Технология оксидирования стали: химическое, анодное, термическое
Одной из важных задач по сохранению металлических конструкций является борьба с вредным воздействием окружающей среды. Повышенная влажность, наличие в воздухе химически активных элементов, способных разрушать целостность металла, особенно стали, приводит к ухудшению таких показателей как надёжность и прочность.
Для решения этой задачи готовые изделия покрывают различными видами защитных покрытий.


Существуют различные методы повышения поверхностной устойчивости и антикоррозийности.
Одним из таких методов является создание на поверхности стали защитной плёнки, используя специальные способы обработки.
Понимание сущности назначения этого процесса требует ответа на вопрос — что такое оксидирование?
Сущность заключается в использовании свойств окислительно — восстановительной реакции, в результате чего на поверхности стали образуется защитная плёнка. Так же производится оксидирование стали.
Этот процесс позволяет решить следующие задачи:
- Защитить стальные конструкции от образования коррозии (особенно это актуально в современном строительстве, где применяются металлические конструкции).
- Ограничить воздействие агрессивных составляющих внешней среды (растворов кислот, щелочей, химических элементов, разрушающих целостность стали).
- Создать поверхностный слой, обладающий хорошими электроизоляционными характеристиками.
- Придать деталям, отдельным элементам, конструкции в целом оригинальные декоративные и эстетические свойства.
Оксидирование металла производится следующими методами:
- С применением химических реакций (химическое оксидирование стали).
- Использование электрохимических процессов (анодное оксидирование).
- Проведением термической обработки (термический метод).
- Создание низкотемпературной плазмы (плазменный метод).
- Лазерным (применяются специальные лазерные установки).


Анодированная сталь
Рассмотрим каждый метод подробнее.
Химическое оксидирование
Этот процесс предполагает обработку металлов растворами, смесями, расплавами химических элементов (такие окислы как окислы хрома). Данное оксидирование позволяет провести так называемую пассивацию поверхности металла. Он предполагает создание в близком к поверхности слое металла неактивного (пассивного) образования. Создаётся тонкий поверхностный слой, защищающий основную часть конструкции.
Технологически этот процесс реализовывается посредством опускания подготовленной металлической детали в раствор щёлочи или кислоты, заданного процентного соотношения.
Выдерживают его там определённое время, которое позволяет полностью провести окислительно — восстановительную реакцию. Затем деталь тщательно промывают, подвергают естественной сушке, окончательной обработке.


Химическое оксидирование стали
Для создания кислотной ванны применяют три вида химически активных кислот: соляную, азотную, ортофосорную. Ускорение протекания химической реакции стимулируют добавлением в раствор кислоты соединений марганца, калия, хрома. Реакция окисления протекает при температуре раствора в интервале от 30 °С до 100 °С.
Применение растворов на основе щелочных соединений позволяет использовать добавки соединений нитрата натрия и диоксида марганца. В этом случае температура раствора необходимо повышать до 180 °С, а с добавками и до 300 °С.
После проведенной процедуры деталь промывают и просушивают. Иногда для закрепления процесса химической реакции применяют бихромат калия. Для увеличения срока сохранения образованной плёнки проводят химическое оксидирование с промасливанием. Иногда такой процесс называют химоксидирование. При окончательном покрытии маслом получается надёжное покрытие от коррозии, обладающее эффектным высоко декоративным чёрным цветом.
Анодное оксидирование
Такой вид называется – электрохимическое оксидирование стали. Иногда его называют и анодное оксидирование стали. Также применяют термин анодирование. В его основу заложен химический процесс электролиза. Его можно проводить как в твёрдых, так и в жидких электролитах. Подготовленную заготовку помещают в ёмкость с оксидным раствором.
Протекание реакции электролиза возможно при создании разности потенциалов между двумя элементами.
Поверхность окисляемого изделия характеризуется положительным потенциалом. Из раствора выделяют химически активные элементы с отрицательным потенциалом. Взаимодействие разнополярных элементов и называется реакцией электролиза (в нашем случае анодирования).


Анодное оксидирование
Протекание реакции анодирования можно выполнить в домашних условиях. Требуется чётко выполнять условия техники безопасности. В реакции участвуют вредные реактивные жидкости и небезопасное напряжение.
Применение анодного оксидирования позволяет создавать защитные плёнки различной толщины. Создание толстых плёнок возможно благодаря применению раствора серной кислоты.
Тонкие плёнки получают в растворах борной или ортофосфорной кислоты. С помощью анодирования можно придать поверхностному слою металла красивые декоративные оттенки. С этой целью процесс проводят в органических кислотах. В качестве таких растворов применяют щавелевую, малеиновую, сульфосалициловую
Специальным процессом анодирования считается микродуговое оксидирование. Оно позволяет получать покрытия, обладающие высокими физическими и механическими характеристиками. К ним относятся: защитные, изоляционные, декоративные, теплостойкие и антикоррозийные свойства. В этом случае оксидирование производится под действием переменного или импульсного тока в специальных ваннах заполненных электролитом. Такими электролитами являются слабощелочные составы.


Анодное оксидирование в домашних условиях
Анодирование позволяет получить поверхностный слой, обладающий следующими свойствами:
- надёжное антикоррозионное покрытие;
- хорошие электрические изоляторы;
- тонкий, но стойкий поверхностный слой;
- оригинальную цветовую гамму.
К анодированию нержавеющей стали требуется специальный подход. Это связано с тем, что такая сталь считается нейтральным (инертным) сплавом. Поэтому на производстве при анодировании большого количества деталей применяют двух этапную процедуру.
На первом этапе анодирование нержавеющей стали производят совместно с другим, более подходящим для этого процесса металлом. Это может быть никель, медь, другой металл или сплав.
На втором этапе производят оксидирование непосредственно самой нержавеющей стали. Для упрощения процесса оксидирования сегодня ведутся разработки специальных добавок, так называемых пассивирующих паст. Эти составы ускоряют процесс реакции нержавеющей стали.
Термическое оксидирование
Согласно термину оксидирование происходит при относительно высоких температурах. Величина этого показателя зависит от марки стали. Например, процесс термического оксидирование обычной стали происходит в специальных печах. Внутри создаётся температура, близкая к 350 °С. Класс легированных сталей подвергаются термическому оксидированию при более высоких температурах. Необходимо разогреть заготовку до 700 °С. Обработка продолжается в течение одного часа. Этот процесс получил название воронение стали.
- Воронение стали
- Стальной пистолет после воронения
Плазменное оксидирование
Такое оксидирование проводят в среде с высокой концентрацией кислорода с помощью низкотемпературной плазмы. Плазма создаётся благодаря разрядам, возникающим при подаче токов высокой или сверхвысокой частоты.
Плазменное оксидирование используют для формирования оксидированных плёнок на достаточно небольших поверхностях.
В основном его применяют в электронике и микроэлектронике. С его помощью образуют слои на поверхности полупроводниковых соединений, так называемых p-n переходах. Такие плёнки используют в транзисторах, диодах (в том числе в туннельных диодах), интегральных микросхемах. Кроме этого она используется для повышения светочувствительного эффекта в фотокатодах.


Плазменное оксидирование
Разновидностью плазменного оксидирования является оксидирование с применением высокотемпературной плазмы. Иногда её заменяют на дуговой разряд с повышением температуры до 430 °С и выше. Применение этой технологии позволяет значительно повысить качество образуемых покрытий.
Лазерное оксидирование
Эта технология достаточно сложна и требует специального оборудования. Для проведения оксидирования используют:
- импульсное лазерное излучение;
- непрерывное излучение.
В обоих случаях применяются лазерные установки инфракрасного диапазона. За счёт лазерного прогрева верхнего слоя материала удаётся получить достаточно стойкую защитную плёнку. Однако этот метод применяется только для поверхности небольшой площади.


Лазерное оксидирование
Оксидирование своими руками
Организовать процесс оксидирования небольших металлических изделий можно в домашней лаборатории. При точном соблюдении последовательности технологических операций добиваются качественного оксидирования.
Весь процесс следует разделить на три этапа:
- Подготовительный этап (включает подготовку необходимого оборудования, реактивов, самой детали).
- Этап непосредственного оксидирования.
- Завершающий этап (удаление вредных следов химического процесса).
На подготовительном этапе проводят следующие работы:
- Грубая зачистка поверхности (применяется щётка по металлу, наждачная бумага, полировочная машина с соответствующими дисками).
- Окончательная механическая полировка поверхности.
- Снятие жирового налёта и остатков полировки. Его называют декопирование. Он проводится в пяти процентном растворе серной кислоты. Время пребывания обрабатываемой детали в растворе равно одной минуте.
- Промывание детали. Эту процедуру проводят в тёплой кипячёной воде. Целесообразно её провести несколько раз.
- Завершающей операцией является так называемое пассирование. Вымытую после обработки деталь, помещают чистую кипячёную воду, в которой предварительно растворяют хозяйственное мыло. Этот раствор вместе с деталью подогревают и доводят до состояния кипения. Процедуру кипения продолжают в течение нескольких минут.


Оксидирование в домашних условиях
На этом предварительный этап заканчивается.
Основной этап оксидирования состоит из следующих операций:
- В нейтральную посуду (лучше с эмалированным покрытием), заливается вода. В ней растворяют около едкий натр. Объём вещества зависит от количества воды. Целесообразно получить раствор около 5 процентов.
- В полученный раствор полностью погружают обрабатываемую деталь.
- Раствор с погруженной деталью нагревают до 150 градусов. Практически это процесс кипячения. Он продолжается примерно два часа. Используя инструмент, проверяют качество процесса. Если необходимо время может быть увеличено.
На завершающем этапе с деталью производят следующие операции:
- Деталь извлекают из ванны с реактивом.
- Укладывают на ровную поверхность, дают её остыть естественным образом (без принудительного охлаждения). Желательно создать условия, ограничивающие контакт с окружающим воздухом.
- Визуально проверяют качество полученного оксидирования. Отсутствие непокрытых участков, плотность образованной плёнки, итоговый цвет.
Таким образом, проводить оксидирование можно и в домашних условиях. Главное, соблюдать указанные рекомендации.
Если вы нашли ошибку, пожалуйста, выделите фрагмент текста и нажмите Ctrl+Enter.
Оксидирование металлов в домашних условиях
Эта статья уделит свое внимание разбору явления оксидирования металлов. Здесь мы рассмотрим общее представление о данном явлении, ознакомимся с некоторыми разновидностями и изучим их на примере со сталью. Также читатель узнает, как совершить подобный процесс самостоятельно.
Определение оксидирования
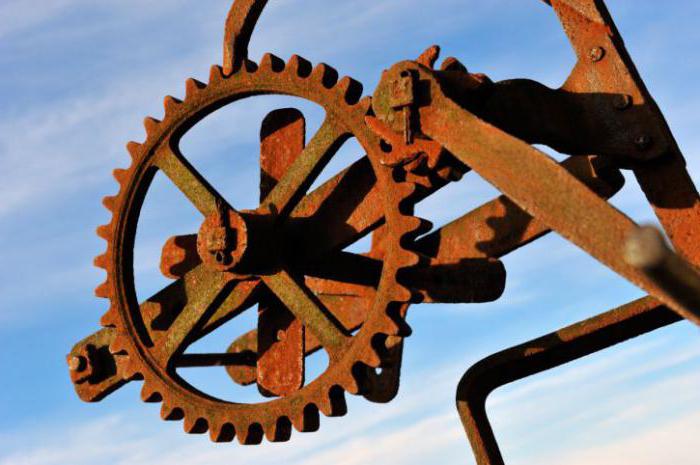
Для начала мы остановимся на понятии самого оксидирования. Это процесс, в ходе которого создается оксидная пленка на поверхностной площади изделия, а также на заготовке. Он становится возможным благодаря проведению окислительно-восстановительных реакций. Чаще всего подобные меры используют при оксидировании металлов, элементов декора и с целью сформировать диэлектрический слой. Среди главных разновидностей выделяют следующие: термическую, плазменную, химическую и электрохимическую форму.
Видовое разнообразие
Останавливаясь на описании выше перечисленных видов, про каждый из них можно сказать, что:
- Термическая форма оксидирования может осуществляться в ходе нагревания определенного изделия или инструмента в атмосферах пара воды или кислорода. Если происходит оксидирование металлов, например, железа и низколегированной стали, то процесс называют воронением.
- Химическая форма оксидирования характеризует себя, в качестве процесса обработки, посредством использования расплавов или растворов окислителей. Это могут быть представители хроматов, нитратов и т. п. Чаще всего это делается с целью придания изделию защиты от процессов коррозии.
- Оксидирование электрохимического типа характеризуется тем, что протекает внутри электролитов. Его также называют микродуговым оксидированием.
- Плазменную форму оксидирования реально осуществлять только при наличии плазмы с низкой температурой. Она должна содержать О2. Вторым условием является наличие разряда постоянного тока, а также ВЧ и/или СВЧ.
Общее понятие окисления
Чтобы лучше понять, что это – оксидирование металлов, желательно будет также ознакомиться и с общей, краткой характеристикой окисления.
Окисление – это процесс химической природы, который сопровождается увеличением показателя степени атомного окисления вещества, какое подвергается данному явлению. Это происходит посредством пересылки отрицательно заряженных частичек – электронов, от атома, который является восстановителем. Его также могут называть донором. Передача электронов совершается по отношению к окислительному атому, электронному акцептору.
Иногда в ходе окисления молекулы исходных соединений могут становиться нестабильными и распадаться на более маленькие составные фрагменты. При этом некоторая часть атомов, образовавшихся молекулярных частиц, будет обладать большей степенью окисления, чем те же виды атомов, но пребывающие в исходном, первоначальном состоянии.
На примере оксидирования стали
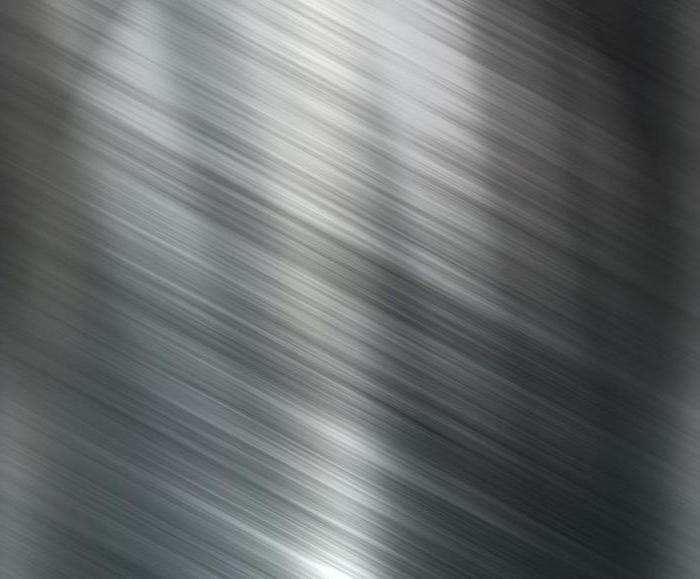
Что это такое – оксидирование металлов? Ответ на данный вопрос лучше будет рассмотреть на примере, для которого мы будем использовать проведение данного процесса со сталью.
Под химическим оксидированием металла – стали, понимают процесс выполнения работы, в ходе которой металлическую поверхность покроют оксидной пленкой. Эту операцию проводят, чаще всего, для образования защитного покрытия или придания новой черты элементу декора; еще это делают с целью создать диэлектрические слоя на изделиях из стали.
Говоря о химическом оксидировании, важно знать: сначала изделие подвергают обработке каким-либо сплавом или раствором хромата, нитрата или некоторого ряда других окислителей. Это придаст металлу защиту против воздействия коррозии. Процедуру можно также проводить с использованием композиций щелочной или кислотной природы.
Химическая форма оксидирования, выполняемая посредством использования щелочей, должна выполняться при температуре от 30 до 180 °С. Для таких процедур необходимо использовать щелочи с примесью небольшого количества окислителей. После того, как деталь обработали щелочным соединением, ее необходимо обязательно очень тщательно промыть, а далее высушить. Иногда заготовку, уже прошедшую через процедуру оксидирования, могут дополнительно промаслить.
Детальнее о кислотном методе
Для применения метода кислотных операций необходимо использовать несколько кислот, чаще это две-три. Основными веществами такого типа являются соляная, ортофосфорная и азотная кислоты. В них добавляются незначительное количество соединений марганца и др. Варьирование температурных показателей, в которых может происходить оксидирование металла – стали, посредством использования кислотного метода, лежит в пределах от 30 до 100 °С.
Химическое оксидирование, описанное для двух методов, дает человеку возможность получить как в производственной, так и в домашней обстановке, пленку, обуславливающую достаточно сильную защиту изделия. Однако важно будет знать, что предохранение стали и других металлов будет более надежным в случае применения электрохимической процедуры. Именно по причине преимущества электрохим. метода над химическим оксидированием, последнее используют реже по отношению к объектам из стали.
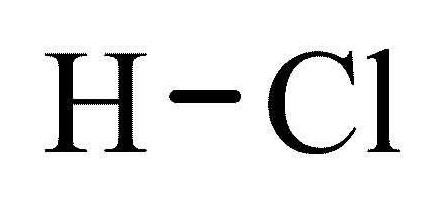
Анодная форма оксидирования
Оксидирование металлов может проходить с применением анодного процесса. Чаще всего электрохимический процесс оксидирования называют именно анодным. Он осуществляется в толще электролитов твердого или жидкого агрегатного состояния. Также применение такого метода позволит нанести на объект пленку высокого качества:
- Толщина тонкослойного покрытия лежит в пределах от 0.1 до 0.4 микрометров.
- Обеспечение электроизоляционных и износостойких свойств возможно в том случае, если толщина будет колебаться от двух-трех до трехсот мкм.
- Защитное покрытие = 0.3 – 15 мкм.
- Могут наноситься слои со свойствами, подобными эмали. Специалисты такую пленку чаще всего называют эматаль-покрытием.
Характеристикой изделия, которое подвергли анодированию, является наличие положительного потенциала. Данная процедура рекомендуется с целью придания защиты элементам микросхем интегрального типа, а также при создании диэлектрического покрытия на поверхности полупроводников, сплавов и сталей.
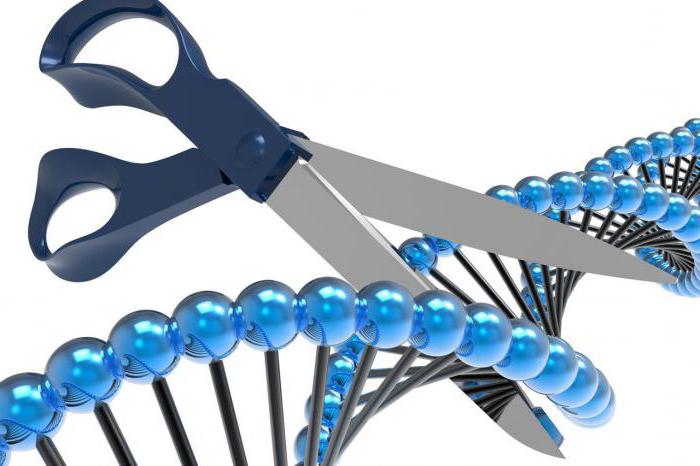
Процесс оксидирования металлов анодированного типа может, при желании, выполнить любой человек в бытовых условиях, дома. Однако очень важно будет соблюдать все условия техники безопасности, и выполнять это необходимо безоговорочно. Это обуславливается использованием в данном методе очень агрессивных соединений.
Одним из частных случаев анодирования считают способ микродугового оксидирования. Он позволяет человеку получать ряд уникальных покрытий с высокими параметрами декоративного, теплостойкого, защитного, изоляционного и антикоррозийного типа. Микродуговая форма протекания процесса может осуществляться только под воздействием переменного или импульсного тока в толще электролитов, обладающих слабощелочным характером. Рассматриваемый способ позволяет получать толщину покрытия от двухсот до двухсот пятидесяти мкм. После выполнения операции поверхность станет похожа на керамику.
Процесс воронения
Оксидирование черных металлов в профессиональной терминологии называют воронением.
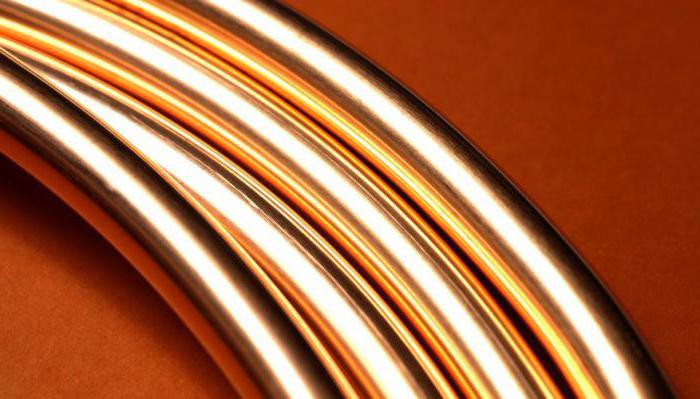
Если говорить о воронении стали, например, об оксидировании, чернении или синении, можно сказать, что это процесс, в ходе которого на чугуне или низколегированной стали образуют слой оксида железа. Как правило, толщина такой пленки лежит в пределах от одного до десяти мкм. Толщина слоя обуславливает и наличие определенного цвета побежалости. В зависимости от возрастания толщины пленочного слоя, цвета могут быть: желтым, бурым, вишневым, фиолетовым, синим и серым.
В настоящее время существует несколько типов воронения:
- Щелочной тип характеризуется использованием соответственных растворов, с добавлением окислителей, в условиях температуры от 135 до 150 градусов по Цельсию.
- Кислотный тип воронения использует кислые растворы и химические или электрохимические способы.
- Термическая форма обработки характеризуется использованием достаточно высоких температур (от 200 до 400 °С). Процесс проходит в толще атмосферы перегретого пара воды. Если используют аммиачно-спиртовую смесь, то требования к температуре возрастают до 880 °С, а в расплавленных солях — от 400 до 600 °С. Использование воздушной атмосферы требует предварительного покрытия поверхности запчасти тоненьким слоем лака, который должен быть асфальтным или масляным.
Ознакомление с термическим оксидированием
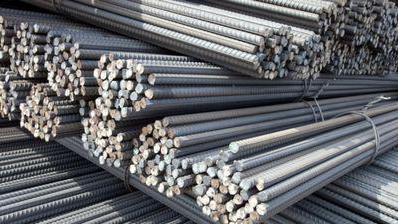
Термическое оксидирование металлов – это методика, в ходе которой оксидную пленку наносят на сталь в пространстве атмосферы водяного пара. Также могут использовать и другие кислородосодержащие среды с достаточно высокими температурами. Провести термическую обработку в домашних условиях довольно сложно, а потому, как правило, ее не выполняют. Упоминая о плазменном типе оксидирования, важно знать, что проделать это дома практически невозможно.
Самостоятельное выполнение операции
Оксидирование металла в домашних условиях можно провести самостоятельно. Проще всего подвергать подобной обработке изделия из стали. Для этого сперва необходимо отполировать или зачистить деталь, над которой будет проведена работа оксидирования. Далее следует удалить с поверхности окислы посредством использования растворов пятипроцентной h3SO4 (серной кислоты). Изделие необходимо держать в течение шестидесяти секунд в жидкости.
Дальнейшие действия
После того, как этап помещения детали в ванну с кислотой пройдет, следует ее промыть под теплой водой и провести работу по пассивированию или, другими словами, прокипятить объект в течение пяти минут. Для этого используют раствор воды из водопровода с пятьюдесятью граммами простого хозяйственного мыла. Здесь расчет идет на 1 литр жидкости. Проведя все эти действия, мы подошли к завершению оксидирования. Чтобы реализовать процедуру, необходимо:
- Использовать емкости, подверженные эмалированию и не имеющие сколов или царапин на внутренней поверхности.
- Наполнить емкость водой и развести соответствующим количеством граммов едкого натра (с расчетом на 1 литр = 50 грамм).
- Перенести сосуд с водой на плиту и сверху расположить изделие.
- Нагревать смесь, приблизительно до 135-150 °С.
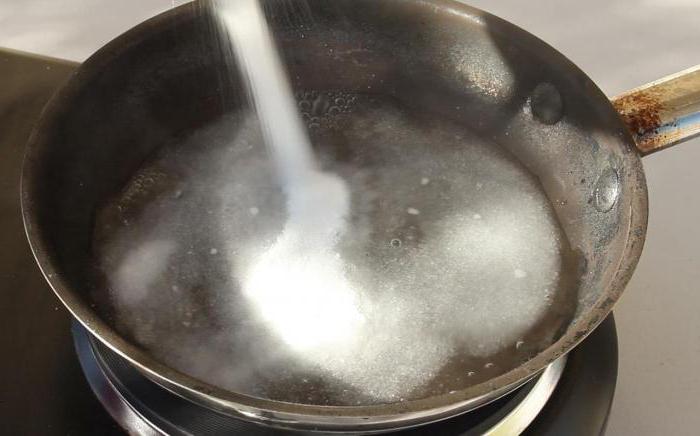
Спустя 90 минут деталь можно вытягивать и созерцать собственную работу.
Некоторые данные
Читателю будет знать, что в случае потребности проведения подобной операции, но при отсутствии умения или желания, с такой просьбой можно обратиться к различным специалистам. Оксидирование металлов в Москве, например, может выполняться как специалистами в различных сферах услуг, так и на дому, людьми. Некоторые виды такого средства придания защиты детали, могут быть довольно дорогими. В столице РФ анодированный тип оксидирования будет стоить довольно дорого, однако придаст высокий показатель надежности объекту. Чтобы найти специалистов в подобном деле, достаточно набрать в запросе поиска гугла, например: «выполнение химического оксидирования в … (определенном городе или области)», или нечто подобное.
Оксидирование стали – все способы нанесения защитного покрытия
Под оксидированием стали понимают процедуру создания на металлических поверхностях оксидной пленки. Данная операция проводится для образования декоративных и защитных покрытий, а также специальных диэлектрических слоев на стальных изделиях.
1 Особенности химического оксидирования
Интересующий нас процесс можно выполнить по нескольким технологиям. Оксидирование принято делить на:
- химическое;
- электрохимическое;
- термическое;
- плазменное.
При химическом оксидировании поверхность изделий обрабатывают расплавами либо растворами хроматов, нитратов и других окислителей, что увеличивает антикоррозионную защиту металла. Подобная процедура может выполняться посредством применения щелочных или кислотных композиций.
Рекомендуем ознакомиться
Химическое оксидирование щелочного типа выполняется при температурах от 30 до 180 градусов. Для него используют щелочи и небольшое количество окислителей. После обработки деталей щелочными соединениями их обязательно промывают (весьма тщательно), а затем просушивают. В некоторых случаях заготовки, прошедшие процедуру оксидирования, дополнительно промасливают.
Для кислотной операции обычно применяют композиции, состоящие из 2–3 кислот – соляной, ортофосфорной, азотной, в которые добавляют в незначительных объемах соединения марганца и другие соединения. Температура такого способа оксидирования варьируется в пределах 30–100 градусов. Используется он чаще всего для декорирования и защиты от коррозии ржавления.
Химическое оксидирование любого из двух описанных типов позволяет получать в производственных и в домашних условиях пленки с достаточно высокими защитными характеристиками. При этом электрохимическая процедура предохранения стали от коррозионных явлений считается более эффективной. Именно поэтому химическое оксидирование для стальных изделий используется реже, нежели электрохимическое.
2 Анодное оксидирование – что оно собой представляет?
Анодный процесс (именно так обычно называют оксидирование электрохимического вида) осуществляется в твердых либо жидких электролитах. Он обеспечивает высоконадежные пленки следующих типов:
- тонкослойные покрытия с толщиной от 0,1 до 0,4 микрометров;
- электроизоляционные и износостойкие слои толщиной от 2–3 до 300 микрометров;
- защитные покрытия от 0,3 до 15 микрометров;
- специальные эмалеподобные слои (именуются в среде специалистов эматаль-покрытиями).
При анодировании поверхность окисляемого изделия характеризуется положительным потенциалом. Такая процедура рекомендована для защиты элементов интегральных микросхем, создания на полупроводниковых материалах, сплавах и сталях диэлектрических покрытий. При желании анодирование можно выполнить в домашних условиях, но при четком и безоговорочном соблюдении стандартов техники безопасности, так как для операции используются агрессивные соединения.
Частным случаем анодирования считается методика микродугового оксидирования, которая позволяет получать уникальные покрытия с высокими декоративными, теплостойкими, защитными, изоляционными и антикоррозионными параметрами. Микродуговой процесс осуществляется под действием переменного или импульсного тока в электролитах, имеющих слабощелочной характер.
Рассматриваемый способ нанесения специальных слоев обеспечивает толщину покрытий на уровне 200–250 микрометров. После выполнения операции поверхность изделия внешне похоже на керамику. Микродуговое оксидирование при наличии оборудования нередко производят в домашних условиях. Во время процесса в воздух не выделяется каких-либо опасных для человека веществ. По этой причине микродуговая обработка становится все более популярной среди домашних мастеров.
3 Тонкости термического и плазменного оксидирования
Термический процесс подразумевает, что оксидная пленка формируется на стали в атмосфере водяного пара либо иной кислородсодержащей среде при достаточно высоких температурах. В домашних условиях такую операцию не выполняют, так как она требует использования специальных печей, в которых железо либо низколегированные стали нагревают примерно до 350 градусов.
Если же речь идет об обработке средне- и высоколегированных сталей, температура в печи и вовсе должна равняться 650–700 градусам. Общая длительность термического оксидирования, как правило, составляет около часа.
Практически нереально выполнить в домашних условиях и плазменное оксидирование. Оно производится в низкотемпературной плазме, содержащей кислород. Плазменная среда при этом создается обычно посредством ВЧ- и СВЧ-разрядов, реже применяются разряды постоянного тока. Качество получаемых защитных пленок оксидов при плазменном процессе очень высокое. Поэтому его применяют для нанесения покрытий на ответственные детали:
- кремниевые поверхности;
- полупроводниковые изделия;
- фотокатоды.
4 Как самостоятельно выполнить операцию?
Самый простой способ нанесения защитного покрытия на стальные изделия в домашних условиях не требует особых умений. При желании оксидирование своими руками может выполнить любой. Сначала деталь, которую планируется обработать, полируют либо зачищают. Затем с ее поверхности удаляют окислы (декапируют), используя для этих целей раствор (пятипроцентный) серной кислоты. Изделие помещают в него на 60 секунд.
После ванны с кислотой деталь необходимо промыть в теплой воде и подвергнуть ее пассивированию – пятиминутному кипячению, которое осуществляют в растворе водопроводной воды с 50 граммами обычного хозяйственного мыла (такое количество моющего средства рассчитано на один литр воды). Теперь поверхность полностью готова к оксидированию. Для реализации процедуры следует:
- взять эмалированную емкость, не имеющую царапин и сколов;
- налить в нее воду (один литр) и развести 50 граммов едкого натра;
- поместить емкость на плиту, положить в нее изделие и подогреть смесь до 140–150 градусов.
Через полтора часа деталь можно доставать – оксидирование успешно завершено!
Анодирование стали в домашних условиях
Одной из важных задач по сохранению металлических конструкций является борьба с вредным воздействием окружающей среды. Повышенная влажность, наличие в воздухе химически активных элементов, способных разрушать целостность металла, особенно стали, приводит к ухудшению таких показателей как надёжность и прочность.
Для решения этой задачи готовые изделия покрывают различными видами защитных покрытий.
Химическое оксидирование
Этот процесс предполагает обработку металлов растворами, смесями, расплавами химических элементов (такие окислы как окислы хрома). Данное оксидирование позволяет провести так называемую пассивацию поверхности металла. Он предполагает создание в близком к поверхности слое металла неактивного (пассивного) образования. Создаётся тонкий поверхностный слой, защищающий основную часть конструкции.
Технологически этот процесс реализовывается посредством опускания подготовленной металлической детали в раствор щёлочи или кислоты, заданного процентного соотношения.
Выдерживают его там определённое время, которое позволяет полностью провести окислительно — восстановительную реакцию. Затем деталь тщательно промывают, подвергают естественной сушке, окончательной обработке.
Для создания кислотной ванны применяют три вида химически активных кислот: соляную, азотную, ортофосорную. Ускорение протекания химической реакции стимулируют добавлением в раствор кислоты соединений марганца, калия, хрома. Реакция окисления протекает при температуре раствора в интервале от 30 °С до 100 °С.
Применение растворов на основе щелочных соединений позволяет использовать добавки соединений нитрата натрия и диоксида марганца. В этом случае температура раствора необходимо повышать до 180 °С, а с добавками и до 300 °С.
После проведенной процедуры деталь промывают и просушивают. Иногда для закрепления процесса химической реакции применяют бихромат калия. Для увеличения срока сохранения образованной плёнки проводят химическое оксидирование с промасливанием. Иногда такой процесс называют химоксидирование. При окончательном покрытии маслом получается надёжное покрытие от коррозии, обладающее эффектным высоко декоративным чёрным цветом.
Анодное» оксидирование
Такой вид называется – электрохимическое оксидирование стали. Иногда его называют и анодное оксидирование стали. Также применяют термин анодирование. В его основу заложен химический процесс электролиза. Его можно проводить как в твёрдых, так и в жидких электролитах. Подготовленную заготовку помещают в ёмкость с оксидным раствором.
Протекание реакции электролиза возможно при создании разности потенциалов между двумя элементами.
Поверхность окисляемого изделия характеризуется положительным потенциалом. Из раствора выделяют химически активные элементы с отрицательным потенциалом. Взаимодействие разнополярных элементов и называется реакцией электролиза (в нашем случае анодирования).
Протекание реакции анодирования можно выполнить в домашних условиях. Требуется чётко выполнять условия техники безопасности. В реакции участвуют вредные реактивные жидкости и небезопасное напряжение.
Применение анодного оксидирования позволяет создавать защитные плёнки различной толщины. Создание толстых плёнок возможно благодаря применению раствора серной кислоты.
Тонкие плёнки получают в растворах борной или ортофосфорной кислоты. С помощью анодирования можно придать поверхностному слою металла красивые декоративные оттенки. С этой целью процесс проводят в органических кислотах. В качестве таких растворов применяют щавелевую, малеиновую, сульфосалициловую
Специальным процессом анодирования считается микродуговое оксидирование. Оно позволяет получать покрытия, обладающие высокими физическими и механическими характеристиками. К ним относятся: защитные, изоляционные, декоративные, теплостойкие и антикоррозийные свойства. В этом случае оксидирование производится под действием переменного или импульсного тока в специальных ваннах заполненных электролитом. Такими электролитами являются слабощелочные составы.
Анодирование позволяет получить поверхностный слой, обладающий следующими свойствами:
- надёжное антикоррозионное покрытие;
- хорошие электрические изоляторы;
- тонкий, но стойкий поверхностный слой;
- оригинальную цветовую гамму.
К анодированию нержавеющей стали требуется специальный подход. Это связано с тем, что такая сталь считается нейтральным (инертным) сплавом. Поэтому на производстве при анодировании большого количества деталей применяют двух этапную процедуру.
На первом этапе анодирование нержавеющей стали производят совместно с другим, более подходящим для этого процесса металлом. Это может быть никель, медь, другой металл или сплав.
На втором этапе производят оксидирование непосредственно самой нержавеющей стали. Для упрощения процесса оксидирования сегодня ведутся разработки специальных добавок, так называемых пассивирующих паст. Эти составы ускоряют процесс реакции нержавеющей стали.
Термическое оксидирование
Согласно термину оксидирование происходит при относительно высоких температурах. Величина этого показателя зависит от марки стали. Например, процесс термического оксидирование обычной стали происходит в специальных печах. Внутри создаётся температура, близкая к 350 °С. Класс легированных сталей подвергаются термическому оксидированию при более высоких температурах. Необходимо разогреть заготовку до 700 °С. Обработка продолжается в течение одного часа. Этот процесс получил название воронение стали.
Плазменное оксидирование
Такое оксидирование проводят в среде с высокой концентрацией кислорода с помощью низкотемпературной плазмы. Плазма создаётся благодаря разрядам, возникающим при подаче токов высокой или сверхвысокой частоты.
Плазменное оксидирование используют для формирования оксидированных плёнок на достаточно небольших поверхностях.
В основном его применяют в электронике и микроэлектронике. С его помощью образуют слои на поверхности полупроводниковых соединений, так называемых p-n переходах. Такие плёнки используют в транзисторах, диодах (в том числе в туннельных диодах), интегральных микросхемах. Кроме этого она используется для повышения светочувствительного эффекта в фотокатодах.
Разновидностью плазменного оксидирования является оксидирование с применением высокотемпературной плазмы. Иногда её заменяют на дуговой разряд с повышением температуры до 430 °С и выше. Применение этой технологии позволяет значительно повысить качество образуемых покрытий.
Лазерное оксидирование
Эта технология достаточно сложна и требует специального оборудования. Для проведения оксидирования используют:
- импульсное лазерное излучение;
- непрерывное излучение.
В обоих случаях применяются лазерные установки инфракрасного диапазона. За счёт лазерного прогрева верхнего слоя материала удаётся получить достаточно стойкую защитную плёнку. Однако этот метод применяется только для поверхности небольшой площади.
Оксидирование своими руками
Организовать процесс оксидирования небольших металлических изделий можно в домашней лаборатории. При точном соблюдении последовательности технологических операций добиваются качественного оксидирования.
Весь процесс следует разделить на три этапа:
- Подготовительный этап (включает подготовку необходимого оборудования, реактивов, самой детали).
- Этап непосредственного оксидирования.
- Завершающий этап (удаление вредных следов химического процесса).
На подготовительном этапе проводят следующие работы:
- Грубая зачистка поверхности (применяется щётка по металлу, наждачная бумага, полировочная машина с соответствующими дисками).
- Окончательная механическая полировка поверхности.
- Снятие жирового налёта и остатков полировки. Его называют декопирование. Он проводится в пяти процентном растворе серной кислоты. Время пребывания обрабатываемой детали в растворе равно одной минуте.
- Промывание детали. Эту процедуру проводят в тёплой кипячёной воде. Целесообразно её провести несколько раз.
- Завершающей операцией является так называемое пассирование. Вымытую после обработки деталь, помещают чистую кипячёную воду, в которой предварительно растворяют хозяйственное мыло. Этот раствор вместе с деталью подогревают и доводят до состояния кипения. Процедуру кипения продолжают в течение нескольких минут.
На этом предварительный этап заканчивается.
Основной этап оксидирования состоит из следующих операций:
- В нейтральную посуду (лучше с эмалированным покрытием), заливается вода. В ней растворяют около едкий натр. Объём вещества зависит от количества воды. Целесообразно получить раствор около 5 процентов.
- В полученный раствор полностью погружают обрабатываемую деталь.
- Раствор с погруженной деталью нагревают до 150 градусов. Практически это процесс кипячения. Он продолжается примерно два часа. Используя инструмент, проверяют качество процесса. Если необходимо время может быть увеличено.
На завершающем этапе с деталью производят следующие операции:
- Деталь извлекают из ванны с реактивом.
- Укладывают на ровную поверхность, дают её остыть естественным образом (без принудительного охлаждения). Желательно создать условия, ограничивающие контакт с окружающим воздухом.
- Визуально проверяют качество полученного оксидирования. Отсутствие непокрытых участков, плотность образованной плёнки, итоговый цвет.
Таким образом, проводить оксидирование можно и в домашних условиях. Главное, соблюдать указанные рекомендации.
Если вы нашли ошибку, пожалуйста, выделите фрагмент текста и нажмите Ctrl+Enter.
Анодирование металла — это процесс электрохимического наращивания оксидной пленки путем анодного окисления.
Оксидная плёнка, полученная путем анодирования, прочно держится на поверхности своего металла. Возможно формирование оксидной пленки на поверхности металла другим способом — за счет повышения температуры. Но данный процесс возможен только до некоторой толщины, выше которой оксидная пленка трескается, ломается и отслаивается. При анодировании можно получать более толстые оксидные пленки, сохраняющие защитные свойства и прекрасную адгезию к субстрату.
Анодирование возможно практически для любого металла. Однако при анодировании есть ряд требований к росту пленки и ее адгезии. Во-первых, анодируемый металл должен образовывать только один устойчивый оксид. Образование двух различных оксидов ухудшает адгезию и повышает вероятность растрескивания пленки. По этой причине анодирование железа и меди крайне затруднительно. Во-вторых, при хорошей адгезии к металлу оксидная плёнка должна вместе с тем оставаться пористой, чтобы обеспечить беспрепятственный доступ электролита к поверхности металла для лучшего окисления и ее более быстрого роста. Этим требованием удовлетворяет очень мало металлов. Фактически, анодированию подвергают только алюминий, титан и тантал. Наиболее широко распространено анодирование алюминия.
Окисление алюминия на аноде сопровождается выделением кислорода. Наиболее распространёнными являются ванны с серной кислотой. В особых случаях применяют ванны с хромовой или щавелевой кислотой. Разряжаемый кислород частично реагирует с алюминием анода, а частично теряется в виде газа. По этой причине образующаяся оксидная плёнка содержит массу микроканалов, через которые к поверхности металла может поступать электролит. В результате толщина оксидной плёнки может достигать довольно больших значений. Данный механизм иллюстрирует рис. 1.
1 — гидратированный Al 2 O 3 ; 2.- Al 2 O 3 ; 3 — основной металл алюминий; 4 — микроканалы внутри плёнки; 5 — электролит (присутствует и внутри микроканалов)
Рис. 1. Механизм роста оксидной пленки алюминия.
В начале анодирования толщина пленки мала, ее сопротивление невелико и для поддержания необходимой плотности тока требуется небольшое напряжение. По мере роста толщины пленки и возрастания ее сопротивления, ток падает. При слишком большой толщине пленки она даже может начать растворяться. По закону Фарадея скорость образования пленки зависит от тока. Поэтому необходимо поддерживать требуемую плотность тока на протяжении всего процесса анодирования. Этого можно достичь постепенно увеличивая прикладываемое напряжение по мере анодирования.
Другой способ состоит в использовании менее крепкой кислоты. Однако ниже определенного значения крепость кислоты уменьшать нельзя. Поскольку в процессе анодирования кислота расходуется, при этом она должна обладать достаточной электропроводностью, иначе повышение прикладываемого напряжения вызовет ее разогрев.
Рабочие параметры процесса анодирования металлов приведены в табл. 1.
Таблица 1. Рабочие параметры процесса анодирования металлов.
Все работы по анодированию проводятся с использованием защитных средств, респиратор, очки и защитные перчатки, ибо работаем пусть и с разбавленной, но с кислотой и щелочью! В идеале в проветриваемом помещении. Соблюдаем ТБ!
Первоначально готовим саму деталь, механическая полировка, чем «чище» поверхность те более глянцевая будет деталь, можно применять и химическую полировку, но этот процесс еще более вредный для здоровья, нежели сама анодировка, поэтому выводим деталь на полировальном круге и другими средствами.
Для подвеса детали в рабочей ванне необходимо использовать алюминиевые токоподводы, никаких посторонних металлов, в идеале на детале можно оставлять конструктивный выступ, для подключения, но при его спиливании будет не покрытое место, я воспользовался конструктивными резбовыми отверстиями, на куске алюминиевого провода нарезал резьбу и просто вкрутил в эти отверстия, получается хороший, плотный контакт.
Толщину токоподвода надо подбирать с учётом силы тока, необходимого для анодирования, иначе проводник начнёт греться в месте контакта, а как следствие на нём пойдёт бурная реакция и его начнёт растравливать и уменьшать его сечение, и так в геометрической прогрессии, до полного растворения :)) (в одной из попыток так и произошло из-за плохого контакта)
Перед погружением в электролит деталь необходимо обезжирить, способов море, от Пемолюкса и прочих порошков, до средства КРОТ, намой взгляд КРОТ самое близкое к нужному, это слабый раствор щёлочи NaOH с добавлением ПАВ.
Я обезжиривал в чистом растворе NaOH+вода, концентрацию точно не замерял, но чем насыщенее раствор, тем быстрее будет процесс просто. Посути раствор растворяет тонкий слой оксида алюминия, так сказать «естественное» анодирование, окисление поверхностного слоя на воздухе, так что сильно с травлением не стоит затягивать, иначе начнёт растравливать саму деталь ))
В процессе травления идёт бурное выделение газов (кажется водорода) работать только в защитной маске и остерегаться попадания раствора на кожу, ибо ожог не хуже чем от кислоты будет.
После травления к детале уже прикасаться нельзя, иначе от прикосновений остаются жирные следы и как следствие неравномерное покрытие, пятна и прочие радости, после промывки от раствора щелочи под проточной водой клал деталь в чашку с водой, в идеале дистиллированной, что бы на неё ничего не попало, пока готовимся к следующему этапу.
Что касатся рабочей ванны можно использовать эмалированную (без сколов) или пластиковую посудину, но тогда дно и стенки придётся «выкладывать» из свинца или иного стойкого к электролиту материала, эти пластины выполняют роль катода.
Так же необходимо позаботиться об охлаждении рабочей ванны, в процессе хим реакции электролит будет нагреваться.
Я использовал 2 титановые гофты (квадратная банка) получается вся площадь гофты является катодом, что весьма положительно влияет на равномерность нанесения, ток более равномерный по пповерхности детали, ну и титану кислота не помеха.
Так же была организованная Водяная баня, только в обратную сторону, для охлаждения, вода проточная со скважины.
В качестве электролита взят Электролит для аккумуляторных батарей, разбавленный в пропорции 1:1 дистиллированной водой. При приготовлении раствора электролита соблюдаем ТБ и льём не разбавленный электролит в дистиллированную воду (Соблюдая правило Кислоту в Воду, дабы избежать закипания)
После смешивания электролит нагреется, остужаем его градусов до 15-20, и впринципи поддерживаем такую температуру, от 10 до 25 градусов, это будет «Тёплое анодирование» которое позволит в дальнейшем окрасить деталь красителем для ткани и им подобными.
Если температура будет ниже, близкая к 0, то мы получим «холодное» анодирование, слой будет плотнее и прочнее, но красителем его уже не окрасиш, поры слишком плотные будут, возможно получиться окрасить Химическим способом, но я пока такой не осваивал, поэтому в домашних условиях проще добиться Теплого анодирования.
Пока деталь плавает в воде, подключаем токоподвод к источнику тока.
В качестве источника тока лучше использовать блоки со стабилизацией по току, что бы не бегать и не следить за током, чем больше площадь детали, тем более мощный придётся искать блок.
Площадь данной детали, примерно, составила 490см2, плотность тока должна быть 15-20мА на см2 итого получаем тока 7,3-9,7А при напряжении 12в, хотя в процессе роста оксидной плёнки напряжение может подрости, я брал источник с параметрами 20А и 30в максимальные значения.
При Холодном анодировании для поддержания заданного тока может потребоваться напряжение гораздо больше чем 12в, ибо чем плотнее слой, тем больше его электрическое сопротивление.
На следующих этапах соблюдаем главное правило: «Погружение в раствор и доставание из раствора детали ТОЛЬКО при включенном источнике тока!»
Иначе кислота начнёт разъедать деталь и загрязнять раствор…
Погружаем деталь в раствор, при включенном источнике тока, достаточно самого минимального значения, просто что бы между анодом и катодом было напряжение! Опять же не забываем про маску, очки и перчатки!
Зачем размещать деталь под углом, при строго горизонтальном расположении шайбы было замечено, что торцы покрываются более плотным слоем чем плоскости, плюс если имеются не сквозные отверстия, деталь необходимо размещать так, чтобы а)электролит полностью их заполнил и б)чтобы из них мог выходить газ скапливающийся в процессе, иначе может образоваться газовый пузырь, который вытиснит электролит, и соответсвенно в этом месте деталь не покроется оксидным слоем.
Ну и по возможности деталь должна быть равноудалена от катода, тоесть стенок ванны.
Вокруг детали начнётся активное выделение пузырьков газа, кислорода, сам по себе он не особо вреден, а вот аэрозоль кислоты, образующаяся при лопании пузырьков, когда они доходят до поверхности, весьма вредно вдыхать, поэтому накрываем всё это хозяйство.
Как только накрыли крышкой, выставляем на блоке питания необходимый ток и засекаем минут 40-60
Пока ждём начинаем готовить раствор красителя, в качестве красителя можно использовать анилиновы красители разбавленные в воде или краску для заправки картриджей для струйников.
Я использовал вчастности Colouring для устройств Canon/Epson/HP/Lexmark продаётся в ДНС по 200-300р за 100мл, бывает Голубой (Cyan), Пурпурный (даёт цвет от красного до фиолетового) (Magenta), Желтый и Чёрный, так же есть Светло-голубой и Светло-пурпурный.
С голубым у меня получилось, желтый и чёрный не пробовал, а вот Magenta не захотел красить пробник почему-то.
Я разбодяживал 2 пузырька примерно на 3л воды, далее подогреваем этот раствор до 60градусов.
Все работы лучше проводить в резиновых перчатках, отмывается эта дрянь с рук очень плохо!
Периодически посматриваем как идёт процесс, раствор становится мутным от обилия пузырьков, но больших пузирей не должно быть!
При анодировании крупных деталей (ну или большого количества мелких 😉 ) возникает проблемка, за которой необходимо следить.
На одной фото обратил внимание на красный налёт на стенках ванны, это медь из сплава Д16Т выходит в раствор и осаждатся на стенках, когда деталь большая, слой становится толстым и отпадает от стенок и начинает бултыхаться какое то время в растворе, пока не растворится и снова не выпадит на стенках, НО за время своего бултыхания эти частицы попадая на поверхность детали устраивают местные прогары, что визуально видно как чёрные полоски как от электроразрядов…
Поэтому необходимо периодически сливать электролит, промывать ванну в воде и счищать медь со стенок.
После окончания процесса Анодирования, не отключая источник тока достаём деталь из раствора.
Далее следует чательная промывка детали в проточной воде, дабы смыть остатки окислительных процессов и вымыть электролит из пор, так же как и ранее ДЕТАЛЬ НЕЛЬЗЯ ТРОГАТЬ РУКАМИ максимум в резиновых перчатках или кистью аккуратно промываем.
Один раз попробовал промывку в слабом растворе щелочи, для нитролизации кислоты, но тут надо очень быстро и аккуратно и снова под проточную воду.
Я некоторое время выдерживал деталь в проточной воде, пока отцеплял от блока питания и возился с краской.
Дальше чистую деталь помещаем в горячий краситель, степень окраски зависит от концентрации раствора, времени выдержки в растворе, и оксидного слоя.
Поэтому при попытке окрасить несколько Больших деталей очень сложно попасть в цвет, ибо слишком много факторов влияющих на это, в этом плане только чёрный цвет самый простой вариант, держим в растворе минут 15, и он точно будет чёрный (точнее коричневато-чёрный)
После того, как получили нужный нам цвет, опускаем деталь в кипяток и варим её так минут 30, воду тоже лучше использовать дистиллированную.
Кипятим деталь для того, чтобы закрыть поры и краска осталась внутри, при проварке часть краски перейдёт в воду и деталь может немного осветлиться, это опять же камень в огород повторяемости цвета на нескольких одинаковых деталях…
В итоге после долгих мучений и экспрементах на «кошках» должно получиться что то подобное 🙂
Всем мира, счастья и с наступающим НГ, и не забываем При работах с кислотами шелочами обязательно использование защитных стредств!
>
что это, виды обработки сталей и сплавов
Ни один материал, включая сталь, не может служить вечно. Его необходимо защищать от влаги, солнечных лучей и низких температур. Оксидирование металла создает на его поверхности тонкую защитную пленку, не позволяющую кислороду из воздуха и воде разрушать материал. При этом изменяются технические характеристики сталей, алюминия и его сплавов.
С точки зрения химии оксидирование – это реакция окисления металла и образование на поверхности тонкого слоя кристаллов, связанных кислородом и другими веществами. Технология нанесения защитного покрытия имеет несколько видов различной сложности. Самая простая использовалась несколько веков назад и доступна любому желающему покрыть защитной пленкой деталь в домашних условиях. Сложная технология требует специального оборудования и осуществляется только в условиях производства.
Суть и назначение технологии
В своей основе оксидирование стали имеет окислительно-восстановительную реакцию металла при его взаимодействии с кислородом воздуха, электролитом или специальными кислотно-щелочными растворами. В результате на поверхности детали образуется защитная пленка, повышающая технические характеристики металла:
- увеличивает твердость;
- снижает образование задиров;
- повышает способность деталей к прирабатыванию;
- увеличивает срок службы;
- создает декоративное покрытие.
Добавление в электролит растворов для окрашивания позволяет создавать изделия из металла с поверхностями разных цветов.
Покрытие оксидной пленкой применяют для различных материалов. В ювелирной промышленности и при создании бижутерии используют оксидирование многих металлов:
- серебра;
- алюминия;
- меди;
- титана;
- латуни;
- бронзы.
Сущность обработки – в увеличении прочности и придании дополнительной декоративности. Изделия из серебра хорошо держат форму. Это позволяет создавать украшения с острыми углами и тонким орнаментом. С помощью оксидов создается патина, имитирующая старину, и другие эффекты.
В зависимости от характеристик и свойств металла используют различные технологии создания сложных окислов на поверхности.
К положительным качествам оксидирования относится его распределение по поверхности тонкой пленкой в несколько микрон – тысячных долей миллиметра. При этом не меняются размеры деталей и посадочных мест сверху и на поверхности.
Виды оксидирования металла
Процесс оксидирования стали имеет несколько разновидностей:
- микродуговое;
- горячее;
- холодное.
К микродуговому относится способ нанесения оксидной пленки с помощью электролизной установки. Деталь помещается в ванну с электролитом. К ней подключается «+» постоянного тока. К ванне – провод с «–». При прохождении тока на поверхности образуются микроочаги с высокой температурой и давлением. В результате происходит окисление. Микродуговое оксидирование применяют для покрытия алюминия, серебра и их сплавов.
Процесс горячего оксидирования стали заключается в нагреве детали или раствора, в котором она находится, для ускорения процесса образования пленки сложных окислов.
К холодным технологиям относятся, в основном, методы химического покрытия и плазменного, когда поверхность насыщается кислородом под воздействием микротоков или в насыщенном растворе солей.
Химическое
Химическое оксидирование проводится погружением деталей в различные растворы. Низкотемпературный процесс покрытия осуществляют при температуре 30–180 °C. Сталь погружают в раствор щелочей или кислот с добавлением марганца. Затем, после извлечения из ванны, промасливают – смазывают маслом или на несколько секунд погружают в него деталь.
Электрохимическое покрытие оксидами проводится при низких температурах – до 100 °C. Электролит представляет собой раствор нескольких нитратов и хроматов. Получают черное покрытие стали.
Пищевая нержавейка содержит много легирующих веществ, включая хром и марганец. Она требует для покрытия сложного оборудования. В домашних условиях ее можно оксидировать в растворе натриевой селитры. Поверхность приобретает яркий синий цвет.
Анодное
Анодное оксидирование небольших деталей доступно делать в домашней мастерской. Для этого надо иметь аккумулятор или выпрямитель тока. Анод подключается к детали и источнику постоянного тока. При погружении стали в раствор слабокислого электролита возникает движение электронов, и вместе с ними частицы солей и кислот проникают в верхний слой металла. В результате образуются кристаллы железа со сложными окислами. Они постепенно покрывают всю поверхность детали слоем в несколько микрон.
Регулировать скорость процесса для образования оксидной пленки нужной толщины можно изменением силы тока и повышением температуры электролита. Анодирование влияет на первоначальные характеристики стали и цветных металлов:
- изменяет цвет;
- увеличивает прочность;
- пленка имеет низкую электропроводность;
- не допускает образования простых окислов железа – коррозии.
Термическое
Кто наблюдал за сваркой деталей или их нагревом в термопечах, видел на поверхности цвета побежалости: от желтого оттенка до синего тона, переходящего в черный. Они зависят от температуры, до которой нагрелась сталь в конкретной точке. Чем сильнее прогрет металл, тем больше он окислен, имеет более темный цвет.
Достаточно нагреть поверхность до 300 ⁰C, чтобы провести термическое оксидирование. На стали появится тонкая пленка окислов желтого и светло-коричневого цвета. Чем выше содержание легирующих веществ, тем сильнее надо греть сталь.
Часто нагрев используют для более активного протекания химического и анодного оксидирования стали. Помещенный в горячий раствор натриевой селитры или смеси кислот металл быстрее вступает в реакцию.
Плазменное
Метод холодного оксидирования – плазменное покрытие деталей. Окисление происходит при низкой температуре. Деталь помещают в плазму, которую создают токи ВЧ или СВЧ, аналогичные микроволновой печи. В камере высокое содержание кислорода.
Плазменное оксидирование применяют, в основном, для повышения светочувствительности и электропроводности деталей оптических приборов и плат.
Лазерное
Оксидировать деталь с помощью лазера можно только в условиях промышленного предприятия. Деталь устанавливается на столе или зажимается в патроне, набирается программа, и лазер прогревает узкие полоски одна возле другой по всей поверхности. Оптимальный вариант – использование станков ЧПУ.
Недостаток лазерного оксидирования сталей – в покрытии заготовок только снаружи. В отверстия малого диаметра головка лазерной установки не войдет.
Оксидирование своими руками
Делать защитное покрытие в домашних условиях проще всего по старинному рецепту. Для этого стальной предмет следует очистить от всех видов загрязнений, протравить в слабом растворе кислоты. Любое оставшееся пятно будет препятствовать процессу оксидирования стали.
- Нагреть конструкционную сталь до 300 ⁰C. Легированные и углеродистые стали требуют более высоких температур. Чем больше легирующих элементов, тем сильнее следует греть.
- Опустить горячую заготовку в льняное масло на 8–18 минут.
- Для получения плотного слоя, надежно защищающего сталь от ржавчины, и создания изоляционного слоя, процедуру следует повторить 4–6 раз.
Каленые стали при нагреве до температуры выше 300 ⁰C могут отпуститься – стать мягче. Поэтому металл после закалки греют индуктором токами ТВЧ до 250–280 ⁰C. Если нет возможности нагреть только поверхность заготовки, температуру снижают до 220–250 °C, увеличив количество нагревов и погружений.
Льняное масло использовали в прошлые века. Сейчас его можно заменить веретенным, широко применяемым для закалки стали.
Оксидирование стали – интересный процесс. С его помощью можно самостоятельно защитить от коррозии небольшие изделия, крепеж в автомобиле и других устройствах.
Какой метод больше всего понравился нашим читателям и что они готовы применить на практике? Нам интересно ваше мнение.
Химическое оксидирование и окрашивание металлов / Кустарь
Химическое оксидирование и окрашивание металлов
Химическое оксидирование и окрашивание поверхности металлических деталей предназначаются для создания на поверхности деталей антикоррозионного покрытия и усиления декоративности покрытия.
В глубокой древности люди умели уже оксидировать свои поделки, изменяя их цвет (чернение серебра, окраска золота и т.п.), воронить стальные предметы (нагрев стальную деталь до 220…325°С, они смазывали ее конопляным маслом).
Составы растворов для оксидирования и окрашивания стали (г/л)
Заметим, что перед оксидированием деталь шлифуется или полируется, обезжиривается и декапируется.
Черный цвет
Едкий натр — 750, азотнокислый натрий — 175. Температура раствора — 135°С, время обработки — 90 мин. Пленка плотная, блестящая.
Едкий натр — 500, азотнокислый натрий — 500. Температура раствора — 140°С, время обработки — 9 мин. Пленка интенсивная.
Едкий натр — 1500, азотнокислый натрий — 30. Температура раствора — 150°С, время обработки — 10 мин. Пленка матовая.
Едкий натр — 750, азотнокислый натрий — 225, азотистокислый натрий — 60. Температура раствора — 140°С, время обработки — 90 мин. Пленка блестящая.
Азотнокислый кальций — 30, ортофосфорная кислота — 1, перекись марганца — 1. Температура раствора — 100°С, время обработки — 45 мин. Пленка матовая.
Все приведенные способы характеризуются высокой рабочей температурой растворов, что, конечно, не позволяет обрабатывать крупногабаритные детали. Однако имеется один «низкотемпературный раствор», пригодный для этого дела (г/л): тиосульфат натрия — 80, хлористый аммоний — 60, ортофосфорная кислота — 7, азотная кислота — 3. Температура раствора — 20°С, время обработки — 60 мин. Пленка черная, матовая.
После оксидирования (чернения) стальных деталей их обрабатывают в течение 15 мин в растворе калиевого хромпика (120 г/л) при температуре 60°С. Затем детали промывают, сушат и покрывают любым нейтральным машинным маслом.
Голубой цвет
Соляная кислота — 30, хлорное железо — 30, азотнокислая ртуть — 30, этиловый спирт — 120. Температура раствора — 20…25°С, время обработки — до 12 ч.
Гидросернистый натрий — 120, уксуснокислый свинец — 30. Температура раствора — 90…100°С, время обработки — 20…30 мин.
Синий цвет
Уксуснокислый свинец — 15…20, тиосульфат натрия — 60, уксусная кислота (ледяная) — 15…30. Температура раствора — 80°С. Время обработки зависит от интенсивности окраски.
Составы растворов для оксидирования и окрашивания меди (г/л)
Синевато-черные цвета
Едкий натр — 600…650, азотнокислый натрий — 100…200. Температура раствора — 140°С, время обработки — 2 ч.
Едкий натр — 550, азотистокислый натрий — 150…200. Температура раствора — 135…140°С, время обработки — 15…40 мин.
Едкий натр — 700…800, азотнокислый натрий — 200…250, азотистокислый натрий — 50…70. Температура раствора — 140…150°С, время обработки — 15…60 мин.
Едкий натр — 50…60, персульфат калия — 14… 16. Температура раствора — 60…65°С, время обработки — 5…8 мин.
Сернистый калий — 150. Температура раствора — 30°С, время обработки — 5…7 мин.
Кроме вышеперечисленных, применяют раствор так называемой серной печени. Получают серную печень, сплавляя в железной банке в течение 10…15 мин (при помешивании) 1 часть (по массе) серы с 2 частями углекислого калия (поташа). Последний можно заменить тем же количеством углекислого натрия или едкого натра.
Стеклообразную массу серной печени выливают на железный лист, остужают и дробят до порошка. Хранят серную печень в герметичной посуде.
Раствор серной печени готовят в эмалированной посуде из расчета 30… 150 г/л, температура раствора — 25…100°С, время обработки определяется визуально.
Раствором серной печени, кроме меди, можно хорошо почернить серебро и удовлетворительно — сталь.
Зеленый цвет
Азотнокислая медь — 200, аммиак (25%-ный раствор) — 300, хлористый аммоний — 400, уксуснокислый натрий — 400. Температура раствора — 15…25°С. Интенсивность окраски определяют визуально.
Коричневый цвет
Хлористый калий — 45, сернокислый никель — 20, сернокислая медь — 100. Температура раствора — 90…100°С, интенсивность окраски определяют визуально.
Буровато-желтый цвет
Едкий натр — 50, персульфат калия — 8. Температура раствора — 100°С, время обработки — 5…20 мин.
Голубой цвет
Тиосульфат натрия — 160, уксуснокислый свинец — 40. Температура раствора — 40…100°С, время обработки — до 10 мин.
Составы для оксидирования и окрашивания латуни (г/л)
Черный цвет
Углекислая медь — 200, аммиак (25%-ный раствор) — 100. Температура раствора — 30…40°С, время обработки — 2…5 мин.
Двууглекислая медь — 60, аммиак (25%-ный раствор) — 500, латунь (опилки) — 0,5. Температура раствора — 60…80°С, время обработки — до 30 мин.
Коричневый цвет
Хлористый калий — 45, сернокислый никель — 20, сернокислая медь — 105. Температура раствора — 90…100°С, время обработки — до 10 мин.
Сернокислая медь — 50, тиосульфат натрия — 50. Температура раствора — 60…80°С, время обработки — до 20 мин.
Сернокислый натрий — 100. Температура раствора — 70°С, время обработки — до 20 мин.
Сернокислая медь — 50, марганцовокислый калий — 5. Температура раствора — 18…25°С, время обработки — до 60 мин.
Голубой цвет
Уксуснокислый свинец — 20, тиосульфат натрия — 60, уксусная кислота (эссенция) — 30. Температура раствора — 80°С, время обработки — 7 мин.
Зеленый цвет
Сернокислый никель-аммоний — 60, тиосульфат натрия — 60. Температура раствора — 70…75°С, время обработки — до 20 мин.
Азотнокислая медь — 200, аммиак (25%-ный раствор) — 300, хлористый аммоний — 400, уксуснокислый натрий — 400. Температура раствора — 20°С, время обработки — до 60 мин.
Составы для оксидирования и окрашивания бронзы (г/л)
Зеленый цвет
Хлористый аммоний — 30, 5%-ная уксусная кислота — 15, среднеуксусная соль меди — 5. Температура раствора — 25…40°С. Здесь и далее интенсивность окраски бронзы определяют визуально.
Хлористый аммоний — 16, кислый щавелевокислый калий — 4, 5%-ная уксусная кислота — 1. Температура раствора — 25…60°С.
Азотнокислая медь — 10, хлористый аммоний — 10, хлористый цинк — 10. Температура раствора — 18…25 С.
Желто-зеленый цвет
От синего до желто-зеленого цвета
В зависимости от времени обработки удается получить цвета от синего до желто-зеленого в растворе, содержащем углекислый аммоний — 250, хлористый аммоний — 250. Температура раствора — 18…25°С.
Патинирование (придание вида старой бронзы) проводят в таком растворе: серная печень — 25, аммиак (25%-ный раствор) — 10. Температура раствора — 18…25°С.
Составы для оксидирования и окрашивания серебра (г/л)
Черный цвет
Серная печень — 20…80. Температура раствора — 60…70°С. Здесь и далее интенсивность окраски определяют визуально.
Углекислый аммоний — 10, сернистый калий — 25. Температура раствора — 40…60°С.
Сернокислый калий — 10. Температура раствора — 60°С.
Сернокислая медь — 2, азотнокислый аммоний — 1, аммиак (5%-ный раствор) — 2, уксусная кислота (эссенция) — 10. Температура раствора — 25…40°С. Содержание компонентов в этом растворе дано в частях (по массе).
Коричневый цвет
Раствор сернокислого аммония — 20 г/л. Температура раствора — 60…80°С.
Сернокислая медь — 10, аммиак (5%-ный раствор) — 5, уксусная кислота — 100. Температура раствора — 30…60°С. Содержание компонентов в растворе — в частях (по массе).
Сернокислая медь — 100, 5%-ная уксусная кислота — 100, хлористый аммоний — 5. Температура раствора — 40…60°С. Содержание компонентов в растворе — в частях (по массе).
Сернокислая медь — 20, азотнокислый калий — 10, хлористый аммоний — 20, 5%-ная уксусная кислота — 100. Температура раствора — 25…40°С. Содержание компонентов в растворе — в частях (по массе).
Голубой цвет
Серная печень — 1,5, углекислый аммоний — 10. Температура раствора — 60°С.
Серная печень — 15, хлористый аммоний — 40. Температура раствора — 40…60°С.
Зеленый цвет
Йод — 100, соляная кислота — 300. Температура раствора — 20°С.
Йод — 11,5, йодистый калий — 11,5. Температура раствора — 20°С.
Внимание! При окрашивании серебра в зеленый цвет необходимо работать в темноте!
Состав для оксидирования и окраски никеля (г/л)
Никель можно окрасить только в черный цвет. Раствор (г/л) содержит: персульфат аммония — 200, сернокислый натрий — 100, сернокислое железо — 9, роданистый аммоний — 6. Температура раствора — 20…25°С, время обработки — 1-2 мин.
Составы для оксидирования алюминия и его сплавов (г/л)
Черный цвет
Молибденовокислый аммоний — 10…20, хлористый аммоний — 5…15. Температура раствора — 90…100°С, время обработки — 2…10 мин.
Серый цвет
Трехокись мышьяка — 70…75, углекислый натрий — 70…75. Температура раствора — кипение, время обработки — 1…2 мин.
Зеленый цвет
Ортофосфорная кислота — 40…50, кислый фтористый калий — 3…5, хромовый ангидрид — 5…7. Температура раствора — 20…40°С, время обработки — 5…7 мин.
Оранжевый цвет
Хромовый ангидрид — 3…5, фтор-силикат натрия — 3…5. Температура раствора — 20…40°С, время обработки — 8…10 мин.
Желто-коричневый цвет
Углекислый натрий — 40…50, хромовокислый натрий — 10… 15, едкий натр — 2…2,5. Температура раствора — 80…100°С, время обработки — 3…20 мин.
Автор: Л.А. Ерлыкин
Читайте еще:
Проблематика оксидирования нержавеющей стали
Автор perminoviv На чтение 6 мин. Опубликовано
Представленная в данной статье информация будет полезна для материаловедов, технологов и инженеров, задействованных в области обработки и изучения свойств металлов. Получение декоративных покрытий все чаще находит применение в различных отраслях машиностроения, автомобилестроения, в производстве предметов быта. Рассмотрим один из самых затребованных способов создания пленки — оксидирование нержавеющей стали.
Термины, определения, виды оксидирования нержавеющей стали
По определению под этим термином понимают создание пленки из оксидов на поверхности нержавеющей стали вследствие реакций окислительно-восстановительного характера. Помимо защитной функции, декоративной отделки, применение этого процесса задействовано при необходимости создания диэлектрических слоев и изменения поверхностных физических процессов происходящих в среде высоких магнитных и электрических полей. В зависимости от того каким способом было получено оксидирование различают:
- Термический процесс
- Химическое воздействие
- Электрохимический процесс
- Плазменное оксидирование
Рассмотрим эти процессы более подробно.
Термический процесс
Термический процесс оксидирования заключается в обработке металла при определенных температурах в среде кислорода или водяного пара. Низколегированные стали и железо при таком воздействии получают пленку, называемую воронением. Температура для воронения составляет 300-350 градусов Цельсия. Для высоколегированных и высоко хромистых сталей этот показатель вырастает до 700 градусов.
Интересная информация: воронение нержавеющей стали в домашних условиях вполне под силу каждому. Для этого существует несколько способов. Любому способу должны предшествовать шлифовка металла и его обезжиривание. Окунаем деталь или изделие в масло. Оно может быть оливковым, машинным, а лучше всего оружейным. Убедившись в равномерности нанесения и попадания масла в труднодоступные места, вынимаем заготовку и даем стечь маслу. После этого начинаем нагрев паяльной лампой. Чем ниже скорость нагрева, тем выше вероятность полного удаления легких фракций, получения равномерного слоя воронения. После преодоления порога в 400 градусов на поверхности появляется характерный черный окрас. По окончании необходимо произвести полировку мягкими войлоками и пастой.
Химическое оксидирование
Химическое оксидирование – получение защитной пленки при взаимодействии металла и расплавов, чаще растворов, оксидирующих веществ. К преимуществам такого метода относятся:
- относительная простота
- отсутствие высокотемпературных источников
- простота оборудования
- низкие трудозатраты
Единственным и самым существенным недостатком данного способа заключается в низких защитных характеристиках такой пленки и низкая стойкость при механических воздействиях. Преимущественное использование химического оксидирования заключается в нанесении подкрасочного слоя, а также для консервации механизмов и деталей в условии хранения в производственных цехах и отапливаемых складах.
Необходимость в использовании большого количества воды, ее последующая очистка, высокая стоимость воды и очищающих реагентов приводит к постепенному вытеснению с производств, в условиях ужесточения природоохранных норм. Холодное химическое оксидирование нержавеющих сталей стало доступным благодаря появлению в продаже двухкомпонентных химических реагентов.
Обратите внимание: Чем выше концентрация активных химических элементов тем быстрее скорость протекания реакции, но глубина проникновения меньше. Соответственно толщина пленки будет меньше.
Электрохимическое оксидирование
Электрохимическое оксидирование нержавеющих сталей способ, который нашел широкое распространение в промышленности. Заключается он в том, что детали подвешиваются на специальные держатели. На этом приспособлении они опускаются в раствор с щелочью, после чего ванна, в котором он находится, присоединяется к отрицательному катоду. Детали подсоединяются к положительному аноду. При пропускании постоянного тока, согласно курсу физики, происходят процессы электролиза, сопровождающиеся повышением температуры. Скорость нанесения и толщина появляющейся пленки зависит от множества факторов. Основные влияющие факторы:
- Плотность протекающего тока.
- Электропроводность раствора, в который помещены детали
- Температура электролита
- Геометрия и конфигурация детали
Интересный факт: в конце предыдущего десятилетия один из гигантов японского автопроизводителя использовал гальваническое чернение нержавеющей стали кузова своих авто. Исследования показали, что в районе перегибов крыши в стойки оксидированный слой имел недостаточную толщину. Долгие изыскания по изменению места крепления электродов к кузову, изменение плотности тока, времени воздействия не приводили к ожидаемому результату. Лишь поменяв электропроводность щелочного раствора, внеся специальные добавки, слой стал равномерным и достаточным для уровня качества предприятия.
Сложная геометрия, острые углы, изогнутые формы в контурах детали приводят к различию потенциалов, возникающих на поверхности нержавеющей стали и соответственно приводят к разности толщин пленки. Для таких деталей целесообразно использование предыдущего метода оксидирования.
Плазменное оксидирование
Оксидирование плазмой происходит при условиях подобных к гальваническому чернению. При определенном достижении критического значения поляризации происходит плазменный микроразряд на поверхность анодируемой детали. В отличие от электрохимического азотирования в формировании образовавшейся пленки участвует не только раствор щелочи, но и материал катода. Характерной особенностью представленного метода можно назвать глубокое проникновение в слой нержавеющего металла и возможность получения равномерного покрытия на объектах сложной геометрической конфигурации.
Интересный факт: в месте пробоя искры при плазменном оксидировании температура составляет порядка 10000К., а давление сопоставимо с величиной 102МПа. После прекращения действия искры происходит резкое охлаждение поверхности, которые приводят к появлению новых физических свойств и исследованию их как элементов нанотехнологий.
Покрытия, которые образуются при применении такого метода, характеризуются повышенной адгезией к основе и свойствам, приближенным к керамике. Учитывая цену оборудования и недостаточность исследований в этой области, его трудоемкость и необходимость высокой квалификации персонала не позволяют широко применять этот процесс в промышленности, ограничиваясь дорогостоящими отраслями и штучными изделиями. Для алюминия, титана и сплава магния плазменное оксидирование находит ниши и распространение в промышленности.
Обратите внимание: терминология этого процесса не устоялась по сегодняшний день. Поэтому встретив в литературе оксидирование в режиме искрения, анодное осаждение, режим максимального напряжения, плазменно-электролитическое оксидирование надо понимать, что это один и тот же процесс – плазменное оксидирование.
Сложности работы по чернению, связанные с нержавеющей сталью
Все описанные выше способы идеально подходят для черных сплавов и мало легированных сталей. Требуется особый подход, комплекс мероприятий для чернения нержавеющей стали, как условно инертного сплава. Разрозненные данные в литературе о прямом чернении нержавеющей стали противоречивы и на практике не всегда срабатывают. В производственных масштабах принято решать этот вопрос двухэтапным подходом. Первый этап анодирование нержавеющей стали другим, более склонным к оксидированию металлом. В основном это никель, реже медь. Второй этап оксидирование полученной поверхности. Химиками многих стран ведется разработка специальных пассивирующих паст, составов для чернения нержавеющих сталей, способных склонять их к оксидированию.
Для нанесения декоративной пленки, неработающей при перепаде температур, на поверхности, не испытывающей больших механических нагрузок, можно применить следующий способ оксидирования:
- Травление в 10% растворе щавелевой кислоты
- Промывка и обработка в 1% растворе сульфида натрия до необходимой степени чернения
- Промасливание образца из нержавеющей стали.
Исходя из представленной информации, можно сделать вывод, что использование чернения для нержавеющей стали носит характер коммерческого декоративного покрытия. Использование оксидирования для достижения более высоких характеристик металла неоправданно и не может быть гарантированно. Для получения пленок защитного характера, расширяющих область применения нержавеющих сталей, стоит рассматривать другие способы и методы.