Активность цемента: методы определения активности
О прочности цемента обычно судят по его марке, которая определяется сразу после выпуска материала. Но в результате транспортировки или при длительном хранении цемент начинает взаимодействовать с частицами воды, происходит реакция гидратации, и прочность цемента падает.
СодержаниеСвернуть
Для нахождения остаточной прочности проводят испытания аналогичные испытаниям по установлению марки. Так осуществляется определение активности цемента.
Что такое активность цемента
Активность цемента (ГОСТ 310.4-81) – прочность при испытании на сжатие образца из цементного раствора. После проведения лабораторных испытаний материалу присваивается марка (производители должны указать ее на упаковке). Например, ЦЕМ 32,5 (М400), ЦЕМ 42,5 (М500) или др.
Цемент может вступать в реакцию с влагой, находящейся в воздухе, при этом образуется твердый цементный камень, что впоследствии отрицательно сказывается на прочности изготавливаемого цементного или бетонного теста. Активность цемента измеряется в МПа, как и его марка.
Особенностью бетона и цемента является то, что эти строительные материалы при эксплуатации со временем становятся только прочнее. Это связано с тем, что процесс гидратации происходит непрерывно. Выделяют три этапа гидратации цемента: активную фазу, перспективную и фазу деградации.
Активная фаза
Длится 28 суток – срок полного застывания цементного раствора. Вступает в реакцию с водой и кристаллизуется за этот период большая часть компонентов.
Перспективная фаза
На протяжении года идет полная кристаллизация, а прочность цемента при этом приближается к максимальному показателю.
Фаза деградации
Кристаллизованные минералы разрушаются в процессе коррозии, в изделии появляются трещины, нарушается структура бетона. Химическая активность цемента может быть меньше его марки даже в полтора-два раза. Например, активность цемента ЦЕМ 32,5 (М400) обычно составляет 200-330 МПа, а активность цемента ЦЕМ 42,5 (М500) – 250-420 МПа.
Активность цемента таблица (представлены несколько заводов изготовителей):
Цементный завод | Марка цемента | Средняя активность кгс/см2 (0.1 МПа) |
Акмянский цементный завод | ЦЕМ 22,5 ЦЕМ 32,5 ЦЕМ 42,5 | 380 476 526 |
Ангарский цементный завод | ЦЕМ 32,5 | 427 |
Балаклейский цементный завод | ЦЕМ 32,5 ЦЕМ 42,5 | 431 528 |
Волковысский цементный завод | ЦЕМ 42,5 | 522 |
Волховский цементный завод | ЦЕМ 32,5 ЦЕМ 42,5 | 473 504 |
Кантский цементный завод | ЦЕМ 22,5 ЦЕМ 32,5 | 374 459 |
Катав-Иваноский цементный завод | ЦЕМ 22,5 ЦЕМ 32,5 | 383 418 |
Красноярский цементный завод | ЦЕМ 32,5 ЦЕМ 42,5 | 470 559 |
Чимкентский цементный завод | ЦЕМ 22,5 ЦЕМ 32,5 | 377 440 |
Факторы, влияющие на активность цемента
На активность цемента оказывают воздействие условия хранения, химический состав материала и дисперсность частиц, которая определяется степенью помола компонентов.
Процесс проведения испытаний активности цемента
Испытания по определению активности цемента по ГОСТу 310.4-81 проводятся в несколько этапов:
- Приготовление цементного теста. Смешивают вяжущее вещество и песок в соотношении примерно один к трем, затем смесь выкладывают горкой и начинают наливать воду. В/Ц отношение составляет от 0,4 до 0,5, но количество воды в смеси может корректироваться в зависимости от результатов второго этапа.
- Определение расплыва конуса смеси. Чтобы испытания по определению активности бетонной смеси, показали максимально точный результат, смесь должна быть нужной консистенции. Испытания по определению подвижности смеси проводят с помощью конуса и встряхивающего стола, диаметр расплыва должен лежать в пределах 105-115 миллиметров.
- Укладка раствора в формочки. Формы имеют размер 4х4х16 сантиметров, их стенки необходимо смазать машинным маслом. После заливки раствора его необходимо уплотнить, то есть провибрировать.
- Твердение цемента. В первый день процесс твердения происходит в емкости с раствором гидравлических веществ, затем 27 суток резервуаре с холодной водой.
- Проведение испытаний. На прочность испытывают три балочки, после чего результаты экспериментов суммируют и находят среднее значение.
Методы определения пределов прочности
Выбор метода определения активности цемента зависит от того, для каких целей цемент будет использоваться в дальнейшем, какой вид и класс бетона будет из него изготавливаться.
Определение пределов прочности на изгиб
Испытание проводят на гидравлических прессах. Образец располагают продольно на двух опорах, постепенно начинают его нагружать. Предел прочности в данном случае определяется по формуле:
Р – нагрузка, l – расстояние между двумя опорами, b и h – ширина и высота балки. Полученное значение измеряется в МПа.
Определение прочности при сжатии
Испытания на прочность при сжатии также проводятся на гидравлических прессах. Чтобы получить значение , надо разделить силу, при которой балка разрушилась (Р) на исходную площадь поперечного сечения бетонного образца.
Определение прочности при пропаривании
Для конструкций, в которых бетон будет подвержен пропариванию с целью сокращения сроков твердения, целесообразно находить активность цемента при пропаривании. В этом случае цемент предварительно проходит обработку в специальной пропарочной камере.
Ускоренный метод
Все стандартные методы по измерению прочности требуют времени, но можно определить активность цемента и ускоренным методом. Для этого применяются специальные приборы, они помогают установить активность материала контракциометрическим методом. В основе работы приборов лежит свойство цемента изменять свой объем при гидратации.
Приборы для определения активности цемента
Существуют различные приборы для определения активности цемента, вот некоторые из них:
- Индикатор активности цемента ИАЦ-04М. Система позволит определить активность образца за 5 минут. Активность цемента вычисляется на основании найденной удельной проводимости В/Ц раствора. Прибор дает большую погрешность – до 5 % в ту или иную сторону, поэтому полностью заменить стандартные испытания им не получится. Индикатор позволит вовремя обнаружить сбои в работе оборудования по изготовлению цемента, неправильный химический или минеральный состав, недопустимые условия хранения.
- Цемент-прогноз 2. Позволяет определить активность цемента в ускоренном режиме за 3 часа, измерения производятся за счет нахождения величины конракции цементного теста. В обычных случаях определение активности производится в 1, 3, и 7-суточных режимах.
Индикаторы активности цемента не могут давать очень точных результатов, но их использование целесообразно, когда нет времени на стандартные лабораторные испытания.
Заключение
Активность цемента является показателем прочности цемента. Она напрямую зависит от условий транспортировки и хранения, а также от продолжительности хранения. Определить активность цемента можно при проведении стандартных лабораторных испытаний, порядок которых описан в ГОСТ 310.4-81.
При необходимости можно провести быстрое тестирование на прочность измерителем активности цемента, но будет получаться результат с низкой точностью.
Определение марки (активности) цемента
Активность цемента определяется как показатель фактической прочности образцов, специально изготовленных для анализа и испытанных в заданных условиях, определенных нормативными документами.
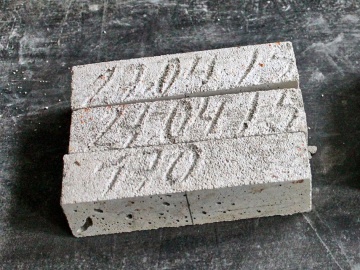
Существует два параметра, определяющих активность (марку) цемента – это определение прочности на разрыв и на изгиб. Для таких испытаний необходимы специально созданные образцы из цементного теста нормальной консистенции, размерами 40*40*160 мм. Все этапы их изготовления и испытания определяются ГОСТом 310.4-81.
Для определения активности цемента применяют как прямые, так и косвенные методы. Прямые методы, самые действенные, но требуют длительного времени (процесс определения основан на твердении цемента), так что для оперативных задач используют косвенные, более быстрые методы. Здесь подходы могут быть различные: кто-то использует контракцию, кто-то оценивает активность через электропроводность цементной суспензии. Оценка активности через электропроводность – простой путь, который при этом нельзя назвать надежным. Прогнозируемые результаты не имеют методологического обоснования и потому рекомендацию для использования в серьезных случаях получить не могут.
Действие контракциометров основано на установлении связи активности цемента с процессом уменьшения объема цемента в результате гидратации специально изготовленного цементного раствора. Это единственный вид приборов, который может быть признан эффективным для оперативного определения активности цемента.
Существуют приборы контракциометры КД-07 и ВМ-7.7, которые могут дать методологически обоснованный результат, однако в данном случае в процессе определения активности (марки) цементов требуется визуальное наблюдение за технологическим процессом, а также проведение подсчета результатов вручную в соответствие с установленной методикой.
Приготовление цементного раствора нормальной консистенции для определения марки цемента
Определение марки цемента предполагает приготовление цементно-песчаного раствора заданным образом. Для смешивания раствора в пропорции 1:3 понадобится:
- 500 г цемента (непосредственно того образца, который назначен к исследованию).
- 1,5 кг песка. Для получения точного результата важно выбрать правильный песок – чистый (мытый) кварцевый песок, с содержанием SiO2 не менее 98%. Влажность материала – менее 0,2 % с потерями при прокаливании менее 0,05%.
Если не соблюсти эти условия, то оценку марки цемента нельзя будет признать корректной.
Оба компонента высыпают в чашу, внутренняя часть которой протерта мокрой тканью. Срок для промешивания – 1 минута. Затем в смеси делается лунка, в которую вливают 200 г воды. Время, выделяемое на впитывание – 0,5 минут, а затем в течение минуты перемешивают вручную. Далее смесь помещают в мешалку (ее чашу протирают влажной тканью) и мешают в течение 2,5 минут.По окончанию процесса нужно оценить консистенцию получившегося раствора. Для этого применяют встряхиватель, на котором имитируют виброуплотнение раствора.
Смесь закладывается в два этапа слоями равной толщины в стандартную форму-конус, установленную на диск встряхивающего столика, а после этого штыкуется по ГОСТу:
- нижний слой – 15 раз,
- верхний слой – 15 раз.
Затем, в указанной последовательности, выполняются следующие действия:
- Форму для загрузки снимают, излишки раствора срезают.
- Цементный конус встряхивают 30 раз в течение 30 ± 5 секунд.
- Основание конуса измеряют по перпендикулярным диаметрам и берут среднее значение.
Раствор нормальной консистенции и приемлем для измерений, если его расплыв 106-115 мм.
Изготовление образцов
Образцы для определения марки цемента изготавливают стандартных размеров в специальных формах. Формы должны быть разъемными и из прочного материала – к примеру, из чугуна или стали. Перед заполнением раствором форму смазывают машинным малом, а стыки – вазелином. Форму заполняют на 10 мм, устанавливают на вибростенд и после запуска установки форма заполняется окончательно – порционно в течение 2 минут. Через три минуты установка отключается, а излишки смеси снимают ножом, смоченным в воде. Образец сглаживают, маркируют и, оставляя его в форме, выдерживают в специализированной ванне с гидравлическим затвором 24 часа (в случае растрескивания образца, оставляют его в ванной еще на 48 часов). Затем их достают из ванны, извлекают из форм и укладывают в бассейн с водой. Вода должна быть 20 ± 2 градусов по Цельсию и накрывать образцы минимум на 20 мм. Воду в бассейне заменяют раз в две недели. И после 28 суток твердения их извлекают из ванной, испытания проводятся максимум за час.
Виды определения пределов прочности
В зависимости от особенностей дальнейшего использования цемента и бетона на его основе существует несколько различных подходов к определению активности. Рассмотрим несколько методик.
Определение прочности на изгиб
Суть метода в постепенном увеличении нагрузки на образец посредством специального пресса (скорость нагружения — 50±10Н/с). При этом испытание образцов производится при их расположении поперечной гранью – продольно. Итоговый результат берут как среднее арифметическое между двумя самыми высокими показателями испытаний образцов из трех.
Определение прочности при сжатии
Определение прочности цемента при пропаривании
Для изготовления конструкций из бетона или железобетона подчас необходимо сократить срок твердения. Для этого используют тепловлажную пропарку. Именно поэтому для таких случаев целесообразно использовать определение активности цемента при пропаривании.
Подготовка образцов и все процедуры проводятся в стандартных условиях, однако пропаривание необходимо производить в специализированной камере. Стандартизированная температура — 20±3 градусов по Цельсию при выключенном обогреве в течение 2 часов. Значение прочности определяется в соответствие с ГОСТом.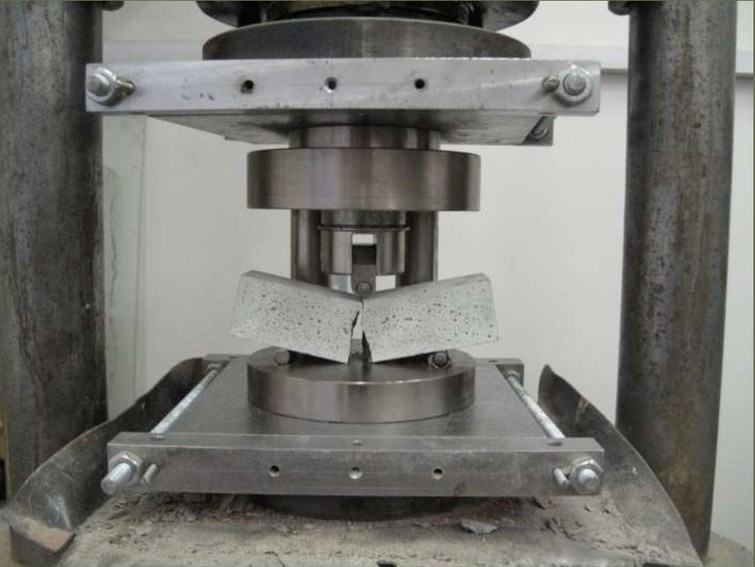
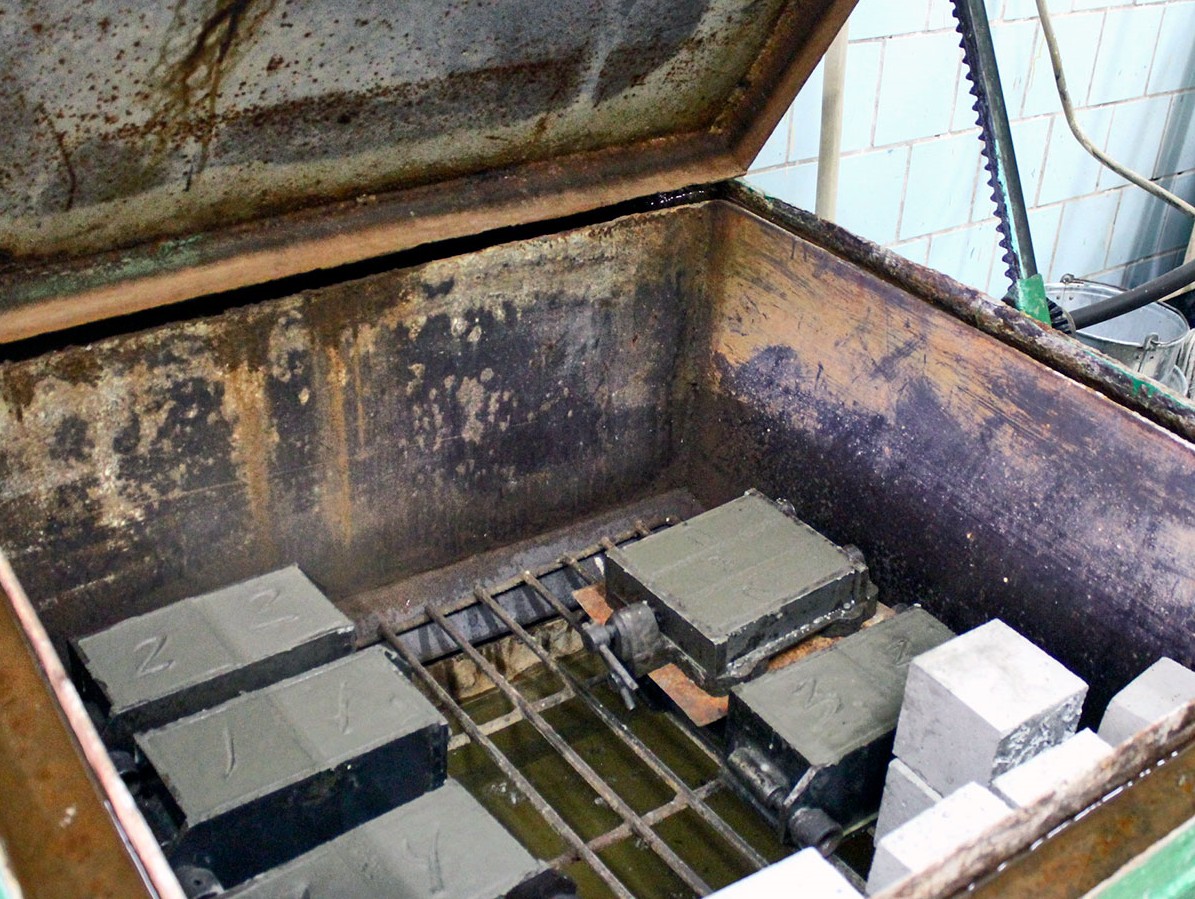
Однако все эти методы требуют очень длительного времени. Самый скорый метод определения марки цемента без потери точности измерений – контракциометрический. Он использует для оценки показатели уменьшения объема раствора при гидратации материала. Именно эти данные ложатся в основу расчетов активности цемента. Именноэтот метод лег в основу нового прибора предприятия «Интерприбор».
Этот прибор позволяет исследования по определению активности цемента проводить в ускоренном режиме – то есть фактически в течение 3 часов. Также «Цемент-прогноз» позволяет работать с такими измерениями как сроки схватывания цемента, морозостойкость, прочность и водонепроницаемость бетона.
Новый прибор для определения активности цемента
В 2009 году компания «Интерприбор» разработала и запатентовала прибор «Цемент-Прогноз», основанный на контракциометрическом методе измерений. Этот прибор автоматический. В его стандартную комплектацию входят: электронный блок, стакан для проб цементного образца, камера измерения и сервисное ПО, нацеленное на обработку данных по методике. Именно программное обеспечение позволяет все результаты перенести на компьютер, заархивировать и, при необходимости, конвертировать в Exсel.
Принцип работы прибора основан на регистрации изменения объема воды в герметичной камере, дополнительно можно фиксировать температуру пробы. Камера заполняется водой, а в нее помещается образец в специальном мерном стакане. Измерение занимает в минимальном варианте три часа, по факту которых все измерения переносятся в компьютер. Но существует и 7-суточный контракционный цикл измерений.
Электронный блок позволяет через соединительную коробку подключать и одновременно производить измерения в трех камерах, регистрируя результаты на дисплее прибора и компьютере. Сервисное ПО предлагает обширный объем функций по обработке результатов. Прибор внесен в Государственный реестр средств измерений.
Использование «Цемент-Прогноза» в рабочем процессе облегчит и другие технологические измерения, в частности оценку водоцементного отношения и прочность бетона (МИ 2488-98), морозостойкость (МИ 2489-98), водонепроницаемость бетона (МИ 2625-2000).
-
ИЗМЕРИТЕЛЬ МОРОЗОСТОЙКОСТИ
БЕТОН-ФРОСТ ускоренно определяет морозостойкость бетона по величине аномальных пиков объемных деформаций в соответствии с ГОСТ 10060.3-95. Прибор позволяет пров… -
ИЗМЕРИТЕЛЬ АКТИВНОСТИ ЦЕМЕНТА
Ускоренное определение активности цемента за 3 часа по величине контракции цементного теста в соответствии с методиками измерения МИ 2486-98, МИ 2487-98.
-
Вакуумные измерители проницаемости ВИП-1 предназначены для определения водонепроницаемости бетона и сопротивления проникновению воздуха в соответствии с ГОСТ 12…
Активность цемента и марка (таблица)
Активность цемента – показатель, являющийся ключевым для определения характеристик прочности готового монолита на изгиб и сжатие. Данный параметр напрямую зависит от таких факторов, как тонкость помола клинкера, условия и сроки хранения готовой смеси, а также состава материала.
Определить активность можно несколькими методами – в условиях завода и лаборатории выполняют ряд исследований в порядке, установленном ГОСТом. Сложно, но возможно это сделать и в домашних условиях. Также может использоваться специальный прибор.
В зависимости от активности цементу присваивается определенный класс и марка (любая таблица с характеристиками обязательно включает эти данные).
Прежде, чем использовать цемент в работе и реализовывать те или иные задачи, необходимо ознакомиться с сутью понятия и особенностями установки параметра активности.
Что это такое
Точное определение активности цемента демонстрирует абсолютную прочность испытуемого образца, сделанного из цементного раствора. На основании полученных показателей вяжущему присваивают ту или иную марку и больше понятие активности не используют (в технической документации оно не указывается). Но есть определенные случаи, когда активность и марка цемента устанавливаются в домашних условиях.
Уровень прочности может меняться в зависимости от того, какой вид присадок вводится в состав и в каких объемах. При этом, следует учитывать, что присадки влияют на характеристики смеси и активность, но никак не на марку цемента. К примеру, ускоритель твердения может в разной степени понижать срок набора прочности монолитом, но вот на твердость камня не влияет.
Таким образом, получается, что активность цемента – это своеобразное поведение структуры материала на протяжении срока службы залитой конструкции или изделия.
Как проходит процесс гидратации на разных этапах:- На протяжении первых 28 суток после приготовления раствора – монолит набирает прочность по проекту, в это время основной объем структуры вступает в реакцию и кристаллизуется.
- На протяжении времени эксплуатации – кристаллизация еще может проходить, но активность в состоянии покоя может отсутствовать.
- Окончание срока эксплуатации – минералы в составе кристаллов начинают реагировать с водой, что ведет к коррозии, деформации и другим изменениям.
Получается, что активностью называют динамику твердения и набора прочности застывшего камня, а потом и потери прочности.
Виды активности цемента на протяжении времени эксплуатации:- Активная – все компоненты в составе начинают реагировать, через 28 суток перестают кристаллизироваться.
- Перспективная – цемент набирает прочность, достигает 100% состояния по проекту (в течение года при монтаже конструкций до ввода объекта в эксплуатацию).
- Частично гидратированная (комплексная) – крупные негидратированные части остаются в составе монолита и выступают наполнителем.
Такая условная классификация дает возможность правильно определять состав цемента для приготовления разного типа бетонных смесей и выбора оптимального раствора в процессе проектирования.
Факторы, влияющие на прочность цемента
На прочность цемента влияют несколько основных факторов и несколько второстепенных. Но все они должны обязательно учитываться.
Условия хранения
Время и условия хранения цементного порошка влияют на активность и число МПа прочности. Чем дольше хранится цемент, тем менее он прочный в растворе и тем ниже активность. К примеру, за 3 месяца марка М500 обладает показателями марки М400, а по завершении установленного срока хранения порошок теряет 25-30% изначальных параметров.
Снижение активности в процессе хранения цемента:- В закрытом сухом складе и водонепроницаемых мешках порошок хранит свойства на протяжении месяца, через 2% параметр снижается на 5%, через 3 – на 9%, 4 – на 13-16%.
- В бумажных мешках и сухом складе – через месяц отмечается понижение на 5-6%, через 2 – на 10-11%, 3 – 14-15%, 4 – 20-22%.
Состав материала
Многое зависит и от состава клинкера, качества его обработки в процессе производства вяжущего: в него входят основное сырье, минералы. Активность напрямую зависит от объема и вида вводимых в состав добавок, наличия/отсутствия примесей, концентрации клинкера и т.д.
Так, если в составе есть кварц и кальцит, активность понижается, если же больше алита и алюминатов – всегда повышается. В свою очередь, щелочные добавки влияют на скорость прохождения процесса кристаллизации (в сторону ускорения или замедления).
Дисперсность частиц
Здесь речь идет о степени помола всех компонентов. Порошок мелкодисперсный намного быстрее активизирует реакцию по объему, повышая активность. Если помол крупный, набор прочности происходит намного дольше и активность понижается.
Есть определенная взаимосвязь активности и плотности (удельного веса) цемента. Чем выше показатель активности, тем выше плотность.
Ввиду влияния на свойства цемента множества факторов, очень важно осуществлять контрольные испытания с целью определения характеристик. После исследований принимают решение про корректирование состава либо добавку определенных замедлителей/катализаторов.
Как определяется активность
Чтобы определить активность, используются лабораторные тесты, порядок проведения которых указан в ГОСТе 310.4.
Как определяют активность цемента:- Приготовление цементного раствора из вяжущего, многофракционного песка в соотношении 1:3 и водоцементным отношением до 0.5. Сухая смесь перемешивается с водой.
- Испытания конусом и специальным встряхивающим столиком. Цемент должен демонстрировать расплыв от 106 до 115 миллиметров. Если нужно, все операции повторяют с другим объемом воды.
- Из цемента нормальной густоты делают балочки величиной 4х4х16 сантиметров: смесь укладывается в смазанные маслом формы, послойно и с использованием виброплощадки.
- В первые сутки цемент твердеет в ванне с гидравлическим раствором, потом 28 суток в холодной воде. Вода меняется через 14 суток.
- Три полученных результата (конус, балки, твердение в воде) суммируются и определяется самая близкая по индексу марка вяжущего.
Если сроки исследований не определены или использовался несвежий цемент, активность может быть определена неправильно.
В домашних условиях
Приобретая вяжущее, его проверяют на качество и прочность. Сделать это вне лаборатории и без специальных средств трудно, но можно. Обычно оценивают состояние и цвет. Порошок с высокой активностью должен быть серого цвета с зеленым подтоном. Он хорошо протекает сквозь пальцы, комки могут быть только в мешке и минимального размера (и разминаются легко в руках). Если есть твердые комки – свойства ухудшаются.
Тестирование водно-визуальным методом:- Смешивание цемента с щелочной минеральной водой до получения консистенции теста.
- Формирование образца в форме диска с тонкими краями и утолщением внутри. Если тестовый образец затвердел за 10-12 минут и ощутимо нагрелся – цемент качественный, активность высокая. Материал низкого качества твердеет в течение получаса, потом может покрываться трещинами.
- Затвердевший диск аккуратно оборачивают влажной тканью, отправляют в полиэтиленовый пакет или емкость из пластика. Выжидают 3 суток, достают и смотрят: материал должен стать еще более прочным, при постукивании давать металлический отзвук, от удара не рассыпаться. Возможно наличие минимальных трещин в формате сетки.
Осуществляя тестирование, нужно проверять цемент разных партий – материал везде разный.
Новый прибор для определения
Для определения активности цемента могут использоваться специальные приборы. Так, компания «Интерприбор» в 2009 году запатентовала устройство «Цемент-Прогноз», которое осуществляет контракциометрический способ исследований. Прибор работает автоматически, комплектация включает: сервисное ПО (благодаря ему можно переносить результаты исследований на компьютер, отправлять в архив, Excel), камера изменения, стакан для проб образца, электронный блок.
Прибор определяет температуру и изменения объема воды в камере. Камеру заполняют водой, отправляют образец в стакане, ждут три часа и получают результаты. Есть и цикл контракционных измерений, проходящий за 7 суток.
Благодаря соединительной коробке электронный блок можно подключать к 3 камерам, проводя в них исследования одновременно. Функций для обработки результата огромное множество. В Государственный реестр измерений прибор внесен.
«Цемент-Прогноз» позволяет не только облегчить проведение исследований, но и выполнять их в разных форматах: есть приборы для измерения водонепроницаемости бетонного монолита, прочности и водоцементного отношения, морозостойкости и т.д.
Планируя выполнять ремонтно-строительные работы, очень важно проверять качество и свойства используемого цемента, так как от него зависят долговечность и надежность конструкций/сооружений. До начала работ нужно точно определить, что вяжущее соответствует марке и указанным характеристикам.
ГОСТ 310.4-81 Цементы. Методы определения предела прочности при изгибе и сжатии (с Изменениями N 1, 2), ГОСТ от 21 августа 1981 года №310.4-81
ГОСТ 310.4-81
Группа Ж19
Цементы
МЕТОДЫ ОПРЕДЕЛЕНИЯ ПРЕДЕЛА ПРОЧНОСТИ ПРИ ИЗГИБЕ И СЖАТИИ
Cements. Мethods of bending and compression strength determination
МКС 91.100.10
ОКП 57 3000
Дата введения 1983-07-01
1. РАЗРАБОТАН Министерством промышленности строительных материалов СССР
Государственным комитетом СССР по делам строительства
Министерством энергетики и электрификации СССР
ВНЕСЕН Министерством промышленности строительных материалов СССР
2. УТВЕРЖДЕН И ВВЕДЕН В ДЕЙСТВИЕ Постановлением Государственного комитета СССР по делам строительства от 21.08.81 N 151
3. ВЗАМЕН ГОСТ 310.4-76
4. ССЫЛОЧНЫЕ НОРМАТИВНО-ТЕХНИЧЕСКИЕ ДОКУМЕНТЫ
5. ИЗДАНИЕ (апрель 2003 г.) с Изменениями N 1, 2, утвержденными в августе 1984 г., мае 1990 г. (ИУС 1-85, 9-90)
Настоящий стандарт распространяется на цементы всех видов и устанавливает методы их испытаний для определения предела прочности при изгибе и сжатии.
(Измененная редакция, Изм. N 2).
1. АППАРАТУРА
Мешалка для перемешивания цементного раствора.
Чаша и лопатка.
Встряхивающий столик и форма-конус.
Штыковка.
Формы для изготовления образцов-балочек.
Насадка к формам.
Вибрационная площадка.
Прибор для испытания на изгиб образцов-балочек.
Пресс для определения предела прочности при сжатии.
Пластинки для передачи нагрузки.
Пропарочная камера.
1.1. Мешалка для перемешивания цементного раствора
1а. Для перемешивания цементного раствора применяют лопастную мешалку. Ее схема, взаимное расположение, размеры и предельные отклонения размеров лопастей и чаши приведены на черт.1а.
В систему лопастей входят две активные (ведущая и ведомая) и одна пассивная (лопасть-скребок). Все три лопасти совершают планетарное вращение относительно оси чаши, а активные лопасти, кроме того, вращаются вокруг собственных осей во встречных направлениях.
Частота вращения лопастей составляет, мин:
— планетарного | 40±2 | ||
— осевого: | |||
— ведущей лопасти | 80±4 | ||
— ведомой лопасти | 160±8 |
Черт.1а. Схема мешалки для перемешивания цементного раствора
Схема мешалки для перемешивания цементного раствора
_______________
* Предельно допустимый размер при износе.
1 — чаша; 2 — ведомая лопасть; 3 — ведущая лопасть; 4 — лопасть-скребок
Черт.1а
Лопасть-скребок должна соприкасаться с поверхностью чаши.
Рабочие части лопастей могут быть защищены сменными протекторами, в качестве которых используют трубки из резины или других эластичных, износостойких и коррозионно-стойких в среде цементного раствора материалов.
Для перемешивания цементного раствора допускается применять бегунковую мешалку.
Схема бегунковой мешалки, основные размеры и их предельные отклонения приведены на черт.1.
Черт.1. Мешалка для перемешивания цементного раствора
Мешалка для перемешивания цементного раствора
__________
* 7 мм при износе.
1 — основание; 2 — чаша; 3 — ось чаши; 4 — ось бегунка; 5 — бегунок
Черт.1
Масса деталей мешалки, допустимые отклонения при изготовлении и износе должны соответствовать указанным в таблице.
В килограммах
Наименование детали | Номинальная | Предельная масса, допускаемая при | ||
изготовлении | износе, | |||
не более | не менее | |||
1. Бегунок с шестеренкой без оси | 19,1 | 19,4 | 19,1 | 18,5 |
2. Бегунок с шестеренкой и осью | 21,5 | 22,0 | 21,5 | 20,9 |
Частота вращения чаши должна быть (8±0,5) мин, а валика мешалки — (72±5) мин. Число оборотов чаши мешалки при перемешивании каждой пробы должно быть 20, после чего мешалка автоматически отключается.
1.2. Чаша и лопатка — по ГОСТ 310.3 (при использовании бегунковой мешалки).
1.1, 1.2. (Измененная редакция, Изм. N 2).
1.3. Встряхивающий столик и форма-конус
Конструкция столика должна обеспечивать плавный без перекосов подъем подвижной части на высоту (10±0,5) мм и ее свободное падение с этой высоты до удара о неподвижную преграду. Масса перемещающейся части столика должна быть (3500±100) г при изготовлении.
Число встряхиваний за рабочий цикл определения расплыва должно составлять 30 с периодичностью одно встряхивание в секунду.
Пример конструкции столика приведен на черт.2. При помощи кулачка 1, получающего движение от привода, перемещающаяся часть, состоящая из диска 2 и штока 3, поднимается на заданную высоту и затем совершает свободное падение до удара о неподвижную преграду — станину 4. Диск 2 должен быть выполнен из коррозионно-стойкого металла со шлифованной рабочей поверхностью.
Черт.2. Встряхивающий столик и форма-конус
Встряхивающий столик и форма-конус
________________
* Для испытания цемента с расплывом конуса более 200 мм применяют диск диаметром 300 мм. Указанный допуск — для изготовления.
1 — кулачок; 2 — диск; 3 — шток; 4 — станина; 5 — форма-конус с центрирующим устройством; 6 — насадка
Черт.2
Столик должен быть установлен горизонтально и закреплен на фундаменте либо на металлической плите массой не менее 30 кг. Отклонение от горизонтальности рабочей поверхности диска столика не должно превышать 1 мм на диаметр 200 мм.
Форму-конус с центрирующим устройством 5, обеспечивающим точную установку формы на диске столика и предохраняющим ее от смещения в процессе штыкования раствора, и насадку 6 изготовляют из коррозионно-стойких материалов; их основные размеры приведены на черт.2.
Эксцентриситет установки формы-конуса с центрирующим устройством относительно оси столика не должен быть более 1 мм при изготовлении.
(Измененная редакция, Изм. N 1, 2).
1.4. Штыковка (черт.3) для уплотнения раствора в форме-конусе должна быть изготовлена из стали с твердостью не менее 45 .
Черт.3. Штыковка
Штыковка
1 — стержень; 2 — рукоятка
Черт.3
Масса штыковки составляет (350±20) г.
Рукоятку рекомендуется изготовлять из неметаллического малогигроскопичного материала.
(Измененная редакция, Изм. N 2).
1.5. Разъемные формы для образцов-балочек (черт.4) изготовляют из материалов, удовлетворяющих условиям их эксплуатации и обеспечивающих жесткость форм и стабильность размеров образцов.
Продольные и поперечные стенки формы должны при закреплении плотно прилегать друг к другу и к поддону, не допуская при изготовлении образцов вытекания воды из формы.
Пределы допускаемого износа стенок форм — не более 0,2 мм по ширине и высоте.
Черт.4. Формы для изготовления образцов-балочек
Формы для изготовления образцов-балочек
_______________
* Допуск для изготовления формы.
Черт.4
(Измененная редакция, Изм. N 1, 2).
1.5.1. Устройства, используемые для разъема и чистки форм, должны обеспечивать выполнение соответствующей операции без повреждения образцов и деталей формы.
1.6. Насадка к формам балочек (черт.5) должна обеспечивать плотное прижатие стенок формы к ее основанию и формы в целом к столу вибрационной площадки.
Окно насадки по размерам должно соответствовать внутреннему контуру формы.
Допускается применять насадку с разделительными перегородками.
Черт.5. Насадка к формам балочек
Насадка к формам балочек
Черт.5
(Измененная редакция, Изм. N 1, 2).
1.7. Вибрационная площадка для уплотнения цементного раствора в формах балочек должна иметь вертикальные колебания с амплитудой (0,35±0,03) мм, частотой колебаний 3000 в минуту и быть укомплектована реле времени.
(Измененная редакция, Изм. N 1).
1.8. Прибор для испытания на изгиб
Для испытания образцов балочек на изгиб могут быть использованы приборы любой конструкции, удовлетворяющие следующим требованиям.
Средняя скорость нарастания испытательной нагрузки на образец должна быть (0,05±0,01) кН/с [0,12±0,02) МПа/с в пересчете на единицу площади приведенного сечения балочки]. Захват для установки образца должен быть снабжен цилиндрическими элементами, изготовленными из стали твердостью 56…61 .
Нижние опорные элементы должны иметь возможности поворота относительно горизонтальной оси, лежащей на нижней опорной плоскости образца и являющейся осью ее продольной симметрии.
Схема расположения образца на опорных элементах, их форма, размеры и взаимное расположение приведены на черт.6.
Черт.6. Схема расположения образца на опорных элементах
Схема расположения образца на опорных элементах
Черт.6
(Измененная редакция, Изм. N 1, 2).
1.9. Для определения предела прочности образцов при сжатии могут быть использованы прессы любой конструкции с предельной нагрузкой до 500 кН, удовлетворяющие техническим требованиям ГОСТ 28840 и обеспечивающие нагружение образца в режиме чистого сжатия.
Для компенсации пространственного отклонения от непараллельности опорных граней образца пресс должен иметь подвижную шаровую опору. Допускается применять шаровые опоры любой конструкции, обеспечивающей возможность проведения поверки пресса. Пресс должен быть снабжен приспособлением для центрированной установки нажимных пластинок, передающих нагрузку на образец.
(Измененная редакция, Изм. N 1).
1.9.1. (Исключен, Изм. N 1).
1.10. Нажимные пластинки для передачи нагрузки на половинки образцов-балочек должны быть изготовлены из стали твердостью 56…61 . Форма и размеры пластинки приведены на черт.7.
Черт.7. Пластинки для передачи нагрузки на половинки образцов-балочек
Пластинки для передачи нагрузки на половинки образцов-балочек
Черт.7
При наличии приспособлений, обеспечивающих фиксацию пластинок на верхней и нижней опорных плитах пресса в отцентрированном и совпадающем при прижиме по периметру рабочих плоскостей положении, их допускается изготовлять без упоров. При этом взаимное смещение вертикальных граней пластин не должно быть более 0,5 мм, а на расстоянии 3 мм от одной из торцевых граней нижней или верхней пластинки должен находиться упор, определяющий положение балочки и не препятствующий деформациям образца при испытании.
(Измененная редакция, Изм. N 1, 2).
1.11. Конструкция пропарочной камеры должна обеспечивать создание в ней среды насыщенного пара заданной температуры.
1.12. Порядок поверки аппаратуры приведен в приложении 2.
(Измененная редакция, Изм N 1).
2. ПРОВЕДЕНИЕ ИСПЫТАНИЯ
2.1. Определение консистенции цементного раствора
2.1.1. Для определения консистенции цементного раствора отвешивают 1500 г нормального песка (по ГОСТ 6139*), 500 и 200 г воды (В/Ц=0,40). Компоненты загружают в предварительно протертую влажной тканью чашу лопастной мешалки в следующей последовательности: песок, вода, цемент. Чашу устанавливают на мешалку и перемешивают в течение (120±10) с.
_______________
* На территории Российской Федерации действует ГОСТ 6139-2003, здесь и далее по тексту. — Примечание изготовителя базы данных.
При использовании бегунковой мешалки песок и цемент высыпают в предварительно протертую мокрой тканью сферическую чашу и перемешивают лопатой в течение 1 мин.
Затем в центре сухой смеси делают лунку, вливают в нее воду в количестве 200 г (В/Ц=0,40), дают воде впитаться в течение 0,5 мин и перемешивают смесь в течение 1 мин.
2.1.1.1. При применении бегунковой мешалки допускается перемешивать цемент и песок до и после приливания воды в мешалках, обеспечивающих хорошее перемешивание раствора и не изменяющих зерновой состав песка.
2.1.2. При применении бегунковой мешалки раствор переносят в предварительно протертую мокрой тканью чашу мешалки и перемешивают в течение 2,5 мин (20 оборотов чаши мешалки).
2.1.3. Форму-конус с центрирующим устройством устанавливают на диск встряхивающего столика. Внутреннюю поверхность конуса и диск столика перед испытанием протирают влажной тканью.
2.1.1.-2.1.3. (Измененная редакция, Изм. N 2).
2.1.4. По окончании перемешивания заполняют раствором форму-конус на половину высоты и уплотняют 15 штыкованиями металлической штыковкой. Затем наполняют конус раствором с небольшим избытком и штыкуют 10 раз.
После уплотнения верхнего слоя избыток раствора удаляют ножом, расположенным под небольшим углом к торцевой поверхности конуса, заглаживая с нажимом раствор вровень с краями конуса, затем конус снимают в вертикальном направлении. Нож предварительно протирают влажной тканью.
(Измененная редакция, Изм. N 1).
2.1.5. Раствор встряхивают на столике 30 раз за (30±5) с, после чего штангенциркулем измеряют диаметр конуса по нижнему основанию в двух взаимно перпендикулярных направлениях и берут среднее значение. Расплыв конуса с В/Ц=0,40 должен быть в пределах 106-115 мм. Если расплыв конуса окажется менее 106 мм, количество воды увеличивают для получения расплыва конуса 106-108 мм. Если расплыв конуса окажется более 115 мм, количество воды уменьшают для получения расплыва конуса 113-115 мм.
Водоцементное отношение, полученное при достижении расплыва конуса 106-115 мм, принимают для проведения дальнейших испытаний.
2.2. Определение предела прочности при изгибе и сжатии
2.2.1. Непосредственно перед изготовлением образцов внутреннюю поверхность стенок форм и поддона слегка смазывают машинным маслом. Стыки наружных стенок друг с другом и с поддоном формы промазывают тонким слоем солидола или другой густой смазки.
На собранную форму устанавливают насадку и промазывают снаружи густой смазкой стык между формой и насадкой.
(Измененная редакция, Изм. N 1).
2.2.2. Для определения прочностных характеристик цементов изготавливают образцы-балочки из цементного раствора, приготовленного как указано в пп.2.1.1 и 2.1.2, с В/Ц=0,40 и консистенцией, характеризуемой расплывом конуса 106-115 мм. Если при В/Ц=0,40 расплыв конуса менее 106 или более 115 мм, образцы изготовляют при водоцементном отношении, определенном по п.2.1.5.
2.2.3. Для каждого установленного срока испытаний изготовляют по три образца (одна форма).
2.2.4. Для уплотнения раствора форму балочек с насадкой, подготовленную по п.2.2.1, закрепляют в центре виброплощадки, плотно прижимая ее к плите. Допускается устанавливать две формы, симметрично расположенные относительно центра виброплощадки, при условии одновременного их заполнения.
Форму по высоте наполняют приблизительно на 1 см раствором и включают вибрационную площадку. В течение первых 2 мин вибрации все три гнезда формы равномерно небольшими порциями заполняют раствором. По истечении 3 мин от начала вибрации виброплощадку отключают. Форму снимают с виброплощадки и избыток раствора удаляют ножом, расположенным под небольшим углом к поверхности укладки, заглаживая с нажимом раствор вровень с краями формы. Образцы маркируют. Нож предварительно должен быть протерт влажной тканью.
2.2.5. После изготовления образцы в формах хранят (24±1) ч в ванне с гидравлическим затвором или в шкафу, обеспечивающем относительную влажность воздуха не менее 90%.
2.2.4, 2.2.5. (Измененная редакция, Изм. N 1).
2.2.6. По истечении времени хранения, указанного в п.2.2.5, образцы осторожно расформовывают и укладывают в ванны с питьевой водой в горизонтальном положении так, чтобы они не соприкасались друг с другом.
Вода должна покрывать образцы не менее чем на 2 см. Воду меняют через каждые 14 сут. Температура воды при замене должна быть (20±2) °С, как и при хранении образцов.
2.2.6.1. Образцы, имеющие через (24±1) ч прочность, недостаточную для расформовки их без повреждения, допускается вынимать из формы через (48±2) ч, указывая этот срок в рабочем журнале.
(Измененная редакция, Изм. N 1).
2.2.7. По истечении срока хранения образцы вынимают из воды и не позднее чем через 30 мин подвергают испытанию. Непосредственно перед испытанием образцы должны быть вытерты.
(Измененная редакция, Изм. N 2).
2.2.8. Определение предела прочности при изгибе
Образец устанавливают на опорные элементы прибора таким образом, чтобы его горизонтальные при изготовлении грани находились в вертикальном положении. Схема расположения образца на опорных элементах показана на черт.6. Образцы испытывают в соответствии с инструкцией, приложенной к прибору.
2.9.9. Предел прочности при изгибе вычисляют как среднее арифметическое значение двух наибольших результатов испытания трех образцов.
2.2.10. Определение предела прочности при сжатии
Полученные после испытания на изгиб шесть половинок балочек сразу же подвергают испытанию на сжатие. Половинку балочки помещают между двумя пластинками таким образом, чтобы боковые грани, которые при изготовлении прилегали к стенкам формы, находились на плоскостях пластинок, а упоры пластинок плотно прилегали к торцевой гладкой плоскости образца (черт.8). Образец вместе с пластинами центрируют на опорной плите пресса. Средняя скорость нарастания нагрузки при испытании должна быть (2,0±0,5) МПа/с. Рекомендуется использовать приспособление, автоматически поддерживающее стандартную скорость нагружения образца.
Черт.8. Положение образца между нажимными пластинками при испытании на сжатие
Положение образца между нажимными пластинками при испытании на сжатие
1 — нижняя плита пресса; 2 — пластинки; 3 — верхняя плита пресса
Черт.8
(Измененная редакция, Изм. N 1).
2.2.11. Предел прочности при сжатии отдельного образца вычисляют как частное от деления величины разрушающей нагрузки (в кгс) на рабочую площадь пластинки (в см), т.е. на 25 см.
2.2.12. Предел прочности при сжатии вычисляют как среднее арифметическое значение четырех наибольших результатов испытания шесть образцов.
2.3. Определение прочности цемента при пропаривании
2.3.1. Образцы для определения прочности цемента при пропаривании изготовляют в соответствии с пп.2.1. и 2.2. Для предохранения поверхности образца от попадания конденсата формы накрывают пластинами, выполненными из коррозионно-стойких материалов и не оказывающими давления на образцы. Формы с образцами помещают в пропарочную камеру, где выдерживают в течение (120±10) мин при температуре (20±3) °С (при отключенном подогреве).
(Измененная редакция, Изм. N 2).
2.3.2. Пропарку ведут по следующему режиму:
— равномерный подъем температуры до (85±5) °С … (180±10) мин
— изотермический прогрев при температуре (85±5) °С … (360±10) мин
— остывание образцов при отключенном подогреве … (120±10) мин.
Затем открывают крышку камеры.
2.3.3. Через (24±2) ч с момента изготовления образцы расформовывают и сразу же испытывают в соответствии с п.2.2.
ПРИЛОЖЕНИЕ 1. (Исключено, Изм. N 2).
ПРИЛОЖЕНИЕ 2 (обязательное). ПОВЕРКА АППАРАТУРЫ
ПРИЛОЖЕНИЕ 2
Обязательное
1. Поверке подлежат:
— мешалка для перемешивания цементного раствора;
— встряхивающий столик и форма-конус;
— штыковка;
— формы для изготовления образцов-балочек;
— вибрационная площадка;
— прибор для определения предела прочности образцов при изгибе;
— пресс для определения предела прочности образцов при сжатии;
— пластинки для передачи нагрузки на половинки образцов-балочек.
2. Поверку проводят в соответствии с утвержденными инструкциями с периодичностью не реже одного раза в год.
3. Поверяемые параметры аппаратуры приведены в таблице.
Объект поверки | Поверяемый узел | Поверяемый параметр |
1. Мешалка лопастная для перемешивания цементного раствора | Лопасти активные | Диаметр описанной окружности, размеры сторон сечения |
Лопасть пассивная | Размеры сторон сечения, длина горизонтальной части | |
2. Мешалка бегунковая для перемешивания цементного раствора | Бегунок | Диаметр, ширина, радиус закругления |
Ось с бегунком в сборе | Масса | |
Чаша | Диаметр вписанного круга | |
Механизм в сборе | Частота вращения чаши в минуту, частота вращения бегунка в минуту, зазор между дном чаши и нижней точкой поверхности бегунка, расстояние от центра вращения чаши до средней вертикальной плоскости бегунка | |
3. Встряхивающий столик | Механизм в целом | Высота подъема падающих частей, полное число встряхиваний за рабочий цикл (для автоматических столиков), отклонение от горизонтальной рабочей поверхности диска |
4. Форма-конус с центрирующим устройством | Размеры | |
5. Штыковка | Размеры рабочей поверхности | |
6. Форма для изготовления образцов-балочек | Внутренние размеры, параллельность стенок | |
7. Вибрационная площадка | Амплитуда колебаний | |
8. Прибор для определения предела прочности при изгибе | Опорные и передающие нагрузку элементы | Размеры элементов и их взаимное расположение |
Прибор в целом | Точность воспроизведения нагрузок | |
9. Пресс для определения предела прочности при сжатии | Точность воспроизведения нагрузок | |
10. Пластинки для передачи нагрузки на половинки образцов-балочек | Состояние рабочей поверхности, размеры, плоскостность рабочей поверхности, перпендикулярность боковых граней |
Приложение 2. (Измененная редакция, Изм. N 2).
Электронный текст документа
подготовлен АО «Кодекс» и сверен по:
официальное издание
Цементы. Методы испытаний: Сб. ГОСТов.
ГОСТ 310.1-76-ГОСТ 310.3-76, ГОСТ 310.4-81,
ГОСТ 310.5-88, ГОСТ 310.6-85. —
М.: ИПК Издательство стандартов, 2003
Определение марки (активности) цемента
Навигация:
Главная → Все категории → Цемент
Марку цемента, или его активность, определяют по прочности на сжатие и изгиб стандартных образцов размером 40х40х х 160 мм, изготовленных из цементно-песчаного раствора состава 1:3 нормальной консистенции после необходимого срока твердения (для портландцемента, шлакопортландцемента и пуц-цоланового цемента — 28 сут, для быстротвердеющего портландцемента — 3 и 28 сут, для глиноземистого — 3 сут) в стандартных условиях (ГОСТ 310.4-81). Ниже рассмотрена методика определения марки (активности) портландцемента.
При определении марки используют стандартный песок, что позволяет исключить влияние качества песка на прочность испытуемого цемента. Стандартный песок (ГОСТ 6139-91) представляет собой чистый кварцевый песок (содержание Si02 > 98%; потери при прокаливании
Рис. 4.4. Мешалка для цементного раствора: 1 — чаша; 2 — бегунок; 3, 4 — скребки
Приготовление цементного раствора нормальной консистенции.
Для приготовления необходимого количества цементно-песчаного раствора состава 1:3 (по массе) отвешивают 500 г испытуемого цемента и 1500 г стандартного песка и высыпают их в предварительно протертую мокрой тканью чашу (см. рис. 4.3, а). Цемент с песком перемешивают в течение 1 мин. Затем в центре сухой смеси делают лунку, вливают в нее воду в количестве 200 г (В/Ц = 0,4) и дают ей впитаться в течение 0,5 мин, после чего смесь перемешивают вручную в течение 1 мин.
Подготовленный таким образом раствор переносят в предварительно протертую влажной тканью чашу 1 мешалки (рис. 4.4) и перемешивают в ней в течение 2,5 мин (20 оборотов чаши).
Как исключение смесь можно перемешивать вручную не менее 5 мин круглым шпателем в сферической чаше (см. рис. 4.3).
Рис. 4.5. Встряхивающий столик;
По окончании перемешивания определяют консистенцию раствора. Для этого применяют встряхивающий столик (рис. 4.5), представляющий собой металлический диск, покрытый шлифованным стеклом. При вращении кулачка диск с помощью штока, скользящего в направляющих, поднимается на 10 мм, а затем резко падает. Таким образом имитируется виброуплотнение раствора.
На стекло столика ставят коническую форму 5 с загрузочной воронкой. Внутреннюю поверхность конуса и стекло перед укладкой раствора протирают влажной тканью.
Для определения консистенции раствор укладывают в форму-конус в два приема (слоями равной толщины). Каждый слой уплотняют штыковкой из нержавеющей стали диаметром 20 мм, массой (350 ±20) г. Нижний слой штыкуют 15 раз, верхний — 10 раз. Штыкование ведут от периферии к центру, придерживая форму рукой. Далее снимают загрузочную воронку, излишек раствора срезают ножом и осторожно снимают форму-конус.
Полученный конус цементного раствора встряхивают на столике 30 раз в течение (30 ± 5) с. Затем штангенциркулем или металлической линейкой измеряют диаметр конуса по нижнему основанию в двух взаимно перпендикулярных направлениях и берут среднее значение.
Консистенция раствора считается нормальной, если расплыв конуса составляет 106…115 мм. Если расплыв конуса менее 106 мм или раствор при встряхивании рассыпается, приготовляют новую порцию раствора, увеличивая количество воды до получения расплыва конуса Ю6…115мм. Если расплыв конуса более 115 мм, то испытание повторяют с меньшим количеством воды, добиваясь расплыва 106…115 мм. Водоцементное отношение, полученное при достижении расплыва конуса 106…115мм, принимают для проведения дальнейших испытаний. Погрешность определения В/Ц не более 0,01.
Рис. 4.6. Форма для образцов-балочек (с) и насадка к ней (б)
Изготовление образцов. Разъемные формы, в которых изготовляют образцы, рассчитаны на три образца (рис. 4.6, а). Детали форм выполнены из стали или чугуна с твердостью по Бри-неллю не менее НВ140. Продольные и поперечные стенки форм, скрепляемые зажимным винтом, отшлифованы и плотно прилегают к отшлифованной поверхности поддона.
Перед заполнением формы растворной смесью ее внутренние поверхности слегка протирают машинным маслом, а стыки наружных стенок с поддоном и одна с другой смазывают техническим вазелином. На форму устанавливают металлическую насадку (рис. 4.6, б), облегчающую укладку раствора. После этого форму жестко закрепляют в центре виброплощадки.
Виброплощадка (рис. 4.7) состоит из станины, к которой пружинами прикреплена рама с установленной на ней площадкой. Колебательные движения площадки создает прикрепленный к ней электродвигатель, на валу которого находится дебаланс (эксцентрично закреплен груз).
Форму заполняют приблизительно на 1 см раствором и включают виброплощадку. Затем в течение 2 мин вибрации все три гнезда формы равномерно небольшими порциями заполняют раствором. По истечении 3 мин от начала вибрации виброплощадку отключают и снимают с нее форму. Далее смоченным водой ножом срезают излишек раствора, заглаживают поверхность образцов и маркируют их.
Образцы в формах хранят (24 ± 2) ч на столике 3 в ванне с гидравлическим затвором (рис. 4.8). Затем образцы осторожно расформовывают и укладывают в горизонтальном положении в ванну с водой так, чтобы они не соприкасались один с другим. Воду, которая должна покрывать образцы не менее чем на 2 см, меняют через каждые 14 сут. Температура воды весь срок хранения должна быть (20 ± 2) °С.
Рис. 4.7. Лабораторная виброплощадка:
1 – станина; 2 – электродвига тель; 3 – площадка; 4 — рама; 5 -пружины
Рис. 4.8. Ванна с гидравлическим затвором: 1— ванна; 2 — герметичная крышка; 3 — столик
Рис. 4.9. Схема расположения образцов-балочек на опорных элементах
Образцы, прочность которых через 24 ч недостаточна для расформовывания их без повреждений, допускается вынимать из форм через 48 ч с отметкой об этом в рабочем журнале.
По истечении срока хранения образцы извлекают из воды и не позднее чем через 1 ч подвергают испытанию.
Непосредственно перед испытанием образцы-балочки насухо вытирают и испытывают на изгиб, а затем каждую из полученных половинок балочки — на сжатие.
При испытании глиноземистого цемента образцы в форме хранят первые 6 ч в ванне с гидравлическим затвором, а затем в воде комнатной температуры. Через (24 ± 2) ч с момента изготовления образцы вынимают из формы и часть их испытывают, а оставшиеся хранят в воде до последующих испытаний через 3 сут.
Определение предела прочности при изгибе. Это испытание производят на машинах (п. 3.9), обеспечивающих нарастание нагрузки в среднем (50±10)Н в секунду. Образец устанавливают на опорные элементы машины таким образом, чтобы его горизонтальные при изготовлении грани находились в машине в вертикальном положении (рис. 4.9). Испытание образцов и расчет предела прочности при изгибе выполняют в соответствии с инструкцией, прилагаемой к испытательной машине. Предел прочности при изгибе испытуемого цемента вычисляют как среднее арифметическое из двух наибольших значений результатов испытания трех образцов.
Определение предела прочности при сжатии. Полученные после испытания на изгиб шесть половинок балочек сразу же подвергают испытанию на сжатие на прессах с предельной нагрузкой 200…500 кН.
Рис. 4.10. Испытание половинок балочек на сжатие:
а — пластинки; б — схема испытания; 1 — пластинки; 2, 4 — плиты пресса; 3 – образец (балочка)
Для того, чтобы результаты испытаний половинок балочек были сопоставимы, несмотря на разный размер, используют металлические пластинки (рис. 4.10, а), через которые нагрузка от плит пресса передается на образец. Пластинки, изготовляемые из нержавеющей стали, имеют плоскую полированную поверхность; площадь поверхности пластинки, соприкасающейся с образцом, равна 25 см2.
Половинку балочки помещают между двумя пластинками (рис. 4.10, б) таким образом, чтобы боковые грани, которые при изготовлении прилегали к продольным стенкам формы, находились на плоскостях пластинок, а упоры пластинок плотно прилегали к торцовой гладкой грани образца. Образец вместе с пластинками центрируют на опорной плите 4 пресса. Средняя скорость нарастания нагрузки на образец при испытании должна составлять (5± 1,25) кН в секунду.
Предел прочности при сжатии цемента вычисляют по результатам шести испытаний как среднее арифметическое четырех наибольших результатов.
Полученное таким образом значение называют активностью цемента.
Определение марки цемента. Марку цемента находят по результатам определения пределов прочности цемента при сжатии и изгибе, сравнивая эти результаты с требованиями ГОСТа на соответствующий цемент.
Определение прочности цемента при пропаривании.
Бетонные и железобетонные изделия изготовляют, ускоряя твердение бетона с помощью его тепловлажностной обработки (пропари-вания). Поэтому ГОСТ 10178-85 предусматривает определение прочности цемента при пропаривании. Образцы для этого испытания готовят так же, как и для стандартных определений, но их твердение протекает по специальному режиму. Формы с образцами для твердения помещают в пропарочную камеру при температуре (20±3)°С при отключенном подогреве на (120 ± +10) мин.
Похожие статьи:
Равномерность изменения объема цемента
Навигация:
Главная → Все категории → Цемент
Статьи по теме:
Главная → Справочник → Статьи → Блог → Форум
ГОСТ Р 55224-2012 Цементы для транспортного строительства. Технические условия, ГОСТ Р от 27 ноября 2012 года №55224-2012
ГОСТ Р 55224-2012
Группа Ж12
ОКС 91.100.10
Дата введения 2013-07-01
1 РАЗРАБОТАН Обществом с ограниченной ответственностью Фирма «ЦЕМИСКОН» (ООО Фирма «ЦЕМИСКОН»)
2 ВНЕСЕН Техническим комитетом по стандартизации ТК 465 «Строительство»
3 УТВЕРЖДЕН И ВВЕДЕН В ДЕЙСТВИЕ Приказом Федерального агентства по техническому регулированию и метрологии от 27 ноября 2012 г. N 1248-ст
4 ВВЕДЕН ВПЕРВЫЕ
Правила применения настоящего стандарта установлены в ГОСТ Р 1.0-2012 (раздел 8). Информация об изменениях к настоящему стандарту публикуется в ежегодном (по состоянию на 1 января текущего года) информационном указателе «Национальные стандарты», а официальный текст изменений и поправок — в ежемесячном информационном указателе «Национальные стандарты». В случае пересмотра (замены) или отмены настоящего стандарта соответствующее уведомление будет опубликовано в ближайшем выпуске ежемесячного информационного указателя «Национальные стандарты». Соответствующая информация, уведомление и тексты размещаются также в информационной системе общего пользования — на официальном сайте Федерального агентства по техническому регулированию и метрологии в сети Интернет (gost.ru)
Введение
Действующий в настоящее время ГОСТ 31108-2003, гармонизированный с европейским региональным стандартом [1] в части классификации, основных технических требований, методов испытаний, критериев и методов оценки соответствия цементов, распространяется только на цементы общестроительного назначения и не содержит специальных требований к цементам для транспортного строительства, в том числе требований к минералогическому составу клинкера и прочности цемента на растяжение при изгибе, приоритетных для бетона дорожных и аэродромных покрытий.
Настоящий стандарт устанавливает технические требования к специальным цементам, применяемым в транспортном строительстве, классы прочности и типы по вещественному составу в зависимости от назначения цемента с учетом классификации и методов испытаний цементов, установленных в ГОСТ 30515, ГОСТ 31108 и ГОСТ 30744 соответственно.
В текст настоящего стандарта в отличие от ГОСТ 31108 включены следующие основные требования:
— классификация цементов для транспортного строительства по назначению;
— ограничения по типам и классам прочности цементов, которые могут применяться в транспортном строительстве;
— предел прочности на растяжение при изгибе цемента для бетонов дорожных и аэродромных покрытий;
— дополнительные требования к вещественному составу цемента и минералогическому составу клинкера.
1 Область применения
Настоящий стандарт распространяется на цементы, изготавливаемые на основе портландцементного клинкера нормированного состава и применяемые в транспортном строительстве для изготовления бетонов дорожных и аэродромных покрытий, мостовых конструкций, железобетонных изделий, в том числе железобетонных труб, шпал, опор линий электропередачи, бордюрного камня и др., а также для бетона дорожных оснований и укрепления грунтов, для которых специальные требования к минералогическому составу клинкера не предъявляются (далее — цементы), и устанавливает требования к цементам и компонентам их вещественного состава.
Требования настоящего стандарта допускается использовать при проектировании и изготовлении других железобетонных изделий и конструкций, если это не противоречит действующим нормативным документам на эти изделия и конструкции (стандартам, сводам правил и др.).
2 Нормативные ссылки
В настоящем стандарте использованы нормативные ссылки на следующие стандарты:
ГОСТ Р 51795-2001 Цементы. Методы определения содержания минеральных добавок
ГОСТ 310.4-81 Цементы. Методы определения предела прочности при изгибе и сжатии
ГОСТ 310.6-85 Цементы. Метод определения водоотделения
ГОСТ 3476-74 Шлаки доменные и электротермофосфорные гранулированные для производства цемента
ГОСТ 4013-82 Камень гипсовый и гипсоангидритовый для производства вяжущих материалов. Технические условия
ГОСТ 5382-91 Цементы и материалы цементного производства. Методы химического анализа
ГОСТ ISO 9001-2011 Системы менеджмента качества. Требования
ГОСТ 10178-85 Портландцемент и шлакопортландцемент. Технические условия
ГОСТ 30108-94 Материалы и изделия строительные. Определение удельной эффективной активности естественных радионуклидов
ГОСТ 30515-97 Цементы. Общие технические условия
ГОСТ 30744-2001 Цементы. Методы испытаний с использованием полифракционного песка
ГОСТ 31108-2003 Цементы общестроительные. Технические условия
Примечание — При пользовании настоящим стандартом целесообразно проверить действие ссылочных стандартов в информационной системе общего пользования — на официальном сайте Федерального агентства по техническому регулированию и метрологии в сети Интернет или по ежегодному информационному указателю «Национальные стандарты», который опубликован по состоянию на 1 января текущего года, и по выпускам ежемесячного информационного указателя «Национальные стандарты» за текущий год. Если заменен ссылочный стандарт, на который дана недатированная ссылка, то рекомендуется использовать действующую версию этого стандарта с учетом всех внесенных в данную версию изменений. Если заменен ссылочный стандарт, на который дана датированная ссылка, то рекомендуется использовать версию этого стандарта с указанным выше годом утверждения (принятия). Если после утверждения настоящего стандарта в ссылочный стандарт, на который дана датированная ссылка, внесено изменение, затрагивающее положение, на которое дана ссылка, то это положение рекомендуется применять без учета данного изменения. Если ссылочный стандарт отменен без замены, то положение, в котором дана ссылка на него, рекомендуется применять в части, не затрагивающей эту ссылку.
3 Термины и определения
В настоящем стандарте применены термины по ГОСТ 30515.
4 Классификация
4.1 По назначению цементы для транспортного строительства подразделяют на:
— цемент для бетонов дорожных и аэродромных покрытий;
— цемент для бетонов дорожных оснований;
— цемент для изготовления железобетонных изделий и мостовых конструкций, применяемых в транспортном строительстве;
— цемент для укрепления грунтов.
4.2 Классификация цементов, указанных в 4.1, по типам и классам прочности приведена в таблице 1.
Таблица 1 — Типы и классы прочности цементов для транспортного строительства
Назначение цемента | Обозначение по назначению | Типы по вещественному составу | Классы прочности |
Для бетона дорожных и аэродромных покрытий | ДП | ЦЕМ I, ЦЕМ II/А-Ш* | 32,5Н; 32,5Б; 42,5Н; 42,5Б; 52,5Н; 52,5Б |
Для бетона дорожных оснований | ДО | ЦЕМ II/А-Ш, ЦЕМ II/В-Ш, ЦЕМ Ill/A, ЦЕМ V/A** | 32,5Н; 32,5Б; 42,5Н |
Для железобетонных изделий и мостовых конструкций | ЖИ | ЦЕМ I, ЦЕМ II/А-Ш* | 32,5Н; 32,5Б; 42,5Н; 42,5Б; 52,5Н; 52,5Б |
Для укрепления грунтов | УГ | Типы не устанавливают***. Содержание минеральных добавок допускается до 80% массы цемента без учета материалов, содержащих сульфат кальция | 22,5Н; 32,5Н |
* Содержание доменного гранулированного шлака по ГОСТ 3476 в цементах типа ЦЕМ II/A-Ш должно быть не более 15% суммарной массы основных компонентов цемента. ** Композиционный цемент типа ЦЕМ V/A допускается применять для бетона дорожных оснований только на основании заключения о его пригодности, выданного испытательным центром, аккредитованным на право выполнения испытаний цементов или бетонов. *** Возможность применения конкретного цемента должна быть подтверждена экспериментально. Примечание — В настоящей таблице для цементов каждого назначения приведены разрешенные к применению типы и классы прочности цементов. В проектной документации указывают конкретный тип и класс прочности цемента из числа указанных в таблице, который должен быть применен при изготовлении бетонных и/или растворных смесей согласно данному проекту. |
4.3 Условное обозначение цемента, кроме цемента для укрепления грунтов, должно включать в себя:
— наименование цемента по ГОСТ 31108;
— обозначение типа и класса прочности цемента в соответствии с таблицей 1;
— обозначение цемента по назначению в соответствии с таблицей 1;
— обозначение настоящего стандарта.
Пример условного обозначения портландцемента для бетона дорожных и аэродромных покрытий ДП, типа ЦЕМ I, класса прочности 42,5Н:
Портландцемент ЦЕМ I 42,5Н ДП ГОСТ Р
То же композиционного цемента для бетона дорожных оснований ДО, типа ЦЕМ V/A со смесью золы и шлака, класса прочности 32,5Н:
Композиционный цемент ЦЕМ V/A (Ш-3) 32,5Н ДО ГОСТ Р
В условное обозначение цемента допускается не включать его наименование по ГОСТ 31108, например:
ЦЕМ V/А (Ш-3) 32,5Н ДО ГОСТ Р
4.4 Условное обозначение цемента, предназначенного для укрепления грунтов, должно включать в себя слово «цемент», класс прочности цемента, обозначение по назначению УГ и обозначение настоящего стандарта.
Пример условного обозначения цемента класса прочности 22,5 Н для укрепления грунтов:
Цемент 22,5Н УГ ГОСТ Р
4.5 Условное обозначение цемента, в котором содержание щелочных оксидов не превышает 0,6% его массы, дополняют словом «низкощелочной» или обозначением «НЩ». Обозначение «НЩ» помещают после обозначения класса прочности цемента.
Пример условного обозначения низкощелочного цемента со шлаком для бетона дорожных и аэродромных покрытий, класса прочности 42,5Б:
Низкощелочной цемент ЦЕМ II/А-Ш 42,5Б ДП ГОСТ Р
или ЦЕМ II/А-Ш 42,5Б НЩ ДП ГОСТ Р
5 Технические требования
Цементы, применяемые в транспортном строительстве, должны соответствовать требованиям настоящего стандарта и изготавливаться по технологической документации, утвержденной предприятием-изготовителем.
5.1 Вещественный состав цемента конкретного типа с учетом примечания к таблице 1 должен соответствовать ГОСТ 31108.
5.2 Прочность на сжатие цемента конкретного класса прочности в возрасте 2; 7 и 28 сут должна соответствовать требованиям ГОСТ 31108.
Примечание — До отмены ГОСТ 10178 ориентировочное соотношение между марками цемента по ГОСТ 10178 и классами прочности по ГОСТ 31108, если необходимо, определяют по приложению А настоящего стандарта.
5.3 Прочность на растяжение при изгибе цемента для бетона дорожных и аэродромных покрытий должна соответствовать значениям, приведенным в таблице 2.
Таблица 2 — Прочность на растяжение при изгибе
Срок испытаний, сут | Прочность на растяжение при изгибе, МПа, не менее, цемента класса | |||||
32,5Н | 32,5Б | 42,5Н | 42,5Б | 52,5Н | 52,5Б | |
2 | — | 3,9 | 3,9 | 4,1 | 4,1 | 4,4 |
7 | 4,1 | — | — | — | — | — |
28 | 5,5 | 5,5 | 6,0 | 6,0 | 6,5 | 6,5 |
5.4 Удельная поверхность цемента для бетона дорожных и аэродромных покрытий, а также для изготовления железобетонных изделий и мостовых конструкций должна быть не менее 270 и не более 350 м/кг при измерении методом воздухопроницаемости.
5.5 Начало схватывания цемента для бетона дорожных и аэродромных покрытий, дорожных оснований и цемента, применяемого для изготовления железобетонных изделий и мостовых конструкций, в том числе железобетонных труб, должно наступать не ранее 2 ч от начала затворения.
5.6 Цемент, применяемый в транспортном строительстве, должен выдерживать испытания на равномерность изменения объема. Расширение не должно превышать 10 мм.
5.7 Содержание щелочных оксидов в пересчете на () в цементе для бетона дорожных и аэродромных покрытий не должно превышать 0,8% массы цемента.
5.8 Водоотделение цемента для бетона дорожных и аэродромных покрытий и изготовления железобетонных изделий и мостовых конструкций не должно быть более 28%.
5.9 Цемент для бетона дорожных и аэродромных покрытий не должен обладать признаками ложного схватывания.
5.10 Содержание в цементе, применяемом для транспортного строительства, нерастворимого остатка, оксида серы, оксида магния и иона хлора должно соответствовать требованиям ГОСТ 31108.
5.11 Требования к материалам
5.11.1 Портландцементный клинкер
Минералогический состав клинкера, используемого для изготовления цемента для бетона дорожных и аэродромных покрытий, мостовых конструкций и железобетонных изделий, используемых в транспортном строительстве, должен соответствовать приведенному в таблице 3.
Таблица 3 — Минералогический состав портландцементного клинкера
Клинкерный минерал | Содержание клинкерного минерала, % массы клинкера, применяемого для изготовления цемента | |
для бетона дорожных и аэродромных покрытий | для железобетонных изделий и мостовых конструкций | |
, не более | 7 | 7 |
Сумма (), не более | 24 | — |
, не менее | 55 | 55 |
Для изготовления цемента для бетона дорожных оснований и укрепления грунтов применяют портландцементный клинкер, соответствующий требованиям ГОСТ 31108.
5.11.2 Минеральные добавки — основные компоненты цемента
Минеральные добавки, допускаемые к применению в соответствии с ГОСТ 31108, при содержании их в цементе свыше 6% его массы за вычетом массы материалов, содержащих сульфат кальция, а также суммарной массы технологических и специальных добавок, относятся к основным компонентам цемента.
При расчете содержания добавки по ГОСТ Р 51795 полученные результаты округляют до ближайшего целого числа.
При изготовлении цемента для бетона дорожных и аэродромных покрытий, для железобетонных изделий и мостовых конструкций в качестве основного компонента применяют только добавку доменного гранулированного шлака по ГОСТ 3476.
При изготовлении цемента для бетона дорожных оснований применяют минеральные добавки, предусмотренные ГОСТ 31108, в соответствии с типами цемента, приведенными в таблице 1.
При изготовлении цемента для укрепления грунтов применяют любые активные минеральные добавки или добавки-наполнители, не ухудшающие свойства цемента.
5.11.3 Вспомогательные компоненты цемента
Вспомогательными компонентами вещественного состава цемента являются минеральные добавки, содержание которых в цементе не превышает 5% суммарной массы основных и вспомогательных компонентов.
При изготовлении цементов, кроме цементов для бетонов дорожных и аэродромных покрытий, допускается применять любые вспомогательные компоненты вещественного состава цементов, соответствующие требованиям 5.2.3 ГОСТ 31108.
При изготовлении цементов для бетона дорожных и аэродромных покрытий и железобетонных изделий в качестве вспомогательного компонента допускается применять только доменный гранулированный шлак по ГОСТ 3476.
5.11.4 Материалы, содержащие сульфат кальция
Для изготовления цементов применяют природный гипсовый, ангидритовый или гипсоангидритовый камень по ГОСТ 4013 или другие материалы, содержащие в основном сульфат кальция, по соответствующему нормативному документу.
5.11.5 Специальные и технологические добавки
Требования к специальным и технологическим добавкам — по ГОСТ 31108. При изготовлении цементов для бетона дорожных и аэродромных покрытий, а также для железобетонных изделий и мостовых конструкций содержание органических добавок не должно быть более 0,15% массы цемента.
Согласие потребителя на введение специальных добавок должно быть указано в договорах (контрактах) на поставку цемента.
5.12 Упаковка
Упаковка цемента — по ГОСТ 30515.
5.13 Маркировка
Маркировка цемента — по ГОСТ 30515. Условное обозначение цемента принимают по 4.3, 4.4 или 4.5 настоящего стандарта.
На упаковке и/или в товаросопроводительной документации следует указывать наименование использованных специальных и технологических добавок.
6 Требования безопасности
6.1 Удельная эффективная активность естественных радионуклидов в цементе должна быть не более 370 Бк/кг, а в компонентах, применяемых при его изготовлении, — не более 740 Бк/кг.
6.2 При изготовлении и применении цемента должны выполняться требования гигиенических норм по содержанию цементной пыли в воздухе рабочей зоны и атмосфере населенных пунктов.
6.3 Не допускается вводить в цемент вспомогательные компоненты, специальные или технологические добавки, повышающие класс опасности цементов.
7 Правила приемки
7.1 Приемку цемента, в том числе приемку в потоке, проводят по ГОСТ 30515, ГОСТ 31108, а также 8.2 настоящего стандарта.
7.2 Допускаются приемка и отгрузка потребителю партий цемента с малозначительными дефектами.
К малозначительным дефектам относят дефекты, указанные в таблице 7 ГОСТ 31108, а также единичные результаты испытаний, указанные в таблице 4.
Таблица 4 — Малозначительные дефекты
Наименование показателя | Единичные результаты испытаний (малозначительный дефект) |
Начало схватывания цементов ДП, ДО и ЖИ | Менее 2 ч, но не ранее 1 ч 45 мин |
Удельная поверхность, м/кг | Менее 270, но не менее 250 |
Прочность на растяжение при изгибе | Снижение относительно значений, приведенных в таблице 2, не более чем на 0,2 МПа |
Содержание | Более 0,8%, но не более 0,9% |
7.3 Дефекты, превышающие указанные в таблице 4, считают значительными.
К значительным дефектам относятся также любые отклонения от требований настоящего стандарта по минералогическому составу портландцементного клинкера и равномерности изменения объема цемента.
Партии цемента, в которых установлен значительный дефект, приемке в качестве цементов для транспортного строительства не подлежат. В отношении таких цементов должен быть применен порядок управления несоответствующей продукцией по ГОСТ ISO 9001 либо иной порядок, установленный изготовителем.
7.4 В документе о качестве указывают наименование цемента и/или его условное обозначение по 4.3, 4.4 или 4.5. Документ о качестве оформляют в соответствии с ГОСТ 30515.
8 Подтверждение соответствия
8.1 Для подтверждения соответствия качества цемента требованиям настоящего стандарта и возможности его сертификации изготовитель должен проводить оценку качества цемента по переменным или по числу дефектных проб (приемочному числу).
8.2 Подтверждение соответствия проводят по результатам всех испытаний за период от 6 до 12 мес в соответствии с разделом 8 и приложением Ж ГОСТ 30515.
8.3 Оценку качества цемента по переменным проводят по следующим показателям: прочность на сжатие и растяжение при изгибе, содержание оксида серы (VI).
8.4 Оценку качества цемента по приемочному числу проводят по следующим показателям: удельная поверхность, начало схватывания, водоотделение, содержание щелочных оксидов.
8.5 Оценку качества цемента по минералогическому составу клинкера и равномерности изменения объема цемента не проводят.
9 Методы испытаний
9.1 Физико-механические показатели цемента определяют по ГОСТ 30744, водоотделение — по ГОСТ 310.6.
Наличие признаков ложного схватывания определяют по методике, утвержденной в установленном порядке.
9.2 Химический состав цемента и материалов, применяемых при его изготовлении, определяют по ГОСТ 5382.
9.3 Вещественный состав цемента определяют по ГОСТ Р 51795 только в пробах, отобранных на предприятии-изготовителе, в порядке, установленном ГОСТ 30515. Вещественный состав цементов в пробах, отобранных из транспортных средств, в том числе при их разгрузке у потребителя или на промежуточном складе, допускается определять, если имеются пробы клинкера и минеральных добавок, использованных при изготовлении данной партии цемента, подтвержденные актами отбора проб по ГОСТ 30515.
9.4 Удельную эффективную активность естественных радионуклидов определяют по ГОСТ 30108.
10 Транспортирование и хранение
Транспортирование и хранение цементов — по ГОСТ 30515.
11 Гарантии изготовителя
Гарантии изготовителя — по ГОСТ 31108.
Приложение А (рекомендуемое). Усредненное соотношение между марками цемента по ГОСТ 10178 и классами прочности по ГОСТ 31108 и настоящему стандарту
Приложение А*
(рекомендуемое)
_______________
* Настоящее приложение допускается применять до отмены ГОСТ 10178.
Усредненное соотношение между марками цемента по ГОСТ 10178 и классами прочности по ГОСТ 31108 и настоящему стандарту приведено в таблице А.1. Соотношение рекомендуется применять для примерной оценки марки цемента, если фактически применяемый цемент квалифицирован классом прочности по ГОСТ 31108, а в нормативной, проектной или иной документации или в составе бетонных или растворных смесей предусмотрено применение цемента, качество которого задано марками по ГОСТ 10178, а также для примерной оценки класса прочности цемента, если его качество в документе о качестве изготовителя определено маркой по ГОСТ 10178.
Таблица А.1 — Соотношение между марками и классами прочности цемента
Марка цемента по ГОСТ 10178 | Нормативная прочность, МПа | Расчетная прочность по ГОСТ 31108, МПа | Среднее соотношение , % | Класс прочности цемента по ГОСТ 31108 и настоящему стандарту |
300 | От 29,4 до 39,1 | От 20,7 до 32,6 | 76,9 | 22,5 |
400 | От 39,2 до 48,9 | От 32,7 до 44,6 | 87,3 | 32,5; 42,5 |
500 | От 49,0 до 53,8 | От 44,7 до 50,7 | 92,6 | 42,5 |
550 | От 53,9 до 58,7 | От 50,8 до 56,7 | 95,3 | 42,5; 52,5 |
600 | От 58,8 до 68,5 | От 56,8 до 68,6 | 98,2 | 52,5 |
Соотношение между марками и классами прочности рассчитано с использованием уравнения регрессии:
, 0,87, (А.1)
где — активность цемента в возрасте 28 сут при испытаниях по ГОСТ 30744, МПа;
— активность цемента в возрасте 28 сут при испытаниях по ГОСТ 310.4, МПа;
— коэффициент корреляции между и .
Уравнение (А.1) получено по результатам параллельных испытаний по ГОСТ 310.4 и ГОСТ 30744 более двух тысяч образцов цемента. В выборку включены результаты испытаний всех испытанных цементов независимо от их вида и марки по ГОСТ 10178.
Остаточная дисперсия при оценке регрессии (часть общей дисперсии, не зависящая от корреляции между и )
, (А.2)
составляет 24,3% .
Примеры использования таблицы А.1:
Пример 1 — Для цемента класса 42,5 с активностью в возрасте 28 сут 45,3 МПа необходимо определить ориентировочную марку цемента по ГОСТ 10178.
Решение: в соответствии с таблицей А.1 среднее соотношение активностей цементов по ГОСТ 31108 и ГОСТ 10178 в интервале расчетных прочностей 44,750,7 МПа составляет 92,6%. Ориентировочная активность цемента при испытаниях по ГОСТ 310.4 равна 48,9 МПа.
Цемент предположительно относится к марке 400 по ГОСТ 10178, но без большой погрешности может быть принята марка 500.
Пример 2 — Для цемента марки 300 с активностью в возрасте 28 сут 31,5 МПа необходимо определить ориентировочный класс прочности цемента.
Решение: в соответствии с таблицей А.1 среднее соотношение активностей цемента в интервале расчетных прочностей 29,439,1 МПа составляет 76,9%. Ориентировочная активность цемента при испытаниях по ГОСТ 30744 равна 24,2 МПа.
Цемент предположительно относится к классу 22,5 по ГОСТ 31108.
Библиография
________________
* Доступ к международным и зарубежным документам, упомянутым в тексте, можно получить, обратившись в Службу поддержки пользователей. — Примечание изготовителя базы данных.
[1] | EN 197-1:2000* | Цемент. Часть 1. Состав, технические требования и критерии соответствия обычных цементов |
(EN 197-1:2000) | (Cement — Part 1: Composition, specification and conforming criteria for common cements) |
_______________
* Действует EN 197-1:2011.
Электронный текст документа
подготовлен ЗАО «Кодекс» и сверен по:
официальное издание
М.: Стандартинформ, 2013
Страница не найдена — ZZBO
ВибропрессыWP_Term Object ( [term_id] => 46 [name] => Вибропрессы УЛЬТРА [slug] => vibropress-ultra [term_group] => 0 [term_taxonomy_id] => 46 [taxonomy] => product_cat [description] => [parent] => 45 [count] => 12 [filter] => raw )
WP_Term Object ( [term_id] => 49 [name] => Передвижные вибропрессы [slug] => vibropress-mobile [term_group] => 0 [term_taxonomy_id] => 49 [taxonomy] => product_cat [description] => [parent] => 45 [count] => 2 [filter] => raw )
WP_Term Object ( [term_id] => 47 [name] => Вибропрессы СТАНДАРТ [slug] => vibropress-standart [term_group] => 0 [term_taxonomy_id] => 47 [taxonomy] => product_cat [description] => [parent] => 45 [count] => 8 [filter] => raw )
WP_Term Object ( [term_id] => 48 [name] => Вибропрессы МАКСИМАЛ [slug] => vibropress-maximal [term_group] => 0 [term_taxonomy_id] => 48 [taxonomy] => product_cat [description] => [parent] => 45 [count] => 8 [filter] => raw )
WP_Term Object ( [term_id] => 51 [name] => Вибропрессы блоков ФБС [slug] => vibropress-fbs [term_group] => 0 [term_taxonomy_id] => 51 [taxonomy] => product_cat [description] => [parent] => 45 [count] => 3 [filter] => raw )
WP_Term Object ( [term_id] => 59 [name] => Вибропрессы для колец ЖБИ [slug] => zhbi-koltsa [term_group] => 0 [term_taxonomy_id] => 59 [taxonomy] => product_cat [description] => Предлагаем оборудование для производства колодезных колец по ГОСТ 8020-90 любых размеров.
Два типа оборудования: вибропрессы КС и виброформы.
[parent] => 0 [count] => 17 [filter] => raw )
WP_Term Object ( [term_id] => 52 [name] => Прессы для колки камней [slug] => vibropress-pk-kolk [term_group] => 0 [term_taxonomy_id] => 52 [taxonomy] => product_cat [description] => Прессы для колки камней серии ПК предназначены для раскалывания различного типа камней природного и искусственного происхождения, как по заранее отформованным в них углублениях, так и без последних для получения декоративной (ломанной) лицевой поверхности.
Усилие колки от 10 до 80 тонн. Ширина раскола от 400 мм до 1000 мм. Идеально подходит для раскалывания гранита, мрамора и других натуральных камней.
[parent] => 45 [count] => 4 [filter] => raw )