнах и других печах глиноземистых шлаков осуществляются в мощных дробилках и мельницах и связаны с большим, чем при производстве цемента, расходом энергии (80-110 квт-ч на 1 т цемента) вследствие высокой твердости шлаков (7,0-7,5 по шкале Мооса). Охлажденный шлак подвергается двухступенчатому дроблению на щековой и конусной дробилке, а затем измельчается в трубных мельницах. Глиноземистый цемент измельчается до прохождения сквозь сито № 008 не менее 90% подвергаемой просеиванию пробы (ГОСТ 969-41). В состав глиноземистого цемента при помоле можно вводить до 2% специальных добавок.
Глиноземистый цемент — Вяжущие материалы
Глиноземистый цемент
Глиноземистый цемент — быстротвердеющее гидравлическое вяжущее, состоящее преимущественно из моноалюмината кальция (СаО * А1203). Свое название этот цемент получил от технического названия оксида алюминия А1203 — глинозем.
Промышленное производство глиноземистого цемента началось во Франции в 1912 г. под названием цемент фондю (в Европе этот цемент до сих пор носит такое название). Глиноземистый цемент с успехом использовался французами в ходе Первой мировой войны для срочного восстановления мостов и других инженерных сооружений. В других европейских странах его производство началось только в 20-е годы. Причина этого не только в том, что производство глиноземистого цемента было строго засекречено, но и в том, что Франция в то время была одной из немногих стран, имеющих залежи бокситов и дешевую электроэнергию ГЭС — два фактора, необходимых для производства глиноземистого цемента.
Получение. Сырьем для глиноземистого цемента служат, как уже было сказано, бокситы и чистые известняки. Бокситы — горная порода, состоящая из гидратов глинозема (А1203 * лН20) и примесей (в основном Fe203, Si02, СаО и др.). Бокситы широко используются в различных отраслях промышленности: для получения алюминия, абразивов, огнеупоров, адсорбентов и т. п., а месторождений с высоким содержанием А1203 очень немного.
Производство глиноземистого цемента более энергоемко, чем производство портландцемента. Клинкер глиноземистого цемента получают либо плавлением в электрических или доменных печах (при 1500…1600 °С), либо спеканием (при 1200…1300 °С). Размол клинкера затруднен из-за его высокой твердости. В целом из-за того, что производство глиноземистого цемента очень энергоемко, а сырье (бокситы) — дефицитно, его стоимость в 8… 10 раз выше, чем стоимость портландцемента.
Состав. Химический состав глиноземистого цемента, получаемого разными методами, находится в следующих пределах: СаО — 35…45 %; А1203 – 30…50 %; Fe203 – 0…15 %; Si02 – 5…15 %. В минеральном составе клинкера глиноземистых цементов преобладает однокальциевый алюминат СаО * А1203 (СА), определяющий основные свойства этого вяжущего. Кроме того, в нем присутствуют: алюминаты — СА2, С12А7; двухкальциевый силикат C2S, отличающийся, как известно, медленным твердением, и в качестве неизбежной балластной примеси алюмосиликат кальция — геленит — 2СаО * А1203 * 2Si02, не способный к твердению.
Твердение. Процесс твердения глиноземистого цемента и прочность образующегося цементного камня существенно зависят от температуры твердения. При нормальной температуре (до + 25 °С) основной минерал цемента СА взаимодействует с водой с образованием кристаллического гидроалюмината кальция и гидроксида алюминия в виде гелевидной массы:
2(СаО * А1203) + 11Н20 = 2СаО * А1203 * 8Н20 + 2А1(ОН)3
Суммарное тепловыделение (Q) у глиноземистого цемента немного ниже, чем у портландцемента (около 300…400 кДж/кг), но протекает оно в очень короткие сроки (в первые сутки выделяется 70…80 % от общего количества теплоты). Поэтому в случае больших объемов бетонирования возможен перегрев бетонов на глиноземистом цементе.
Если же температура твердеющего глиноземистого цемента превысит 25…30 °С, то изменяется химизм твердения, и вместо С2АН8 образуется С3АН6; при этом прочность цементного камня будет ниже в 2…2,5 раза.
Поэтому глиноземистый цемент не рекомендуется использовать для бетонирования массивных конструкций, где возможен саморазогрев бетона, а также в условиях жаркого климата. Нельзя также его пропаривать. При работах в зимних условиях, напротив, саморазогрев и быстрое твердение делают глиноземистый цемент очень перспективным.
Свойства. У глиноземистого цемента удивительное сочетание свойств.
Сроки схватывания почти такие же, как у портландцемента: начало — не ранее 30 мин, конец — не позднее 12 ч (реально 4…5 ч).
Твердение. После окончания схватывания прочность нарастает очень быстро (лавинообразно). Уже через сутки глиноземистый цемент набирает до 70 % от марочной прочности, которая у него определяется в 3-суточном возрасте. Марки у глиноземистого цемента такие же, как у портландцемента: 400; 500 и 600.
Усадка глиноземистого цемента при твердении на воздухе ниже, чем у портландцемента, в 3…5 раз. Пористость цементного камня также ниже (приблизительно в 1,5 раза). Это связано с тем, что при одинаковой с портландцементом водопотребности глиноземистый цемент при твердении химически связывает 30…45 % воды от массы цемента (портландцемент — около 20%).
Среда в процессе твердения и в затвердевшем цементном камне у глиноземистого цемента слабощелочная. Свободного Са(ОН)2 цементный камень не содержит. Это обстоятельство в сочетании с пониженной пористостью делает бетоны на глиноземистом цементе более устойчивыми к коррозии в пресной и минерализованной воде.
Области применения. Глиноземистый цемент целесообразно использовать при аварийных и срочных работах, при зимних работах и в тех случаях, когда от бетона требуется высокая водостойкость и водонепроницаемость. Кроме того, глиноземистый цемент является компонентом многих расширяющихся цементов.
Специальная область использования глиноземистых цементов — жаростойкие бетоны. Объясняется это тем, что, во-первых, в продуктах твердения этого цемента нет Са(ОН)2, и, во-вторых, при температуре 700…800 СС между продуктами твердения цемента и заполнителями бетона начинаются реакции в твердой фазе, по мере протекания которых прочность бетона не падает, а повышается, так как бетон превращается в керамический материал (опасность присутствия Са(ОН)2 заключается в том, что при нагреве он переходит в СаО, который при любом контакте с водой гасится, разрушая при этом бетон).
—
Глиноземистый цемент, называемый иногда алюминатным или высокоглиноземистым, представляет собой гидравлическое вяжущее, основными компонентами которого являются алюминаты кальция, в противоположность портландцементу, который состоит в основном из силикатов кальция. Примерами такого цемента могут служить: французский «ciment fondu», германский «Schmelzzement», американский «lumnite cement».
Спекмэн в США и Вид во Франции независимо друг от друга разработали технологию производства глиноземистого, цемента. Оба исследователя опирались на предшествующие работы Вика, Кандло и Шота. Опыты Бэйтса показали, что можно использовать вращающуюся печь для получения клинкера глиноземистого цемента.
Спекмэн пытался получить вяжущее с высокой прочностью в раннем возрасте, добавляя к извести или портландцементу алю-минатные соединения, изготовленные из боксита и высокоглинозе-мистых шлаков. Примерно в 1910 г. на рынке появились различные натуральные цементы под названием «алька», содержавшие добавку алюминатов Спекмэна. В дальнейшем было организовано производство высокоглиноземистых натуральных цементов, а затем глиноземистого цемента, подобного тому, который был получен Видом.
Вид, работавший во Франции, ставил своей задачей создать глиноземистый цемент с повышенной сульфатостойкостью, который был необходим для строительства в некоторых районах страны, изобиловавших гипсом. Он решил эту задачу путем сплавления бокситов или других глиноземистых и железистых материалов, содержащих мало кремнезема, с известью в соответствующей пропорции.
Полученный продукт обладал не только сульфатостойкоетью, но и высокой прочностью в раннем возрасте. В 1918 г. после пятилетнего опыта применения этого цемента французским правительством для военных нужд, он ‘был выпущен для общего пользования.
Производство
Сырьем для производства глиноземистого цемента служат обычно низкосортные бокситы и известняк (высокосортные бокситы идут на производство глинозема). Точно дозированная и хорошо перемешанная смесь сырьевых материалов нагревается до температуры, при которой известь вступает в реакцию с глиноземом, образуя соединения алюминатов кальция. Сырьевая смесь полностью плавится примерно при 1540° С. Расплав выпускают из печи, дают ему застыть, охлаждают и затем размалывают с добавками или без них. Во избежание рассыпания застывшего расплава необходимо держать на сравнительно низком уровне содержание кремнезема в смеси.
В США глиноземистый цемент производится по способу плавления тонкоизмельченной сырьевой смеси во вращающейся печи. Эта печь отличается от обычной вращающейся печи, применяемой для производства портландцемента спеканием, тем, что разгрузочный конец ее резко сужен; в этой конической части несколько задерживается обжйгаемый материал, что облегчает процесс полного расплавления его. Для ускорения реакции между известью и бокситом прибегают к спеканию сырьевой смеси при температуре ниже точки начала плавления.
В других странах для производства глиноземистого цемента применяют отражательные или электродуговые печи. Шахту печи загружают кусками известняка и боксита, а также бокситовыми брикетами, из которых под действием горячих газов, выделяющихся из печи, удаляются СОо и другие летучие вещества. Материал постепенно опускается и попадает в печь, где происходит плавление его. В отражательной печи выпуск расплава производится непрерывно, а в электрической — периодически.
Скорость охлаждения расплава оказывает большое влияние на сроки схватывания и скорость твердения глиноземистого цемента. Методы охлаждения, применяемые на том или ином заводе, обычно держатся в секрете. Скорость охлаждения влияет также на размалываемость клинкера или застывшего расплава. Ввиду исключительной твердости и абразивности глиноземистого клинкера его приходится молоть значительно крупнее, чем клинкер портландцемента.
Химические и физические свойства
По пределам колебаний химического состава он заметно отличается от глиноземистого цемента, производимого в некоторых странах. Следует отметить, что американский глиноземистый цемент содержит примерно одинаковое количество извести и глинозема. Значительное количество закиси железа ib глиноземистом цементе показывает, что плавление сырья происходит в восстановительной среде.
Петрографическое исследование глиноземистого цемента показывает, что он состоит из кристаллической фазы, главным образом однокальциевого алюмината, который окружен темной аморфной массой, содержащей большое количество железа и немного извести, глинозема и кремнезема, не успевших закристаллизоваться. В кристаллической фазе часто присутствуют небольшие количества устойчивой и неустойчивой модификаций пятикальциевого трехалюмината, причем устойчивая модификация, очевидно, преобладает в тех случаях, когда содержание железа в цементе очень ограничено. Отношение кристаллических компонентов к аморфным колеблется в зависимости от скорости охлаждения и режима обжига в печи.
Работы Ранкина и Райта по изучению системы СаО—А1203— Si02 показали, что в ней должен образовываться также трехкальциевый пятиалюминат, хотя он и не может быть обнаружен при микроскопическом исследовании.
В некоторых цементах кремнезем присутствует в форме кристаллического двухкальциевого алюмосиликата (галенита, C2AS). В большом количестве это соединение может понизить прочность цемента. Кроме того, кремнезем может присутствовать и в форме ортосиликата кальция (C2S). Второстепенные компоненты, иногда наблюдаемые в глиноземистом цементе (окись титана, сульфиды, скись фосфора, щелочи), как полагают, не оказывают существенного влияния на его свойства.
При гидратации глиноземистого цемента образуются большие количества геля, что объясняется реакцией между водой и СА, а также устойчивой и неустойчивой модификациями С5А3. Это геле-образное аморфное вяжущее вещество является носителем высокой прочности твердеющего цементного теста в раннем возрасте, в результате чего цемент приобретает значительную часть своей конечной прочности уже в первые сутки. Но и после этого срока гидратация продолжается, причем образуются новые количества аморфного вещества, способствующего созданию плотной непроницаемой структуры бетона.
Если глиноземистый цемент гидратируется при температуре около 27° С или выше, то образуются кубические кристаллы трехкальциевого гидроалюмината, причем прочность бетона снижается. Поэтому бетон, изготовленный из глиноземистого цемента, в период от начала схватывания до односуточного возраста поливают водой, чтобы рассеять тепло, выделяющееся при быстрой гидратации. По той же причине не применяют пропаривания глиноземистого бетона и укладывают его слоями не толще 30 см. Бетон из глиноземистого цемента, подвергавшийся сильному нагреванию во время твердения, имеет характерный шоколадно-серый оттенок. Орошение бетона водой предупреждает шелушение его поверхности вследствие карбонизации.
Для получения цемента с нормальными сроками схватывания обычно прибегают к регулированию скорости охлаждения расплава. Наряду с этим применяются и некоторые замедлители схватывания, как хлористый натрий, нитрат натрия, глицерин, сахар. Излишнее количество сахара может задержать схватывание на неопределенное время. Гипс, который служит обычно для замедления схватывания портландцемента, ускоряет схватывание глиноземистого цемента. Другие формы серного ангидрида также ускоряют схватывание. Подобным же образом действуют на глиноземистый цемент гидроокись кальция, гидроокись натрия, карбонаты кальция и натрия.
Добавка небольшого количества портландцемента ускоряет начало схватывания теста, раствора и бетона из глиноземистого цемента. В свою очередь небольшая добавка глиноземистого цемента ускоряет схватывание портландцемента. Добавка одного цемента к другому в избыточном количестве может вызвать мгновенное схватывание. Это свойство используется для получения высокопластичного, но быстросхватывающегося цементного раствора, который необходим при укладке дорожных бетонных плит и заделке отверстий в бетонных сооружениях под гидростатическим давлением. Следует иметь в виду, что при смешивании разных цементов известное влияние на сроки начала схватывания оказывают также и колебания в содержании S03 и щелочей в портландцементе.
Объемные деформации твердеющего теста глиноземистого цемента при увлажнении и высыхании в основном такие же, как и у портландцементного теста. Это относится и к усадке при высыхании свежего цементного теста. Коэффициент термического расширения и показатели проницаемости у обоих цементов также одинаковы. Модуль упругости глиноземистого цемента несколько выше и составляет около 315 000 кг/см2. Величина его колеблется в зависимости от прочности, как и у портландцемента, а прочность в свою очередь изменяется с изменением водо-цементного отношения и температуры твердения.
Применение
Глиноземистый цемент применяется для изготовления различных специальных бетонов — огнеупорного, жаростойкого, корро-зиестойкого и быетротвердеющего, а также для защиты каменных или бетонных сооружений от действия грунтовых вод. ‘
Хотя усиленное разогревание бетона из глиноземистого цемента во время твердения вредно отражается на его прочности, а в особо неблагоприятных условиях температуры и влажности может даже вызвать разрушение его, тем не менее при правильном подборе заполнителей и хорошей технологии можно изготовить прекрасный огнеупорный бетон для футеровок. Заполнители для такого бетона могут быть кислые, основные или нейтральные. Состав смеси может колебаться от 1 : 4 (цемент — заполнители по объему) для низкотемпературных печей (1090 °С) до 1 : 7 для высокотемпературных (1425 °С и выше). Такие огнеупорные бетоны отличаются хорошей прочностью в холодном состоянии и приобретают очень высокую прочность в условиях огня или высокой температуры благодаря остекловыванию, т. е. поверхностному оплавлению компонентов.
Жаростойкий бетон применяется для строительства фундаментов печей, трубопроводов для пропуска горячих газов, полов под печами и возле печей, т. е. в таких местах, где он подвергается значительному действию тепла при температуре ниже точки плавления. Так как глиноземистый цемент не выделяет извести при гидратации, он является прекрасным вяжущим для изготовления такого бетона. В качестве заполнителей могут быть применены старые огнеупоры, дорожный клинкер, облицовочный клинкерный кирпич, диабаз, наждак, измолотые до предельной крупности 3,75 см. Для улучшения изоляционных свойств бетона можно применить легкие огнеупорные заполнители. Следует избегать заполнителей, которые выделяют известь. Оптимальный состав бетона (по объему): 1 часть цемента на 2,5 части мелкого заполнителя (предельная крупность зерен 6 мм) и на 2,5 части крупного заполнителя. При применении очень плотных заполнителей следует увеличить количество мелких заполнителей по отношению к крупным.
Глиноземистый цемент отличается не только повышенной сульфатостойкостью, но и хорошей устойчивостью против действия органических кислот, различных соединений серы, серной кислоты, молочной кислоты, соляного раствора, крахмала, сахарозы, кислотных масел, тростникового сока, мелассы. Он неустойчив в отношении уксусной, соляной и азотной кислот, сильных растворов сульфатов и каустиков. Бетон состава 1:2:4с высококачественными тяжелыми заполнителями обычно обладает удовлетворительной солестойкостью. Следует избегать применения тощих смесей, которые требуют более длительного перемешивания.
Монолитный бетон из глиноземистого цемента с обыкновенными заполнителями созревает уже через сутки после укладки в нормальных атмосферных условиях. Благодаря повышенному тепловыделению этот бетон можно укладывать при низкой температуре без применения защитных мер или с минимальной защитой. Отпадает также необходимость в добавке хлористого кальция в качестве ускорителя твердения. При изготовлении бетона для большинства строительных работ достаточно, чтобы расход цемента составлял 300—330 кг/м3. при минимальном количестве воды. Выдержка бетона может не превышать 24 час. после укладки.
Смеси глиноземистого цемента и портландцемента обычно применяются для защиты бетонных, кирпичных и каменных сооружений от просачивания воды. Эти смеси наносятся обычным способом или торкретированием.
Читать далее:
Глиноземистый и расширяющиеся цементы
Цементы с минеральными добавками
Специальные виды портландцемента
Свойства портландцемента
Схватывание и твердение портландцемента
Производство портландцемента
Неорганические вяжущие вещества
Разные материалы для штукатурных работ
Заполнители для штукатурных работ
Вяжущие материалы для штукатурных работ